Case Study: LOX Valve Internal Fire
When operators first discovered an internal leak in Valve V6272A, they weren’t particularly concerned. The valve was located beneath a large liquid oxygen (LOX) tank at an air separation unit (ASU), and from the outside, everything looked fine. Industrial oxygen components need maintenance or replacement from time to time, so operators and maintenance staff drained the tank and removed insulation to get a closer look at the piping system.
What they found that day was a most unwelcome surprise. Markings visible on the outside of the pipes (and later discovered inside) suggested a significant oxygen fire had occurred inside the system itself. Thankfully, the internal fire did not breach the piping of the tank. If it had, thousands of gallons of LOX would have drained out into an area where personnel may have been present. A rapid discharge of so much LOX could have led to life-threatening fires, explosions of organic materials, and even severe cryogenic injuries.
How and when had this happened? There was no way to know just how long the valve had been in operation in its current damaged state. Despite the mystery surrounding the event, answers had to be found. If such an incident ever occurred again, those involved might not be so lucky.
Calling on WHA for answers
In order to find answers, our customer engaged the specialized forensic team at WHA International. Since 1987, WHA has performed failure analyses after oxygen fire incidents. Our engineers apply a uniquely data-driven approach, combining decades of forensic experience with the latest tools and technologies.
This analysis was challenging because the fire didn’t burn out of the valve, and the exact date of fire was unknown. Ultimately, WHA’s meticulous evaluation of the fire evidence would help reveal answers, resulting in critical knowledge for the client to develop safety improvements.
Failure Analysis Approach
WHA utilizes a failure analysis approach specifically for oxygen fires, which is consistent with industry standard ASTM G145. The oxygen fire failure analysis is based on the fire triangle concept, which requires three legs for a fire to occur: oxidizer, fuel, and ignition.
- Document the incident scene and post-incident condition of fire damage.
- Develop sequence of events.
- Determine a timeline from any witness reports, video recordings, data trends, etc.
- Determine the operating conditions (pressure, temperature, concentration, phase, flow) prior to and during the fire event.
- Disassemble and document evidence.
- Identify fire-damaged parts and materials consumed by burning.
- Evaluate fire patterns such as melt flows, propagation paths, and kindling chains.
- Identify potential origins from fire patterns.
- Perform Oxygen Fire Failure Analysis.
- Oxidizer: Determine system conditions at time of incident.
- Fuel: Determine materials of construction that exhibit burning based on fire patterns and any potential contaminants. Evaluate their flammability at the system conditions at the time of the incident.
- Ignition: Identify active ignition mechanisms at the time of the incident based on the presence and severity of characteristic elements.
- Evaluate the degree to which potential origins and associated kindling chain scenarios match physical evidence and active ignition mechanisms.
- Identify most probable origin and most probable ignition mechanism.
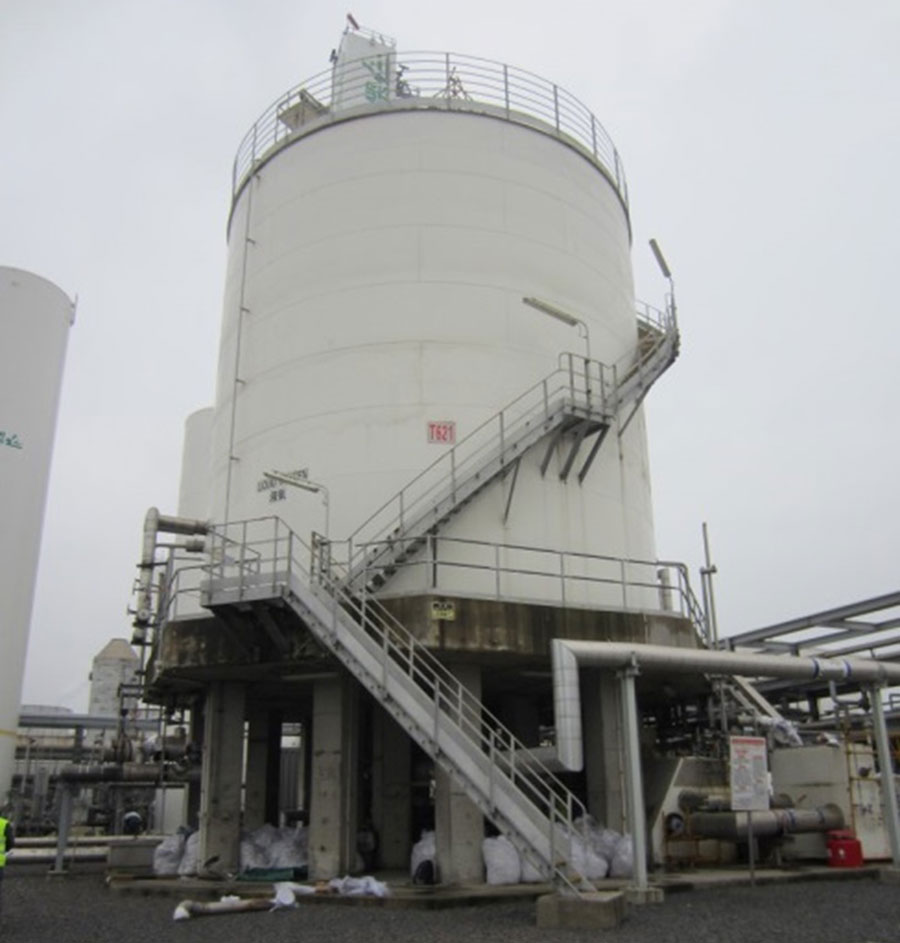
Incident Description
The incident occurred inside one of the two main isolation (drain) valves below the LOX tank pictured above.
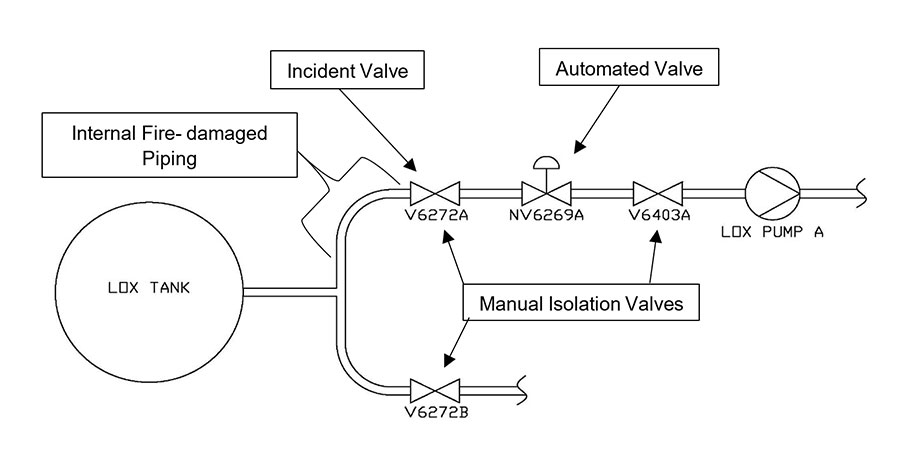
This fire incident was particularly challenging to investigate because damage was not discovered until well after the fire occurred. In 2014, without any knowledge of the fire event, operators determined that V6272A was leaking internally, so the LOX tank was emptied and insulation around the piping was removed for visual inspection and disassembly.
Upon discovering external surface patterns consistent with severe heat, personnel removed and disassembled the valve and piping for further inspection. The internal inspection revealed a significant oxygen fire had occurred, which burned large quantities of the piping and valve. Somehow, the fire extinguished and did not lead to burn through, which was an extremely fortunate outcome given the potentially catastrophic consequences.
Once the internal fire damage was discovered, additional details from the system’s history operation and inspection began to come together. Namely, large pieces of metallic flake debris were discovered in the strainer on LOX pump A in 2013 and 2014. These may have originated from the fire and migrated downstream, after fire extinguishment, as resolidified metallic combustion products.
Additionally, suspicious pressure spikes were recorded on February 20, 2010 and on August 12, 2011, but it is also possible that the fire occurred when the tank was first filled in 2009. Incredibly, this represents a 5-year window of time during which the fire could have occurred.
Upon discovery of the fire-damaged valve, WHA was engaged to provide forensic engineering services to help determine what went wrong.
LOX Tank Area Inspection
The piping system around the discharge valve was documented during the initial inspection. External surface patterns on the upstream piping were among the first indicators that an internal fire event had occurred. Further internal inspection provided more clues to how the fire propagated.
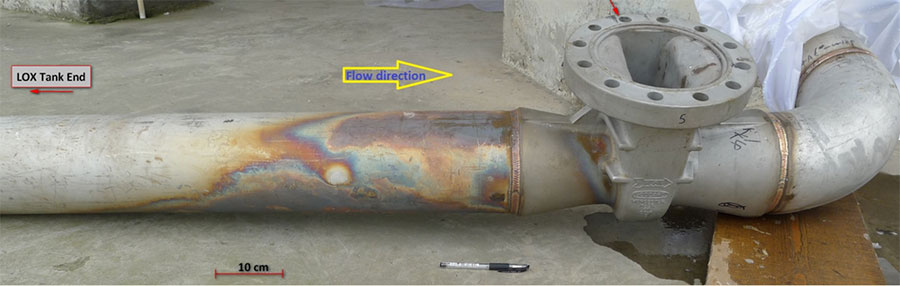
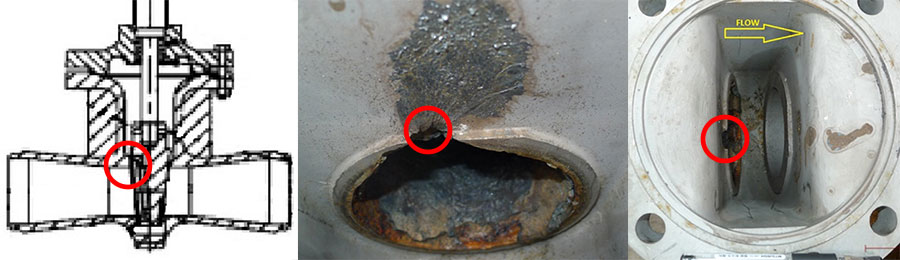
To learn more about the original condition of the system and the after-effects of the fire, engineers examined the internal surfaces of the bodies of the sister valve located on the adjacent piping train (V6272B) and the manual isolation valve downstream of subject valve (V6403A). Both were inspected with UV light and no residues were visually detected. No fire damage and minimal particulate were observed.
A spare (exemplar) valve (identical to the incident valve) was also obtained from a storage facility on-site for subsequent inspection and reference.
Evidence Documentation & Reconstruction
During the inspection and disassembly both onsite and in laboratories, samples were collected for material characterization of organic and metallic materials (including residues and particulate). The material characterization was performed using laboratory analysis techniques, such as Fourier Transform Infrared (FTIR) spectroscopy and Energy-Dispersive X-ray Spectroscopy (EDS).
The following items were documented, and notable findings are discussed below.
- Spare valve (exemplar): The valve had been procured at the same time as the incident valve and had been held in storage since then. When the wedge was disassembled from the stem, an oil-like residue was immediately noticed on the threaded end of the stem under white and UV light. FTIR analysis of the residue was consistent with a hydrocarbon-based oil. After the hydrocarbon residue was identified, communication with the valve manufacturer revealed that machine oil was used for drilling during assembly and that subsequent portions of the component were then attempted to be cleaned together as an assembly. Cleaning assemblies is considered a poor practice for oxygen cleaning and is typically ineffective at removing residues at the mating surfaces. This finding was clearly a concerning source of hydrocarbon that may have contributed to the ignition.
- V6272B valve (B Train valve): This valve was the same model as the incident valve but located on the mirrored Train B pipeline. No fire damage was observed, and no evidence of hydrocarbons were detected or observed in the threaded connection between the wedge and stem or other locations in the valve. Significant quantities of particulate matter were discovered within the valve, consistent with debris found in the LOX tank.
- V6272A valve (incident valve): The stem/wedge connection exhibited fire patterns consistent with a hydrocarbon-based oil burning in the threaded portion of the stem/wedge. Although the stainless-steel wedge itself exhibited no consumption, significant portions of the seat and seat clamp were consumed in the fire event (see Fig. 5). However, the fire path between the stem/wedge connection (location of the hydrocarbon oil) and the partially burned seat assembly of the valve (location of greatest fire damage) was not clearly distinguishable and complicated the failure analysis. The inlet side of the valve (up to the wedge) also exhibited the greatest level of fire damage and metal consumption throughout the whole internal circumference, as shown in the reconstruction photo (Fig. 6).
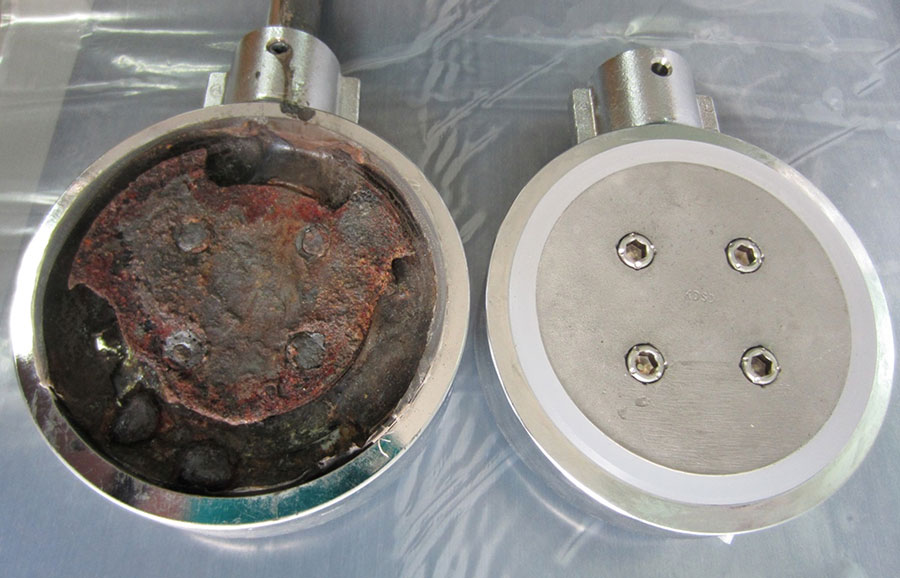
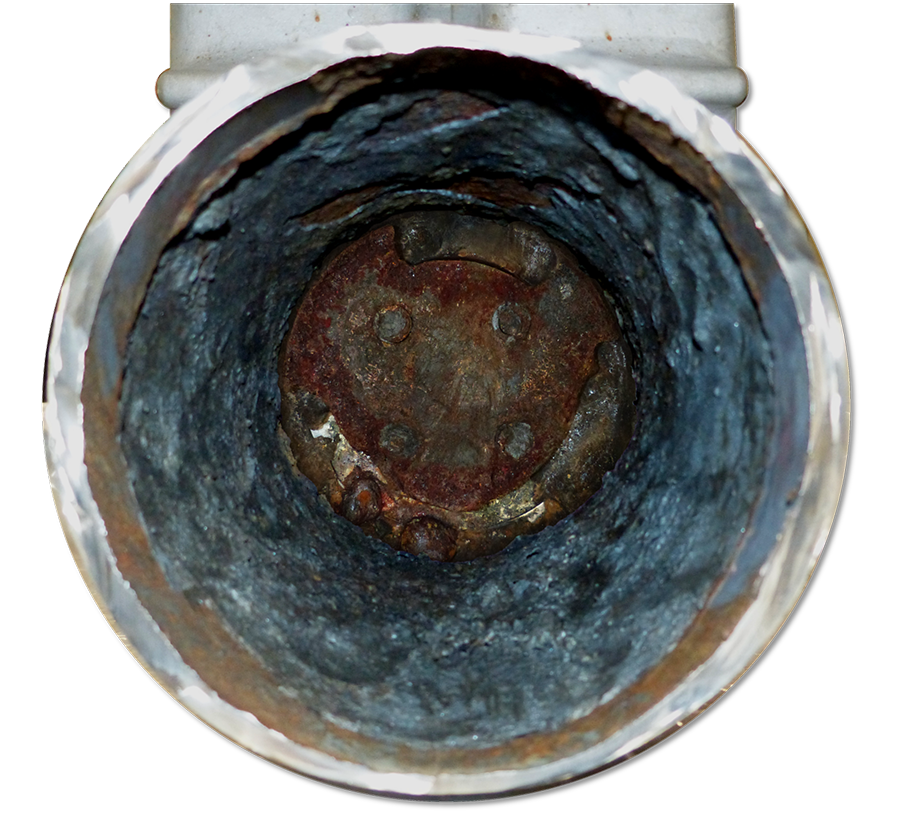
The threads of the V6272A seat clamp screws were coated with particulate and grease-like residues. These threads were extracted with solvent and the FTIR analysis of the filtered solvent extraction identified a perfluorinated lubricant and a hydrocarbon-based contaminant with a carbonyl stretch. This FTIR analysis suggested this contaminant was different to the hydrocarbon oil found on the stem/wedge connection and likely represents a different hydrocarbon source.
- Piping upstream of V6272A valve: The piping section upstream of the incident valve exhibited internal fire patterns and slag deposits (Fig. 7). Variation in pipe wall thickness suggest the pipe end attached to the valve was also partially consumed with the burning event and would have expected to develop significant quantities of slag, that likely separated (flaked-off) from the piping and flowed downstream into the downstream pump strainers as discovered on two occasions during the 5-year window of system operation.
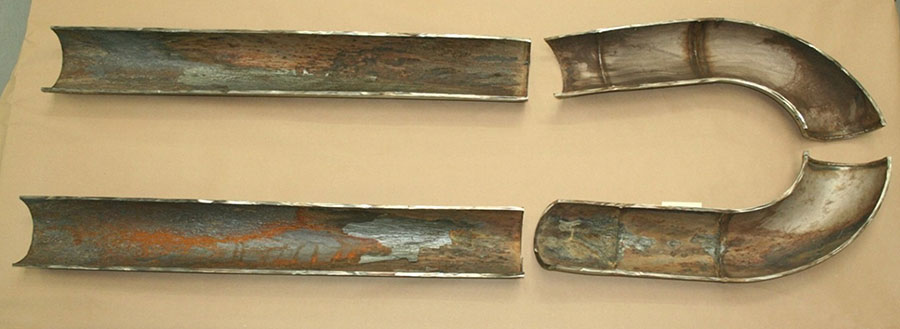
- V6403A valve (isolation valve downstream of incident valve): This valve was an isolation valve downstream of the incident valve. Although internal surfaces exhibited minor dark residues, stains, and particulate debris, FTIR analysis of these samples identified no organic contamination. No evidence of fire damage, adhered slag deposits/development or metal consumption was observed in this valve.
- LOX Tank: Significant amounts of various types of debris were recovered from the tank and analyzed. Debris ranged from fine particles/dust, plastic pieces, viscous materials, and larger metallic particles.
Reconstruction of the evidence allowed development of potential scenarios under which ignition occurred and the fire progressed inside the system. The evidence of the V6272A and attached piping suggest that the valve was in the closed position when the fire occurred.
Failure Analysis
Following evidence documentation and reconstruction, the forensic team was able to consider three critical elements associated with an oxygen fire event: oxidizer conditions, fuel consumption, and ignition mechanisms.
Oxidizer Conditions
Presence of an Oxidizer: The exact timing of the incident remains unknown, but the valve was assumed to be filled with LOX on the upstream side and possibly on the downstream side as well (LOX-full or partially full).
Pressure: Because of the high likelihood that the valve was closed at the time of the event, we can assume that no LOX/GOX (gaseous oxygen) flow occurred past the wedge seat of the valve at the time of ignition. Therefore, the maximum potential pressure at the time of ignition was 2 bar from the head pressure of the tank.
Temperature/Phase: If the ignition occurred during initial filling, then the temperature of the valve would be between ambient temperature and LOX cryogenic temperatures and the phase of the oxygen would be expected to be mixed phase. If the ignition occurred at a later date, the temperature and phase would be consistent with LOX on the upstream side, and likely GOX on the downstream side when the valve was closed because the valve was orientated vertically.
Fuel Consumption
In an oxygen fire event, more flammable materials can spread fire to other less flammable materials in a “kindling chain.”
Based on the fire patterns, material specifications, and material characterization work, the following materials were considered present and exhibited burning in the fire event. They are listed in order from most flammable to least flammable (but not necessarily representing a kindling chain order) based on available oxygen compatibility data.
- Hydrocarbon contamination: Sources included the stem/wedge connection machining oil, seat clamp screws, and impurities in LOX accumulating at V6272A valve (sump) via distillation (LOX boiling) at wedge. Although the quantity of hydrocarbon impurities in the LOX was low per industry standards, the long duration that the valve remained in a closed position could have facilitated the concentration of soluble hydrocarbons, which are mechanically shock sensitive.
- Particulate
- PCTFE Seat
- Wedge Pin (Thin Stainless Steel)
- Seat Clamp and Screws (Stainless Steel)
- Wedge/Stem Connection (Stainless Steel)
- Valve body (Stainless Steel)
Ignition Mechanisms
Based on the understanding of oxidizer conditions and fuel consumption, the following potential ignition mechanisms were identified:
- Mechanical impact ignition of hydrocarbons from violent LOX vaporization at the wedge during LOX tank filling
- Mechanical impact ignition from momentary cavitation induced vibrations upon closing the valve under flowing conditions (i.e., while downstream pump was operating)
- Mechanical impact ignition of hydrocarbons from mechanical vibrations generated in other parts of the system and transmitted through piping towards V6272A
- Particle promoted ignition of hydrocarbons during LOX tank filling involving particle acceleration within valve inlet due to violent LOX vaporization (considered a lower probability because of cold targets)
The three mechanical impact ignition mechanisms presented above could translate mechanical energy at multiple locations inside the valve. Hydrocarbon-based materials can become extremely shock sensitive in LOX and can require minimal mechanical impact energy for ignition. In addition, the potential for accumulation of hydrocarbons at the closed seat (i.e., sump) via LOX boiling over many days was theoretically demonstrated.
Conclusions
Based on the evidence, analysis, and testing experience, the failure analysis team determined the most probable fire origin was at the upstream sealing surface and seat of the valve. The most probable ignition mechanism was repetitive mechanical impact (vibrations) at this location, causing ignition of contaminants.
The following observations provide the main support for these conclusions:
- Evaluation of the fire patterns indicated the greatest amount of consumption was at the upstream sealing surface of the valve body and upstream side of the wedge.
- The most ignitable materials present at the most probable origin were hydrocarbon-based contamination and particulate. The evidence suggests various types of hydrocarbon contamination were present at the wedge/stem connection and potentially on the seat and seat clamp.
- Repetitive mechanical impact ignition from vibrations was considered feasible at the most probable origin.
- The wedge/stem connection was not completely fixed and exhibited independent movement. The stem of the valve represents a slender beam which was considered more susceptible to vibrations.
- The lack of fire propagation downstream of the seat suggests a reverse flow configuration developed upon loss of the seal. The presence of a reverse flow scenario was consistent with the LOX-full system configuration which allowed pressure to rapidly develop immediately downstream of the valve’s seat (due to heat transfer and the fire at the wedge/stem connection) prior to loss of seal at the seat.
Lessons Learned
WHA’s failure analysis method is uniquely rooted in a data-driven approach — not simply anecdotal opinions. Our team of highly specialized engineers, chemists, and consultants leverage decades of forensic experience combined with the latest tools and technologies.
What’s more, our process is unique because we go beyond analysis results to help clients understand and interpret the data. Based on the failure analysis of this fire incident, the client and WHA generated the following takeaways:
- Conduct system design reviews to identify potential closed-ends (“deadlegs”), where LOX can exist against a closed valve, with no flow. This can be caused by a number of circumstances such as: equipment maintenance; control valves staying closed for extended periods; or closed cryogenic equipment drain valves.
- Where such circumstances are identified, periodically open the valve or find other means of purging the line up to the valve, to flush out particulates and / or accumulating hydrocarbons in the LOX.
- Avoid machining assemblies after cleaning operations and avoid cleaning assemblies.
Because of the detailed analysis and resulting recommendations, the client was able to return to operating their systems confidently. Operators were equipped with the awareness and practices they needed to prevent future incidents and help ensure safety.
Together, WHA and the customer worked to publish a detailed paper through ASTM international to help bring awareness of this unique case study to the industry at large. The above practices are now recommended for all similar industrial oxygen systems and components.
At WHA, we simplify oxygen safety
If you need answers following an oxygen fire incident or would like to analyze the fire risk of your systems, components, and materials, please reach out to our experienced engineering team.
For more details on this incident see “ASTM STP 1626 Failure Analysis of a LOX Valve: Internal Fire Only” by Gwenael J. Chiffoleau, Derek Miller, Brad Forsyth, Barry Newton. Produced by WHA International in partnership with Air Products & Chemicals, Inc.
Share this entry
Related Articles
Case Study: Fire Station Medical Oxygen Cylinder Fire
A medical oxygen cylinder experienced a catastrophic failure and burnout during a routine fire station equipment check
Real world oxygen fire evidence underscores the need for safety
Over 30+ years of investigating oxygen fires at WHA International, Inc., we have documented hundreds of incidents...
Case Study: Aluminum Oxygen Tank Fires Initiated by Impact
In recent years, several notable oxygen tank fires have occurred after a fall or sudden impact. WHA...
Request an expert
consultation
Contact us to request a free consultation with an experienced engineer who can help you better understand your needs and our solutions.