Why clean for oxygen service?
Highlights
- Contamination (like small particulate or non-compatible oils and greases) can lead to dangerous fires in oxygen systems.
- All parts must be specially cleaned before use in an oxygen system.
- Operators must also maintain cleanliness throughout assembly and maintenance.
- WHA International provides technical training for oxygen cleaning and cleanliness inspection.
Recently, updates were published for two important international standards that provide guidance and best practices for oxygen cleaning. Previously, both the Compressed Gas Association (CGA) and the European Industrial Gases Association (EIGA) agreed upon general cleaning philosophies, but they differed in their definition of cleanliness levels (i.e. “how clean is clean?”). Today the two standards have been harmonized to simplify standards internationally through CGA G-4.1 and EIGA IGC 33-18. Those who are familiar with oxygen cleaning specifics can download the complete updated standard document from either CGA’s or EIGA’s websites.
In light of these recent updates, our engineers have organized some thoughts on WHA’s oxygen cleaning philosophy. Read on to better understand how it works and why it’s such an important part of oxygen safety…
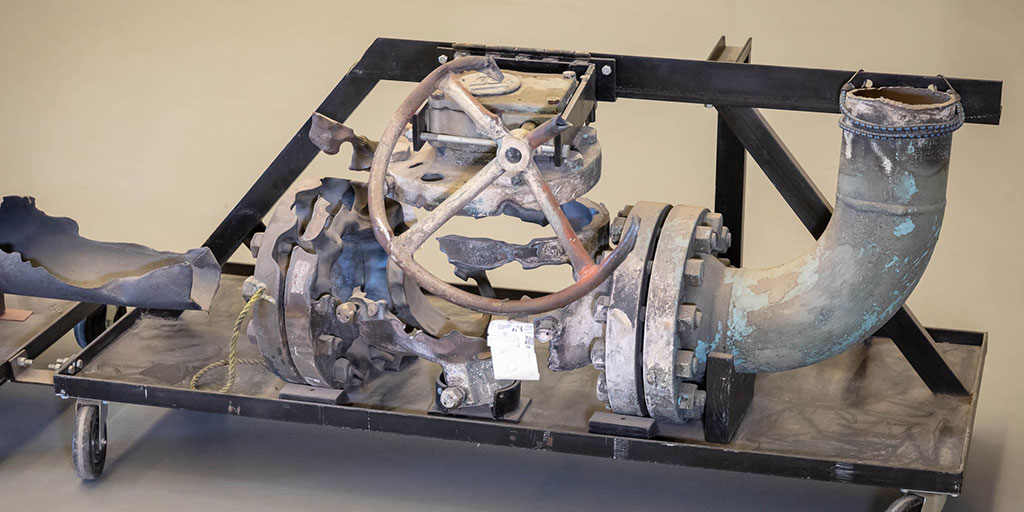
Why is oxygen cleaning so important?
Have you ever noticed the label “use no oil” on an oxygen pressure gauge or other hardware? This warning is prominently displayed on the gauge face because that component was precision cleaned for oxygen use, and it needs to stay clean for safe operation!
When our engineers provide technical training on oxygen cleaning, the first thing they do is reference the fire triangle. Oxygen fires occur when three elements come together: a fuel, an oxidizer, and an ignition source. Simply put, contaminants are fuels that ignite easily in oxygen and burn vigorously. Common contaminants include hydrocarbon-based oils and greases (“use no oil!”) as well as metal particulates and other debris.
The biggest problem with these contaminants is that once they ignite, they can kindle ignition to other less flammable materials. If you have ever started a campfire, you know that you must first ignite paper and small twigs in order to spread the flame to the larger logs. This effect is called a kindling chain, and often contaminants can initiate kindling chains in an oxygen systems because they are so easy to ignite. In fact, it’s a primary contributor to many of the oxygen fires our engineers investigate.
When considering oxygen system and component cleanliness, WHA follows a four-step approach to ensure safe use:
- Start clean
- Verify clean
- Assemble clean
- Maintain clean
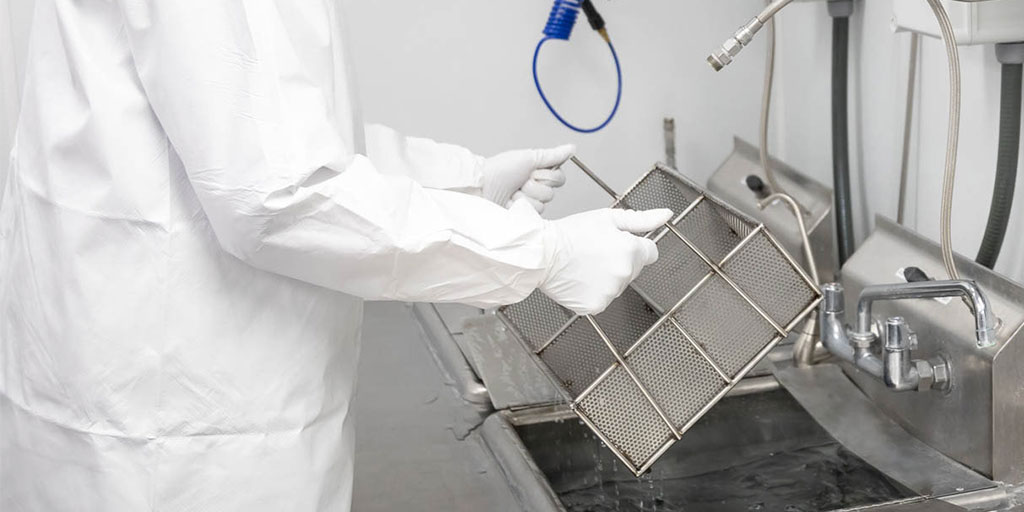
1. Start Clean
Never install a component that is not “bagged and tagged” or marked as oxygen-clean! All piping and components used in oxygen systems MUST be cleaned using a process that has been verified capable of meeting the acceptance criteria published in international cleaning standards such as ASTM G93, ISO 15001, CGA G-4.1, EIGA IGC 33-18, SAE ARP 1176, MIL-STD-1330D, or others.
Precision cleaning of oxygen components typically takes place in designated and controlled cleaning areas and includes:
- Component disassembly
- Cleaning (such as with aqueous detergents and water, acidic or alkaline chemicals, or special solvents)
- Rinsing
- Drying
- Bag and label
Do your components need oxygen cleaning? WHA offers oxygen precision cleaning services with quick turnaround times and exceptional quality control. Our engineers also offer process review and consulting to help clients set up and optimize their own in-house cleaning processes.
2. Verify Clean
After precision oxygen cleaning has been performed, it’s important to verify that the component is cleaned to the proper standards for safe operation. Our WHA clean room facility is specially equipped to perform highly-detailed quantitative cleanliness verification. In the field, our engineers rely upon proven qualitative visual inspection methods.
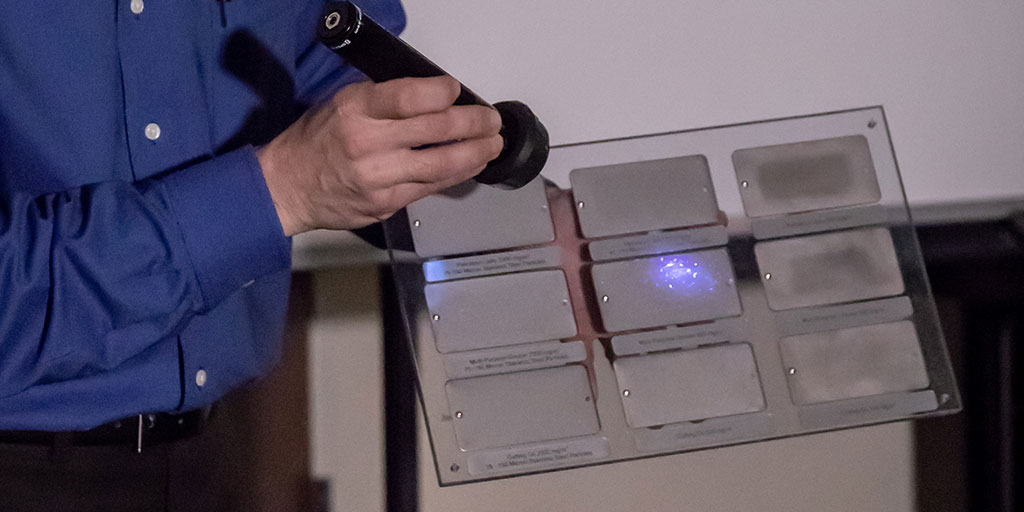
In our technical training courses, we demonstrate oxygen clean verification techniques using our custom-built O2 Inspection Kits to teach students how to perform visual inspections on various hardware. These techniques are simple and inexpensive, but effective in detecting gross levels of contaminant. This is often considered the last line of defense in assuring cleanliness before a component is installed into the oxygen system.
- Aid of bright white light can reveal particles greater than approximately 50 micron (0.002”). These contaminants can include moisture, grease, oil, rust/corrosion, paint, or other debris in large quantities (generally >500mg/m2).
- A black (UV) light is also used for visual inspection because many hydrocarbon-based contaminants and other particles fluoresce at ultraviolet wavelengths. This technique can reveal dust and lint particles greater than 50 micron (0.002”) as well as large quantities of grease and oils.
- Other visual verification methods include using a special lint-free cloth and black/white light to perform a wipe test. This technique is simply another method to detect abnormalities and verify surface cleanliness.
How do you know your components are clean enough? WHA offers oxygen cleanliness verification (OCV) as a standalone service for clients who wish to test the cleanliness of their own parts, components, and systems, or to verify that their cleaning process is successful at complying with a published cleaning standard.
3. Assemble Clean
It’s important to remember that even though a component may have “started clean,” a lot can happen between the time of manufacture and final system assembly. Our engineers have seen multiple instances where oxygen clean hardware is either delivered in an unclean state, or where the cleanliness is compromised during assembly. We’ve even investigated oxygen fires caused by insects building nests inside open oxygen piping during assembly!
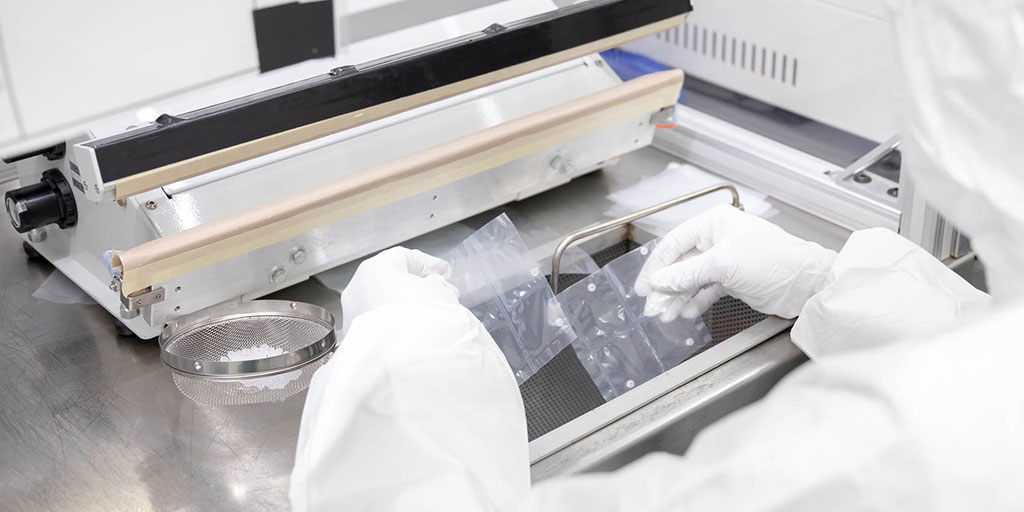
Some best practices for oxygen system assembly include:
- Always assemble oxygen components in a clean area. Avoid assembling outdoors in bad weather or in contaminated air environments. If a clean room is unavailable or impractical, oftentimes you can set up a temporary clean area for assembly that can be sufficient, depending on the application.
- Use visually clean tools
- Prefer clean, powder-free gloves
- Avoid touching oxygen-clean surfaces with leather work gloves or bare hands
- Keep piping components bagged or sealed until ready for install
- Stage necessary assembly items (tools, gaskets, fittings, etc.) nearby
- Do not place ANY foreign objects inside oxygen-clean piping
- Avoid particle generation when installing threaded connections. Use specified oxygen compatible lubricants and pipe tape sparingly, as directed
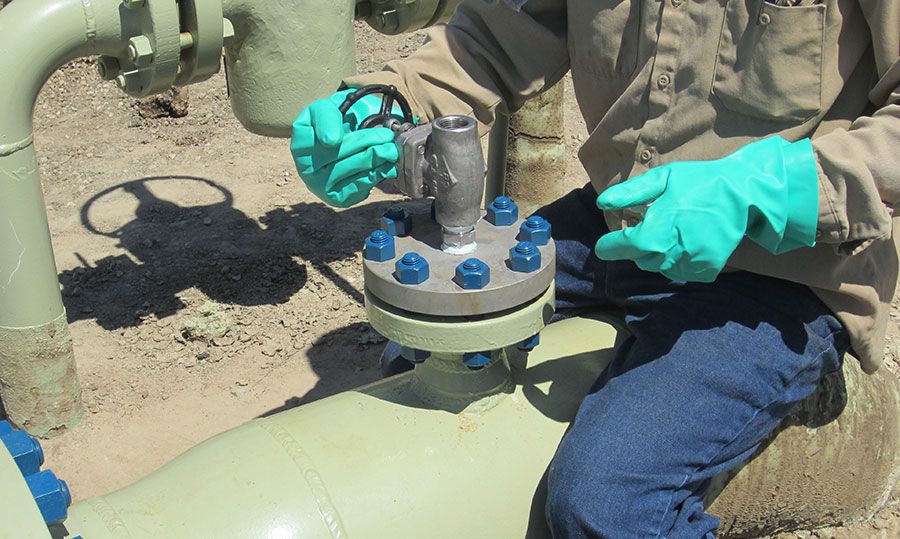
4. Maintain Clean
Finally, it’s essential to maintain proper cleanliness throughout the life of your oxygen system. We like to tell people that once an oxygen system has been initially cleaned and assembled, you’d prefer to never have to reclean it. This goal can often be achieved through good maintenance practices. For disassembly, inspection, cleaning, and reassembly, we teach many of the same principles outlined under “assemble clean” with a few additions:
- Before opening an oxygen system, make sure that its exterior surfaces have been thoroughly cleaned of visible contaminants such as oils, greases, dust and particulates.
- Maintain a clean environment, as much as possible.
- Use clean tools, gloves, and clothing.
- Protect open ports with oxygen-compatible plugs, caps, bags, or flange blinds.
Want to learn more about oxygen cleaning? Our industry-leading oxygen safety training includes basic training on oxygen cleaning. We also offer a special add-on module and custom-built O2 Inspection Kits for those wishing for a more in-depth look at oxygen cleaning, verification, assembly, and maintenance practices.
How can WHA simplify oxygen cleaning for you?
Our experienced engineers and chemists are available to assist with your oxygen cleaning needs through both oxygen cleaning services and technical training.
Because WHA deals with so many different applications of oxygen that require different levels of cleaning, our engineers have learned how to customize both consulting and cleaning services to make it applicable to clients’ specific applications. “There are very different levels of cleanliness out there, and we know how to achieve each of those,” explains WHA engineer Dr. Gwenael Chiffoleau. “That means we can help customers identify the best value in balancing cleanliness level and cost … We’ve supported everything from small, high pressure medical equipment requiring high levels of cleanliness, to large pipeline applications existing in dirtier environments where you still have to maintain the right cleanliness.”
“WHA is unique because we clean our own oxygen systems in addition to our customers’ parts and components … We apply the same meticulous cleaning philosophy and approach to assure that our customers’ systems are just as safe as our own.”
Dr. Gwenael Chiffoleau, WHA International, Inc.
At WHA, we’re also happy to equip companies who would like to handle their own cleaning in-house. Our industry-leading oxygen safety training includes basic training on oxygen cleaning, and we offer a special add-on module and custom-built O2 Inspection Kits for those wishing for a more in-depth look at oxygen cleaning, verification, assembly, and maintenance practices.
Originally published on December 10, 2018.
Share this entry
Related Articles
WHA Launches Oxygen Equipment Supplier Certification Program
Ignition and combustion hazards are present in almost all oxygen and oxygen-enriched systems, and catastrophic fires have…
Oxygen Cleaning Service Team Receives Vendor Award
WHA’s oxygen cleaning service team recently received recognition from its client, Trace-A-Matic, for excellent service in a…
Oxygen Cylinder Safety
An oxygen tank, or “oxygen cylinder,” is a pressurized container that stores and transports oxygen in its…
Request an expert
consultation
Contact us to request a free consultation with an experienced engineer who can help you better understand your needs and our solutions.