Real world oxygen fire evidence underscores the need for safety
Highlights
- WHA International’s investigations of oxygen fires over the past thirty years underscore the importance of oxygen safety.
- Oxygen fires occur in many different settings, including in medical, home health, and industrial environments.
- WHA’s oxygen safety training courses utilize case studies and artifacts from real world fires to learn about oxygen safety and defend against oxygen fires.
- WHA’s findings and collaboration with organizations like ASTM and NASA-WSTF have informed new standards, materials recommendations, and industry-wide safety practices.
For thirty-five years, WHA International, Inc. has investigated oxygen fires, documenting hundreds of incidents and related fire-damaged artifacts.
Today, these investigations and their artifacts provide opportunities for our engineers and investigators to analyze and evaluate the intricacies of the fire patterns. They also offer a unique opportunity for participants in many of our technical training courses to witness real oxygen fire evidence first-hand.
While many of these incidents came at the tragic cost of human lives, their investigations resulted in better understanding and improvements in industry.
Many of them also inform industry reports and papers published through entities like ASTM International.
Below, you will find some of the artifacts and case studies from WHA that underscore the need for oxygen safety.
Oxygen regulator fire: The ignition tolerance test (per ASTM G175, Phase 2) evaluates the “fault tolerance” or ability of a component’s design and materials to handle an internal ignition. This video shows an industrial oxygen regulator test that resulted in a kindling chain and catastrophic burnout.
Incident 1: Home Oxygen Concentrator
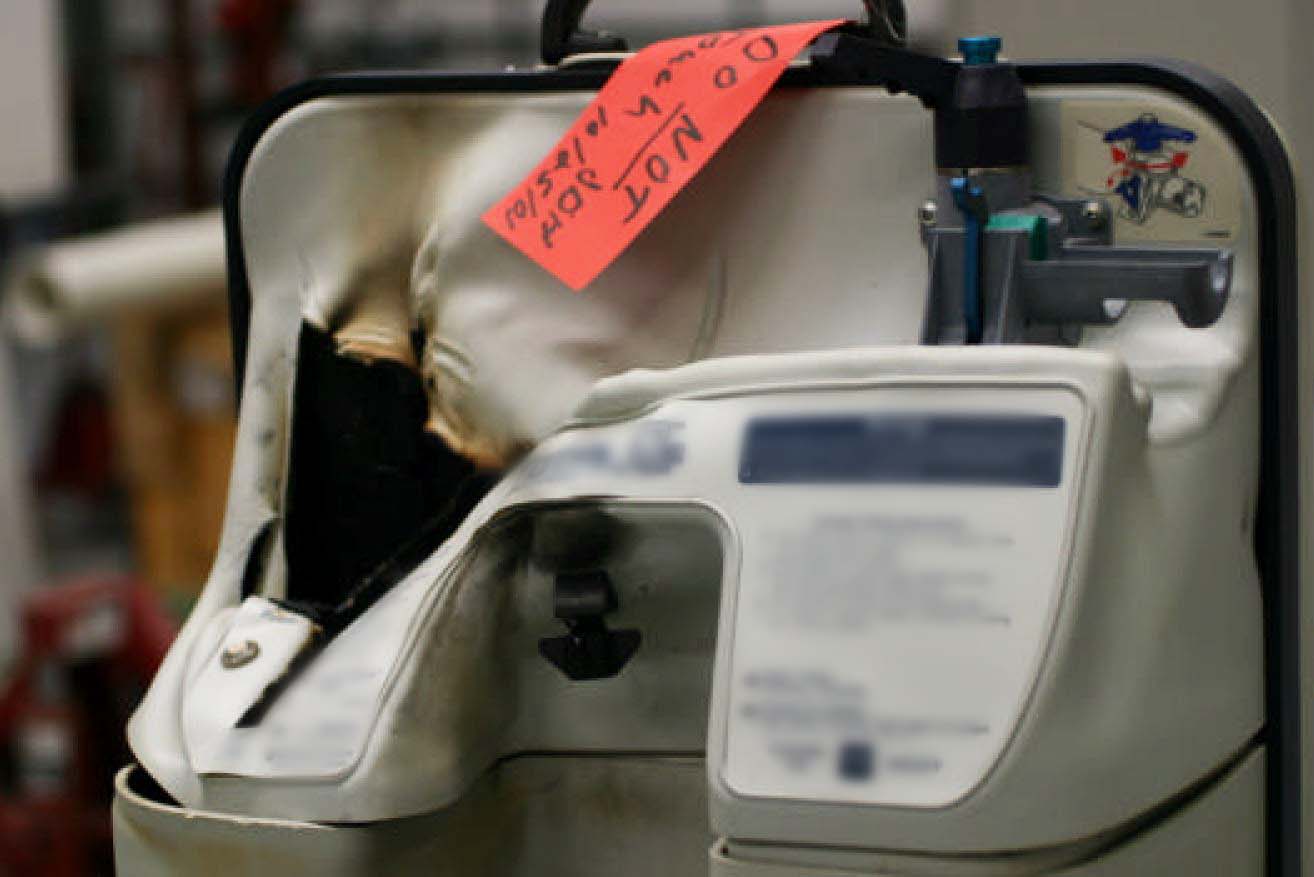
A home healthcare patient was asleep in her bedroom breathing oxygen from an adjacent room via a long canula tube connected to the pictured oxygen concentrator. She woke to the sound of a fire alarm and her dog barking and quickly discovered a fire coming from the concentrator. Thankfully, she was able to unplug the device and extinguish the residual fire with a cup of water.
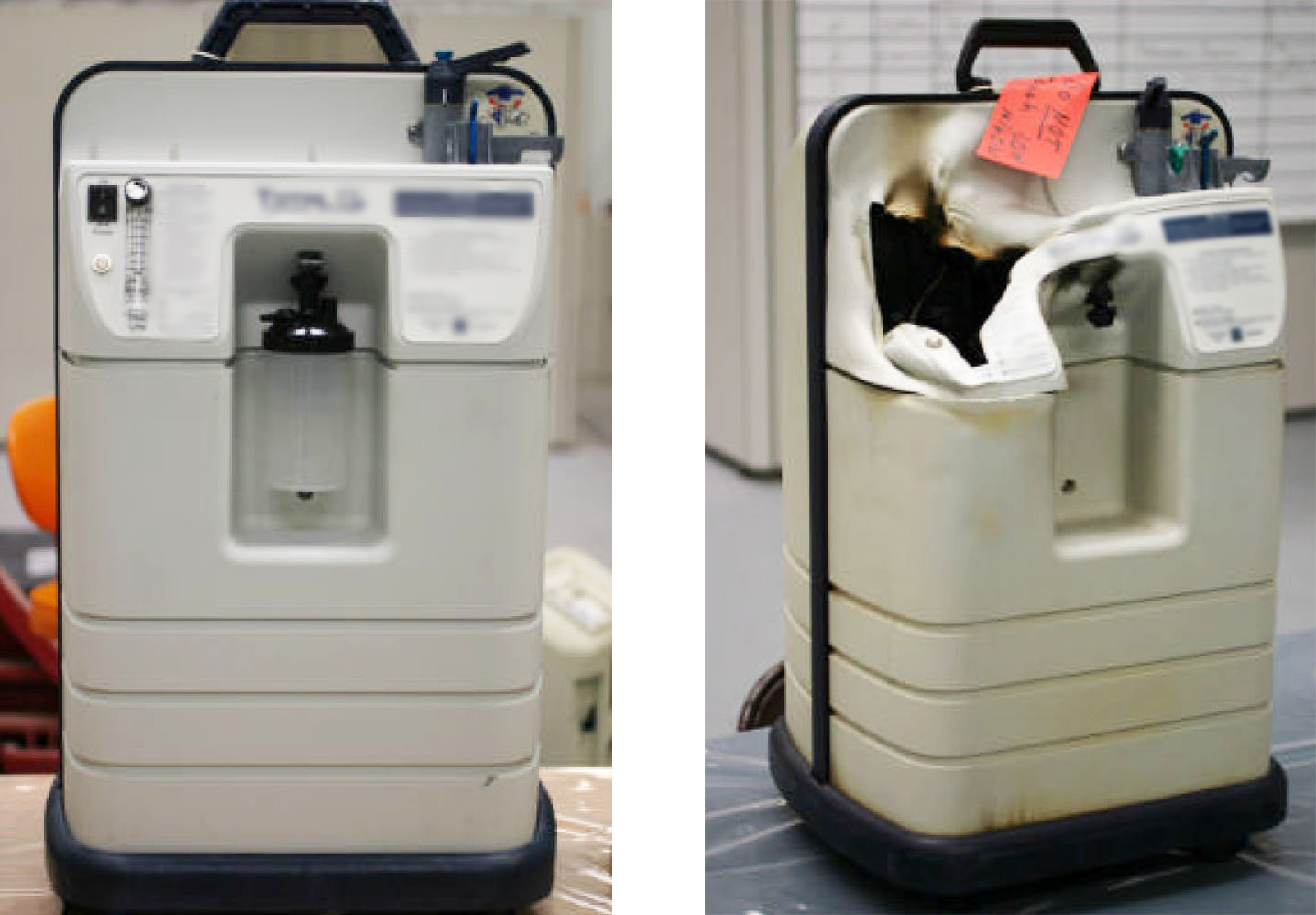
WHA received evidence from the incident to inspect for the risk of electrical fire, but evaluation, reconstruction, and testing showed that the fire originated not from internal electrical components, but from outside the device. The likely fire path was from the canula tubing, burning back through the humidifier and into the concentrator casing.
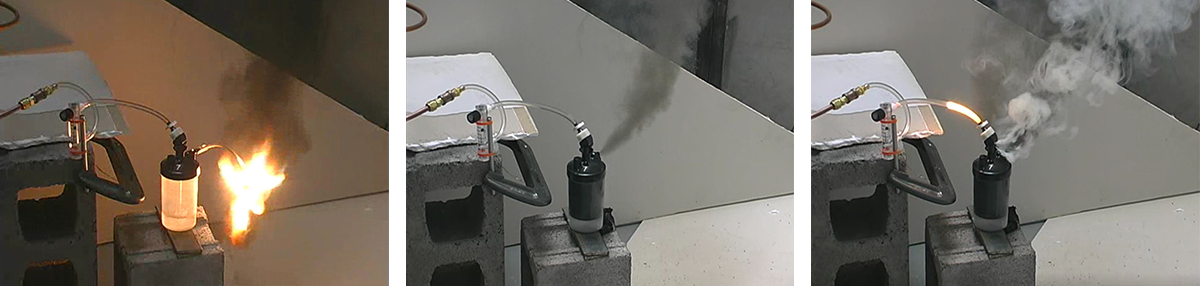
This type of fire ultimately led manufacturers to implement “fire breaks,” or sections of burn-resistant materials, in oxygen concentrators like this one. Today, fire breaks are a safety feature that can reduce the risk of fire propagation into the concentrator from external ignition sources.
Incident 2: Welding Dam Industrial Oxygen Pipeline Fire
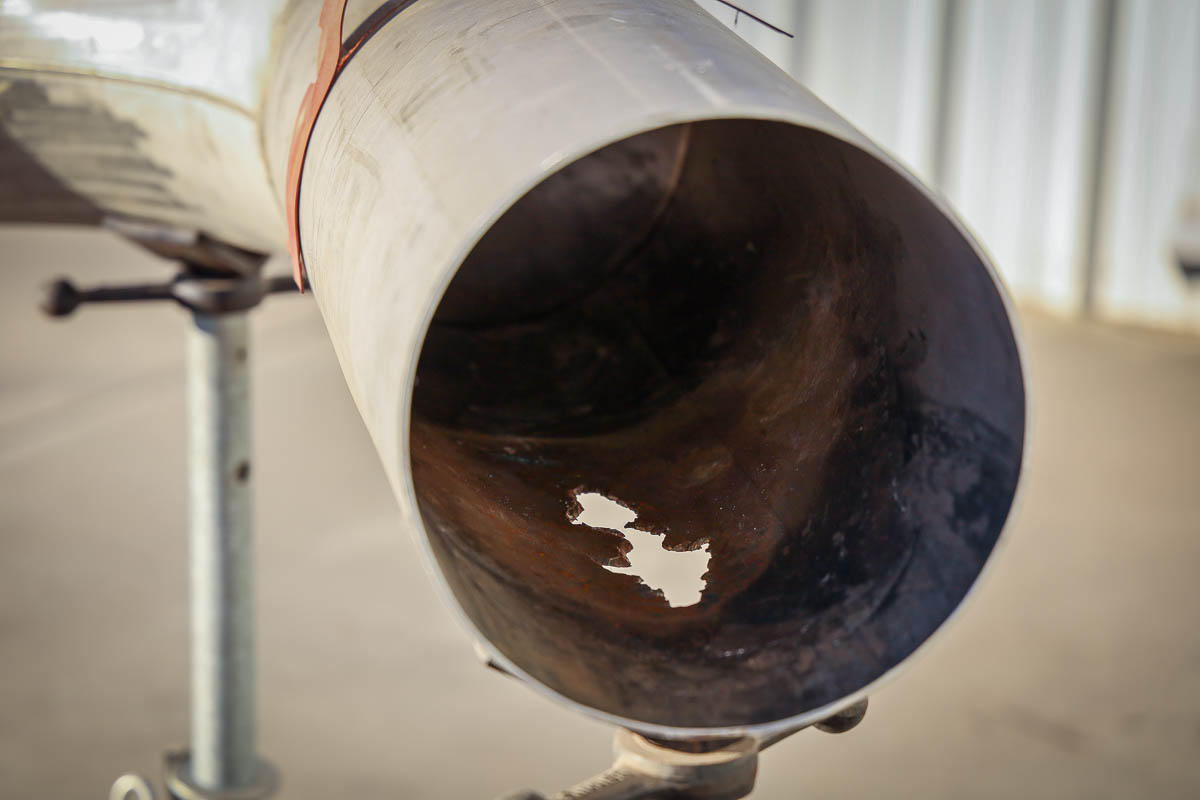
This 250 mm (10 in) stainless steel pipe was believed to be impervious to oxygen fires under its operating conditions at just 2 bar (30 psig) pressure. However, carelessness by contractors in the pipeline assembly process led to an incident. Fortunately, no one was hurt in the ensuing oxygen fire.
WHA’s investigation found a melt flow pattern with trace elements of polyurethane and nylon. This pattern, along with plywood and steel bolts and chains, indicated the presence of a welding dam left inside the pipe.
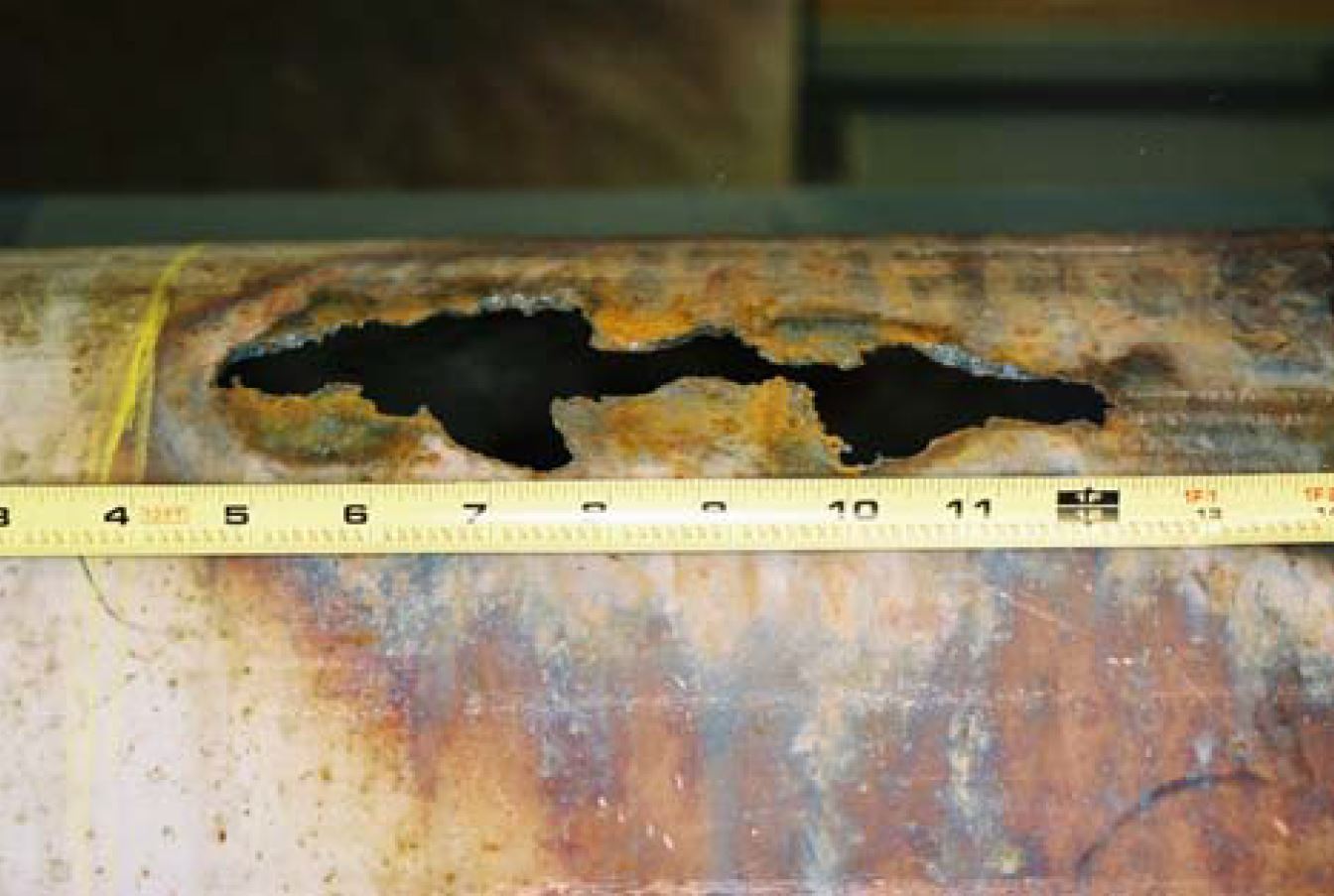
A welding dam is a piece of hardware that is placed in the pipe during welding and initial construction. The investigation concluded that the welding dam was accidentally left in the pipeline during its construction. When the pipeline underwent startup with oxygen, the dam ignited and was pushed through the piping by the gas pressure. It continued to burn as it traveled down the pipeline until it settled and burned through the piping at its resting place. Scorch marks were observed upstream of this location.
Incident 3: LOX Gate Valve Oxygen Fire
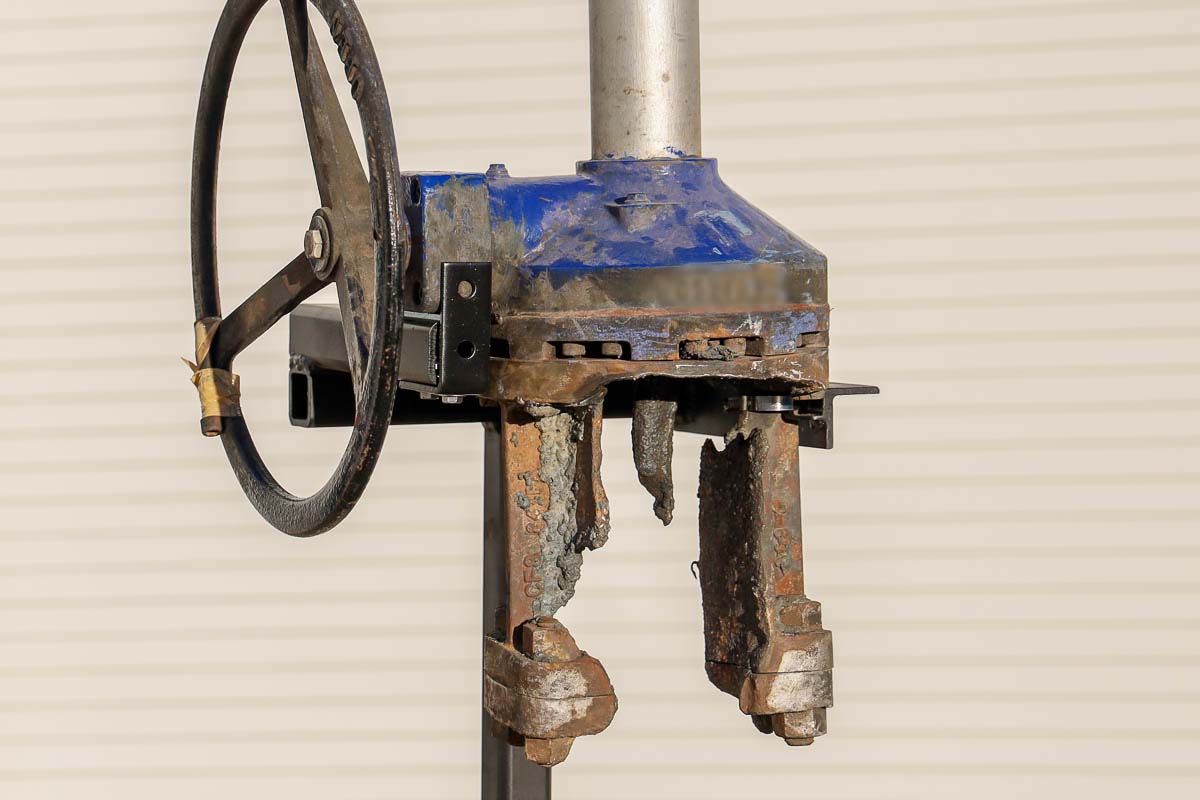
During startup of a large industrial liquid oxygen (LOX) system, this gate isolation valve experienced an internal ignition that propagated in the valve and breached the component under pressure. Tragically, the resulting fire led to the death of two operators.
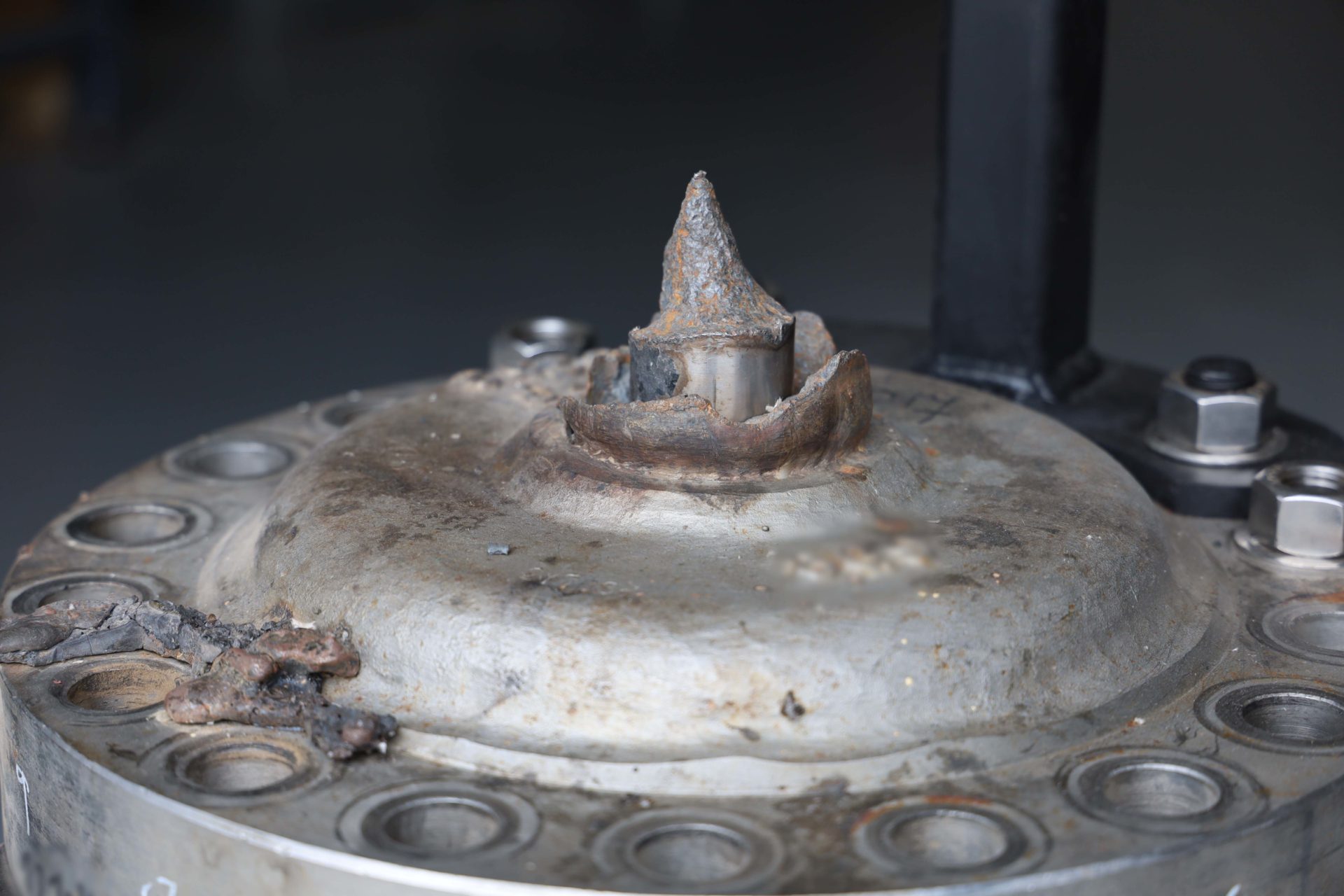
WHA’s investigation of this fire demonstrates the importance of verifying the oxygen compatibility of a material in its final state, AFTER that material has been fully manufactured. In this instance, we found that a contaminant likely used in the manufacturing of the valve’s stem packing had made its way into the valve. There, through operation and exposure to the environment, the contaminant migrated into a severe location where it ignited and produced a kindling chain that led to catastrophic burnout.
At the tragic cost of two human lives, this incident resulted in a change in industry perspective regarding oxygen safety of LOX valves.
Dive deeper: You can read more about the investigation of a similar LOX gate valve in our Case Study: Failure Analysis of a Liquid Oxygen Valve Internal Fire.
Incident 4: Industrial Ball Valve Fire
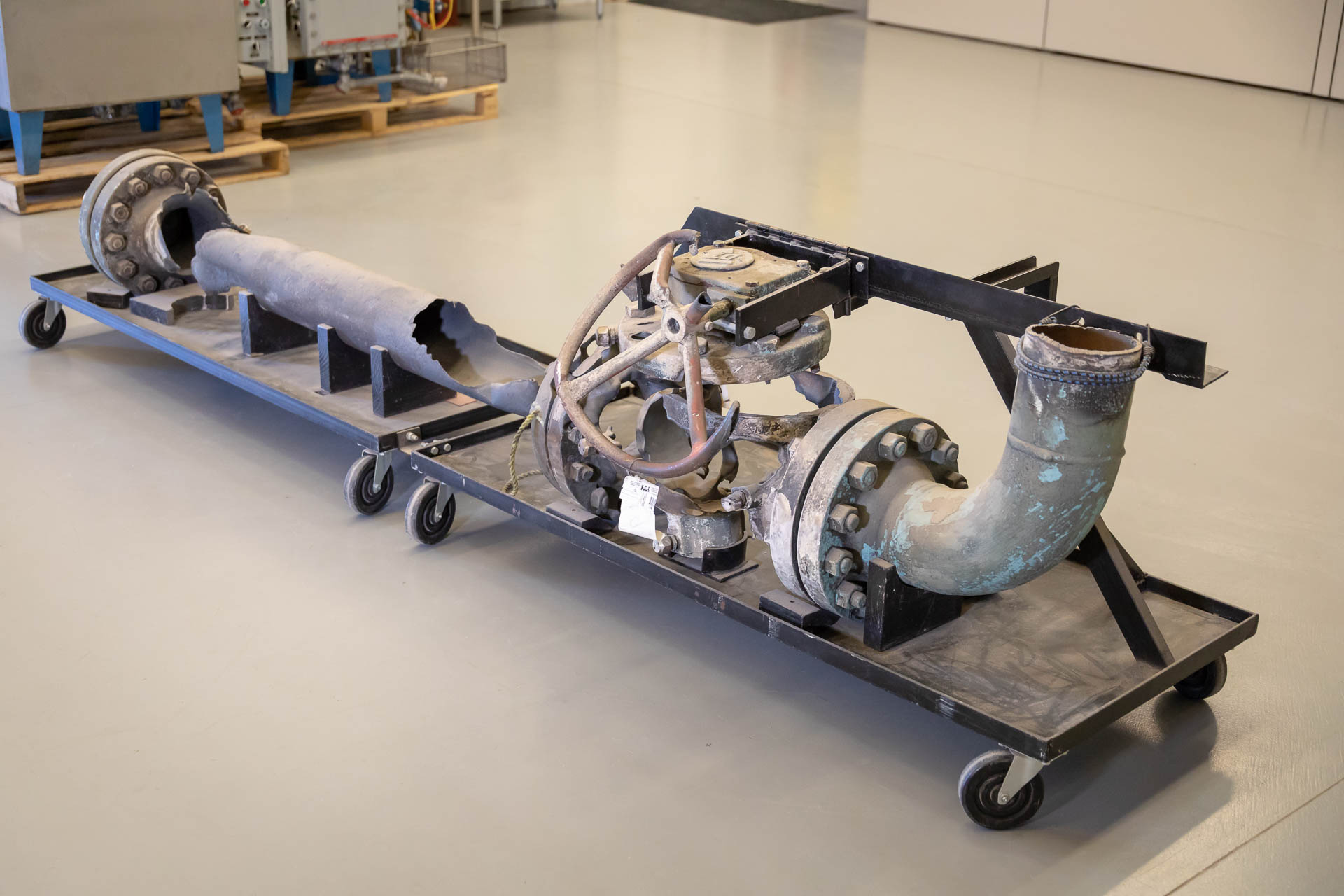
In July 2001, this 150 mm (6 in) ball valve was situated in an industrial oxygen pipeline when it experienced a catastrophic burnout, resulting in significant damage, personnel injury, and the tragic death of the valve operator.
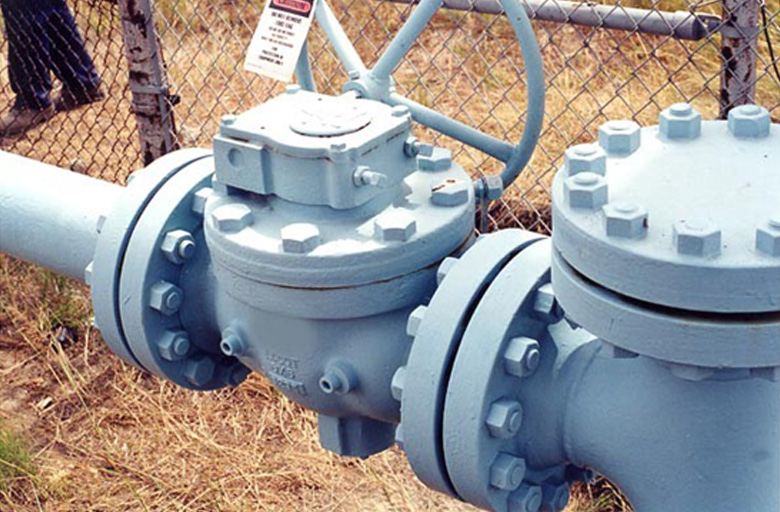
WHA was contacted to provide forensic investigation and failure analysis of the incident. The investigation identified four main contributing factors that led to the fire:
- Incorrect materials (delivery order did not match the order specification)
- Contamination (valve was not properly cleaned for oxygen service)
- Lack of visual inspection prior to assembly (no materials verification or cleanliness verification)
- Incorrect operation (valve was opened under a pressure differential, which created conditions within the valve to support ignition of the contaminants and materials of construction)
This incident demonstrates the potential for extreme fire consequences in oxygen pipeline systems if industry best practices are not implemented.
Dive deeper: Read more about our investigation in our large industrial ball valve fire case study.
Incident 5: Medical Oxygen Cylinder with Aluminum Regulator

In October of 1995, responders arrived at the site of a medical emergency call in Boone, North Carolina. They began ventilating a patient with gaseous oxygen from this high-pressure medical oxygen cylinder, and as they were preparing for transport, a catastrophic burnout occurred within the aluminum regulator. Flames and molten slag from the regulator erupted from the carrying case and engulfed the upper torso of the EMT who was carrying it.
In the late 90s, WHA investigated a total of 28 oxygen fires related to this type of aluminum oxygen regulator, the majority of which involved fire departments or emergency services. Between 1993 and 1999, 11 health care workers were burned, two ambulances were destroyed, and a fire station was damaged.
Each incident involved regulators primarily constructed of aluminum, which can be susceptible to ignition and burning under certain conditions if it is not well-protected in these high-pressure medical applications.
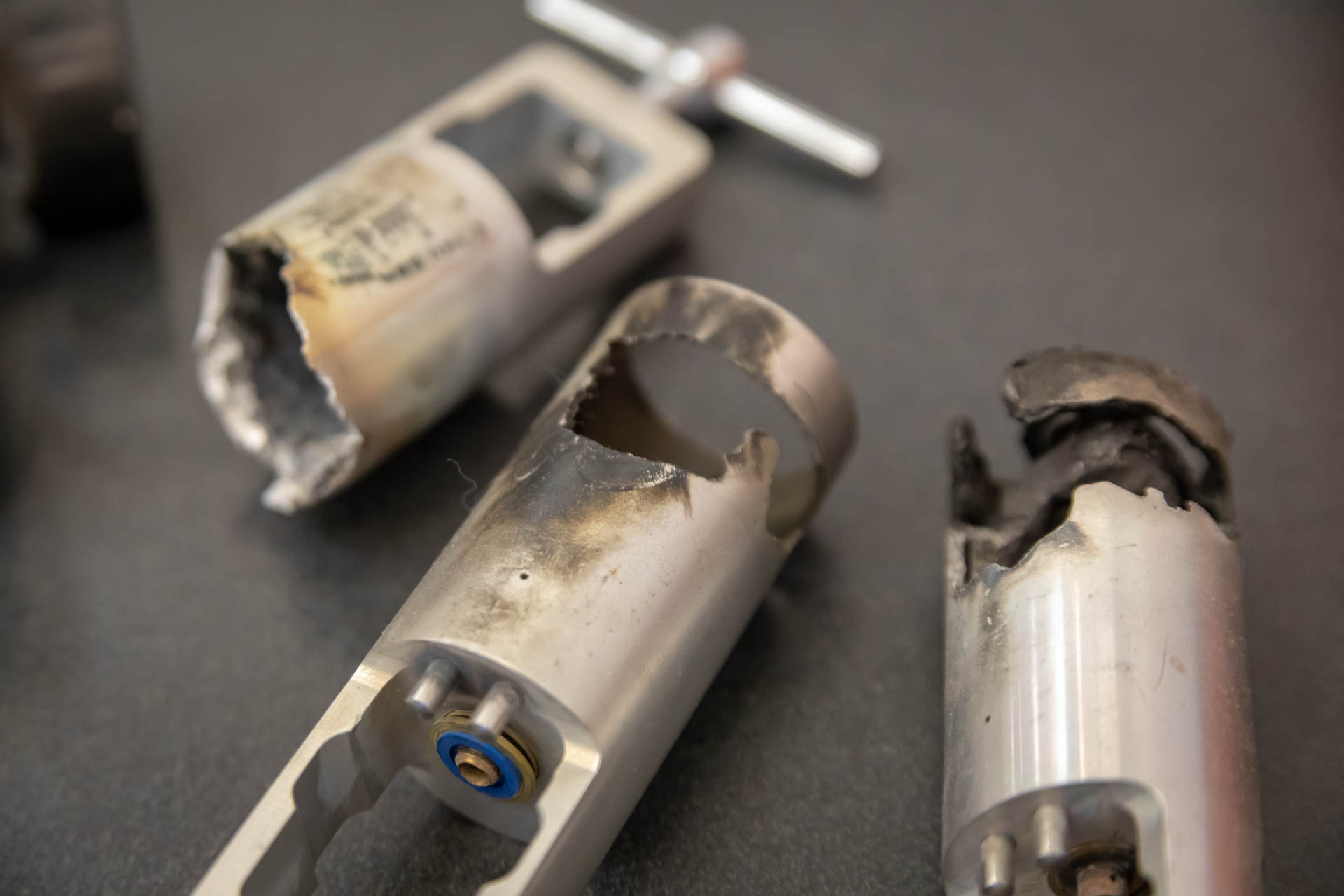
In response to these incidents, the Center for Devices and Radiological Health, a division of the US FDA, began an extensive investigation, calling on the expertise of WHA International, NASA-WSTF, and ASTM International for answers.
Ultimately, WHA engineers helped develop a new international standard for “promoted ignition” testing of medical oxygen regulators and other oxygen components. They also recommended regulator design improvements, including more oxygen compatible materials where needed.
Dive deeper: To read more about our investigation, read our medical oxygen regular research and testing case study.
Helping Industry Stay Safe Around Oxygen
At WHA International, we use the latest tools and decades of experience to help our clients understand and manage hazards and fire risks associated with oxygen, hydrogen, and other hazardous fluids. Our technical services help industries make intelligent decisions that could save lives. Although some of these incidents are sobering, they help us understand the impact and magnitude of real-world oxygen fire events.
We hope these incidents serve as a reminder for the need for industry best practices related to oxygen, including materials and design practices, proper cleaning, inspection, assembly, operations, and related training.
To take preventative safety measures in your own setting, make sure to look into our oxygen safety training. WHA’s engineers, with more than 35 experience in oxygen fire safety expertise, have designed and led these trainings.We also invite you to explore our oxygen safety services, including oxygen failure analysis, hazard analysis, testing, and cleaning.
Originally published November 23rd, 2021.
Share this entry
Related Articles
Battery Safety Insights with Nic Linley, Electrical Engineer
Battery technology continues to evolve rapidly in the 21st Century, powering an expanding array of devices and…
Oxygen Cylinder Filling System Fire Case Study
Oxygen cylinders and pressure systems quietly hold enormous amounts of energy. When things go wrong, the results…
WHA Presents O2 Safety Papers at 2024 ASTM G04 Symposium
In October 2024, Gwenael Chiffoleau, Nic Linley, and Brent Houser traveled to Prague for the 16th ASTM…
Request an expert
consultation
Contact us to request a free consultation with an experienced engineer who can help you better understand your needs and our solutions.