Particle Impact Testing in Oxygen Supports Material Selection and Component Design
In an oxygen system, high-speed gas can mobilize and propel small particles with enough kinetic energy to cause an ignition. This effect is historically defined as a particle impact ignition event.
If particle ignition occurs in an oxygen-enriched environment, it can quickly lead to burnout or catastrophic failure in components like valves and regulators.
WHA’s particle impact test program aims to study the factors contributing to particle impact ignition. This custom oxygen test subjects components or materials to flowing oxygen conditions with a particulate load to help manufacturers determine if they are vulnerable to particle impact ignition in oxygen service.
The mechanics of particle impact ignition
Many components in compressed gas systems operate with pressure differentials – high pressure on the upstream side and low pressure on the downstream side.
Regulators and control valves operate with high-pressure differentials as part of their full-time function: controlling pressure or flow. Isolation valves, vent valves, and pressure safety valves, by comparison, generally only experience transient pressure differentials during opening or venting.
High-pressure differentials in a component increase the internal gas velocity, which can reach the speed of sound. High-speed gaseous oxygen can propel small particles with enough kinetic energy to ignite them (and/or the target material) upon impact.
Particle impact has emerged as a likely ignition mechanism in many historic oxygen fires.
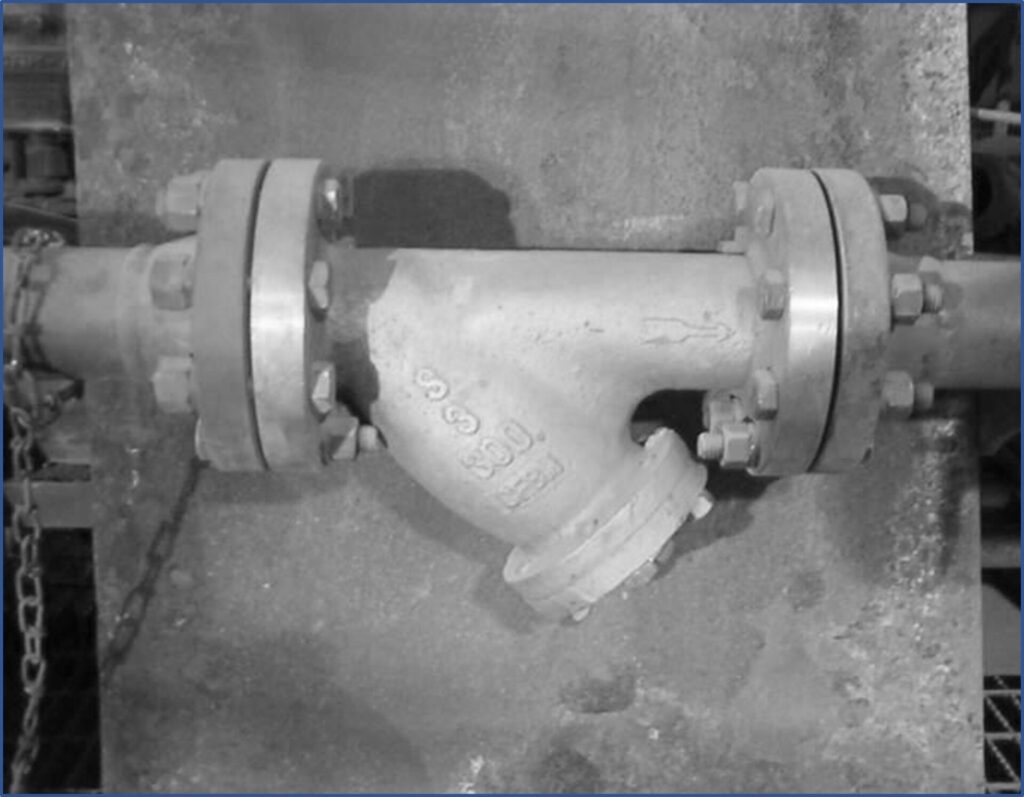
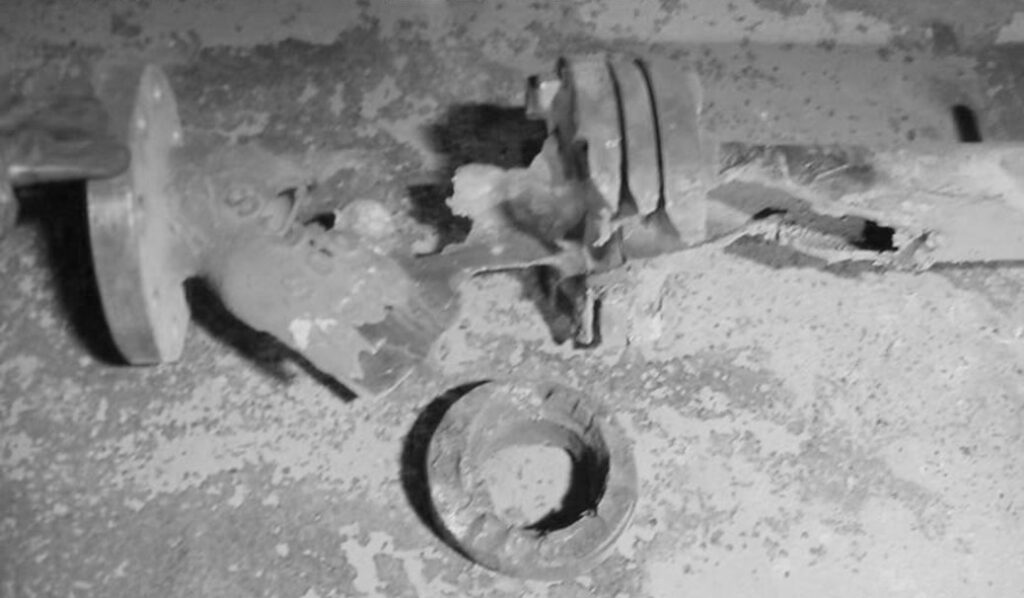
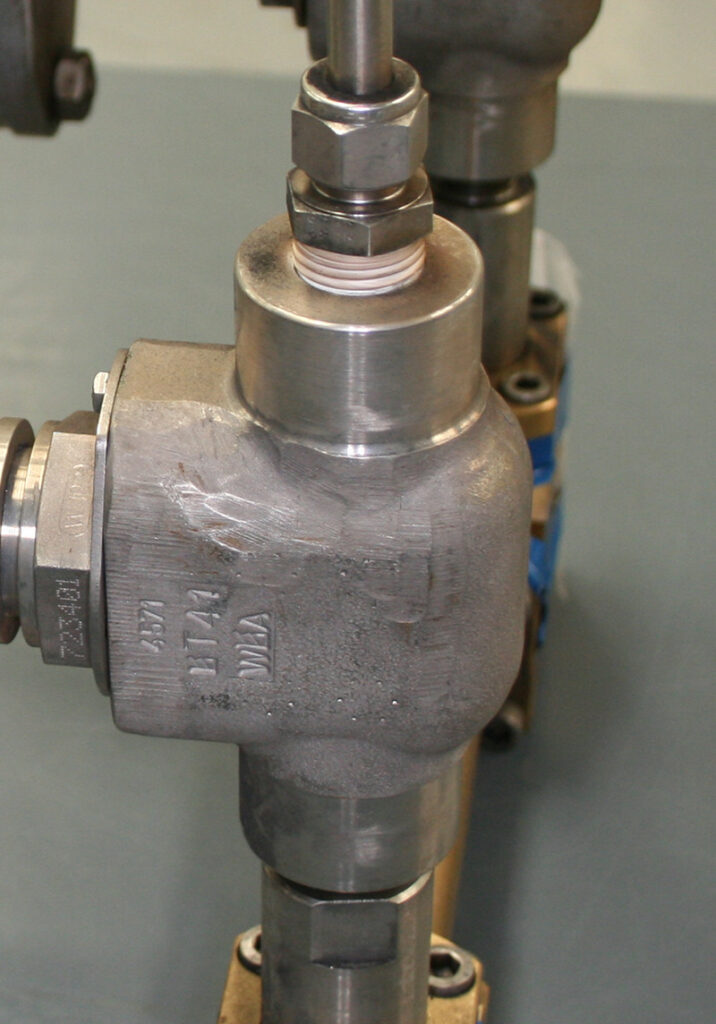
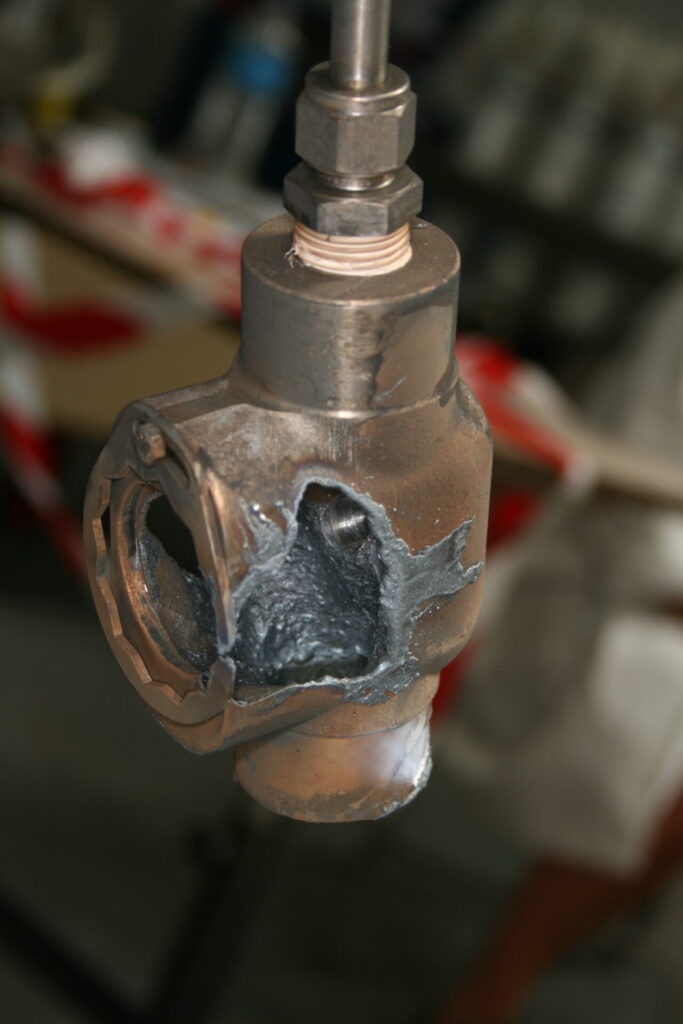
Mitigating the risk of particle impact ignition
Because materials ignite more easily and burn more rapidly in oxygen-enriched environments, contaminants can be a fuel source and ignition threat. Metal particles can originate from multiple sources, including lack of initial cleaning, system assembly, and everyday wear during operation.
The first defense against particle impact ignition is proper oxygen cleaning and maintenance. Cleaning helps minimize the contaminants that can act as high-speed “ammunition” leading to ignition. WHA’s oxygen clean approach is to:
- Start clean
- Verify clean
- Assemble clean
- Maintain clean
Each step is essential to minimize particulate that can ignite through impact. WHA offers training on cleaning for oxygen service, which is covered in our Level 2, Level 3, and Level 4 oxygen safety courses.
Another defense against particle impact ignition considers material compatibility and component design. Certain metal alloys, like aluminum, are particularly susceptible to this ignition mechanism. One industry practice for component design is to ensure that burn-resistant and ignition-resistant alloys (such as Monel 400) are specified when the probability of particle impact ignition is high. However, burn-resistant alloys (such as Monel 400 or brass) are not always practical due to factors like corrosive environments, pressure limitations, lead times, or costs. WHA recommends performing a component-level oxygen fire risk analysis (OFRA) to help identify materials and designs with high particle impact ignition probability. WHA uses the OFRA tool to assess the probability of ignition and mitigate the risk where needed. WHA also teaches this methodology in their Level 3: O2 Design and Level 4: O2 Analyze training courses. Strategies to mitigate particle impact ignition may include materials changes, design changes, or other strategies such as testing.
WHA has developed particle impact testing to better understand the particle impact risk of flammable alloys such as stainless steel in high pressure oxygen applications.
The majority of published particle impact testing has been performed by NASA at relatively severe conditions (high pressures and/or supersonic gas velocities), which may not well represent the conditions of many oxygen applications, such as industrial oxygen piping systems. WHA designed its particle impact test system to evaluate various conditions, including the ignitability of industrial piping alloys (such as stainless steel and carbon steel) at conditions and particle loads representative of larger-diameter industrial piping systems, as well as those of smaller diameter, high-pressure oxygen systems.
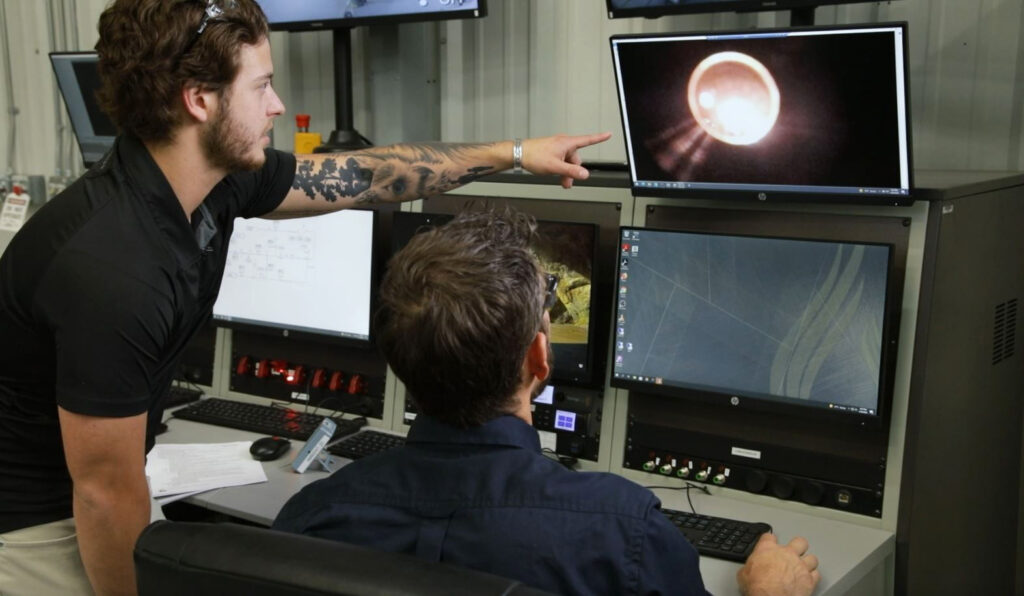
WHA’s particle impact test method
The oxygen safety engineers at WHA International perform particle impact testing in their lab, often as part of a hazard analysis or a failure incident reconstruction or for an oxygen component. Their findings can help inform an origin and cause analysis or assist in evaluating whether a component’s ignition risk could be reduced through a material or design change.
For particle impact testing, WHA uses a special test apparatus set up inside one of the reinforced concrete test cells at WHA’s Test and Training Facility. Technicians purge the system with nitrogen and then with oxygen before loading particles into the system.
Outside the test cell, the technicians establish oxygen flow conditions according to the client’s specifications, then release particulate at high velocities towards the test article. They monitor and record the test from various angles, including the use of high-speed cameras.
The test system has multiple camera ports which can record a potential particle ignition, or “flash,” internally upstream and downstream of the test article. This evidence is especially helpful for particle ignition events that do not result in external burnout. WHA technicians can also monitor temperature transients that may give evidence of ignition. After the test, they will examine the component internally to search for strike marks, slag deposits, melt-flow patterns, and other evidence of particle impacts and/or ignition.
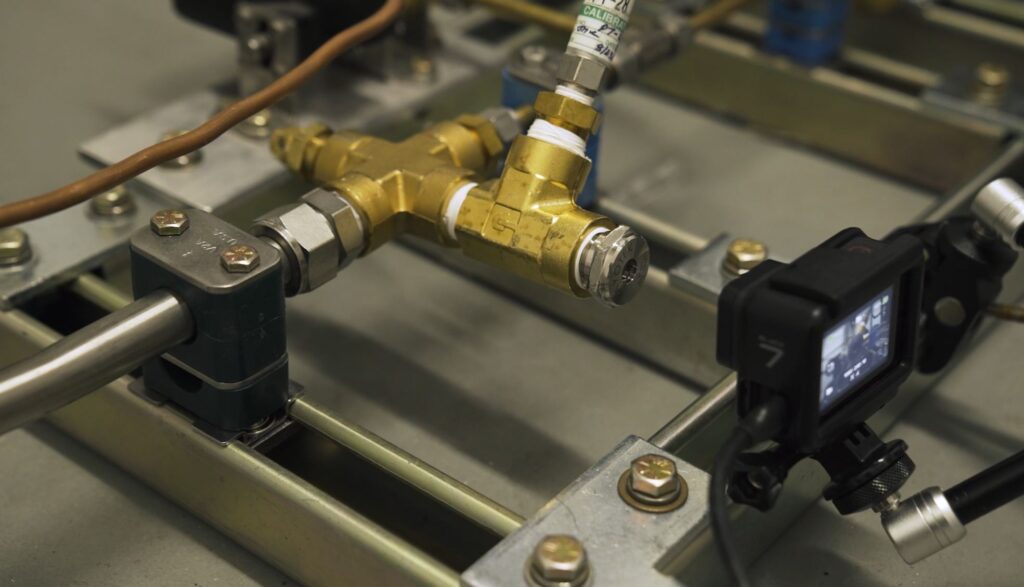
Helping industry use oxygen safely
Clients can use WHA’s particle impact test data to understand how the factors of pressure, temperature, gas velocity, particle mass/quantity, and construction materials can influence the probability of ignition in an assembled component. The tests may indicate that modifications to materials or design are needed before the component can be considered resistant to particle impact ignition.
WHA’s particle impact tests use a similar pass/fail criteria of other ignition tests in oxygen since there is currently no standard test method for this type of testing. WHA engineers can apply statistical methods to express confidence in the results based on the number of repeat tests performed. WHA is hopeful that with enough test data, they can optimize a new quantitative probability analysis model for particle ignition in oxygen control valves.
Share this entry
Related Articles
Battery Safety Insights with Nic Linley, Electrical Engineer
Battery technology continues to evolve rapidly in the 21st Century, powering an expanding array of devices and…
Oxygen Cylinder Filling System Fire Case Study
Oxygen cylinders and pressure systems quietly hold enormous amounts of energy. When things go wrong, the results…
WHA Presents O2 Safety Papers at 2024 ASTM G04 Symposium
In October 2024, Gwenael Chiffoleau, Nic Linley, and Brent Houser traveled to Prague for the 16th ASTM…
Request an expert
consultation
Contact us to request a free consultation with an experienced engineer who can help you better understand your needs and our solutions.