Oxygen Cleaning Inspection Methods
You probably know that specialized cleaning is important for oxygen system safety, but how do you determine if a part is clean?
Here at WHA, our technicians clean over 10,000 parts a month, and we are asked this question with increased frequency. Especially with many new medical oxygen equipment manufacturers entering the market to support COVID-19, companies want to know “how clean is clean?” and “how do we know if our parts are clean enough?”
Why clean for oxygen service?
Contamination is one of the leading causes of oxygen fires. WHA forensic engineers have investigated many fire incidents that could have been prevented with proper cleaning to remove incompatible oils and greases or small particulates.
Materials ignite and burn more easily in oxygen-enriched atmospheres, including metal and nonmetal contaminants. These contaminants are fuels that can be easy to ignite and burn vigorously in oxygen, potentially leading to catastrophic consequences.
When considering oxygen system and component cleanliness, WHA follows a four-step approach to ensure safe use:
- Start clean
- Verify clean
- Assemble clean
- Maintain clean
Oxygen cleaning inspection is an important part of both verifying clean before and after assembly (step 2 and 3) and during routine maintenance (step 4). Each of these four steps is critical to the reducing the overall risk of an oxygen fire caused by contaminants.
You can read more about the science of oxygen cleaning in our article “Why Clean for Oxygen Service?”
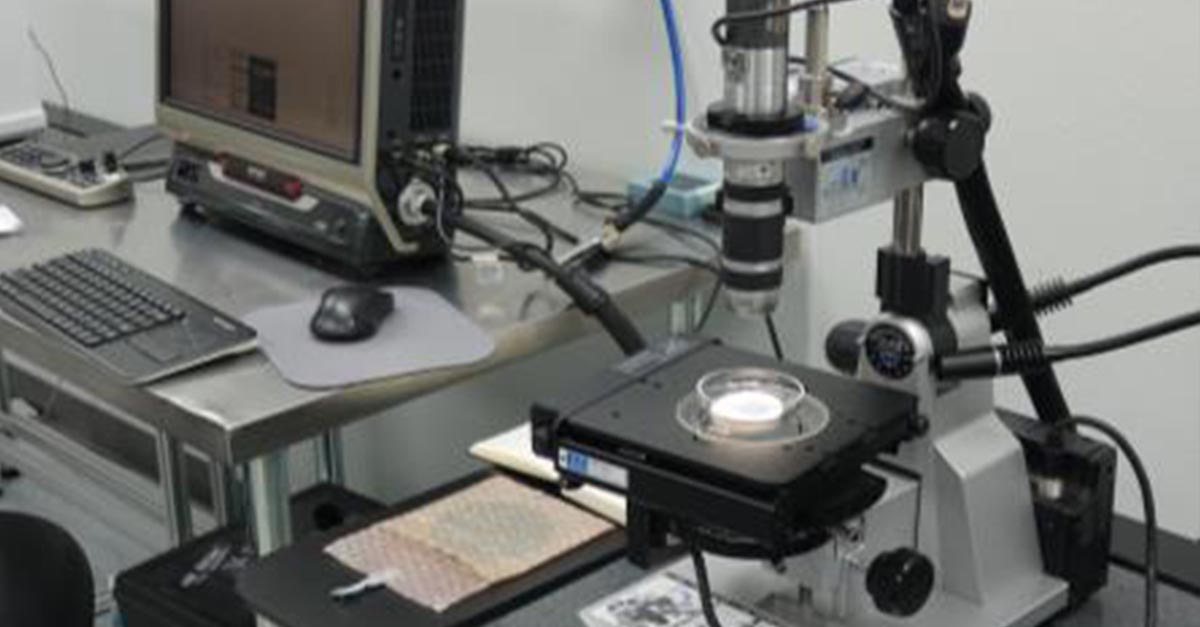
How clean is clean?
Various industries that utilize oxygen rely on their standards to define requirements for oxygen cleaning, including ISO 15001, ASTM G93, EIGA 33/18, CGA G-4.1, MIL-1330D, and SAE ARP1176. At WHA, we are intimately familiar with these, and other international standards on oxygen safety, because we help write them.
When someone asks, “how clean is clean?” the answer ultimately depends on the end application and the probability of contaminant-promoted ignition. For example, small high-pressure cylinder applications typically have tighter restrictions than industrial oxygen piping systems because of their inherent compression heating hazard and general lower tolerance for contaminants. Medical oxygen applications range from high-pressure cylinder supply to low-pressure hospital supply.
Regardless of application, cleaning involves removing both non-volatile residues (NVRs), such as oils and greases, as well as small particulates.
There’s a reason oxygen systems are “precision” cleaned; all of these standards prescribe cleanliness levels below the visual level. They set a quantitative target value for cleanliness, defining types, quantities, and sizes for unacceptable contaminants.
If you have any questions about cleaning requirements for your industry, please reach out to us. One of our oxygen safety experts would be happy to walk you through the relevant standards for your oxygen equipment.
Quantitative Oxygen Cleaning Inspection (OCV)
To find out if a part is “clean enough” for use with oxygen, we typically perform a quantitative oxygen cleaning inspection, otherwise known as oxygen cleanliness verification (OCV) and compare the results with the appropriate cleaning standard. This is often done as part of a process review to verify that an oxygen cleaning program produces the required levels of cleanliness.
At WHA, our team performs OCVs using a precise solvent extraction and gravimetric analysis method. Every OCV is customized to a client’s unique parts and relevant specifications. The entire procedure is performed inside a carefully controlled environment (ISO 14644 Class 5) to ensure no interference from outside contamination.
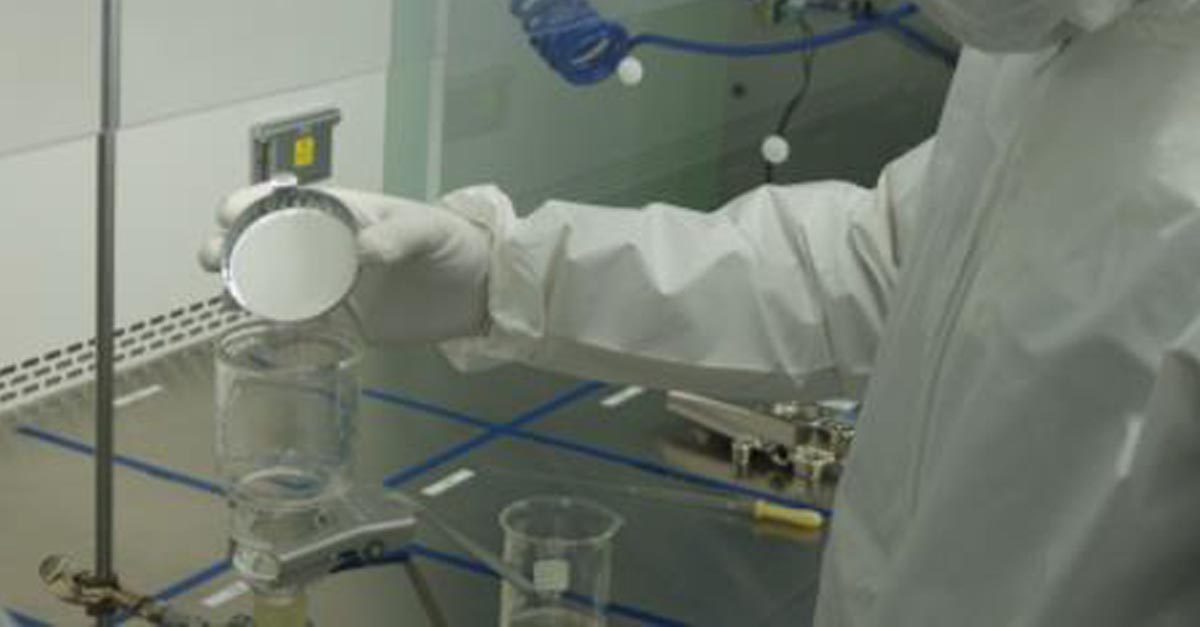
WHA’s Typical Oxygen Cleanliness Verification Method
- Equipment Cleaning: All glassware and weighing trays are meticulously cleaned.
- Solvent Extraction: The clean solvent is then diligently applied to the parts of interest to extract contaminants into solution.
- Sample Filtration: The sample collected is then transferred to the filtration apparatus in order to separate particulate that will be analyzed under the microscope.
- Gravimetric Measurement: The filtered solvent sample is then transferred to a pre weighed tray, where the solvent is allowed to evaporate. The tray weight is then measured to calculate the amount of non-volatile residue that has been collected, while accounting for a control sample.
- Particulate Analysis: Finally, the preserved filter is transferred to a microscope for quantification of particulates.
This process provides a precise measurement of the size and quantity of both NVRs and particulate contaminants. This method is typically performed on piece parts after cleaning prior to assembly. Solvent extraction of assemblies is usually avoided.
If necessary, the extracted contaminants can also undergo material characterization, using techniques such as Fourier Transform InfraRed (FTIR) spectroscopy and Energy Dispersive X-ray (EDX) spectroscopy to determine the type and origin of the contamination. This service can be paired with oxygen fire risk analysis (OFRA) to help clients determine the source of contamination, subsequent fire risk, and further steps to improve cleanliness/safety.
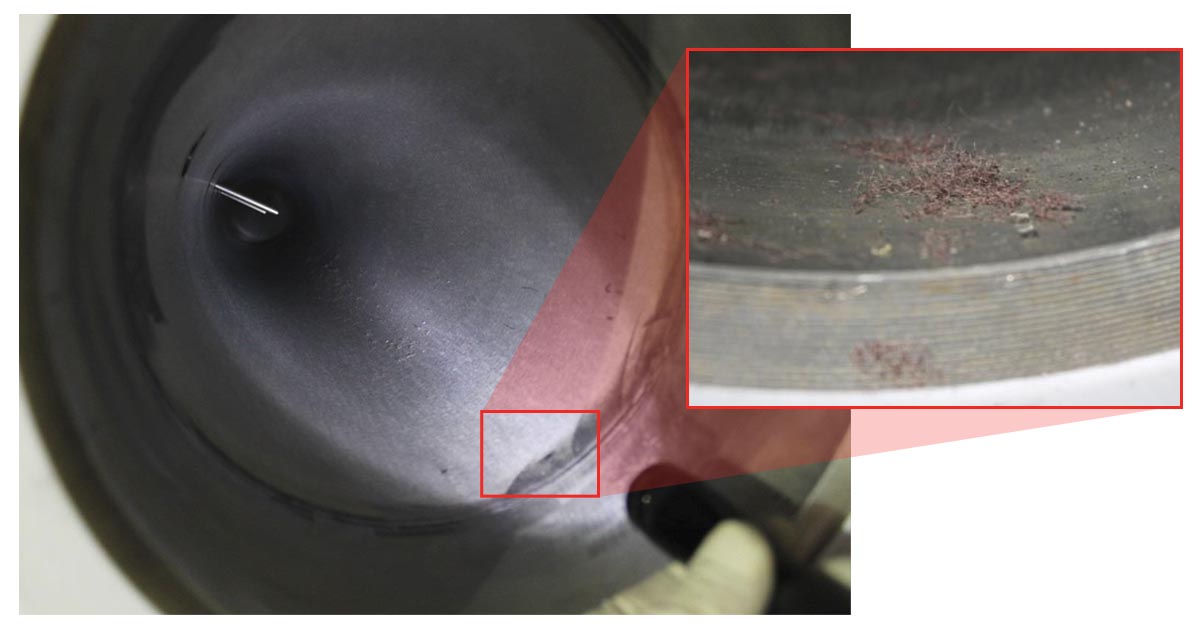
Qualitative (Visual) Oxygen Cleaning Inspection
In addition to quantitative inspection, technical personnel can also utilize a secondary qualitative (visual) inspection method.
Visual inspection cannot guarantee that a part meets quantitative cleanliness requirements, but it can indicate that a part is not clean. For this reason, it’s often performed as part of routine quality checks or maintenance, helping to ensure that no dangerous gross contamination is present.
Our eyes are actually very good inspection tools. We can see particles as small as 40-50 microns in size without a microscope. This is sufficient to detect the particulate levels specified in most oxygen cleaning standards, if we can visually access the oxygen-wetted surfaces of the parts. Visual inspection is fast, convenient, and cost-effective, making it a particularly useful tool in the field.
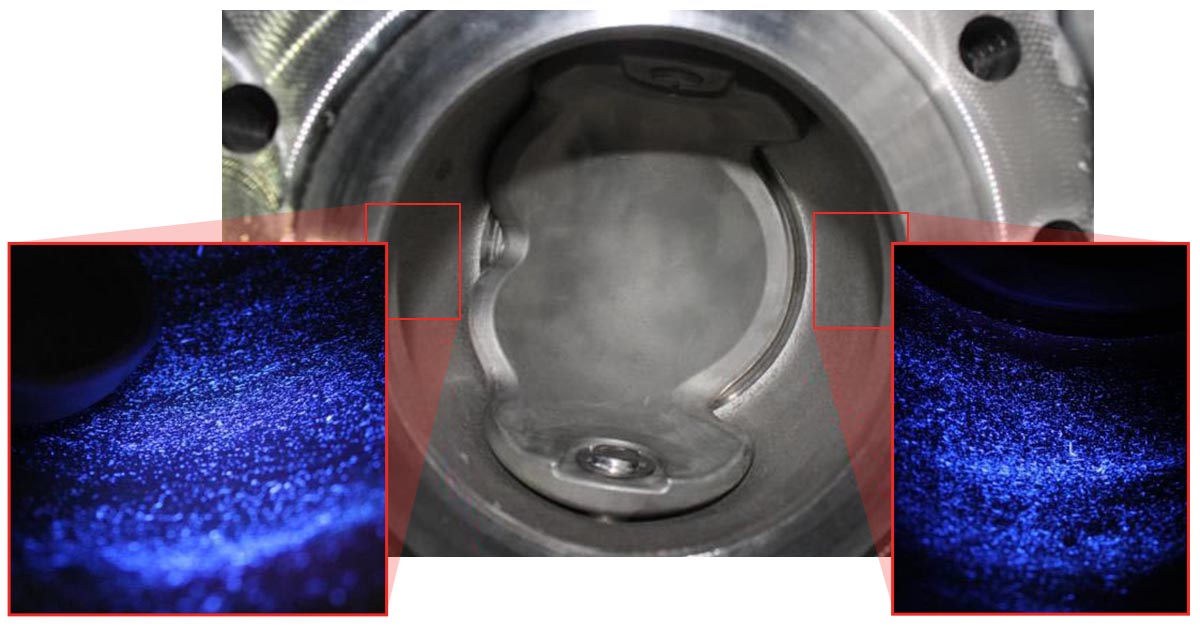
WHA’s Visual Inspection Method
- White Light Inspection: primarily reveals metallic particles and rust. It may also pick up oil sheen at sufficiently high quantities.
- Black Light (UV) Inspection: reveals oils, greases, and residues that fluoresce under UV light (not all oils and greases do). It’s also good at picking up lint and dust. Black light inspection is performed in a dark room and requires special training and plenty of practice.
- Wipe Test (optional): Accessible surfaces are wiped with a lint-free cloth or swab, which can then be inspected under white and black light.
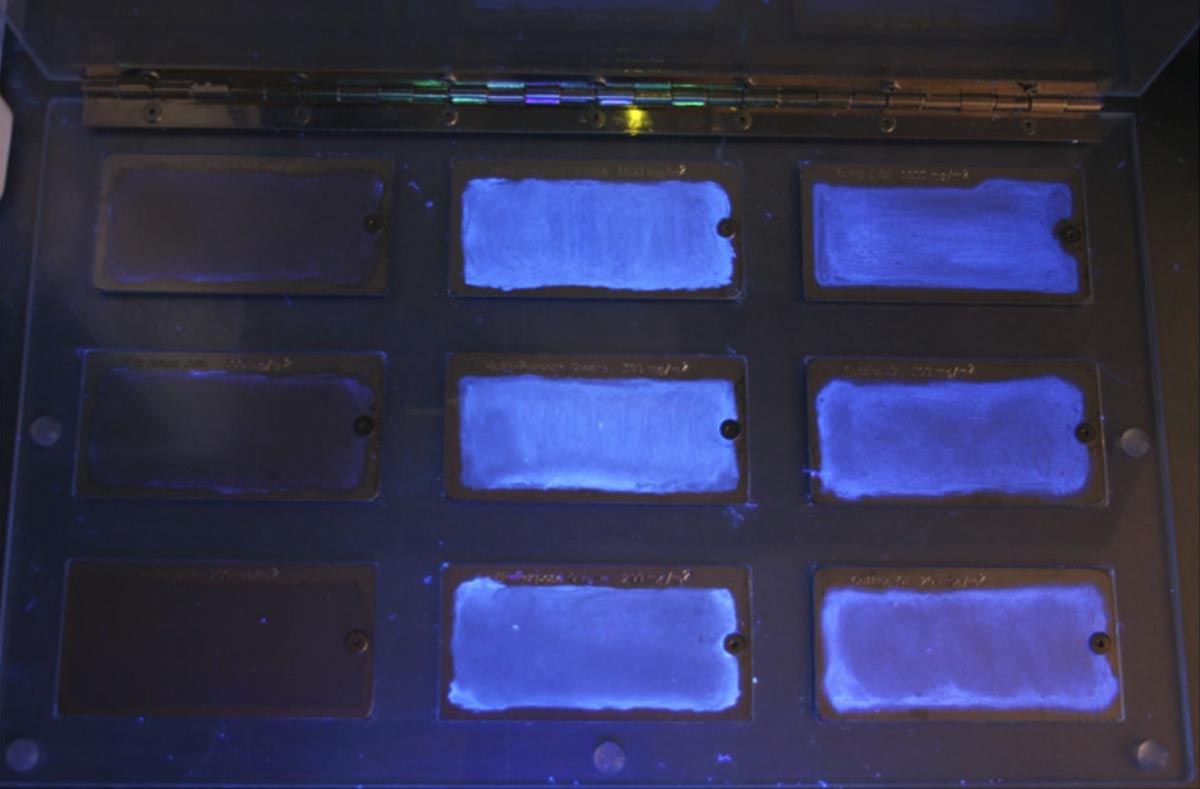
Get Training for Visual Oxygen Cleanliness Inspection
We teach qualitative visual inspection processes as part of our Level 2: O2 practice course, which is fully contained within our level 3 and 4 training courses as well. To aid in teaching visual inspection techniques as well as providing field inspection equipment, we offer a purpose-built O2 Clean Inspection Kit which provides cleaning gear, lights, and prepared training samples to practice visual inspection techniques. Practice is key to reliable performance and interpretation of visual inspection techniques.
Limitations of Visual Inspection
It’s worth repeating that visual inspection has its limitations.
- Even though you may be able to see particles as small as 50 microns, you may not know their exact size or quantity.
- The naked eye is not as good at detecting potentially dangerous levels of NVRs.
- Depending on the part design and accessibility, you may not be able to inspect every surface.
Thus, if you need to show compliance with quantitative cleanliness levels, you will need quantitative cleanliness verification.
Your Partner in Oxygen Safety
If you have questions about oxygen cleaning standards for your unique situation, please don’t hesitate to reach out to us at WHA International. Our experienced team will be happy to help you verify your parts’ cleanliness levels and walk you through an oxygen fire risk analysis, if necessary.
If you need to train technicians for visual inspection, check out our upcoming technical training opportunities or contact us to inquire about custom training options and inspection tools.
Share this entry
Related Articles
Nonmetals Oxygen Compatibility Requirements: Guide to CGA/EIGA Compliance
The Compressed Gas Association (CGA) and European Industrial Gases Association (EIGA) have harmonized key documents providing guidance…
WHA Launches Oxygen Equipment Supplier Certification Program
Ignition and combustion hazards are present in almost all oxygen and oxygen-enriched systems, and catastrophic fires have…
Oxygen Cleaning Service Team Receives Vendor Award
WHA’s oxygen cleaning service team recently received recognition from its client, Trace-A-Matic, for excellent service in a…
Request an expert
consultation
Contact us to request a free consultation with an experienced engineer who can help you better understand your needs and our solutions.