Defend against oxygen fires in medical electrical equipment
Because of the COVID-19 global pandemic, there is an increased demand for medical electrical equipment that handles oxygen.
Many of these oxygen devices are frequently used in situations where potential fuel (clothing and bedding) and ignition sources are readily available. If an unforeseen incident occurs, fire may ignite and propagate quickly due to increased oxygen levels.
“Medical oxygen equipment is in hospitals, care facilities, and even homes,” explains Nic Linley, electrical and forensic engineer at WHA. “Whenever oxygen is involved, you have to consider the failure modes of the device and the potential electrical sources of ignition.”
Today, millions of medical oxygen devices are used safely all around the world, largely thanks to strict international safety standards. Whenever a new device is developed, manufacturers have to ensure that it complies with these standards before being released into the target market.
WHA has both the oxygen hazards analysis expertise and the testing capabilities necessary to help medical device manufacturers demonstrate compliance with these safety standards, including ISO/IEC 60601-1 and ISO 15001.
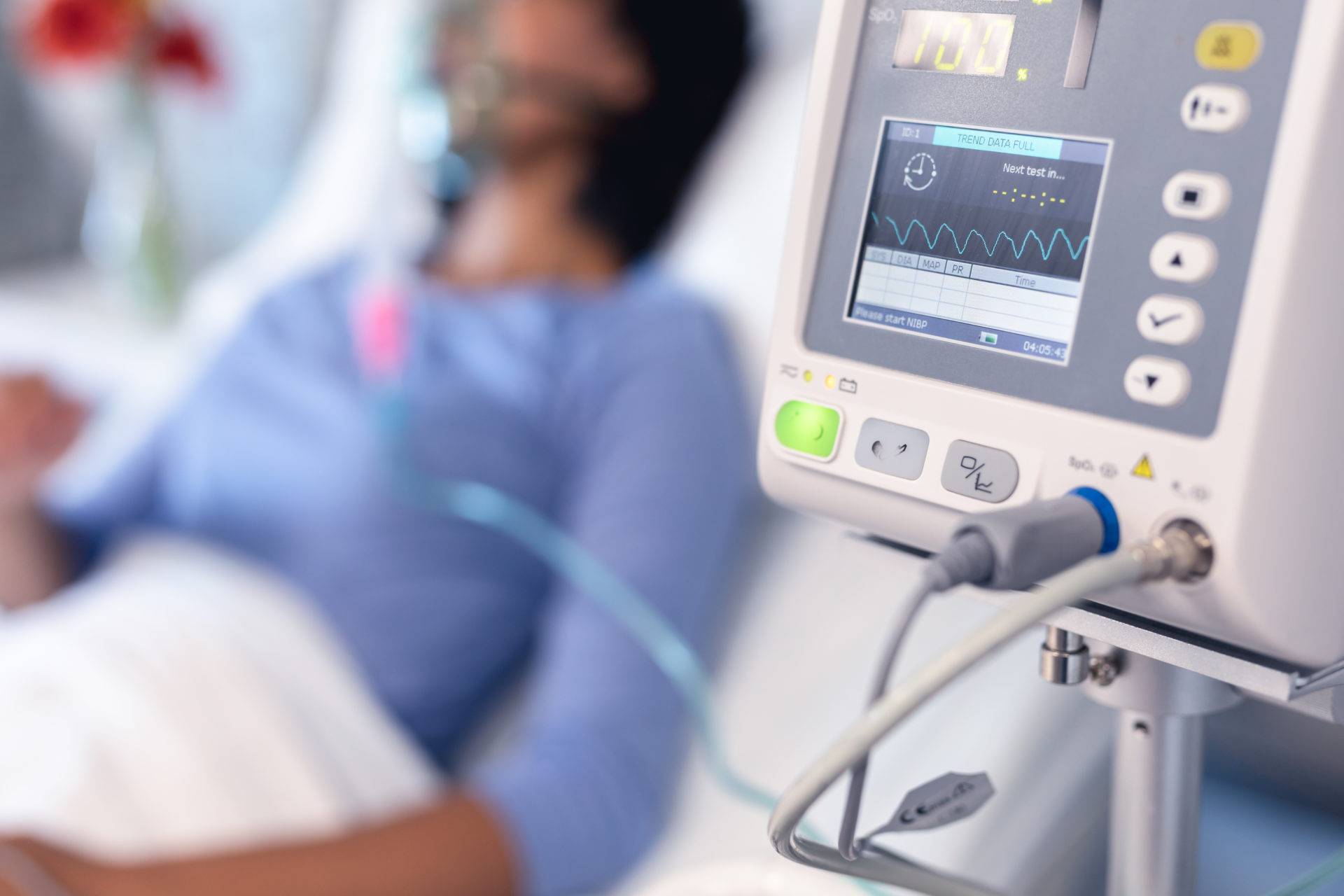
Electrical fire understanding built on experience
Over the past 30+ years, WHA forensic engineers have investigated numerous fires related to medical oxygen equipment, such as oxygen concentrators, respirators, ventilators, CPAPs, and more.
The United States Food and Drug Administration (FDA) mandates that manufacturers investigate any medical devices that have been returned due to field failures, and often, these companies contact WHA to help them understand fire incidents that may have involved electricity and oxygen.
Today, WHA leverages this past experience to help manufacturers understand oxygen fire risks and create safer equipment. Part of this process often involves helping companies demonstrate compliance and achieve certification for their devices.
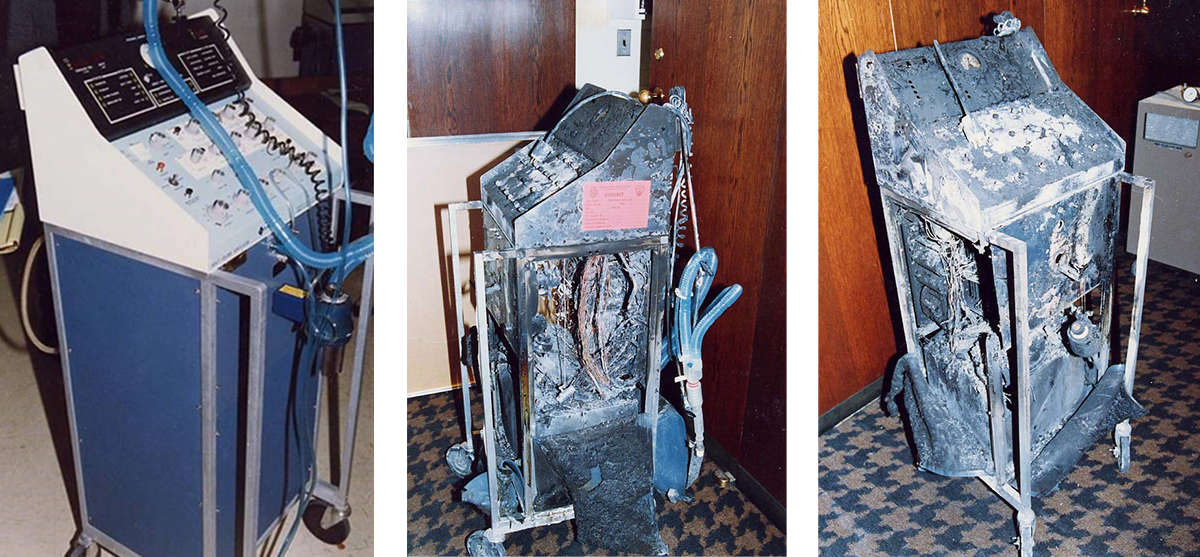
Qualifying electrical devices for use with oxygen
All major markets around the world require manufacturers to follow strict standards for medical equipment. The rules and guides related to oxygen and electrical fire risk can be found in industry standard ISO/IEC 60601-1, subsection 11.2.2.1.
Manufacturers must acquire a stamp by a national certification body before a new device can be sold. These organizations include UL in the United States and CSA in Canada. WHA is one of only a few vendors that can provide the testing and reports needed to demonstrate to these certification bodies that medical electrical equipment that handles oxygen meets the qualifications of the target market.
Different pathways for manufacturers to show compliance with the oxygen requirements of ISO 60601-1
Medical oxygen devices serve a variety of applications with different operating conditions. Because of this, manufacturers can pursue different pathways to certify the safety of an electrical compartment that may normally be in oxygen or may become oxygen enriched due to a leak. Each of these paths set out to demonstrate that the electrical fire risk is acceptable.
#1 Power Limitations:
If a manufacturer can demonstrate that the device’s power requirements are too low to ignite potential fuel and contaminants, then fire risk can be considered acceptable. Equipment is tested in a controlled oxygen enriched environment with up to three times the voltage or current of to the device’s typical electrical load supplying an electric arc to an identified flammable material that may be in the compartment and a potential first fuel in a fire. Observations of no ignition at three times the energy level qualifies the compartment.
#2 Oxygen Concentration:
“In many cases, devices do require significant power to operate, and therefore they cannot pass the first set of tests for certification,” says Nic. “If ignition sources cannot be eliminated, engineers often look to the next side of the ‘fire triangle’ to limit the potential of enriched oxygen.”
Many electrical components already need ventilation and fans for cooling, and certification may be possible if a manufacturer can demonstrate that the oxygen concentration can be sufficiently controlled within the device enclosure by way of ventilation.
#3 Probabilistic Risk Assessment:
“Probabilistic risk assessment of electrical failure modes and failure rates is pretty unique to WHA,” says Nic. “Not many vendors have the expertise and capability to provide it.”
In this pathway, WHA engineers review the device schematics to identify a set of critical components that are above the electrical power thresholds identified in ISO/IEC 60601-1 11.2.2.1a as being levels that are considered sources of ignition. They then run those components against failure mode distribution and rate databases to estimate a predicted rate of failure based on the general history of use of the electrical components and the intended usage (e.g., expected duty cycles, thermal cycling, on/off cycling, etc.). Each of these rates is combined into one overarching failure probability.
Manufacturers can use this probability against their leak rate probability to set a maintenance interval to inspect for faults. “As long as the leak rates and intervals are low, that resulting inspection timeline can be very long,” says Nic.
As long as a manufacturer can demonstrate that the probability of failure and ignition is acceptably low, the device may qualify by a probabilistic risk assessment route.
#4 Consequence of Fire:
A potential testing path listed in ISO 60601-1 11.2.2.1b 4 doesn’t examine the likelihood of a fire, but rather the potential outcomes of a fire. Compliance may be shown if the manufacturer can demonstrate that a fire will safely self-extinguish with a low risk to people and other fuel sources nearby.
“A fire is intentionally staged, and we see what happens,” explains Nic. “Is the fire contained in the enclosure? Does fire reach the patient? Do toxic gases reach the patient? We use various tests and ignition methods to simulate real word conditions and initiate a fire in the equipment. Sometimes these tests even use artificial lungs or resistive breathing elements.”
Additional pathways to compliance:
If compliance cannot be achieved through any of the four main methods, there are still several alternative pathways to qualify an oxygen enriched electrical compartment against ISO/IEC 60601-1.
One such pathway includes cost-benefit analysis. If, for example a device provides unprecedented, effective treatment for critical patient needs, that device may qualify because the benefit outweighs the risk.
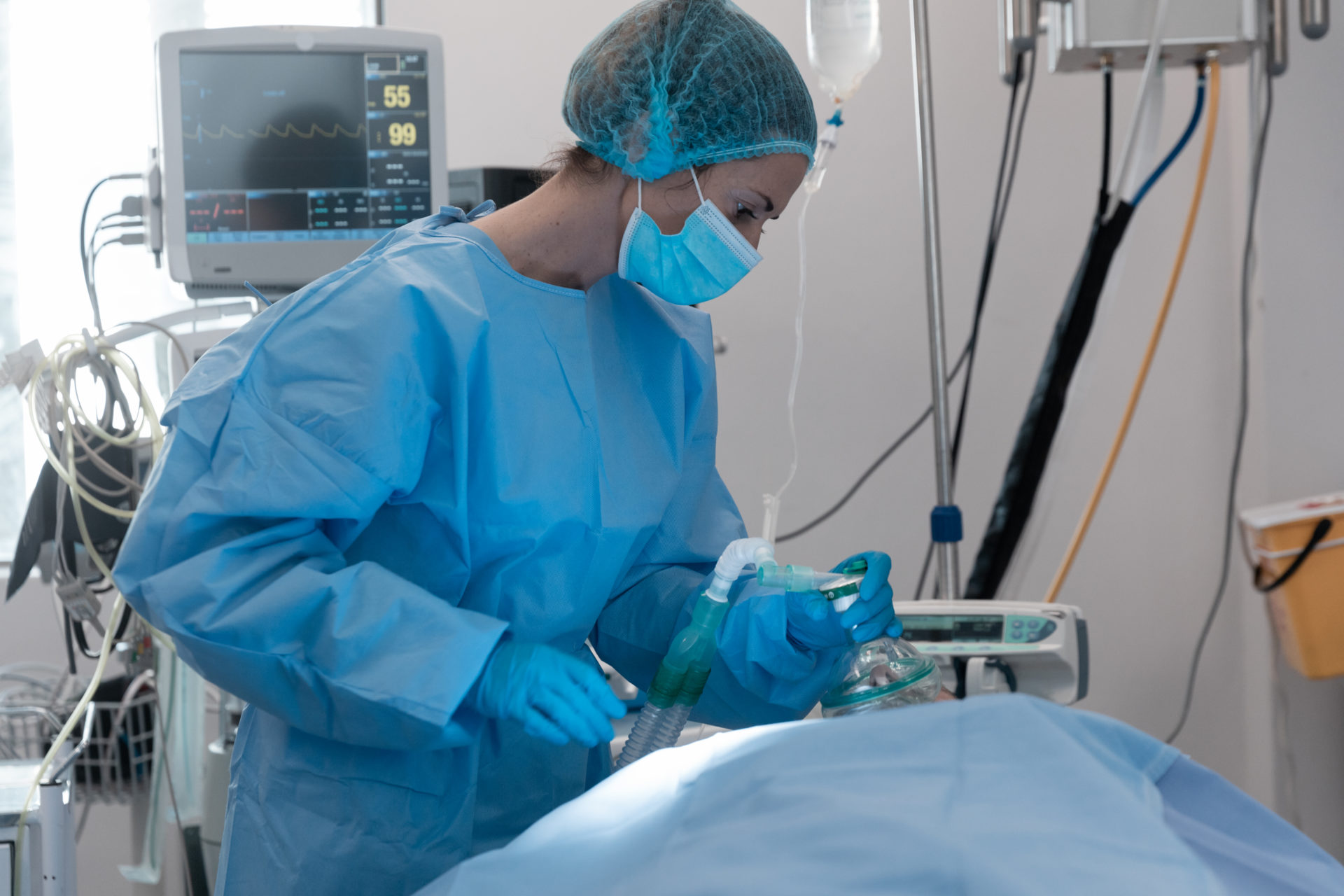
The final steps for component certification
“Following testing and review, WHA writes a report with conclusions based on the medical electrical equipment’s qualifications and any testing performance against the criteria spelled out in ISO 60601-1,” explains Nic. “This WHA report can be submitted to a certification body to help support the manufacturer’s goal of qualifying to ISO 60601-1. Historically, WHA’s reports have proven to represent a key element towards certification.”
Share this entry
Related Articles
Nonmetals Oxygen Compatibility Requirements: Guide to CGA/EIGA Compliance
The Compressed Gas Association (CGA) and European Industrial Gases Association (EIGA) have harmonized key documents providing guidance…
WHA Launches Oxygen Equipment Supplier Certification Program
Ignition and combustion hazards are present in almost all oxygen and oxygen-enriched systems, and catastrophic fires have…
Case Study: Fire Station Medical Oxygen Cylinder Fire
A medical oxygen cylinder experienced a catastrophic failure and burnout during a routine fire station equipment check
Request an expert
consultation
Contact us to request a free consultation with an experienced engineer who can help you better understand your needs and our solutions.