Oxygen Cylinder Safety
Highlights
- Before using an oxygen cylinder, make sure to receive proper safety training relevant to your situation, and follow best safety practices.
- Millions of oxygen cylinders are used safely around the world every day, but they need to be handled with care since materials can ignite more easily and burn rapidly in the presence of oxygen.
- Follow the oxygen cylinder safety precautions below when handling gaseous oxygen (GOX) cylinders — and follow WHA’s oxygen safety training if you need more thorough training for industrial settings.
An oxygen tank, or “oxygen cylinder,” is a pressurized container that stores and transports oxygen in its compressed form. Many different industries use oxygen cylinders — including medical, manufacturing and construction, aviation, scientific research, and emergency services.
Oxygen cylinders must be handled with care. Why? All compressed gas cylinders contain high-pressure contents. If dropped and damaged, an air cylinder can take off like a rocket.
But gaseous oxygen cylinders (GOX cylinders) that contain pure, highly pressurized oxygen present unique hazards as well. They come with a risk of fire, since oxygen supports the combustion of other materials. As a result, GOX cylinders require special handling and operating practices that differ from other compressed gasses.
“Many people don’t realize that oxygen cylinders require unique safety measures. A welder, for instance, may have two compressed gas cylinders side-by-side, oxygen and acetylene, but each must be handled and operated very differently.”
Elliot Forsyth, WHA Engineer
A Note on Medical Oxygen Cylinder Safety at Home
This guide mainly discusses handling oxygen cylinders by industrial personnel and experienced healthcare practitioners. If you need to handle medical oxygen at home, make sure to receive proper training from your healthcare provider and follow recommended safety procedures.
For an overview of general safety procedures for oxygen use in home settings, see the home oxygen fire safety handout from the New York State Office of Fire Prevention and Control.
Oxygen Safety Fundamentals
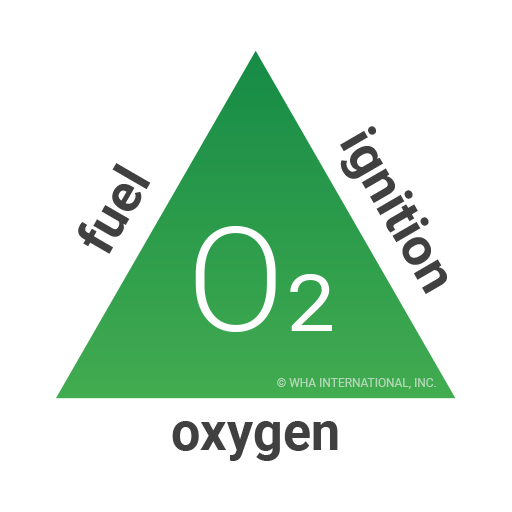
Before we get into the “how” of safely handling oxygen, let’s cover a few oxygen safety basics.
The best way to remember oxygen safety practices is to recall the “fire triangle” illustration that many of us learned about in science class. The fire triangle has three sides which, at the most basic level, remind us there are three factors that all must be present for a fire to occur: oxidizer, fuel, and ignition.
In a compressed oxygen cylinder, pure oxygen gas is the oxidizer, not the fuel – it is not a flammable gas and will not ignite or burn by itself. Instead, oxygen works to make materials (fuels) more flammable and easier to ignite. It is one of three primary elements required for a fire to occur.
Oxygen makes up almost 21% of our atmosphere, which is not necessarily a high concentration. But it’s high enough that many materials can ignite and burn in the presence of an energy or heat source.
However, as oxygen pressures and concentrations increase, nearly all materials will ignite and burn more easily than they do in air. Even the stainless steel components of a regulator can ignite and burn with the ample oxidizer (high concentrations of oxygen) present within a compressed oxygen cylinder. The basic philosophy behind oxygen safety, therefore, is to reduce risk by limiting potential ignition and/or fuel sources in the given oxygen environment.
Oxygen Cylinder Safety
Common oxygen hazards that require careful attention include:
- Contaminants like oils and greases (hydrocarbon-based): These may seem harmless in ambient air, but they become extremely dangerous fuels in the presence of oxygen.
- Small particle contaminants: Metal shavings and other small debris can accelerate and ignite upon impact in compressed oxygen, providing both the fuel and the ignition source to start a fire.
- Fast pressurization: Certain valve styles (i.e. ball valves and cylinder valves) open quickly and can rapidly pressurize systems with compressed oxygen, creating sufficient heat to ignite certain materials and cause a fire.
The safe use of oxygen also includes concepts such as reducing fire consequence by minimizing personnel exposure (i.e. standing to the side of a valve while opening) and limiting the kindling chain of potential fuels that could propagate a small ignition into a large fire.
Keep important safety information on-hand. Download our free poster on oxygen cylinder safety.
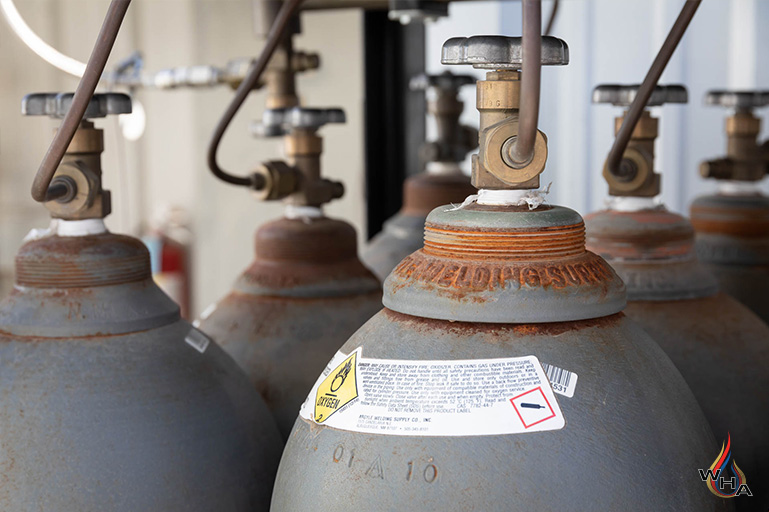
GOX Cylinder Features that Affect Handling
GOX cylinders are typically fitted with a stand-alone cylinder valve or a valve-integrated pressure regulator (VIPR).
Stand-alone cylinder valves are designed to be connected to a stand-alone regulator or a manifold and require special handling, as outlined below.
VIPRs require fewer steps because the cylinder valve and regulator are combined in one device. Still, users must follow manufacturer instructions and particularly avoid contaminating the ports of the VIPR, especially the fill port.
Best Practices for Handling and Using Compressed Oxygen Cylinders with Cylinder Valves
Now, let’s go through the oxygen safety procedures for compressed oxygen cylinders that use cylinder valves.

Step 1. Inspect Your Equipment
Always assess your equipment before using an oxygen cylinder. To safely inspect your equipment:
- Only use oxygen cylinders if experienced and properly trained
- Wear approved personal protective equipment (PPE) including safety glasses
- Identify the product from the cylinder label
- Ensure no oils or greases are present on hands, gloves, or equipment
- Ensure no potential heat sources or points of ignition are nearby
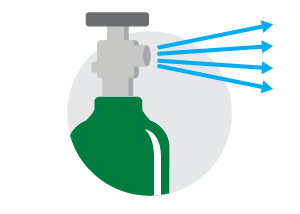
Step 2. Clear Cylinder Valve
Next, you need to inspect and “clear” the cylinder valve.
- First REMOVE PROTECTIVE CAP just prior to cylinder use. (Always keep the protective cap in place when not in use.) Remove any plastic wrapping and ensure no loose pieces remain in the valve outlet.
- Visually INSPECT the cylinder valve outlet for debris (If contaminated, DO NOT OPEN the cylinder valve. Instead, RETURN to the vendor.)
- STAND to the side of the cylinder, and point valve away from personnel and equipment.
- BRIEFLY OPEN the valve for an instant to clear potential debris.
- CLOSE valve. (Do not over-torque cylinder valve.)
- RE-INSPECT cylinder valve outlet for debris. (If contaminated, DO NOT use cylinder valve. Instead, RETURN to vendor.)
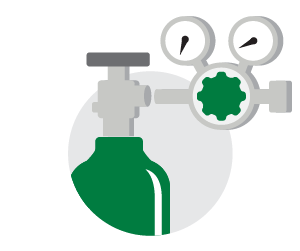
Step 3. Assemble Components
Next, it’s time to assemble the components for the oxygen cylinder.
- Always visually INSPECT the CGA-540 fitting before assembling any oxygen component to the cylinder valve, including regulators, flexible hoses, “pigtail” tubing, or other equipment. DO NOT use components if contaminated with debris.
- WHA recommends that the inlet be fitted with a SINTERED ELEMENT FILTER to protect the regulator from debris.
- Securely CONNECT the fitting to the cylinder valve outlet.
- ENSURE the regulator is fully reduced (i.e. closed).
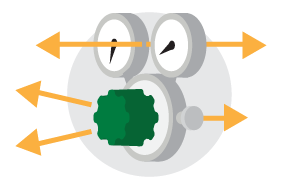
Step 4. System Start-Up
System start-up is one of the most critical steps in using an oxygen cylinder due to the risk of an oxygen fire.
It’s important to note that oxygen cylinder valves have different construction and application from oxygen regulators. Cylinder valves are designed only for “isolation” purposes. As such, they should be operated either completely open or closed. Never partially-open an oxygen valve and leave it to “throttle” or control flow. Although it’s extremely rare, this improper operation can lead to ignition of the plastic valve seat.
- STAND to one side and not in front or behind regulator when opening cylinder valve.
- Although there is a low probability of fire, STAY OUT of potential fire path when opening the cylinder valve (see illustration).
- SLOWLY OPEN cylinder valve. (If audible leaks occur, CLOSE valve immediately.)
- To open most oxygen cylinder valve designs, “backseat” the stem on the packing (open all the way), then back ¼-turn. This helps keep the valve from sticking (and possibly appearing to be closed to other users).
- To close, don’t overload (over-tighten) the plastic valve seat. This can cause excessive wear and damage the valve seat, limiting durability and, more importantly, creating flammable plastic fibers inside the component. A good “rule of thumb” is to stop applying torque when the valve “feels” closed.
- INSPECT gauge to ensure adequate pressure. (DO NOT use cylinders below 25-100 psi (170-700 kPa).)
- DO NOT approach regulator or gauge until above steps have been performed.
- Perform LEAK CHECK with compatible fluids on all required fittings. (If leaks occur, CLOSE cylinder valve, vent pressure, repair leaks.)
- If no leaks, INCREASE (i.e. open) regulator to initiate flow.
“One of the most important things we teach about proper handling of oxygen cylinders is related to operation of the cylinder valve. Always remember to open SLOWLY but open FULLY.”
Elliot Forsyth, WHA Engineer
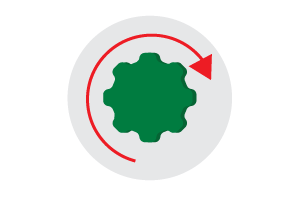
5. System Shut-Down
Oxygen cylinders should never be emptied completely. Most suppliers recommend keeping pressures above 25-100 psig at all times. To shut down the system properly:
- CLOSE the cylinder valve when the work is complete. (DO NOT over-torque)
- VENT regulator to ambient pressure.
- FULLY REDUCE (i.e. close) regulator.
If cylinder is empty (<25-100 psig):
- DISCONNECT the CGA 540 fitting.
- REPLACE the dust cap/plug (if present on the flex hose).
- REPLACE the protective cylinder cap.
- LABEL the cylinder “EMPTY”.
- STORE empty cylinders separately from full cylinders.
- RETURN cylinders promptly to the supplier.
Further Your Oxygen Cylinder Safety Training
While these instructions can serve as a refresher, keep in mind that ALL users of oxygen cylinders should not only have a basic understanding of oxygen fire hazards, but also be trained in their proper use.
That’s why WHA’s engineers have developed a series of in-depth oxygen training courses — from introductory awareness to expert application. In Level 1: O2 Aware, trainees learn how to operate and maintain oxygen systems safely.
As long-time industry leaders in oxygen safety, oxygen failure analysis, and oxygen fire risk analysis (OFRA), WHA’s engineers will give you the knowledge and confidence to handle oxygen systems safely.

The engineers who design and lead the training courses are industry experts who regularly contribute to international standards organizations like ASTM, CGA, ISO, and more.
Your safety — and the safety of others — is too important to ignore. By following oxygen cylinder safety precautions, you’re doing your part to prevent oxygen fires.
Originally published March 27th, 2019.
Share this entry
Related Articles
Oxygen Cleaning Service Team Receives Vendor Award
WHA’s oxygen cleaning service team recently received recognition from its client, Trace-A-Matic, for excellent service in a…
Oxygen Cylinder Safety
An oxygen tank, or “oxygen cylinder,” is a pressurized container that stores and transports oxygen in its…
Will hydrogen power the future of Aerospace?
As the world moves towards clean energy technologies, finding alternatives to traditional fuels is particularly challenging in…
Request an expert
consultation
Contact us to request a free consultation with an experienced engineer who can help you better understand your needs and our solutions.