WHA International Advances NASA Oxygen Safety Methods for Industry
WHA International has shared a close relationship with NASA since its inception in 1987. Many of WHA’s senior personnel came straight from the administration, and the two organizations continue to partner on projects today.
Recently, WHA’s Hazards Analysis and Technical Training Lead Elliot Forsyth paid a visit to Kennedy Space Center (KSC) in Florida to lead an oxygen safety training course custom tailored for NASA personnel and contractors.
“NASA has several different areas around the KSC campus where they use oxygen for a myriad of applications,” shares Elliot. “They fill oxygen cylinders for breathing gas, ground support, and testing purposes, and they have other systems where they supply either gaseous oxygen (GOX) or liquid oxygen (LOX) directly to launch vehicles for use as propellants or on-board breathing gas applications.”
Elliot led KSC personnel through a custom-tailored version of WHA’s Level 2 course on the fundamentals of oxygen systems operations and maintenance, Level 3 on oxygen system/component design, and Level 4 course on oxygen system fire risk analysis. These upper-level courses are particularly relevant as NASA has strict requirements to perform oxygen fire risk analysis (OFRA) — or oxygen compatibility assessments (OCAs) as NASA terms them — on all oxygen equipment, including flight and ground support equipment.
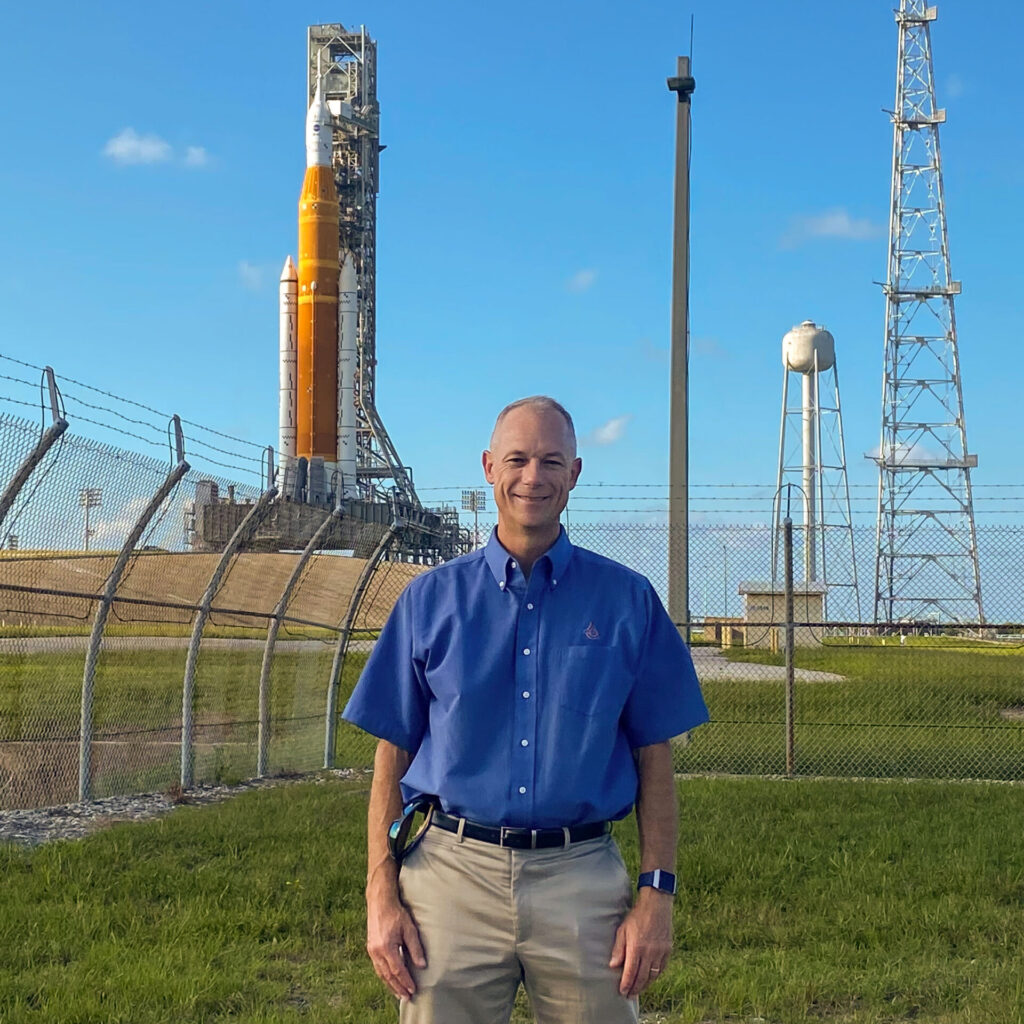
A shared history of oxygen safety
Many of WHA’s technical personnel were involved in the history of the oxygen safety programs developed at NASA, including WHA’s CEO Dr. Barry Newton. Elliot Forsyth also started his career at NASA White Sands Test Facility (WSTF) in Las Cruces, NM — considered the Center of Expertise within NASA for oxygen safety. There, they developed groundbreaking test systems, test data, analysis methodologies, and safety training curriculum.
WHA’s present technical personnel contributed to all 135 space shuttle flights since the beginning of the program. They have also aided in the development of the International Space Station (ISS) and are now contributing to the commercialization of spaceflight by assisting several prominent space flight companies and commercial launch facilities in North America. Former WHA consultants (now retired) also participated in the NASA Mercury and Apollo space programs.
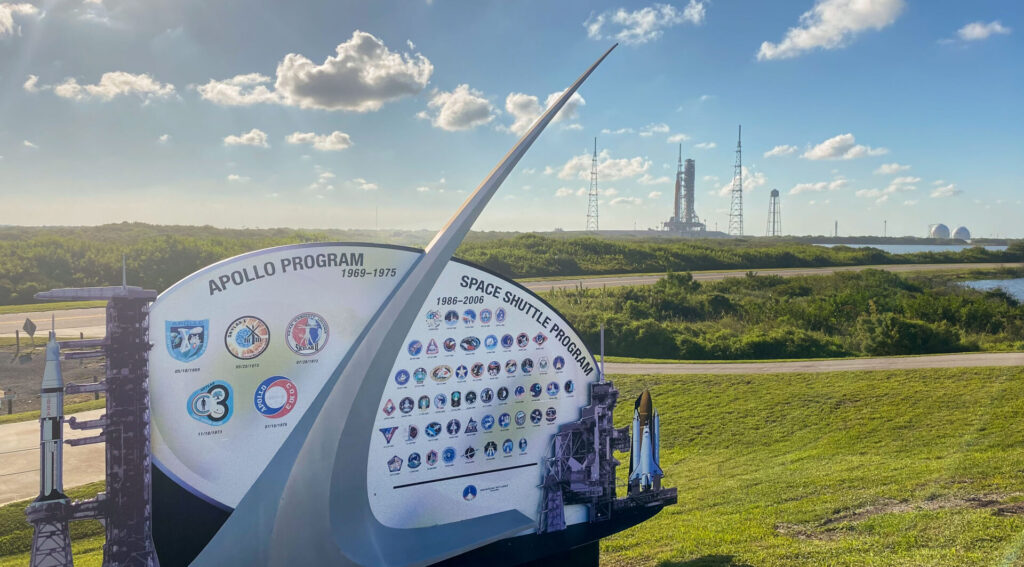
“A lot of research and development went into understanding materials compatibility, ignition mechanisms, oxygen fires, and safe oxygen system design,” explains Elliot. “NASA has always pushed the limits of oxygen technology. Several cornerstone fire incidents inspired follow-up research, such as the Apollo 1 tragedy in 1967 and the spacesuit fire at Johnson Space Center in 1980. This research laid the groundwork for our understanding of oxygen safety today.”
Since the beginning, WHA has continued to attract talented minds with NASA backgrounds. Recent additions like Dr. Harold Beeson provide unique skillsets and perspectives on chemistry and hydrogen safety.
“We all owe a tremendous debt to NASA and its various entities,” says Elliot. “It’s a unique government organization committed to pushing the boundaries of science and publishing research that can be shared with the public. We all benefit as a result.”
Advancing NASA innovations to serve industry
From the shadows of NASA’s historical advancements and cutting-edge technology, WHA International emerged as a leader in technology transfer from the government to the private sector. WHA has applied NASA’s developments in oxygen materials compatibility, design, cleaning, fire risk analysis, and technical training to meet the needs of commercial industries.
“NASA has their own unique methods developed for highly specialized aerospace applications,” shares Elliot. “This is understandable considering the severity of their systems and their very narrow margins for safety. Their designs often have to be more conservative than general industry applications because the consequences of an oxygen fire in a NASA system are almost always severe.”
Because of WHA’s extensive work with all industries that use oxygen — industrial piping and equipment, medical applications, aircraft oxygen, chemical processing, metal refining, and many others — WHA engineers have been able to apply sophisticated NASA methods to commercial applications in very practical ways. In fact, one of WHA’s mottos is, “We simplify oxygen safety.”
“Industrial oxygen applications might use 24-30 inch piping to transmit massive volumes of oxygen to a plant process, and those are very different systems than the small high-pressure oxygen tubing NASA might use in ground support equipment or flight hardware,” says Elliot. “The concepts for avoiding ignition and fire are the same, but the operational conditions and end-uses in industry are all over the map. We help connect the dots for these highly-varied applications.”
Because of their background with NASA’s oxygen safety standards and current work with oxygen industries, WHA personnel are highly involved with global standards development through organizations like ASTM International, Compressed Gas Association (CGA), European Industrial Gases Association (EIGA), International Standards Organization (ISO), and the National Fire Protection Association (NFPA). These valuable partnerships have further accelerated technology transfer and oxygen safety in materials compatibility, system design, cleaning, fire risk analysis, and other areas.
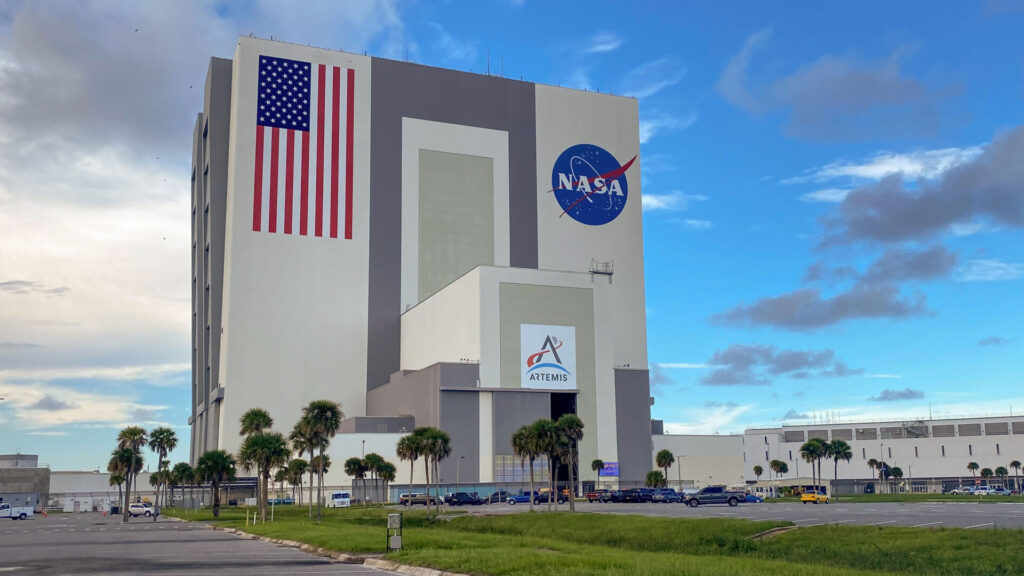
A sustained link between government and industry
Over the years, WHA has developed many unique oxygen test capabilities for materials and components. But sometimes, special projects still require the scale and complexity that can only be found at NASA!
WHA maintains a Space Act Agreement that allows it to work closely with NASA WSTF, providing WHA (and its clients) access to NASA’s unparalleled capabilities. This unique partnership is not easy to obtain, so it serves as a valuable opportunity, especially for smaller companies that couldn’t arrange a Space Act Agreement of their own.
Get cutting-edge oxygen safety training
WHA’s technical training is the perfect solution if you’re looking for state-of-the-art practical training founded on international standards, including those from NASA.
“Regardless of your industry, we teach oxygen safety courses for all levels of personnel, each rooted in the latest technical standards yet practical to implement for your end uses,” explains Elliot. “We simplify oxygen safety for our clients.”
Check out our training page for upcoming events, or you can contact us to inquire about private corporate training customized for your unique needs and applications.
Share this entry
Related Articles
Battery Safety Insights with Nic Linley, Electrical Engineer
Battery technology continues to evolve rapidly in the 21st Century, powering an expanding array of devices and…
Oxygen Cylinder Filling System Fire Case Study
Oxygen cylinders and pressure systems quietly hold enormous amounts of energy. When things go wrong, the results…
WHA Presents O2 Safety Papers at 2024 ASTM G04 Symposium
In October 2024, Gwenael Chiffoleau, Nic Linley, and Brent Houser traveled to Prague for the 16th ASTM…
Request an expert
consultation
Contact us to request a free consultation with an experienced engineer who can help you better understand your needs and our solutions.