NASA Oxygen Safety Spinoff
This summer, you have no doubt heard some of the buzz surrounding the 50th anniversary of the Apollo 11 moon landing. At WHA, we’re proud of our past and continuing efforts to support both government and private space exploration. We’re indebted to NASA and the Apollo program, both of which played a huge role in developing the new science of safety with oxygen, hydrogen, and other hazardous fluids.
“Ever since the initiation of plans for the first rockets to outer space utilizing liquid oxygen, NASA and its contractors have expended great effort in developing information on the compatibility of materials with oxygen.”
Robert Neary, Keynote for first ASTM G-4 symposium, March 31st 1982.
Safety Technology Spinoff
In this article we’re taking a look at a few of the most notable safety advancements that started with NASA. Technology “spinoff” is a phrase commonly attributed to NASA innovations that find new applications in industry and consumer goods. Since the founding of the agency, this spinoff has been touted as a major return on the tax dollars that fund it. Indeed, NASA programs like the Apollo missions have made a huge impact on the science of safety.
Since the 1990s, WHA has operated as a direct link to industry for NASA, providing technical services to the public and advancing technology and understanding that first began with the space program. Any organization that uses oxygen, hydrogen, or other hazardous fluids today can do so safely, in part, due to innovations from NASA.
Here are just a few elements of safety spinoff that began with NASA …
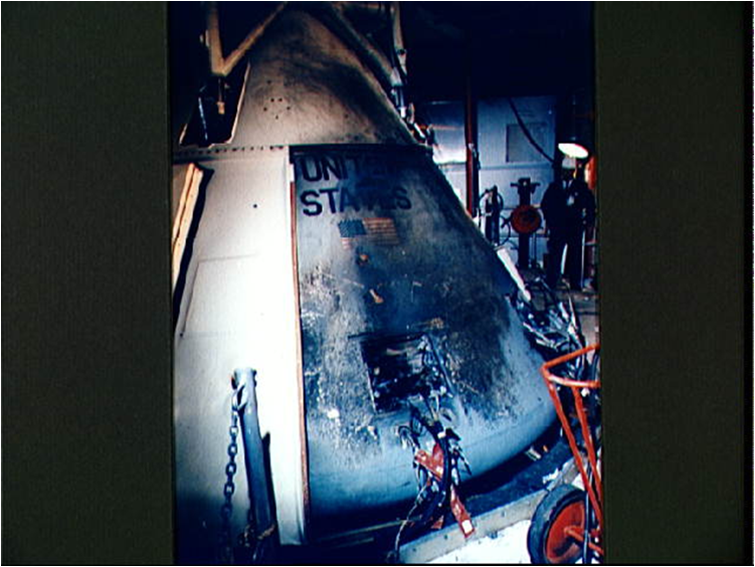
1.Industry Standards
Early accidents with oxygen (most notably the Apollo 1 tragedy in January of 1967) were a huge wake-up call to NASA and industry. Oxygen hazards were generally understood within certain industries that used oxygen, but there was a large deficiency in documented industry standards and best practices for oxygen safety. Since that time, countless NASA engineers, including many that currently work for WHA, have contributed their expertise to developing industry standards for oxygen safety through ASTM Committee G04, which was founded in 1975.
This committee helped establish a better global understanding of oxygen testing, oxygen system design, materials selection, oxygen cleaning, and oxygen fire investigation. These same standards are still being used by NASA and commercial space companies today as a foundation for the safety of oxygen systems used for both ground support and flight hardware.
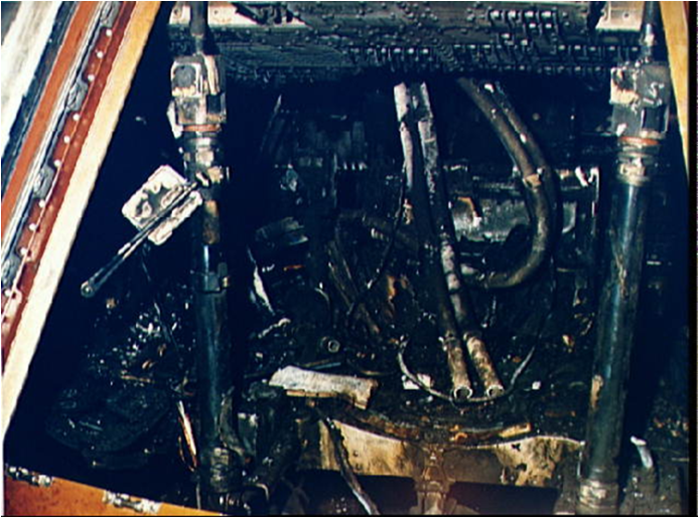
2. Compatibility of Materials in Oxygen
Investigations to the Apollo 1 fire highlighted serious flaws related to the flammability of materials chosen for the pure oxygen environment inside of the command module. NASA lacked an understanding about the flammability of materials in oxygen-enriched atmospheres and also lacked a consistent materials control program.
This urgent need for better understanding resulted in the establishment of multiple test methods developed at NASA White Sands Test Facility and other NASA centers to evaluate the ignition and flammability of materials in oxygen-enriched atmospheres. Many of these tests were later transitioned into full consensus industry standards through ASTM Committee G04.
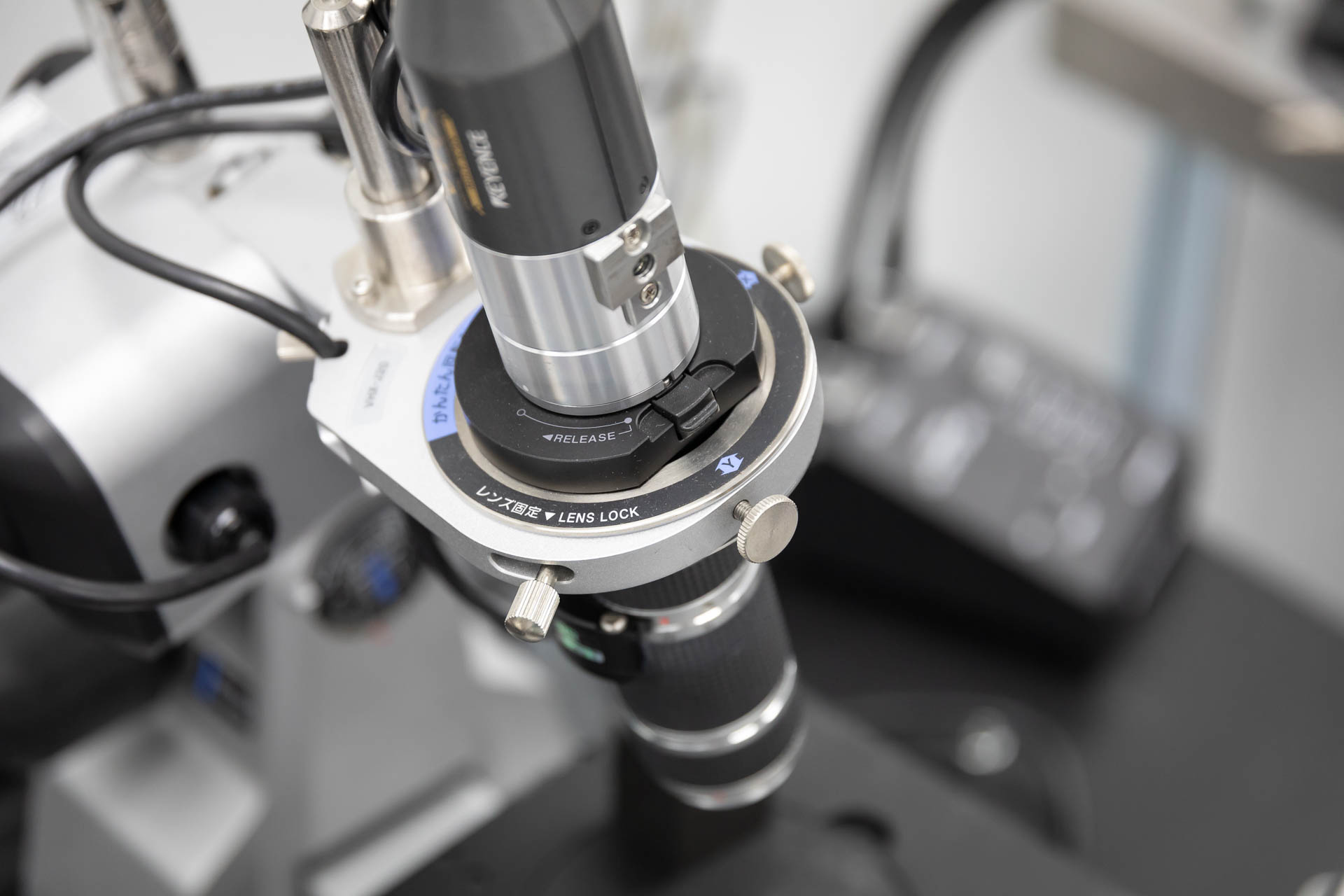
3. Oxygen precision cleaning
Along with spurring improvements to material compatibility, early oxygen incidents at NASA also highlighted the need for better understanding and methodology for oxygen cleaning. All oxygen components and systems, from small oxygen regulators to large industrial oxygen systems, are vulnerable to fires caused by contaminants like greases and particulates. Because of this, all oxygen components and systems must be precision cleaned and maintained clean to be free of these contaminants.
NASA first began documenting and formalizing oxygen cleaning methods early in the space program, and WHA engineers have also been heavily involved in oxygen cleaning and the development of international oxygen cleaning standards.
Today WHA operates its own oxygen clean room that supports the precision cleaning of, on average, over 2500 oxygen parts per week. As evidence of this experience and expertise, WHA currently serves as the technical contact for ASTM G93 (Standard Practice for Cleaning Methods and Cleanliness Levels for Material and Equipment Used in Oxygen-Enriched Environments).
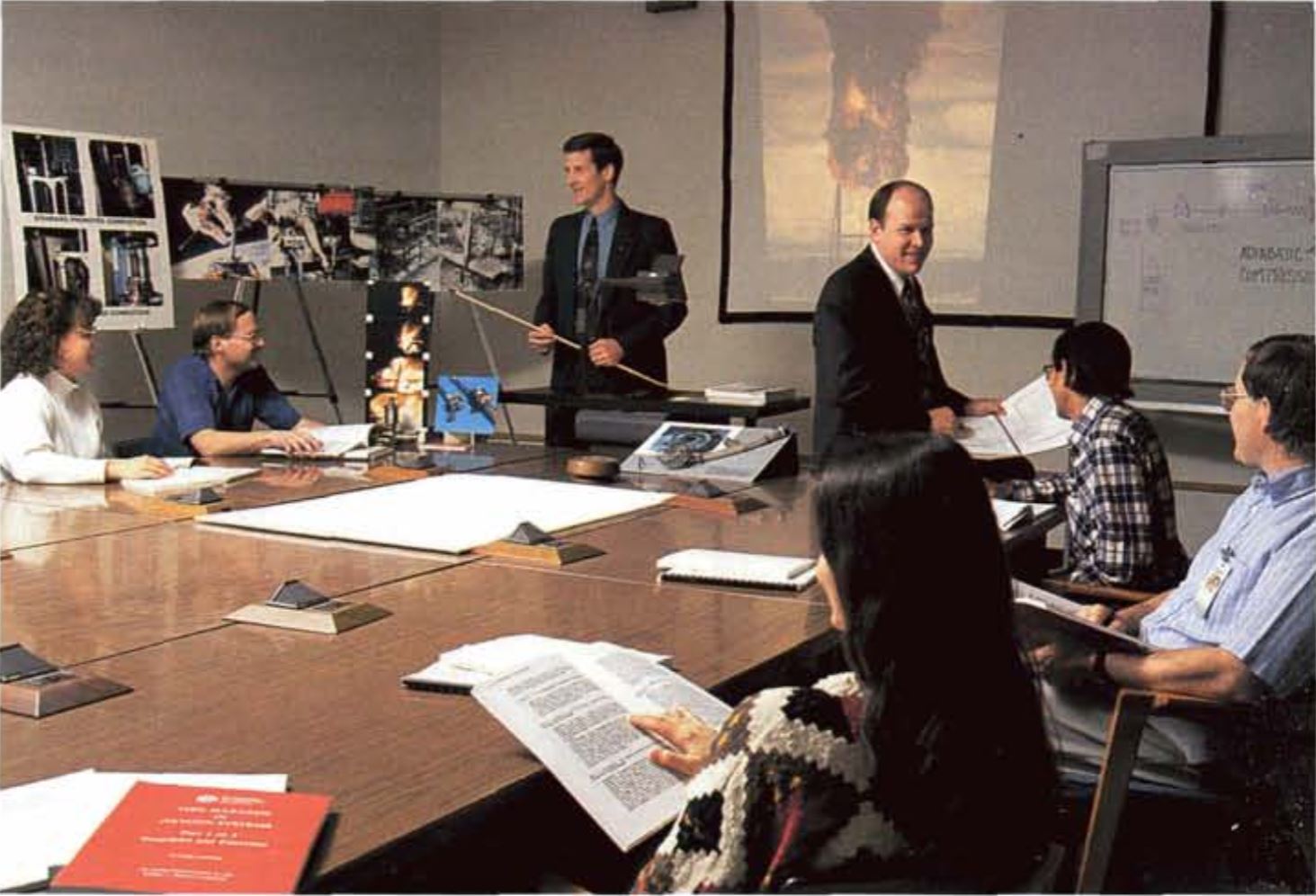
4. Knowledge Transfer
Through decades of failure analysis, hazard analysis, and testing, both WHA and NASA have accrued a wealth of safety knowledge to share with industry. WHA engineers started publishing and presenting peer-reviewed technical papers for industry advancement at the ASTM G04 Committee Symposium in 1995, and they continue to do so today. In addition, Dr. Barry Newton, WHA’s CEO and a former NASA engineer, was a co-developer and instructor of ASTM’s Oxygen Safety Training courses from the early 1990s. WHA has built on this foundation by developing its own custom-tailored oxygen safety training and consulting packages for clients in all industries that use oxygen.
Further, just as NASA has openly shared results of their material compatibility tests for industry benefit, WHA also strives to push industry forward by sharing data. Today WHA offers and maintains the only commercially-available oxygen materials compatibility database, including hundreds of test results freely available online through WHA’s website.
Long-standing cooperation and synergy between NASA and WHA have contributed to increased knowledge about oxygen hazards and implementation of safe practices through harmonized international standards.
5. Better oxygen equipment design and testing
On April 18, 1980, another notable oxygen fire helped trigger industry safety improvements when an unoccupied space suit caught fire during testing at the NASA Johnson Space Center in Houston. A technician was injured, but fortunately there were no fatalities. The equipment recovery cost; however, was estimated at $20 million. Investigations showed that the fire involved a high-pressure oxygen component and manifold made of aluminum — a material we now know to be quite flammable if ignited in oxygen.
Aluminum is highly desirable for aerospace and other applications that require strength and light weight, but given its inherent flammability and many notable fires both within NASA and industry, it became clear that safer oxygen equipment designs were needed, and better test methods were needed to evaluate the ignition risk of aluminum used in oxygen components.
Over several years, WHA and NASA partnered to perform testing and design experimentation which resulted in new equipment designs utilizing a more fire-resistant copper-nickel alloy in “severe areas” of the design but still allowing for the use of weight-saving aluminum in non-severe areas.
One outcome of these test programs was the development of a new standard test for evaluating ignition risk in oxygen components, ASTM G175, jointly developed by NASA, WHA, and partnership with industry through ASTM. Today, new medical oxygen regulator designs are tested to ASTM G175 or similar industry test standards to ensure their safety. These tests are routinely conducted by WHA.
Here’s to NASA
The next time you visit a hospital, sit on an airplane, or see or any of the thousands of applications for oxygen use around us every day, you might take a moment to reflect on the scientists and astronauts at NASA who helped create and advance the field of oxygen safety. These men and women dedicated their careers — sometimes sacrificing even their lives — to help mankind reach the stars and make the world a safer place.
As for us at WHA, we’re thankful for a shared history of innovation together with NASA, and we look forward to a bright future full of new adventures in space and right here on Earth. The sky is the limit — or is it?
Share this entry
Related Articles
Nonmetals Oxygen Compatibility Requirements: Guide to CGA/EIGA Compliance
The Compressed Gas Association (CGA) and European Industrial Gases Association (EIGA) have harmonized key documents providing guidance…
WHA Launches Oxygen Equipment Supplier Certification Program
Ignition and combustion hazards are present in almost all oxygen and oxygen-enriched systems, and catastrophic fires have…
Oxygen Cleaning Service Team Receives Vendor Award
WHA’s oxygen cleaning service team recently received recognition from its client, Trace-A-Matic, for excellent service in a…
Request an expert
consultation
Contact us to request a free consultation with an experienced engineer who can help you better understand your needs and our solutions.