Why Use Hydrogen-Compatible Materials?
If you work with hydrogen, you have probably seen bright red cylinders like these. They have been utilized safely in industry for many years, but oddly enough, they are made of an alloy called 4130 steel, which is generally considered to be “incompatible” with hydrogen based on its material properties in a hydrogen environment.
If 4130 steel has such questionable mechanical properties in hydrogen, why is it used for hydrogen storage cylinders? The answers might surprise you.
Hydrogen compatibility is a complex subject with relatively little industry awareness and understanding. As the hydrogen industry grows, understanding of this topic is becoming more and more important. In this article, WHA’s resident hydrogen experts introduce the idea of hydrogen compatibility to help keep industry safe.
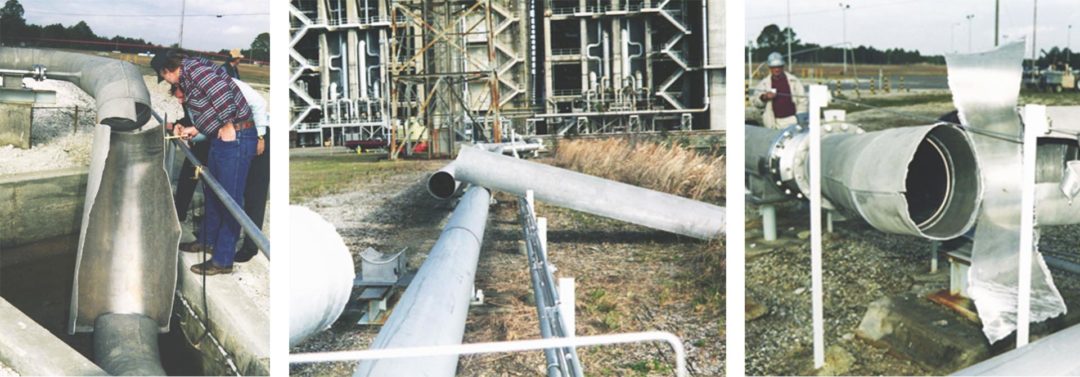
Background: Materials Compatibility
Here at WHA, we use the term “oxygen compatibility” on a regular basis. Using the right materials is an important part of a complete oxygen risk mitigation strategy.
In our oxygen safety training courses, we show how certain materials are compatible (safer) for use with oxygen, while other incompatible materials can cause dangerous failures and fires.
Oxygen Compatibility, n — the ability of a substance to coexist at an expected pressure and temperature with both an oxidant and a potential source(s) of ignition within a risk parameter acceptable to the user. (ASTM G-126)
Aluminum, for example, is often utilized for its high strength, light weight and related cost-savings, but its compatibility varies depending on application. Engineers need to be extremely careful when utilizing aluminum in oxygen component design because it readily supports combustion if ignited in elevated oxygen concentrations and pressures.
You can read our latest case study to learn more about how aluminum medical oxygen regulators caused a number of fires in the 90s and early 2000s before the medical industry switched to more burn-resistant materials like brass, which was considered more compatible for this oxygen application.
Over the years, WHA has compiled thousands of experimental data points to help industry understand which materials are appropriate for different oxygen applications. Much of this data is publicly accessible in our oxygen compatibility materials database. You can read more about oxygen testing here and watch a liquid oxygen mechanical impact sensitivity test here.
Similar concepts and data sets exist and are currently being further developed by WHA for hydrogen material compatibility. Distinctly different from oxygen, the explanation for “why” certain materials are preferred is based on the fundamental properties of hydrogen and its interaction with materials in a given application.
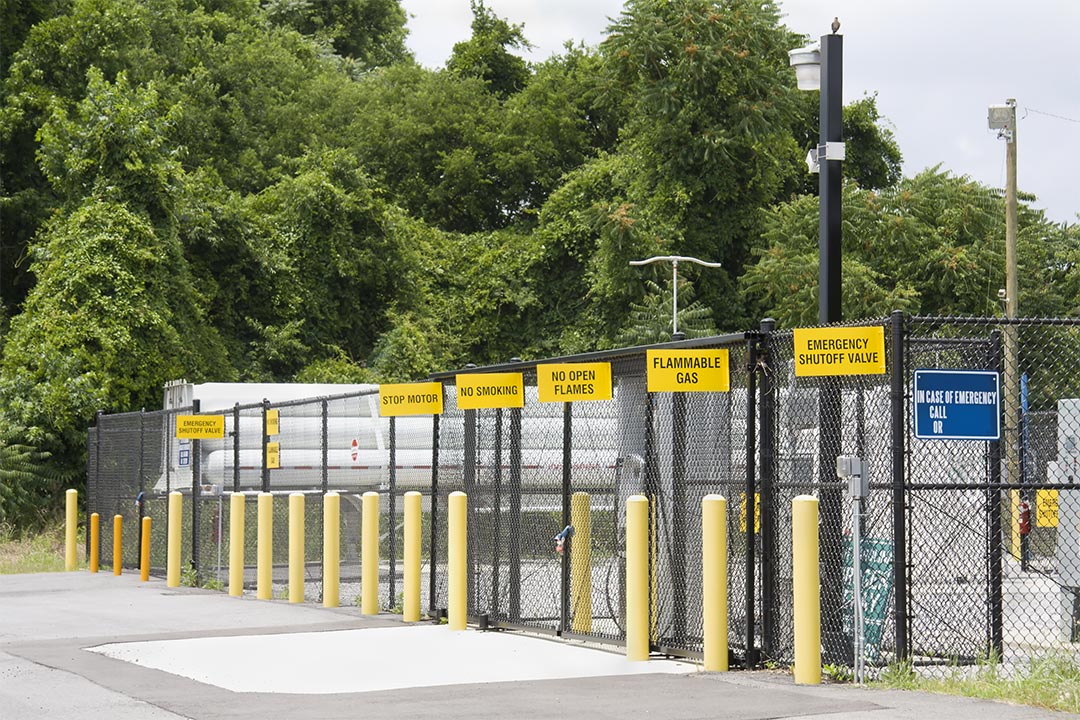
Hydrogen Safety Philosophy
Like with oxygen fire hazards, when it comes to hydrogen systems we still frequently use the “fire triangle” to effectively illustrate the three factors required for fire: fuel (hydrogen), ignition, and an oxidizer. Our primary strategies for risk management are to AVOID unintentional mixing of hydrogen and air, ANTICIPATE ignition mechanisms, and ADOPT best practices for design, operation, etc. You can read more in this article about WHA’s hydrogen risk management philosophy.
Because the energy required to ignite hydrogen is so low, it’s quite difficult to control potential ignition mechanisms with complete confidence. So instead we place great emphasis on controlling the oxidizer side of the triangle, and our primary approach to reduce hydrogen fire risk is to AVOID unintentional mixing of hydrogen and oxygen or air.
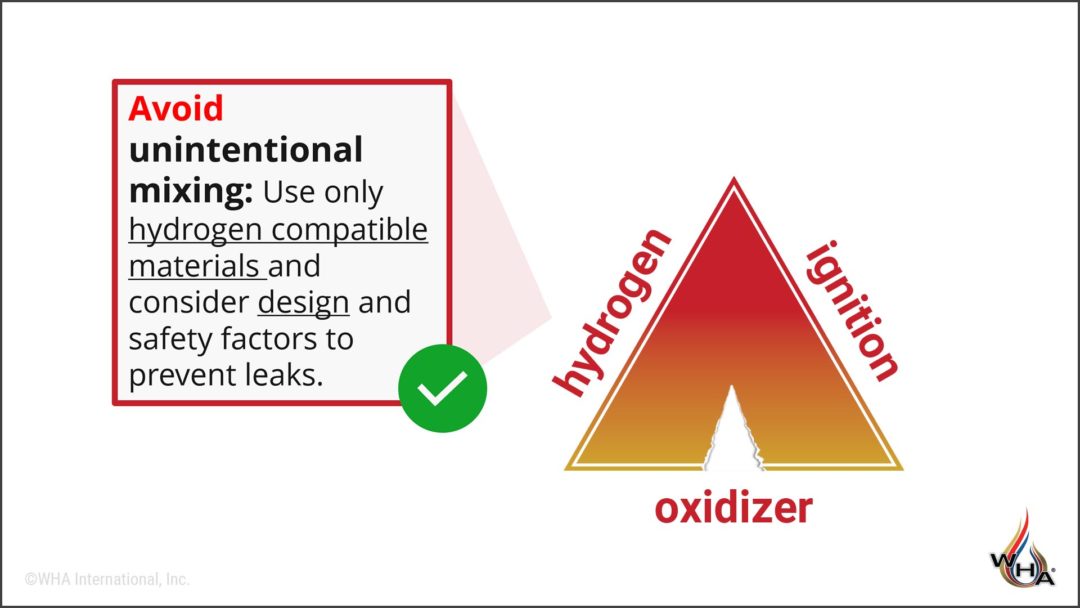
What is hydrogen compatibility?
Our first line of defense against a hydrogen fire is to prevent leaks and avoid unintentional mixing (either within the system, or with outside air). This concept provides a basic definition of hydrogen compatibility…
Hydrogen Compatibility, n — the ability of a material to exhibit reliable mechanical integrity and a low probability of leaks in a given hydrogen application (considering its environment, use, and design) within a risk parameter acceptable to the user.
In other words, a hydrogen-compatible material is one that acts as a reliable barrier between hydrogen and an oxidizer. Hydrogen risk management is often about keeping fuel contained and avoiding potential failures by using the right materials in the right ways.
This can be challenging because hydrogen has several molecular properties that create unique risks. Hydrogen’s small size and low viscosity can cause several problems, namely, its susceptibility for leakage. Tiny H2 molecules can often move through materials commonly thought to be “airtight.”
Hydrogen can also cause an effect called “hydrogen embrittlement” in metals. Atomic hydrogen can permeate into materials causing loss of ductility, cracking, and premature mechanical failure. In fact, grey, ductile, or cast iron are so extremely susceptible to embrittlement, they are generally prohibited from use in hydrogen.
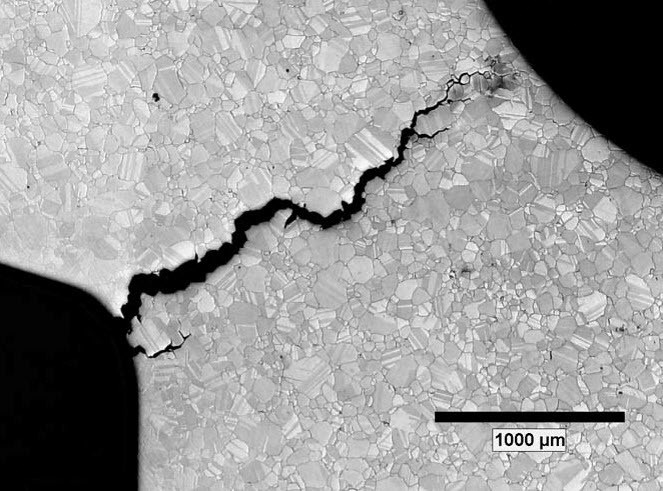
Hydrogen Compatibility Depends on Application!
The concept of hydrogen compatibility is quite complex. It relies heavily on risk management principles as we consider not just the material, but the application and design as well. As shown in the illustration below, a more complete evaluation of a material’s hydrogen compatibility includes variables like environment (pressure, temperature, and purity) as well as applied stress and a material’s susceptibility to leaks.
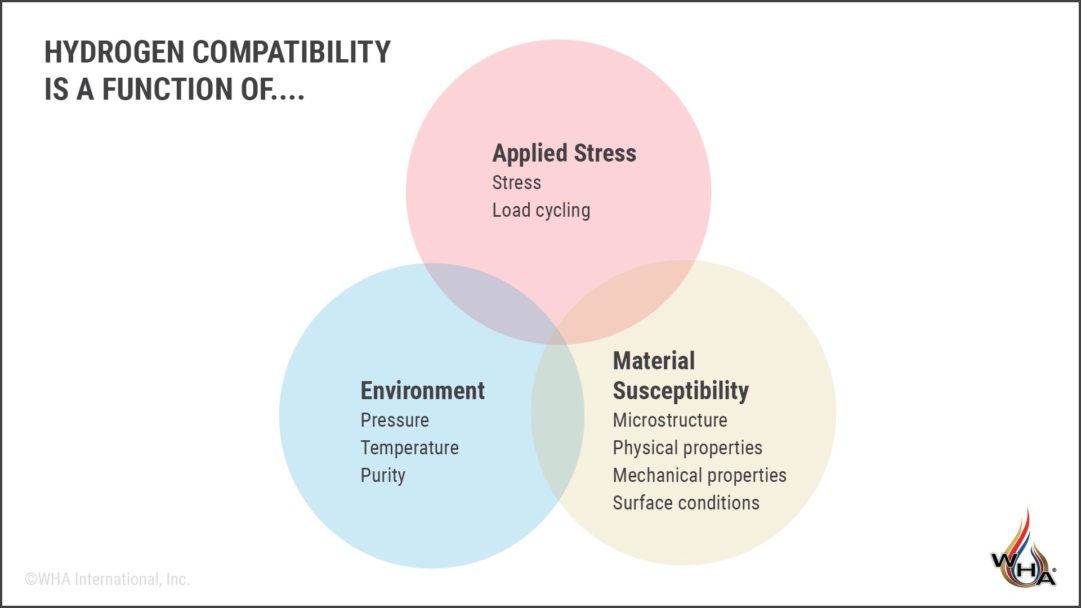
So, back to our original example, if using the wrong materials is so dangerous, how can 4130 steel safely be used for high-pressure H2 cylinders? This type of steel may typically be associated with high hydrogen embrittlement susceptibility, but with thoughtful design and application, the material has been kept within safe operating parameters. For example, appropriate cylinder thickness reduces stress on the metal, and during its lifetime, the material also undergoes relatively light cyclic load cycling. In other words, effective cylinder designs keep stresses below the point where cracks will form and extend. For these reasons, 4130 has long been considered compatible (i.e, low risk of failure) in high-pressure hydrogen cylinders.
Outside of material selection, there are many best practices for hydrogen component and system design, including minimizing the number of joints and fittings and avoiding certain types of threaded connections. To learn more, consider taking a WHA’s Hydrogen Safety Training Course or contact us to inquire about a hazard analysis review with one or our experienced hydrogen experts.
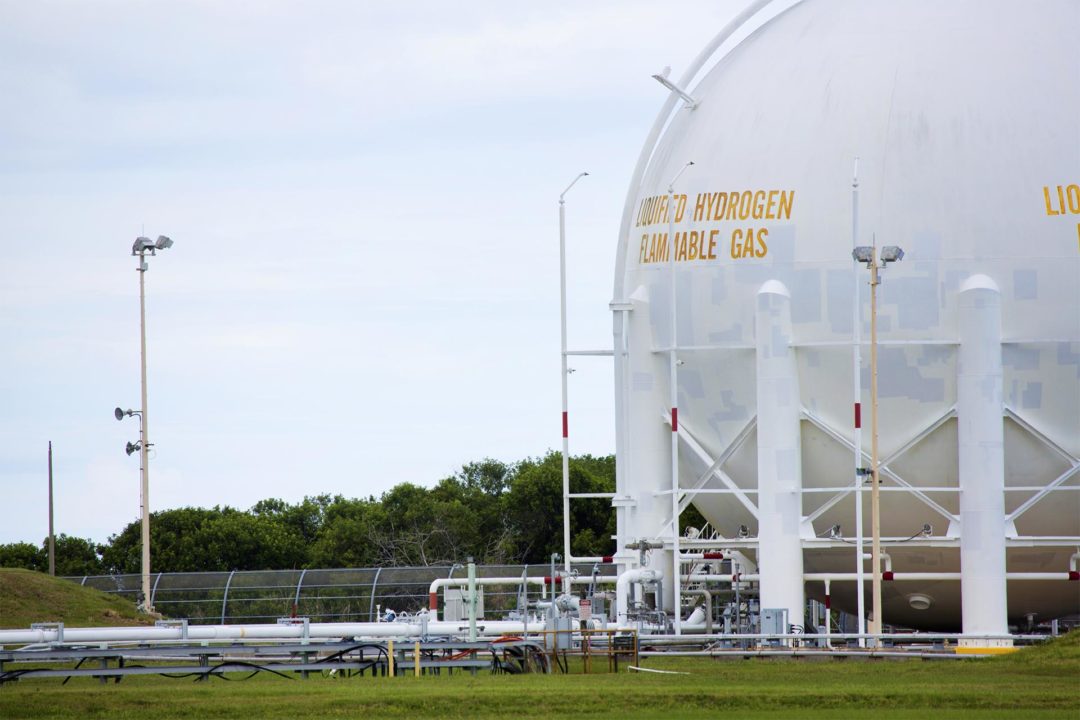
We Simplify Hydrogen Safety
The many variables involved in hydrogen materials compatibility may seem overwhelming, but we’re here to simplify hydrogen safety.
If you need to learn more about hydrogen compatibility and risk mitigation, we would be happy to arrange a consultation with one of our experienced H2 experts. Here at WHA, we support industry with a full suite of hydrogen safety services, including failure analysis, hazard analysis and design consulting, training, and custom testing.
As the hydrogen economy grows, understanding of safety must grow too. And when it comes to hydrogen, we believe industry has a responsibility not just to protect end users, but to maintain public perception as well. Fires and accidents can hinder progress for everyone.
Together, we can look forward to a safe, promising future of hydrogen technology.
Share this entry
Related Articles
Nonmetals Oxygen Compatibility Requirements: Guide to CGA/EIGA Compliance
The Compressed Gas Association (CGA) and European Industrial Gases Association (EIGA) have harmonized key documents providing guidance…
WHA Launches Oxygen Equipment Supplier Certification Program
Ignition and combustion hazards are present in almost all oxygen and oxygen-enriched systems, and catastrophic fires have…
Oxygen Cleaning Service Team Receives Vendor Award
WHA’s oxygen cleaning service team recently received recognition from its client, Trace-A-Matic, for excellent service in a…
Request an expert
consultation
Contact us to request a free consultation with an experienced engineer who can help you better understand your needs and our solutions.