Oxygen Cylinder Filling System Fire Case Study
Highlights
- WHA investigated a fire that occurred during the use of an oxygen cylinder filling system.
- The fire’s origin was traced to a seal in the residual pressure valve (RPV).
- Several operational and design issues contributed to the ignition and fire.
Oxygen cylinders and pressure systems quietly hold enormous amounts of energy. When things go wrong, the results are anything but quiet. In the presence of “enriched” oxygen, even “fireproof” materials can ignite and burn in a violent combustion reaction.
That’s precisely what happened in a recent oxygen cylinder filling system fire. WHA International was called to find out what went wrong.
The subsequent investigation highlights several operational and design issues that are critical to preventing similar incidents in the future.
Incident description
This incident occurred while personnel were operating an oxygen cylinder filling system at a commercial plant.
Oxygen cylinder filling systems are designed to simultaneously fill multiple high-pressure cylinders with medical-grade or industrial oxygen. They are a key part of gas distribution in various sectors, including healthcare, manufacturing, and research.
This system refilled gaseous oxygen (GOX) cylinders to a nominal pressure of 220 bar (3,191 psig). The cylinder filling racks included two manifolds of cylinders, each containing twelve 20 L cylinders and three 50 L cylinders. GOX was supplied from a cryogenic liquid oxygen (LOX) pump and vaporizer.
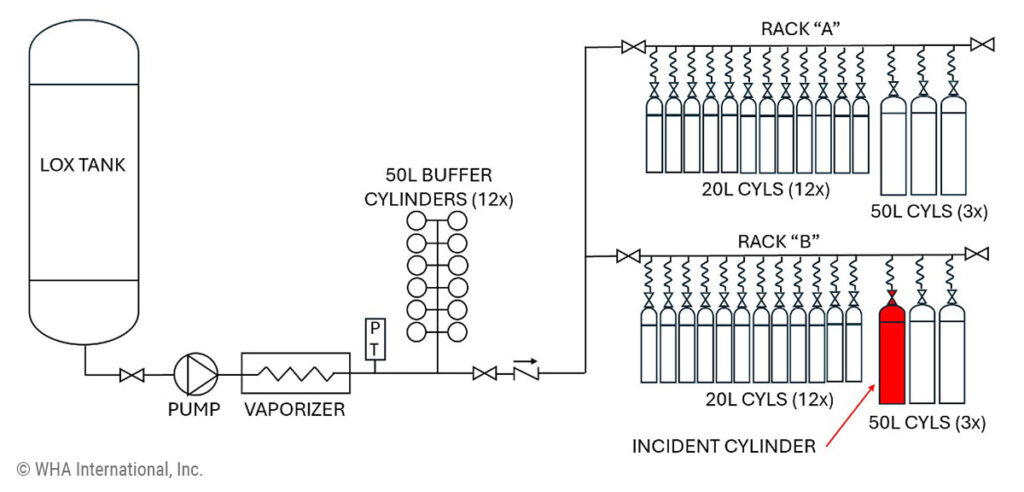
Post-incident observations revealed that an operator was likely closing the cylinder valves after filling when he discovered that one cylinder’s valve had never been opened and, therefore, had not been filled.
He opened the valve in question, and the cylinder immediately exploded, flying off the filling rack and violently ejecting the valve from the top of the cylinder. Another nearby employee heard the deafening bang and witnessed a shower of sparks.
The system operator suffered burn injuries but fortunately avoided further harm from the violent reaction.
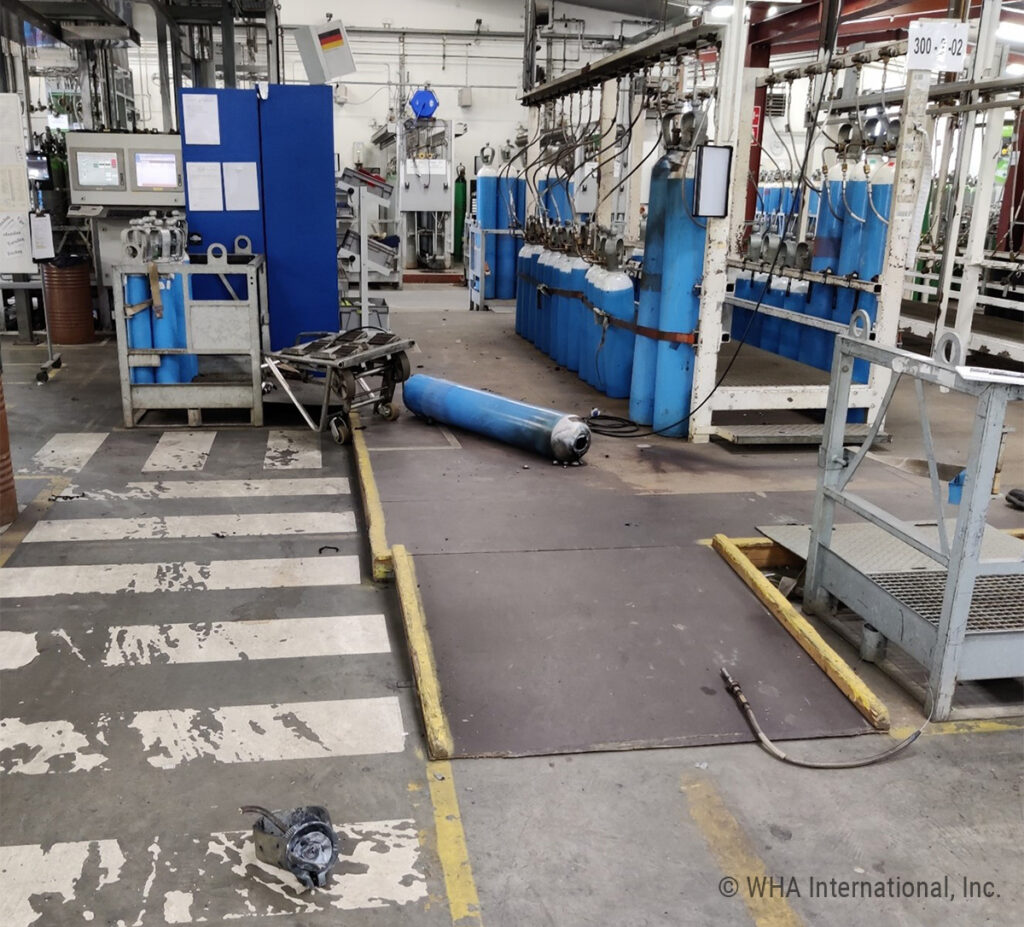
What went wrong? WHA looks for answers
After the incident, WHA stepped in to unravel the mystery behind the blaze. WHA Engineers Brad Forsyth and Brian Anderson served as the principal investigators tasked with finding the most probable fire origin and mechanism of ignition.
The team evaluated the damaged equipment, reviewed incident data, and analyzed materials to determine a timeline and sequence of events leading up to the fire.
How could such a routine task turn into a life-threatening fire so quickly? Let’s take a look at the details…
Key findings
Oxygen fire origin: The fire’s origin was traced to a seal in the residual pressure valve (RPV) at the cylinder valve outlet.
Ignition mechanism: The ignition likely resulted from “flow-induced heating” (also known as “flow-friction”), where high-pressure gas flows across non-metal materials and generates heat.
Kindling chain: Damage observed in the cylinder valve and cylinder suggested a kindling chain developed from the ignition and burning of the RPV seal during high gas flow and, subsequently, the cylinder valve seat and filter. Combustion and melt-flow patterns indicated the fire flowed through the cylinder valve and into the cylinder. This fire (fueled by the burning RPV seal, cylinder valve seat. and filter) caused internal ignition of the carbon steel cylinder at its neck.
Catastrophic failure: Internal carbon steel burning occurred until the cylinder neck structure failed due to thinning and heating, resulting in the ejection of molten metal.
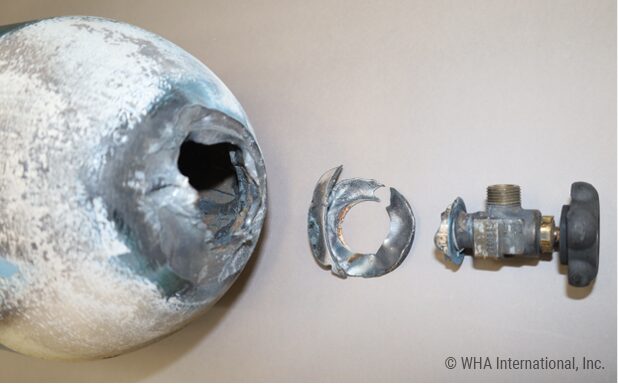
Important lessons learned
WHA’s investigation revealed several key lessons learned from this dangerous oxygen fire. Takeaways involved materials selection, component design, and best practices for operation and maintenance.
MATERIALS: UTILIZE OXYGEN-COMPATIBLE MATERIALS
The fire’s origin was linked to the RPV poppet O-ring at the cylinder valve outlet, which ignited during high flow into the cylinder. Fast-flowing oxygen propelled hot combustion products through the cylinder valve, kindling fire to other materials along the way.
Key takeaway: Using more ignition-resistant materials, such as copper or nickel alloys, can mitigate ignition risk in similar scenarios. ASTM G88 recommends using the most oxygen-compatible materials wherever practical.
DESIGN: AVOID OXYGEN CYLINDER VALVE FILTERS
WHA observed that the valve was equipped with a threaded filter fitting. The filter, which was carbon steel coated with copper and had a thin cross-section, likely provided the intermediate kindling element with sufficient energy to ignite the bulk cylinder.
Key takeaway: Filters may accumulate flammable debris and should be avoided where bi-directional flow can occur in oxygen service. EIGA Safety Info 21/19 specifically recommends against using filters for oxygen cylinder valves
DESIGN: PREVENT FLOW-INDUCED HEATING
WHA determined that the design of the cylinder valve could have accentuated the effect of flow-induced heating within the component. The flow path around the RPV valve may have been the most restrictive region of the system. Additionally, the O-ring was likely susceptible to “blow out,” meaning the high-pressure gas could have dislodged the part, creating further restriction and unintended consequences.
Key takeaway: ASTM G88 provides guidance regarding avoiding designs and scenarios that can contribute to flow-induced heating ignition hazards, including configurations where reverse pressurization could force O-rings out of their grooves.
OPERATION: AVOID HIGH DIFFERENTIAL PRESSURES
Under normal operating procedures, an oxygen filling system will gradually bring multiple cylinders up to pressure at a controlled rate. This fire likely occurred when an operator opened a cylinder valve after the filling cycle, creating a high-pressure differential between the empty cylinder and the fully pressurized filling system.
Key takeaway: OSHA and other international regulations legally compel employers to provide proper safety training for all personnel who work with or around oxygen. Personnel should be trained to recognize and avoid scenarios that could result in operating oxygen equipment with a dangerous high-pressure differential.
Learn More About this Case Study
The full details of this case study will be available in “Oxygen Cylinder Fire During Filling” by Brad Forsyth and Brian Anderson. This technical paper was presented at the ASTM G04 Symposium in Prague on October 21-22, 2024 and will be published in ASTM STP 1653.
WHA leadership is active in the ASTM G04 Committee on Compatibility and Sensitivity of Materials in Oxygen Enriched Atmospheres. They regularly contribute papers and expertise to help improve the science of oxygen safety worldwide.
Share this entry
Related Articles
Battery Safety Insights with Nic Linley, Electrical Engineer
Battery technology continues to evolve rapidly in the 21st Century, powering an expanding array of devices and…
Oxygen Cylinder Filling System Fire Case Study
Oxygen cylinders and pressure systems quietly hold enormous amounts of energy. When things go wrong, the results…
WHA Presents O2 Safety Papers at 2024 ASTM G04 Symposium
In October 2024, Gwenael Chiffoleau, Nic Linley, and Brent Houser traveled to Prague for the 16th ASTM…
Request an expert
consultation
Contact us to request a free consultation with an experienced engineer who can help you better understand your needs and our solutions.