Nonmetals Oxygen Compatibility Requirements: Guide to CGA/EIGA Compliance
Highlights
- CGA and EIGA harmonized key documents providing guidance and requirements for nonmetals in industrial oxygen systems.
- Various oxygen compatibility tests help determine both the ignition resistance and the fire-damage potential of nonmetals.
The Compressed Gas Association (CGA) and European Industrial Gases Association (EIGA) have harmonized key documents providing guidance and requirements for nonmetals in industrial oxygen systems:
- CGA G-4.4 / EIGA Doc 13: Oxygen Pipeline and Piping Systems
- CGA G-4.14 / EIGA Doc 200: Design, Manufacture, Installation, Operation, and Maintenance of Valves Used in Liquid Oxygen and Cold Gaseous Oxygen Systems
These publications outline suggested criteria and standard tests for qualifying nonmetals for oxygen service. The industry looks to these documents for the most relevant guidelines on materials selection and system design for industrial oxygen piping systems, including the rapidly growing sector of oxygen from electrolyzers.
“The harmonized documents provide valuable compatibility requirements, but customers may be unclear as to how to achieve compliance. We want to provide guidance around what testing is required for different applications.”
Greg Odom, Senior Mechanical Engineer, Standard Testing Lead
In this article, the oxygen safety experts at WHA International Inc. outline the contents of the guidance and compliance criteria and which tests are recommended for different scenarios.
Importance of Oxygen-Compatible Materials
Using oxygen-compatible materials is not just a recommendation, it’s a crucial factor for ensuring the safety and reliability of oxygen systems. Incompatible materials can pose serious risks, leading to oxygen fires and potentially catastrophic results.
Nonmetals (e.g., plastics, elastomers, composite materials, and lubricants) can be especially vulnerable given their increased flammability and decreased resistance to ignition in oxygen as compared to metals.
Selecting materials that have been specifically tested and evaluated for oxygen use is paramount in preventing potential accidents and ensuring the integrity of oxygen systems.
Nonmetals Compatibility Test Methods
The CGA/EIGA documents reference several standardized tests to evaluate oxygen compatibility. These tests subject materials to extreme conditions of heat, pressure, and/or mechanical shock in oxygen environments to determine their ignition sensitivity and fire-damage potential.
1. Auto-Ignition Temperature (AIT) Test
This test involves subjecting the material to escalating temperatures in a controlled setting to pinpoint the exact temperature at which it auto-ignites (without an external ignition source) in high-pressure oxygen.
During the AIT test, the sample is exposed to increasing temperatures (heating rate varies between the different standards) while being monitored for signs of self-ignition. By identifying the precise temperature at which ignition occurs, researchers can evaluate the material’s ignition sensitivity when exposed to elevated temperatures in oxygen systems.
The Auto-Ignition Temperature test method is based on ASTM G72, ISO 21010, ISO 11114-3, and other standards.
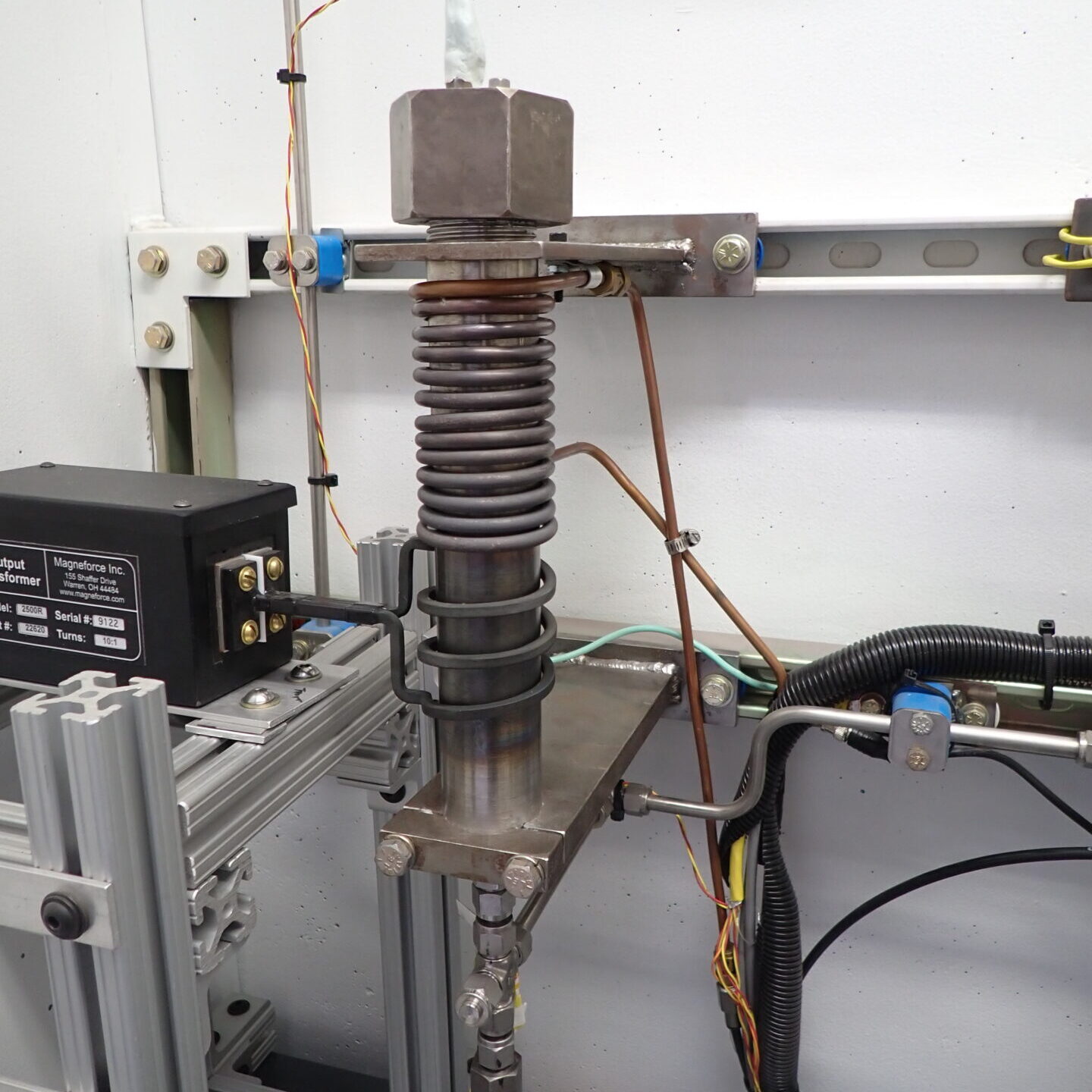
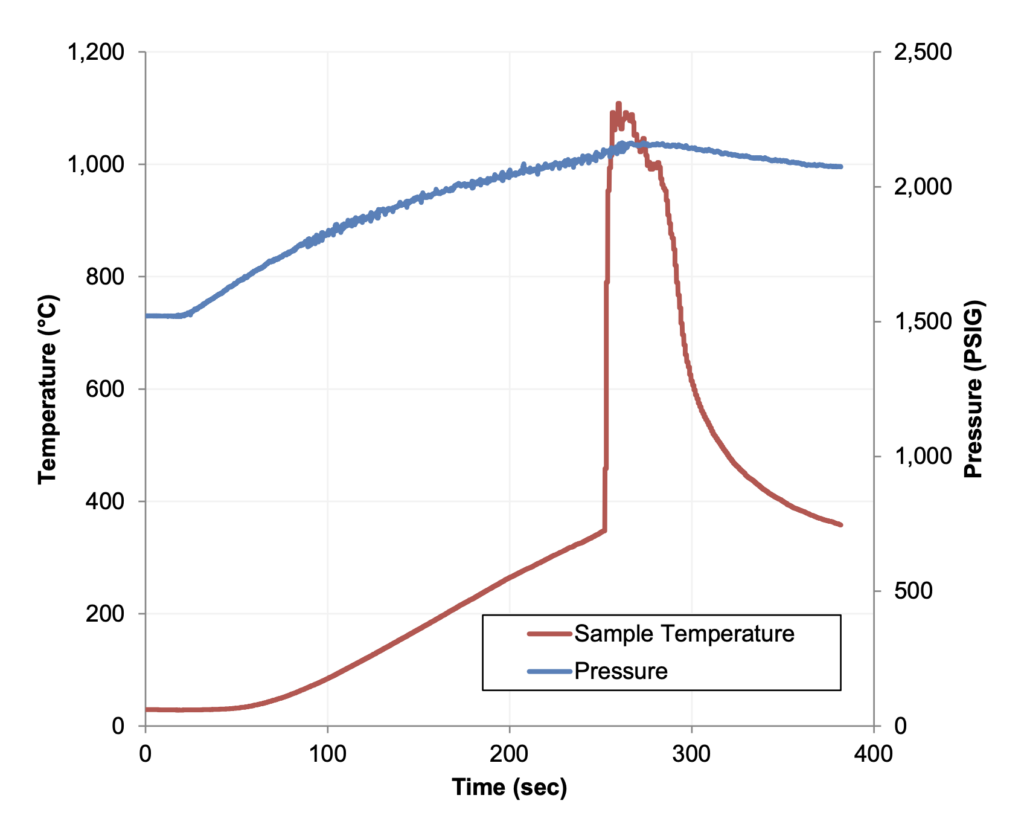
2. Liquid Oxygen Mechanical Impact Sensitivity (LOXMIS) Test
This test assesses the ignitability of materials (primarily nonmetals) in liquid oxygen (LOX), which is a cryogenic fluid at -298 °F (-183 °C, 90 °K). The test simulates the scenario where materials may be subjected to severe mechanical energy, such as impacts or vibrations, during operation in LOX.
During the test, samples of the material are immersed and chilled in liquid oxygen, typically at atmospheric pressure. They are then individually subjected to a sudden large mechanical force (impact energy can vary based on test standard, but 98 Joules is common) delivered by the impact of a 20 lb (9 kg) falling plummet. Researchers can then observe the sample’s behavior, looking for evidence of ignition via light emission, explosive-like sound release, or charring of the sample during posttest sample inspection.
The LOXMIS test method is based on ISO 21010, ASTM G86, ASTM D2512, and other standards.
VIDEO: Watch a liquid oxygen mechanical impact sensitivity (LOXMIS) test.
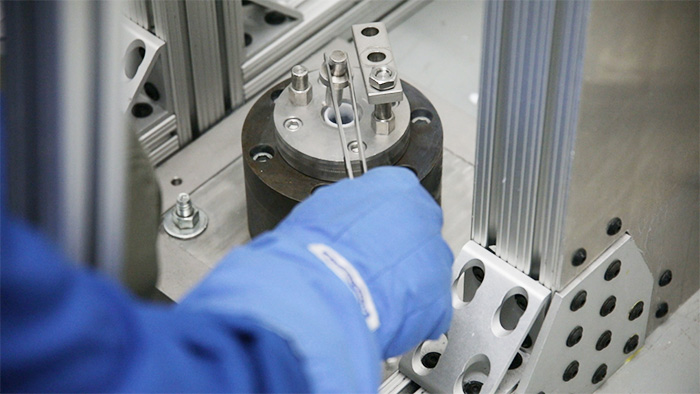
3. Pneumatic Impact Tests
Pneumatic impact testing is designed to assess the ignition sensitivity of nonmetals to compression heating that develops during an oxygen pressure surge (also known as pneumatic impact, gaseous fluid impact, or oxygen shock). This test simulates real-world conditions where nonmetals, including lubricants, may be rapidly pressurized with oxygen during system operation.
In the pneumatic impact (oxygen pressure surge) test, a sample of the nonmetal is placed in a sample cup positioned at the end of a surge tube. An upstream closed valve, holding high-pressure oxygen on its upstream side, is quickly opened to introduce oxygen to the surge tube, which causes pneumatic impact and compression heating at the sample. This mimics the transient pressurization and subsequent heating that can occur in an operational setting such as an oxygen cylinder valve rapidly pressurizing a regulator downstream, or a ball valve rapidly pressurizing a closely-coupled valve downstream. Researchers observe how the nonmetal reacts to these conditions, looking for any signs of ignition or other undesirable outcomes.
The pneumatic impact test method is based on ISO 21010, ASTM G74, and other standards.
4. Heat of Combustion Test
This test involves exposing the material to a pressurized oxygen environment while measuring the heat released during combustion. By quantifying the thermal energy produced, engineers and oxygen equipment designers can evaluate the material’s ability to initiate a kindling chain and create a larger fire within an oxygen component or system.
“Oxygen safety isn’t only concerned with preventing ignition. Combustion testing helps you understand and mitigate what might happen if an ignition does occur within a component.”
Greg Odom, Senior Mechanical Engineer, Standard Testing Lead
During the test, a sample of the material is placed in a controlled chamber filled with pressurized oxygen. An ignition source is then applied to initiate the sample’s combustion, and the calibrated test system measures the total heat generated as the material burns. The data is reported as energy release (Joules) per unit mass (g), which can then be compared to data regarding the energy required to ignite other nearby materials.
The Heat of Combustion test is performed according to the standard test method ASTM D4809.
Key Requirements for Oxygen Compatible Nonmetals
The CGA/EIGA documents provide the following guidelines for nonmetal selection intended for use in oxygen, which can be viewed as compliance requirements for industrial oxygen piping and equipment:
Step 1. Verify the mechanical and chemical suitability (other than oxygen compatibility) of the nonmetallic material based on design and operating conditions (including transient conditions).
Step 2. Review the oxygen compatibility test data available (or perform testing if unknown) considering the following guidelines for preferred nonmetals:
- Heat of combustion (HoC) is less than 2500 cal/g (4500 Btu/lb)
- Auto-ignition temperature (AIT) is at least 300°C (572°F) at a minimum test pressure of 103 bar (1500 psia) per ASTM G72, or 120 bar (1740 psia) per ISO 21010.
- AIT provides a margin of at least 100°C (212°F) above the operating temperature.
- Gaseous fluid impact or mechanical impact tests may provide helpful additional data.
- For liquid oxygen (LOX) service, nonmetals shall pass a mechanical impact (LOXMIS) test in LOX. This is a mandatory requirement.
The CGA/EIGA documents provide additional considerations for lubricants and locking compounds, which are considered compatible if the following conditions are met:
- Auto-ignition temperature (AIT) is at least 400°C (752°F) at the maximum operating pressure in gaseous oxygen or at 103 bar (1500 psia) if the maximum operating pressure is below 120 bar (1740 psi).
- Lubricants must pass a pneumatic impact test (gaseous fluid impact sensitivity or GFIS test) in gaseous oxygen at a pressure of at least 50 bar (725 psi) higher than the maximum operating pressure.
Additional Recommendations for Nonmetals in Oxygen Service
WHA also emphasizes the following recommendations from CGA G-4.14 / EIGA Doc 200:
- Because most nonmetals are flammable if ignited in oxygen service, minimize the quantity of nonmetals used
- Evaluate possible ignition by a kindling chain and take account of heat dissipation in the design by embedding the nonmetallic part in an adequate mass of burn-resistant metal (where necessary) that will act as a heat sink
- Avoid locating nonmetals directly in the gaseous or liquid oxygen flow stream, where possible
- Prevent excessive friction or mechanical impact on nonmetals
It is important to note that many factors can influence oxygen compatibility test results including, but not limited to, polymer resin quality, manufacturing, mechanical properties, porosity, impurities, and oxygen cleanliness. Therefore, WHA recommends that oxygen equipment suppliers adequately control these types of factors to ensure oxygen compatibility test results can be applied to the ongoing production of the specific material.
Furthermore, WHA recommends oxygen nonmetal suppliers test the final configuration of the material (i.e., oxygen-cleaned part) so the oxygen compatibility test results can be applied to the specific end-product.
“These tests all work together. For instance, if a material has a higher AIT, it’s less likely to ignite and more desirable in an oxygen system… but then again, you might want to look at the heat of combustion because ignition is always a possibility, and you need to understand the consequences of ignition too. We can help customers understand the test data and make recommendations based on their system’s final configuration.”
Greg Odom, Senior Mechanical Engineer, Standard Testing Lead
Are Your Nonmetals Safe for Use with Oxygen?
By conducting these tests on the final product configuration, you can navigate the oxygen compatibility requirements, select nonmetallic materials suitable for your oxygen piping system application, and ensure compliance with CGA/EIGA criteria for industrial oxygen systems.
Consult the full CGA/EIGA documents for additional details and considerations.
Contact us for additional information and to inquire about oxygen compatibility testing and other oxygen safety services from WHA International.
Share this entry
Related Articles
Nonmetals Oxygen Compatibility Requirements: Guide to CGA/EIGA Compliance
The Compressed Gas Association (CGA) and European Industrial Gases Association (EIGA) have harmonized key documents providing guidance…
WHA Launches Oxygen Equipment Supplier Certification Program
Ignition and combustion hazards are present in almost all oxygen and oxygen-enriched systems, and catastrophic fires have…
Case Study: Fire Station Medical Oxygen Cylinder Fire
A medical oxygen cylinder experienced a catastrophic failure and burnout during a routine fire station equipment check
Request an expert
consultation
Contact us to request a free consultation with an experienced engineer who can help you better understand your needs and our solutions.