Apollo 1 and the Tragic Beginnings of Oxygen Safety
Prior to 1967, oxygen hazards were generally known, but relatively unexplored. Everything changed following the tragic death of NASA’s Apollo 1 crew members who were trapped in an oxygen fire during a routine launch rehearsal test.
We recently sat down with WHA CEO Dr. Barry Newton to learn more about this historic event and how it continues to shape forensic analysis and the science of safety today.
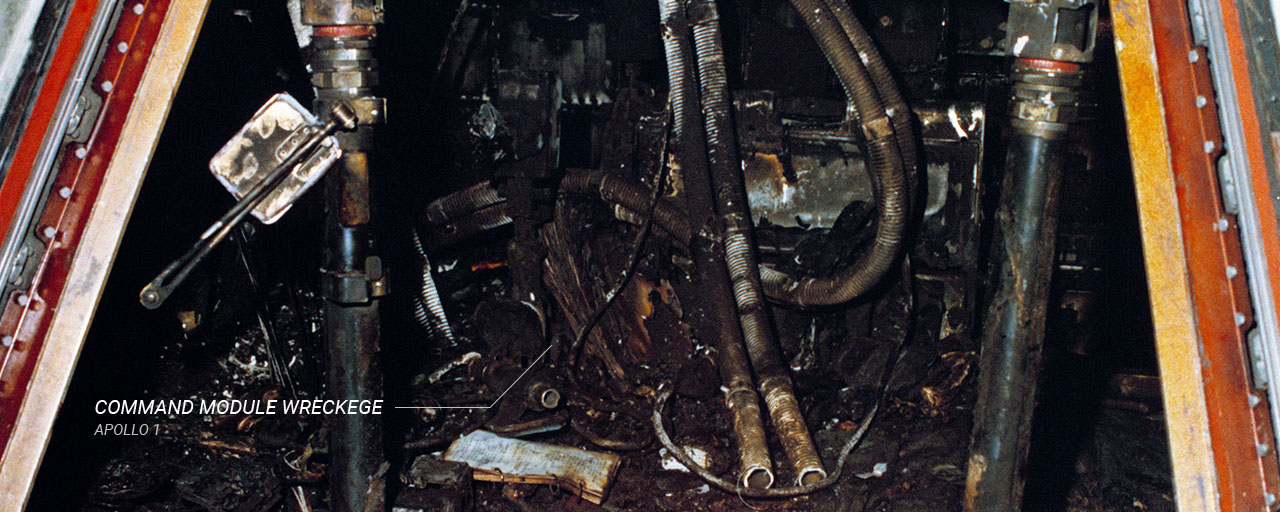
What went wrong with Apollo 1?
Originally, the “plugs-out” launch rehearsal test was classified as “non-hazardous,” because rocket fuel was not involved[1]. Three astronauts, Edward White, Virgil “Gus” Grissom, and Roger Chaffee, were scheduled to practice an entire countdown sequence while seated in the Saturn Command Module on the launch pad.
Tragically, following indications of a power surge, the crew alerted of a “bad fire” over the radio. By the time technicians were able to open the hatch roughly five minutes later, all three astronauts had perished. What began as a routine test ended in unthinkable tragedy. Clearly something had to change.
Following an extensive investigation, NASA determined that the incident was likely caused by an electrical arc from a short-circuited wire. The fire quickly became deadly because the flammable materials throughout the capsule were surrounded with 100% oxygen at a pressure just over atmospheric (slightly elevated).
Furthermore, the astronauts’ escape was significantly delayed by a hatch design that was overly-complicated and incapable of opening inward while the cabin was pressurized.[2]
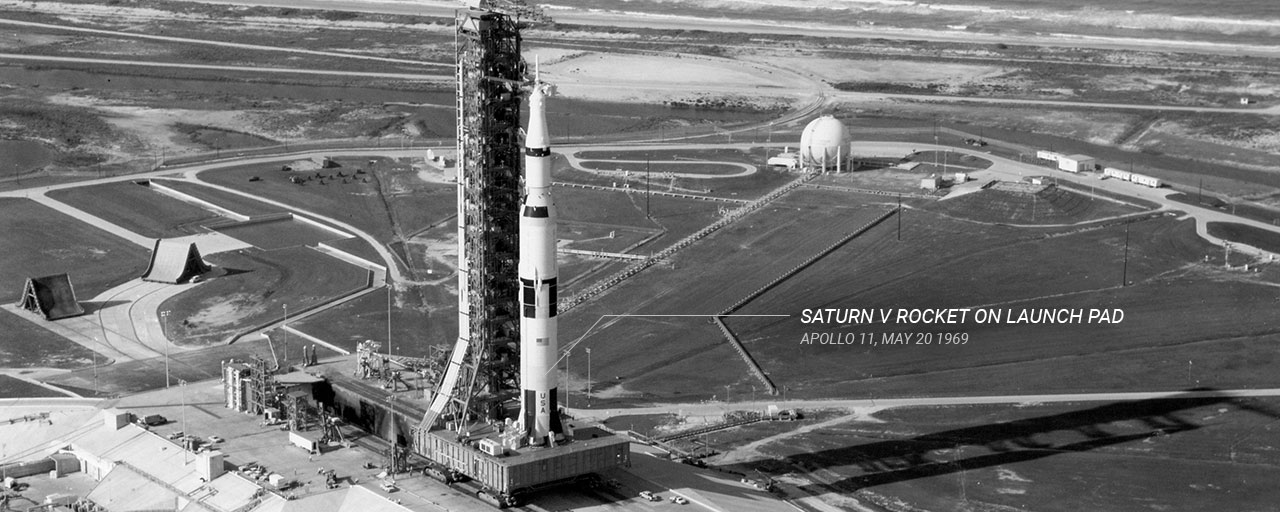
The science of oxygen safety is born
“When Grissom, Chaffee, and White were killed in the Apollo 1 event, that led directly to NASA establishing the Materials Test Facility (MTF) at NASA White Sands Test Facility,” (NASA-WSTF) says Dr. Newton, who managed the MTF during part of his tenure at NASA. At this new facility, NASA developed methods to test the oxygen compatibility of any material designated for an oxygen environment to determine the conditions for safe operation.
“The incident of Apollo 1 had to do with high oxygen-enrichment inside the crew cabin, and the fire developed and propagated because of the inherent flammability of the materials being used in oxygen,” explains Dr. Newton. “So today, as a result, we approach all oxygen systems with a sensitivity towards the fire hazard, specifically evaluating the operating conditions, inherent flammability of the materials, the potential for ignition, and the effects if a fire were to occur.”
“The Apollo fire probably would not have occurred if we had known and implemented the approach for oxygen safety we use today. In many ways, NASA’s Apollo 1 tragedy has led to many of today’s safety advances.”
Dr. Barry Newton, CEO, WHA International, Inc.
Because of Apollo 1 and the sacrifice of its crew, the world of oxygen safety became a top priority for the United States Space Program. Several WHA engineers were among the first to design, fabricate, and implement many of the oxygen and hazardous fluids test systems used by NASA during the Apollo, Space Shuttle, and International Space Station programs.
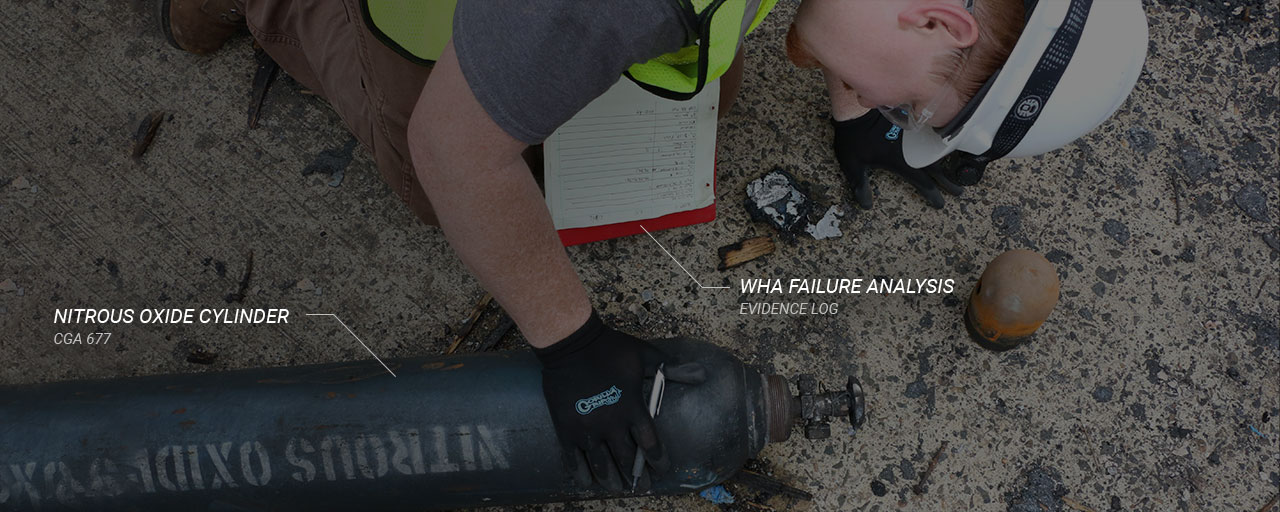
WHA brings oxygen safety to the commercial sector
In the late 1980s, WHA engineers brought their specialized oxygen experience to private industry. They continued to provide design, testing, and failure analysis not only for aerospace, but for many other industries as well.
“Within NASA, oxygen safety was all about the space program,” says Dr. Newton. “At WHA we’ve taken that technology and customized it with our own experience and background over several decades to apply the technology to commercial and private industry.”
“The scientific principles may still be the same, but the questions, the conditions, and the systems that private industry deals with are vastly different than what NASA deals with.”
-Dr. Barry Newton, CEO, WHA International, Inc.
“For instance, Monel is a material that doesn’t burn until you get to pressures approaching 10,000 psi, but it’s really expensive. NASA may be able to afford constructing their oxygen systems using materials like Monel, but industry can only do that on a limited basis. It would be cost-prohibitive, for example, to construct a 1,000 mile pipeline entirely from Monel. So a different philosophy and approach is used to safely bridge that gap between NASA’s preference for non-flammable materials and industry’s need to use more cost-effective and available materials. They have to use good design practices to prevent ignition.”
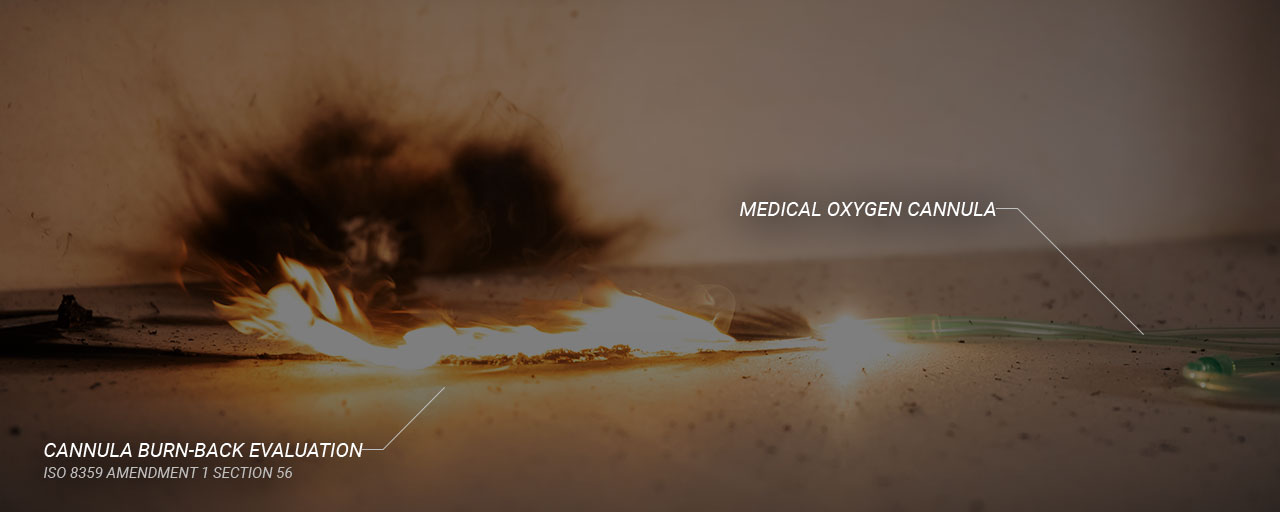
WHA’s data-driven approach to failure analysis
It’s all too common for some engineers and scientists to draw conclusions based on subjective opinions, but Dr. Newton emphasizes WHA’s unique commitment to a scientific approach to failure analysis, based on facts and data: “There really is a mystery to fire events, and once an incident occurs, there can be a lot of confusion, fear, and uncertainty. The client is looking for answers. We try to take that mystery out of the event itself and understand it scientifically first, in order to remove the mystery and mitigate further incidents.”
Testing is often a critical part of failure analysis for WHA. “Accident reconstruction” may be most often associated with automotive accidents, but reconstruction is an equally important principle for fire incidents involving oxygen and other hazardous fluids. WHA engineers carefully identify the materials, conditions, and possible ignition sources before attempting to recreate the accident. In doing so, they can capture valuable data to help reconstruct the circumstances that led to an incident.
How can companies prevent fire incidents from happening in the first place?
Many of the efforts at WHA International are dedicated to preventing and mitigating hazards before a tragic incident ever occurs. Every day, WHA engineers provide safety consulting and analysis, often incorporating the Oxygen Fire Risk Analysis (OFRA) method, which has quickly become industry standard worldwide.
“At WHA, we’re system designers and end-users too. We’re passionate about sharing what we know and furthering the science of safety. We come to work every day to improve the technology, understand the science, and make sure that tragic incidents like Apollo 1 don’t happen in different industry applications around the world. It’s why we do what we do.”
Dr. Barry Newton, CEO, WHA International, Inc.
Standard and custom testing is a key part of ensuring that appropriate materials and components are utilized for oxygen systems in the first place. Proper cleaning is also essential to preparing and maintaining a safe oxygen system.
Companies can also be proactive about safety by taking advantage of WHA’s premiere safety training courses. WHA engineers are passionate about sharing their experience when it comes to safe system design, cleaning, assembly, operation and maintenance.
[1]Orloff, Richard W. (September 2004) [First published 2000]. “Apollo 1 – The Fire: 27 January 1967”. Apollo by the Numbers: A Statistical Reference. NASA History Division, Office of Policy and Plans. NASA History Series. Washington, D.C.: NASA. ISBN 0-16-050631-X. LCCN 00061677. NASA SP-2000-4029. Retrieved July 12, 2013.
[2] Williams, Dr. David R. “The Apollo 1 Tragedy” https://nssdc.gsfc.nasa.gov/planetary/lunar/apollo1info.html
Share this entry
Related Articles
Oxygen Cleaning Service Team Receives Vendor Award
WHA’s oxygen cleaning service team recently received recognition from its client, Trace-A-Matic, for excellent service in a…
Case Study: Fire Station Medical Oxygen Cylinder Fire
A medical oxygen cylinder experienced a catastrophic failure and burnout during a routine fire station equipment check
Oxygen Cylinder Safety
An oxygen tank, or “oxygen cylinder,” is a pressurized container that stores and transports oxygen in its…
Request an expert
consultation
Contact us to request a free consultation with an experienced engineer who can help you better understand your needs and our solutions.