Behind the scenes of WHA’s oxygen testing program
This test was performed in a controlled test environment, but imagine what could have happened if this oxygen regulator failed under real-world conditions during use! This month we’re talking to some of WHA’s test engineers to learn how oxygen testing works and why it’s so important…
Does oxygen testing always include big flames and dramatic explosions?
No, only some tests result in critical failure events. Most of our oxygen tests either result in no ignition at all or include smaller, controlled reactions that help us and our clients better understand the potential effects of oxygen on their components. Ideally, when a component performs well, there is no ignition and no fire at all.
Many materials and components have specific industry-consensus standards associated with safe use. These parameters and standard testing methods are set by global organizations like ASTM International, International Organization for Standardization (ISO), and Compressed Gas Association (CGA). Many oxygen-specific standards were actually developed with significant contribution from WHA. Our engineers actively participate in the leadership of associated committees and working groups within these organizations.

Who utilizes oxygen testing?
Component and materials manufacturers around the world depend on thorough testing to ensure their products are safe for use in oxygen systems. These pressurized systems can pose critical risks to the end user, and many of the issues are unique to oxygen fire hazards.
Around the world, project managers, design engineers, safety/quality managers, and others regularly depend on WHA International, Inc. to ensure their products are safe for use with oxygen.
“It’s not just about meeting the standards. It’s ensuring that the products are safe… We’re oxygen users too, and we protect our personnel by using components and materials with the same high level of safety in our own systems.”
Dr. Gwenael Chiffoleau, WHA International, Inc.
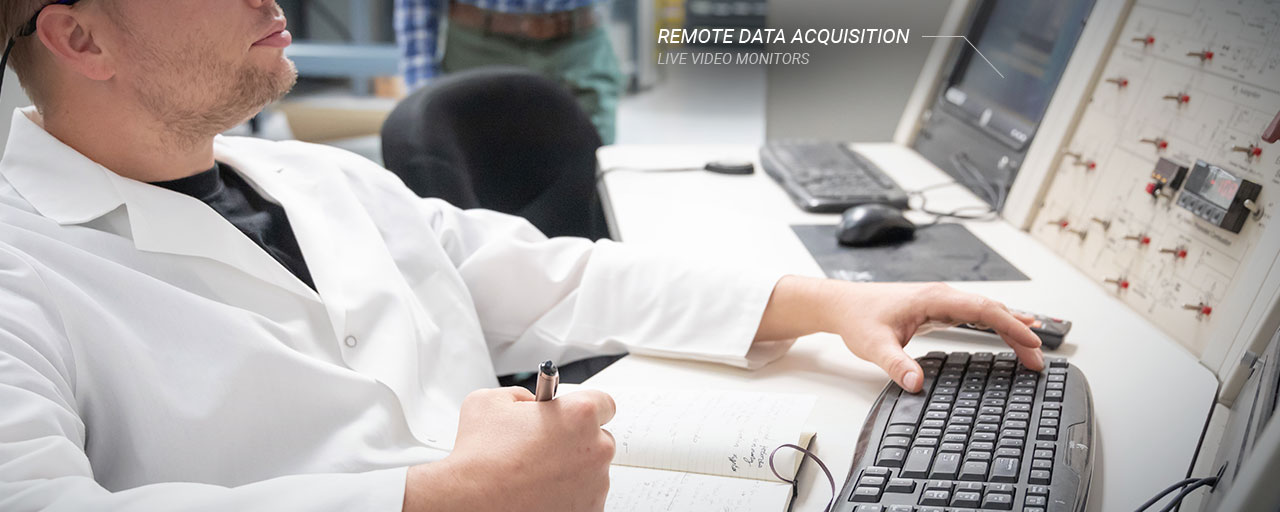
What if my components are not governed by an established standard test?
WHA often designs and executes custom tests for scenarios that are not yet governed by international standards. Like us, many of our clients also go above and beyond by setting their own internal safety standards. As industry needs change and evolve, new or adjustable methodologies are often required. In fact, several of our own custom testing methods are now widely adopted within industries as either a standard or good practice.
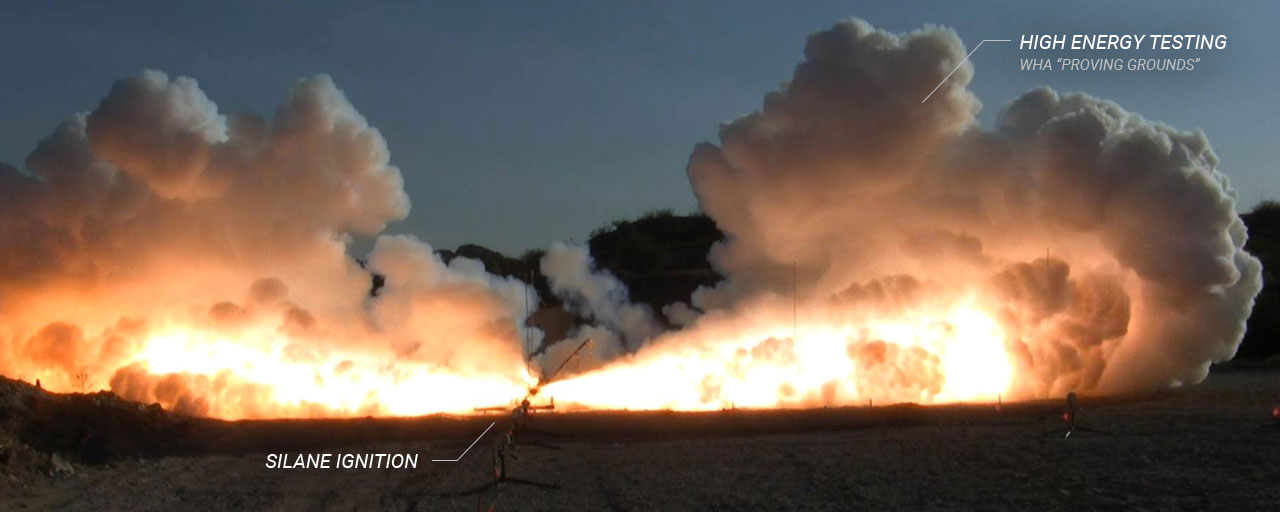
How long does testing usually take?
At WHA, we pride ourselves in fast turnaround times and an exceptional customer experience. From start to finish, our average turnaround time is 2-3 weeks, but expedited testing is also available. Our services are an important step in efficiently moving a product towards production and certification, if needed.
“Especially when dealing with product launch schedules, getting a result quickly is always desirable, so the client can get to the next step… hopefully it’s a pass situation, but if not, they want to know how and why their product failed.”
-Dr. Gwenael Chiffoleau, WHA International, Inc.
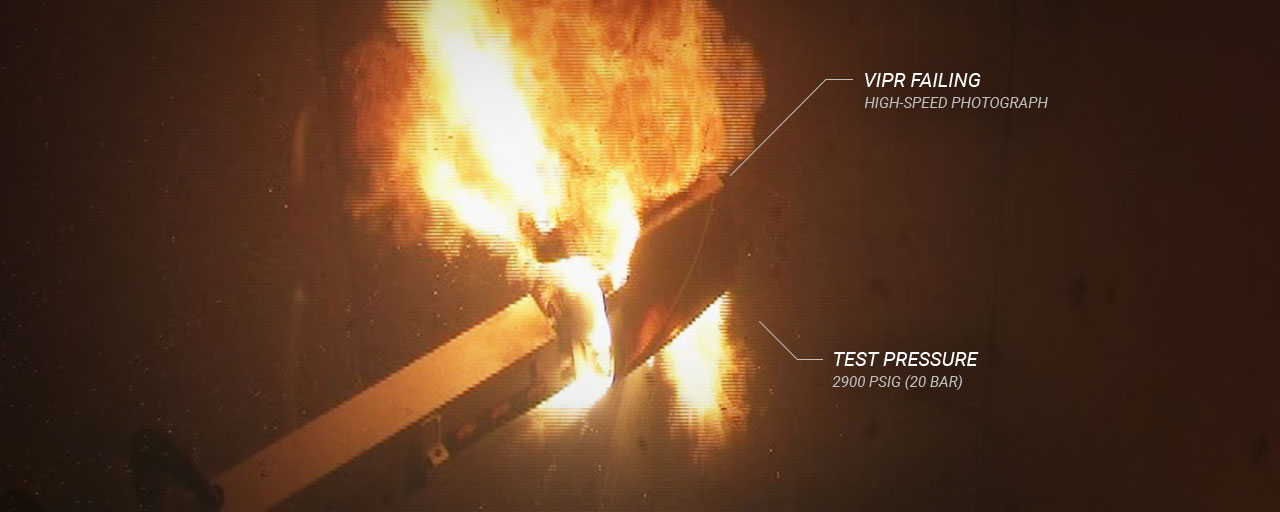
What does the testing process look like?
A typical testing project looks something like this…
- Consultation: Before work begins, we consult with our clients to make sure we understand their objectives and are performing the right test(s) for the job.
- Estimate: Next we provide a cost estimate and a proposed schedule.
- Testing: When the client is ready to go, they ship their materials or components to our labs for testing.
- Reporting: After the tests are performed, the client receives a detailed test report explaining the test process and how their product performed.
- Hazard Analysis Consulting (optional): If the client needs further guidance in order to pass their product tests and improve safety, they can always engage additional consulting services. Our experienced engineers can review design schematics and provide formal recommendations whenever necessary.
“Overall we try to hold the customer’s hand through the whole process… figuring out what they need and really making sure the statement of work meets their goals… we guide them on how to apply the results according to standards.”
Dr. Gwenael Chiffoleau, WHA International, Inc.
Share this entry
Related Articles
Oxygen Cleaning Service Team Receives Vendor Award
WHA’s oxygen cleaning service team recently received recognition from its client, Trace-A-Matic, for excellent service in a…
Oxygen Cylinder Safety
An oxygen tank, or “oxygen cylinder,” is a pressurized container that stores and transports oxygen in its…
Why clean for oxygen service?
Recently, updates were published for two important international standards that provide guidance and best practices for oxygen…
Request an expert
consultation
Contact us to request a free consultation with an experienced engineer who can help you better understand your needs and our solutions.