Advancing Large-Scale Electrolyzer Safety
Highlights
- Companies are utilizing increasingly larger electrolysis systems to keep up with hydrogen demand.
- New and improved electrolysis technologies are enhancing efficiency, expected lifetime, and cost-effectiveness.
- WHA equips the electrolysis industry to address the unique hydrogen and oxygen safety considerations involved in advancing technologies.
Electrolyzer safety is becoming increasingly important as the industry undergoes significant change to meet the growing demand for hydrogen production at scale. Several notable examples of new large-scale electrolyzer projects include:
- The Aces Delta renewable hydrogen production and storage project in Utah, U.S.A
- A green ammonia plant electrolyzer In Queensland, Australia
- A $25B wind-powered electrolyzer project in Canada
- The world’s largest solid oxide electrolyzer in Mountain View California, U.S.A
- A green ammonia plant electrolyzer in Louisiana, U.S.A
- A 25 GW wind and solar-powered electrolyzer by Green Energy Oman
- Europe’s largest PEM green hydrogen electrolyzer by Shell near Cologne, Germany
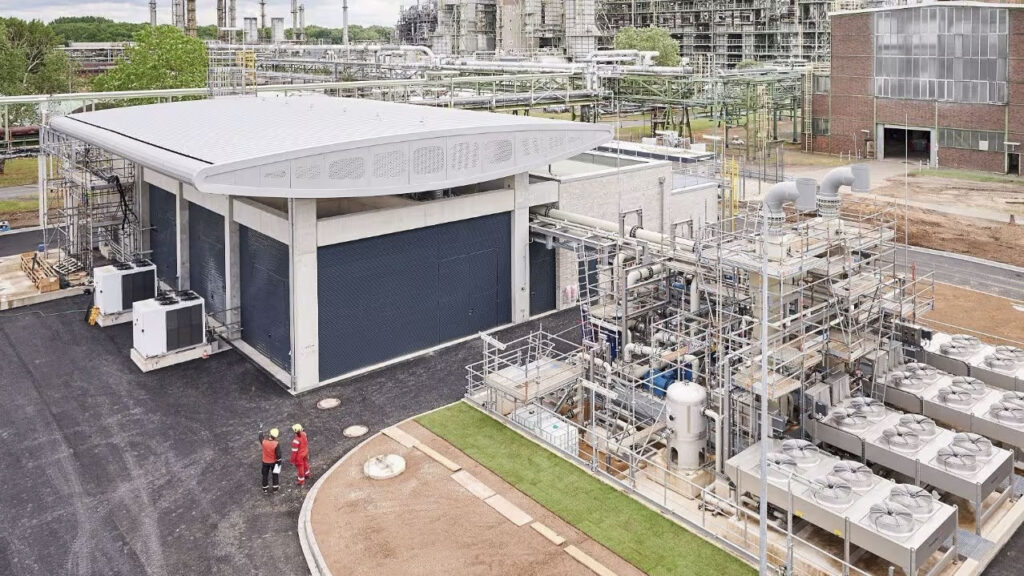
Shifts in Electrolysis Industry to Keep Up with Demand
Advances in electrolysis system materials, designs, and overall system integration are driving the industry’s evolution and shaping its role in the global energy transition.
Recent projects suggest a global progression towards large-scale, efficient, and cost-effective electrolysis systems that often integrate with renewable energy sources. These systems can produce hydrogen for various applications, including transportation, industry, and energy storage.
“Often, increasing the scale of electrolyzers is focused on developing standardized component ‘building blocks’ that can be produced in mass quantities and combined to form a larger energy system,” explains Cory Kreutzer, one of the hydrogen experts at WHA. “As the number of electrolyzers sold in the market increases, economies of scale provide opportunities for reduced electrolyzer and hydrogen production costs.”
Key trends and advancements in electrolysis system technology include:
- Scaling Up for Bulk Hydrogen Production: This shift is driven by the increasing interest in hydrogen as a clean energy carrier for various sectors, such as transportation, industry, and power generation.
- High Efficiency and Low-Cost Electrolyzers: One of the primary goals of the industry is to develop electrolyzers that achieve high energy conversion efficiency while keeping costs competitive. Research and development efforts are focused on optimizing materials and designs to increase efficiency, as well as finding ways to reduce capital, operational expenses, and reliability.
- Renewable Energy Integration: Many large electrolyzer projects are designed to be powered by renewable energy sources, such as wind and solar. This coupling of electrolysis with renewable energy addresses the intermittency issue of renewables by using excess energy during peak production times to generate hydrogen, which can be stored and utilized when renewable energy generation is low. In addition, these projects can help reduce the cost of hydrogen by harnessing excess energy from renewables when the market price for electricity is low.
- Hybrid and Integrated Systems: Electrolyzer systems are increasingly being integrated into broader energy grids. These hybrid systems may combine electrolysis with fuel cells and other energy storage technologies like batteries to ensure a steady supply of hydrogen, as well as grid stabilization services.
- Ammonia and Synthetic Fuel Production: Some large-scale electrolyzer projects are focused on producing ammonia or synthetic fuels, such as green hydrogen-derived ammonia. These products can serve as energy carriers or chemical feedstocks, expanding the potential of electrolysis technology into applications currently dominated by hydrogen produced from fossil fuels.
- Electrolyzer Manufacturing and Deployment: As demand increases, electrolyzer manufacturing is evolving to streamline production processes and reduce costs. Additionally, deployment strategies are being refined to ensure efficient installation, operation, and maintenance of large-scale systems.
- Policy and Investment Support: Governments and private sector investors are recognizing the importance of hydrogen as a clean energy vector. Substantial investments and policy initiatives are being directed toward the development of electrolysis technology, which is contributing to its rapid advancement.
Further Reading: Learn about the top used of industrial hydrogen around the world.
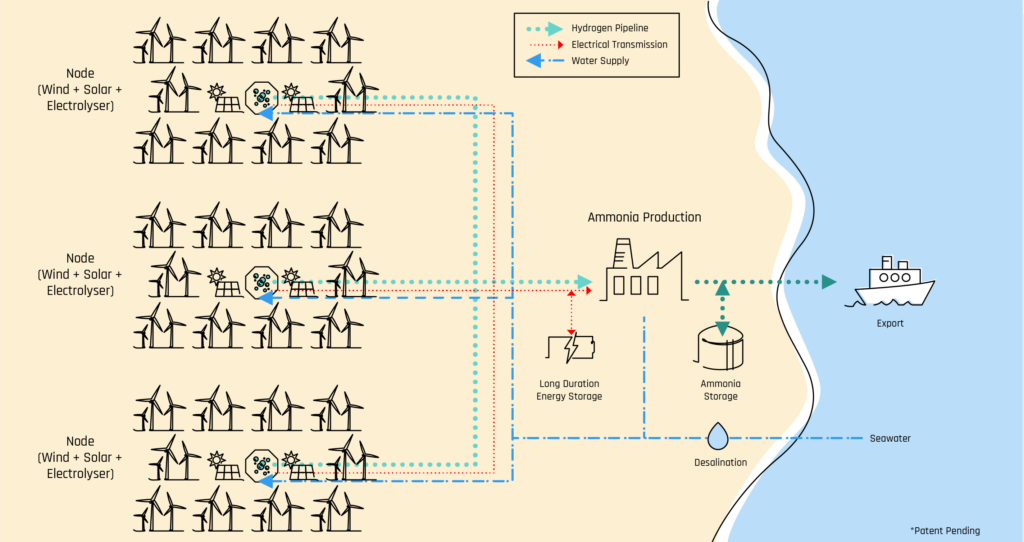
New and Improved Electrolysis Methods
Each electrolyzer technology has its own advantages, drawbacks, and suitability for specific applications. The choice of technology depends on factors such as scale, source of input energy to drive the electrolysis process, efficiency requirements, availability of resources, and cost considerations.
1. Proton Exchange Membrane (PEM) Electrolysis
- Method: In PEM electrolyzers, electricity is used to split high-purity water into hydrogen and oxygen, taking advantage of an electrolyte membrane that conducts protons (H+ ions). The electrolyte membrane separates the hydrogen and oxygen gases by only allowing protons to pass through, facilitating the production of hydrogen.
- Key Features: PEM electrolyzers operate at relatively low temperatures and pressures, enabling fast start-up and shutdown times. They operate at high current density, making them compact relative to some electrolyzer types. They are suitable for being powered by intermittent renewable energy sources due to their quick response and high efficiency at partial loads. PEM systems are more compact, they don’t pose the chemical hazard that the KOH does in alkaline systems, but they have more expensive metal catalysts.
- Applications: PEM electrolyzers are commonly used for small to medium-scale applications, such as hydrogen refueling stations and distributed hydrogen production. However, scale-up of PEM systems for large-scale applications is a major area of emphasis for PEM electrolysis manufacturers.
2. Alkaline Electrolysis:
- Method: Alkaline electrolyzers use a potassium hydroxide (KOH) solution as the electrolyte. Water splitting occurs at the cathode (hydrogen electrode), forming hydrogen and hydroxide ions. Hydroxide ions are then transferred across a diaphragm to the anode to form oxygen.
- Key Features: Alkaline electrolyzers are a mature technology and are known for their reliability, durability, and lower cost compared to newer electrolysis methods. They operate at lower energy density and, typically, slightly higher temperatures compared to PEM electrolyzers.
- Applications: Alkaline electrolyzers are used in a range of applications, including industrial hydrogen production and power-to-gas projects.
3. Anion Exchange Membrane (AEM) Electrolysis:
- Method: AEM electrolyzers are similar to PEM electrolyzers but use an anion exchange membrane instead of a proton exchange membrane. This membrane conducts hydroxide ions (OH-) instead of protons.
- Key Features: AEM electrolyzers offer the advantage of working with non-precious metal catalysts and potentially lower costs. However, they are still in the early stages of development and face challenges related to membrane durability and performance.
- Applications: AEM electrolyzers have the potential to be used in various hydrogen production applications, especially as technology advancements address their current limitations.
4. Solid Oxide Electrolysis (SOEC):
- Method: Solid oxide electrolysis cells operate at high temperatures (typically above 600°C) and split water vapor into hydrogen and oxygen using a solid oxide electrolyte. Electricity and heat are supplied to the cell to drive the electrochemical reaction.
- Key Features: SOECs can achieve high thermodynamic efficiency, especially when waste heat is utilized. They can also be operated bidirectionally as solid oxide fuel cells to generate electricity from hydrogen.
- Applications: SOECs are well-suited for industrial processes that require high-temperature hydrogen, such as ammonia production and steelmaking, where the waste heat can be utilized effectively.
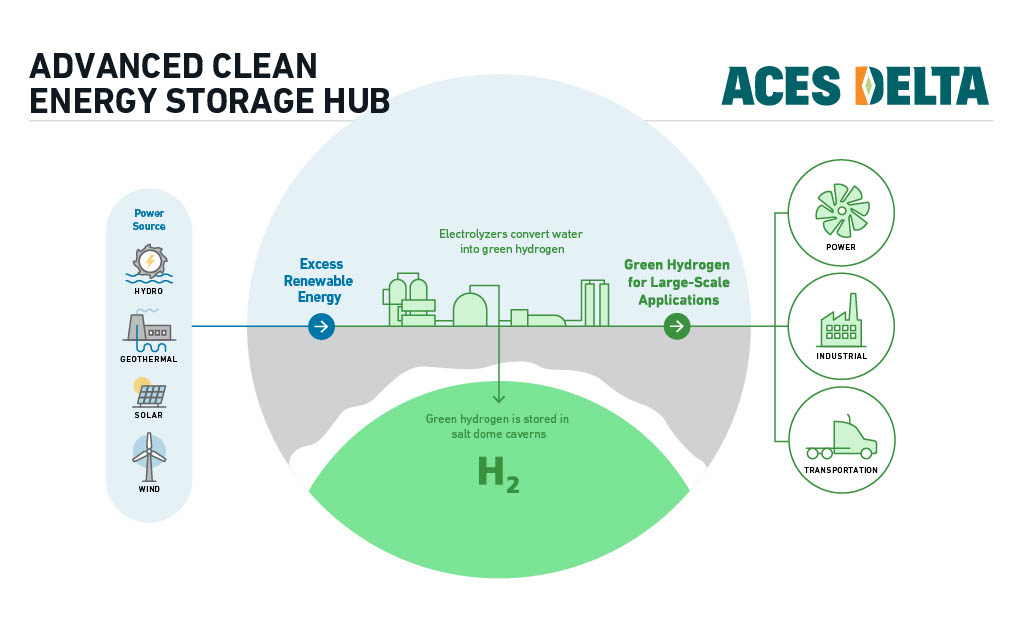
Unique Electrolyzer Safety Considerations
Electrolysis systems incorporate both oxygen and hydrogen, inherently hazardous fluids.
“Not only do the individual hazards associated with hydrogen and oxygen exist, but electrolyzer systems also pose some unique combined hazards,” explains Cory. “Different electrolysis methods each have some unique safety considerations of their own.”
1. Proton Exchange Membrane (PEM) Electrolysis:
- Membrane Degradation: The polymer electrolyte membrane used in PEM electrolyzers can degrade over time due to exposure to high temperatures, high current densities, and impurities in the feedwater, affecting system efficiency and safety. When the membrane degrades, the crossover of hydrogen into the oxygen side of the system increases, resulting in a higher risk of a combustible mixture forming on the oxygen side. Additional safety considerations in PEM systems include the evolution of dissolved hydrogen and oxygen from water in the balance of plant of the electrolyzer system.
2. Alkaline Electrolysis:
- Alkali Leakage: The use of alkaline electrolytes in these systems can lead to concerns about the leakage of caustic solutions, which are corrosive and can be harmful to both human operators and the environment. In addition, damage or degradation of the diaphragm in alkaline systems increases the risk of the mixing of hydrogen and oxygen products, possibly forming a combustible mixture inside the balance of plant of the system.
3. Anion Exchange Membrane (AEM) Electrolysis:
- Membrane Stability: AEM electrolyzers are in early stages of development, and membrane stability is a significant concern. Membranes can degrade due to factors like chemical interactions, pH changes, and operational conditions.
4. Solid Oxide Electrolysis (SOEC):
- High Temperatures: Operating at high temperatures introduces risks of thermal stress, degradation of materials, and potential failures in sealing and insulation, all of which can impact system safety and reliability. In addition, the operating temperature of SOEC systems is above the auto-ignition temperature for hydrogen, so a hydrogen leak from the system or in the area where high temperatures exist will immediately ignite. Steam used in the SOEC systems also poses a hazard that does not exist in low-temperature electrolysis systems.
- Increased Flammability: Materials become more flammable and easy to ignite in oxygen at higher temperatures.
Further Reading: Learn about WHA’s hydrogen risk management philosophy.
WHA helps to advance the electrolysis industry
While the hydrogen and oxygen involved in electrolysis pose unique and complex hazards, companies can mitigate the risks with the right safety practices. WHA currently supports multiple large-scale electrolyzer projects around the world with hazard analysis and safety training.
Contact us to schedule a consultation with one of our engineers and learn more about our available hydrogen and oxygen safety services.
Together, we look forward to a promising future for electrolysis and hydrogen production worldwide.
Share this entry
Related Articles
Hydrogen Tank Explosion Demonstration
Typically, hydrogen is safely stored as a compressed gas or liquid. Although hydrogen is a fuel, it…
Hydrogen Cleaning: Ensuring Safety and Reliability in Pressurized Hydrogen Systems
Hydrogen is an increasingly important and prominent energy carrier, with applications ranging from fuel cells to electrolyzers…
Battery Safety Insights with Nic Linley, Electrical Engineer
Battery technology continues to evolve rapidly in the 21st Century, powering an expanding array of devices and…
Request an expert
consultation
Contact us to request a free consultation with an experienced engineer who can help you better understand your needs and our solutions.