WHA Enhances Electrolysis System Safety
WHA has worked closely with hydrogen and oxygen for decades. Recently, industry has shown increased interest in a unique intersection between the two gases: electrolysis systems. In response, the team at WHA has begun offering specialized hazard analysis services and developed a new electrolysis system safety training course.
“Hydrogen and oxygen both have distinct hazards. Those hazards can be amplified if a fault enables them to mix within an electrolysis system,” explains Danielle “Dani” Murphy Ph.D., one of the resident hydrogen safety specialists at WHA.
A tragic example of these increased hazards occurred at a research facility in Korea, where an alkaline water electrolyzer was set up to generate hydrogen. On May 23, 2019, oxygen permeated the hydrogen storage tank, creating a high-pressure combustible mixture. The tank exploded with the power of 50 kg of TNT. It caused two fatalities, six injuries, and over $30 million in damage.
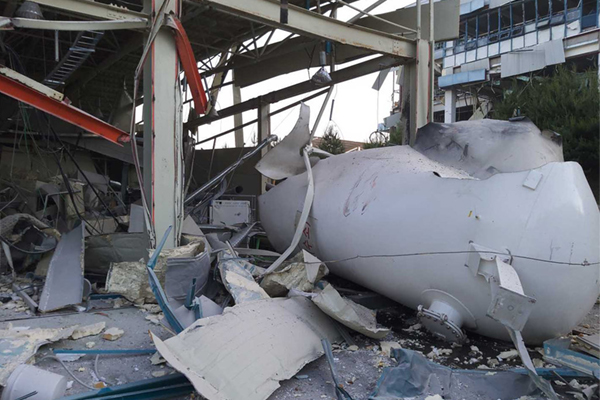
Combined risks of hydrogen and oxygen
To understand and mitigate the hazards of electrolysis systems, we must consider the inherent risks of hydrogen. For that, we look to WHA hydrogen expert Cory Kreutzer, who helped develop the new course on electrolysis system safety.
“Hydrogen is easily combustible,” Cory explains. “It has one of the widest flammability ranges of any fuel and will ignite at anywhere between 4% and 75% concentration in air. It’s much easier to create a combustible mixture of hydrogen compared to other fuels like propane, which will only ignite at 2-10% concentration in air.”
“Hydrogen also has an extremely low ignition energy, meaning it takes little effort to start a combustion reaction. Hydrogen needs as little as .02 mJ of energy to ignite in air, making it 14.5 times easier to ignite than propane, which requires at least .29 mJ. Electrolysis systems have many Balance of Plant (BoP) components and processes that could easily become ignition sources.”
If H2 and O2 mix unintentionally, the results can be deadly. In pure oxygen, hydrogen becomes even easier to ignite and will combust with significantly more energy. Increased oxygen concentrations also increase the severity of an energetic explosion which releases a blast of energy through a pressure wave.
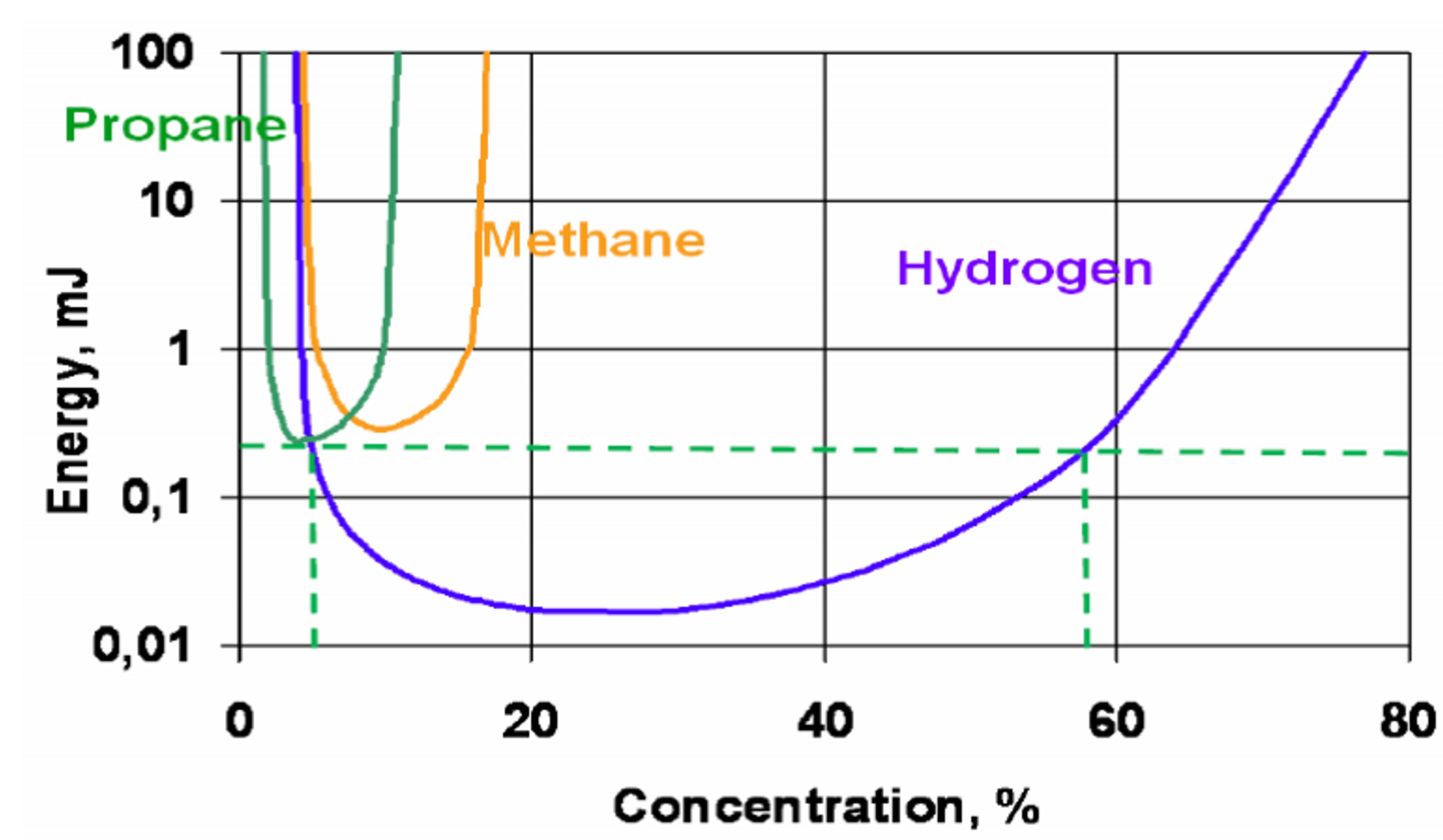
The risks (and advantages) of electrolysis systems
“Electrolyzers are tricky because, by function, hydrogen is in close proximity to high electrical current loads,” Dani says. “Typically, electrical components must be ‘electrically classified’ for safe use around hydrogen when a leak is possible. Organizations like UL will certify that those devices will not spark. However, you cannot electrically classify an electrolyzer. The stack is always a potential ignition source if a combustible gas mixture forms during operation.”
Fortunately, electrolysis systems have their advantages too. Several inherent design factors help mitigate the risk of combustion.
Many electrolysis applications put their H2 to work right away. That means limited fuel is available beyond the small amount in the output process lines. As soon as the power is cut, hydrogen and oxygen production rapidly halt. Since there is limited stored H2 and production can be stopped quickly, there’s less risk of forming a combustible mixture.
Furthermore, many electrolysis systems vent their oxygen into the air at ambient pressure. Ambient air is a much less dangerous oxidizer than pure, pressurized oxygen.
Last, in most applications, mechanical ventilation around the electrolyzer stack and balance of plant (BoP) functions will sweep away any small hydrogen leaks before they reach combustible mixture concentrations. These features can prevent a combustion event by never letting a combustible mixture form in the first place.
Systems integrations
Electrolysis equipment has inherent risks based on system integration. An electrolyzer may be safely engineered by the manufacturer, but what happens when it’s installed in various applications or powered by unique electrical devices? Will vents and failsafe measures still work correctly?
A contributing factor to the Korean electrolyzer incident (mentioned above) was likely using the device outside the manufacturer’s design limits. Because the alkaline water system was not run at proper power levels, cell membrane degradation allowed oxygen to permeate to the hydrogen side of the electrolyzer. Even this relatively simple operational mistake had significant consequences.
“This is a top concern for many clients. They want to ensure they properly install, integrate, and operate their electrolysis equipment within their larger systems,” says Dani. “Manufacturers provide some great safety features. It’s your responsibility to consider how your system will integrate with theirs. You need to understand the function of the electrolyzer and its control strategies, then follow best practices for system integration.”
WHA’s hydrogen safety experts provide several hazard analysis solutions for electrolysis systems integrations, including Hydrogen Combustion Risk Analysis (HCRA), Hazard and Operability Analysis (HAZOP), and code and compliance studies.
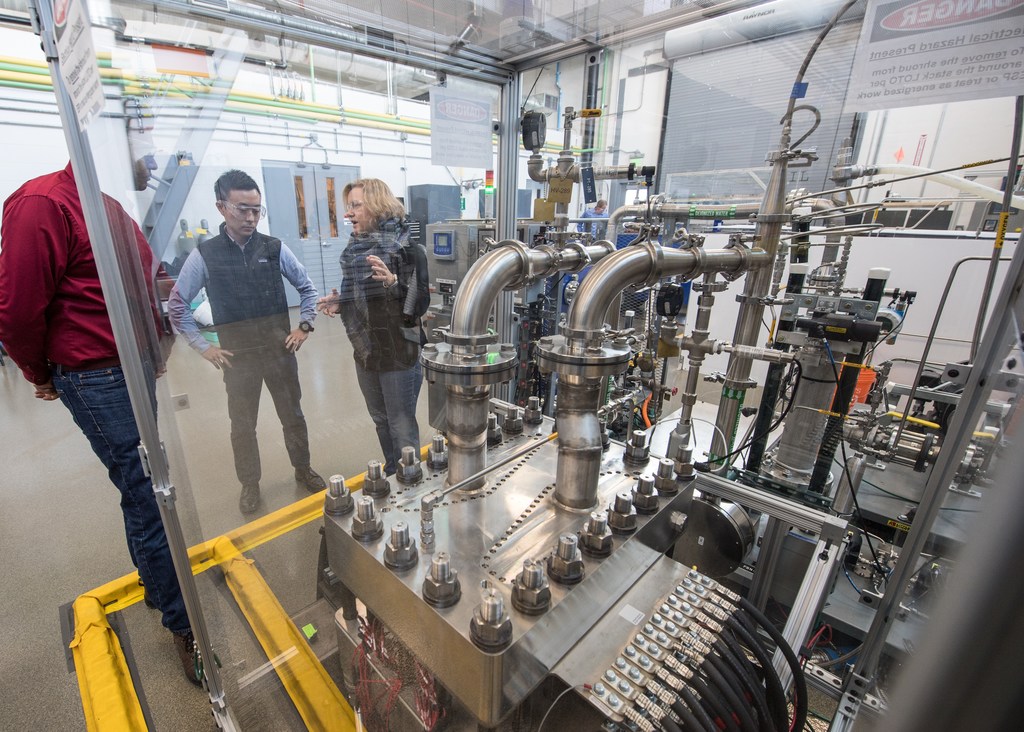
Electrolysis system safety strategies
How can electrolysis system designers and users avoid the energetic consequences of combustion? WHA’s approach to electrolysis safety begins with the fire triangle, a simple illustration featuring three factors necessary for combustion: fuel, ignition source, and oxidizer.
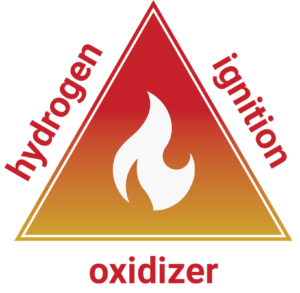
Dani explains how eliminating just one side of the triangle will prevent combustion: “Your fuel is hydrogen, and your oxidizer is oxygen — either in ambient air (21% O2) or pure oxygen. We want to anticipate ignition sources, but because the required ignition energy is so low, we can’t reasonably rule them out. Even a small static spark is enough for combustion.
“Our first defense is to keep the hydrogen away from the oxidizer — what we call ‘avoiding unintentional mixing.’”
WHA’s electrolysis course first considers potential electrolysis system failure modes that can create unintentional mixing. It then explores mitigation strategies, including:
- Leak prevention: Prevent external leaks from mixing hydrogen with ambient air and prevent internal leakage from one part of the system to the other.
- Ventilation: Install mechanical ventilation fans to sweep the electrolyzer enclosure and reduce hydrogen accumulation.
- Venting and disposal: Evaluate concentrations for all operational modes and create procedures for venting O2 and H2 during system startup, operation, and shutdown.
- Purging: Purge H2 systems with nitrogen or other inert gases before and after use (optional).
- Detection: Use personal monitors, leak sniffers, imaging cameras, and fixed H2 Incorporate detection into procedures and automated safety controls.
- Safety planning: Provide regular training to all personnel who work around hydrogen or electrolysis systems. Develop clear plans for maintenance, operation, and emergencies.
Get electrolysis system safety training on-demand
Interested in improving safety around hydrogen and electrolysis systems? You can now take our new electrolysis system safety course on-demand. Contact us to learn more about our specialized consulting and hazard analysis services for electrolyzers.
Share this entry
Related Articles
Hydrogen Tank Explosion Demonstration
Typically, hydrogen is safely stored as a compressed gas or liquid. Although hydrogen is a fuel, it…
Hydrogen Cleaning: Ensuring Safety and Reliability in Pressurized Hydrogen Systems
Hydrogen is an increasingly important and prominent energy carrier, with applications ranging from fuel cells to electrolyzers…
Battery Safety Insights with Nic Linley, Electrical Engineer
Battery technology continues to evolve rapidly in the 21st Century, powering an expanding array of devices and…
Request an expert
consultation
Contact us to request a free consultation with an experienced engineer who can help you better understand your needs and our solutions.