Case Study: Power Plant Hydrogen Explosion
Last updated on September 20th, 2023.
In 2007, a routine gaseous hydrogen (GH2) delivery resulted in a fatal hydrogen explosion at a power plant in Muskingum, Ohio. WHA International was called upon to investigate the failure and understand how hydrogen safety could be improved to prevent future incidents.
Today, this tragic incident serves as a reminder of the unique hazards of hydrogen. The investigation uncovered valuable lessons learned, including best practices related to maintenance, system design, venting, and ventilation.
The following case study is based on a presentation given by Senior Mechanical and Forensic Engineer Daniele Murphy, Ph.D., at the Center for Hydrogen Safety (CHS) 2021 Asia-Pacific Conference. Barry Newton, Ph.D., served as the primary investigator on the original case.
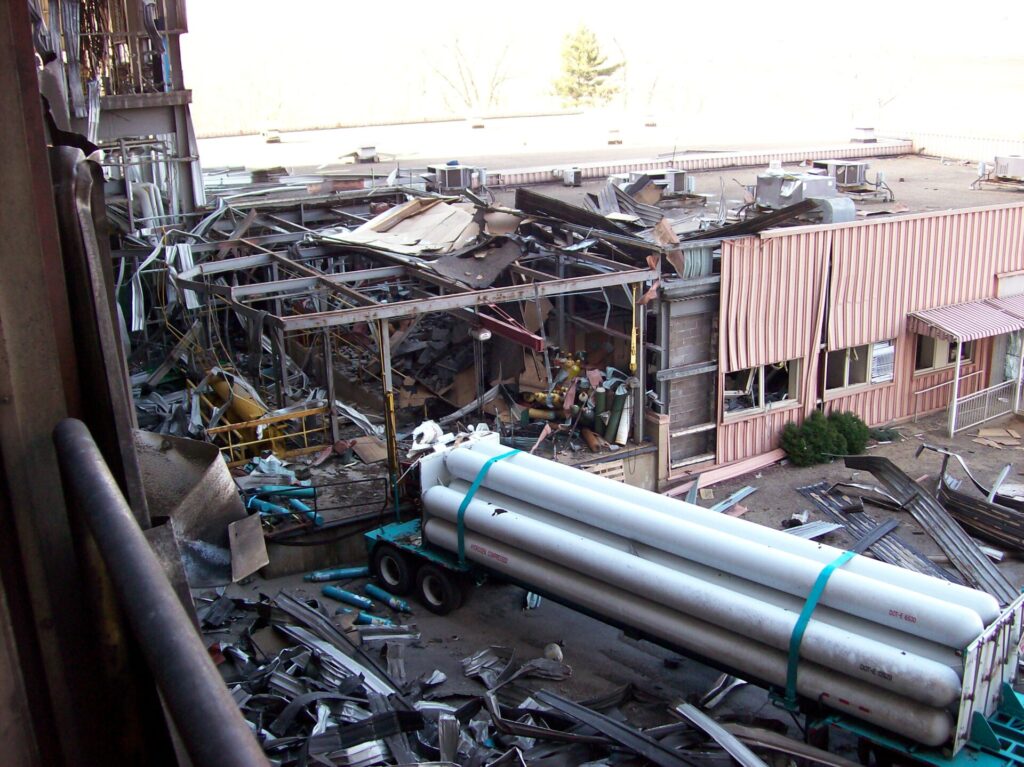
Hydrogen Explosion Incident Description
Around 9 a.m. on January 8, 2007, personnel maneuvered a large tube trailer into position at the power plant. The trailer held ten cylinders filled with hydrogen at 2500 psi (17.2 MPa) which would be transfilled to two onsite storage vessels. These tanks could hold up to 15,000 cubic feet stored at 2000 psi, equating to approximately 35 kg of hydrogen.
The delivery was a routine part of daily operations at the plant, where the hydrogen would be used to cool its generators. Unfortunately, what happened that day was anything but routine. After a rupture disk failed, hydrogen lost containment in the vent piping and rapidly leaked into the air under an overhead awning. Soon after, the combustible mixture in the awning ignited.
The explosion resulted in the death of the delivery truck driver, who was killed as he ran back to his vehicle to turn off the hydrogen. Ten nearby plant personnel were also injured in the event, and the energetic explosion tore apart multiple structures at the plant.
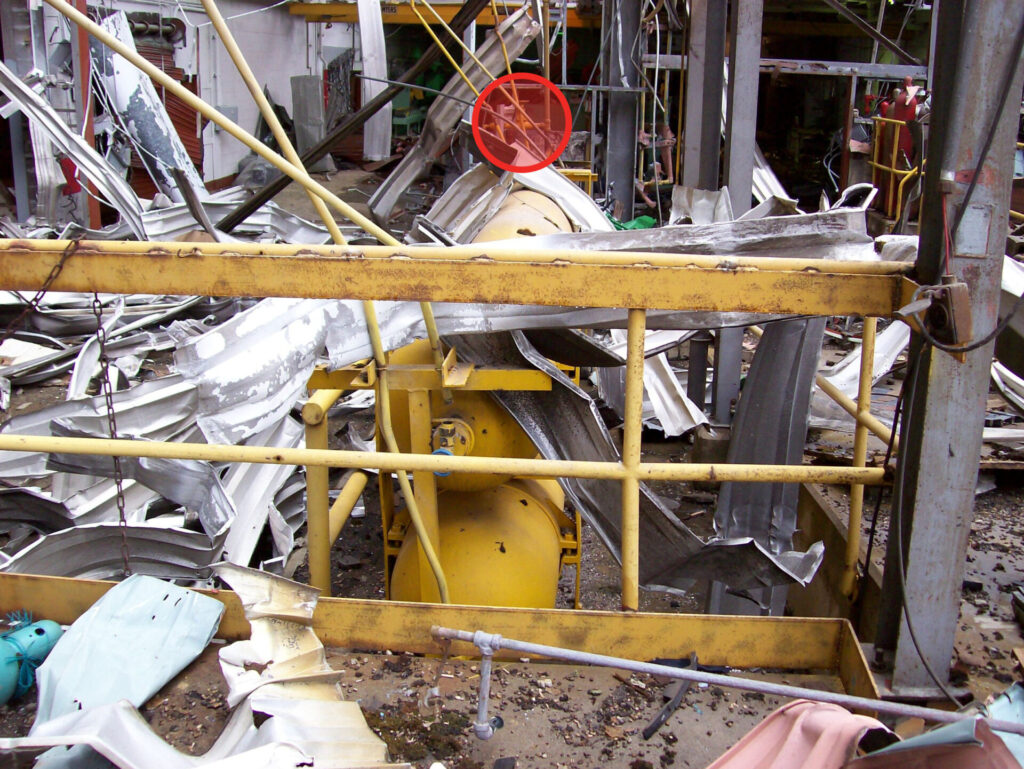
WHA Is Called to Find Answers
Despite the unique hazards of hydrogen, effective fail-safes can help prevent such a tragic accident. In this incident, fail-safes were either missing or didn’t operate as they should.
What went wrong? The hydrogen experts at WHA International were called upon to identify the root cause and uncover answers.
As with many catastrophic incidents, they identified multiple events that occurred in series to result in the explosion:
- This event began with the premature failure of a rupture disk on the onsite storage tank. This failure, in and of itself, should not have led to the explosion. Hydrogen should have escaped through a properly designed vent system and harmlessly dissipated into the environment above the awning. Instead, the pressurized gas caused the vent system to fail, allowing hydrogen to escape.
- Hydrogen gas then accumulated under an improperly designed overhead weather awning before igniting. Multiple potential ignition sources were identified in the awning.
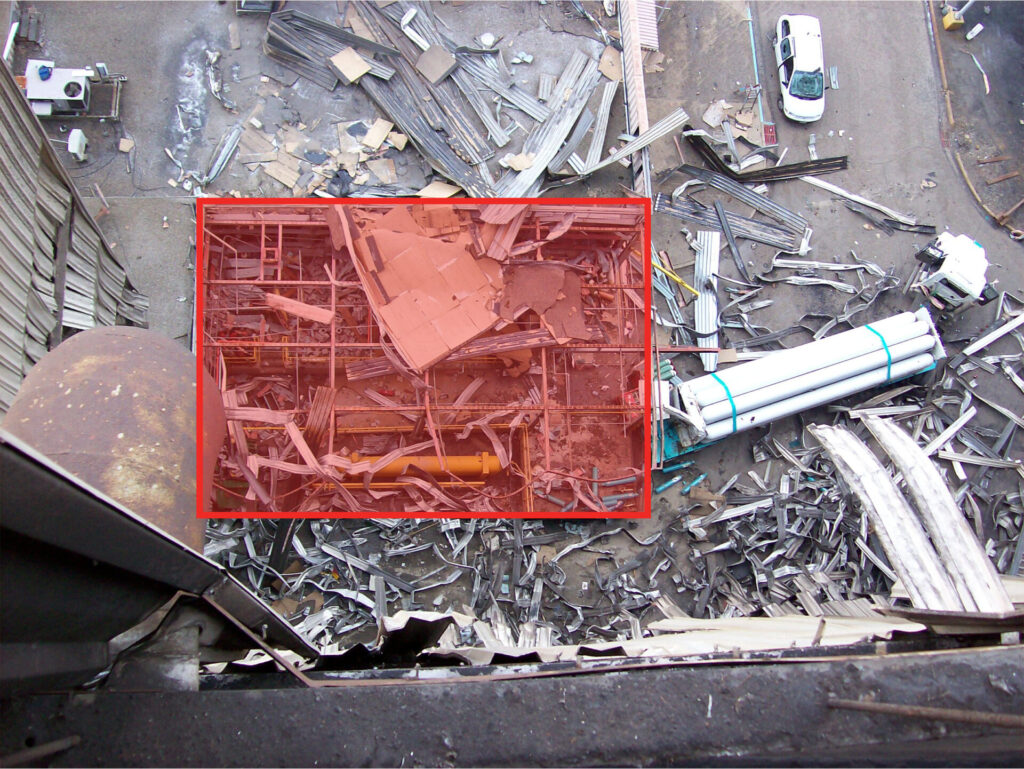
Hydrogen Failure Analysis Findings
Based on the timeline of events, blast indicators, explosion analysis, calculations for release rate, and vent piping flow vs. pressure, WHA engineers could estimate the amount of hydrogen that accumulated before ignition. They believed that gas escaped for more than 10 seconds, resulting in at least 17.7 kg of hydrogen released.
Following a detailed forensic investigation, WHA also conducted custom testing to evaluate the normal rupture pressures of exemplar disks, assess the vent integrity, and verify their calculations.
Key findings included:
1. Improperly sized rupture disk
The rupture disk rating was understood to be based on a US Department of Transportation (DOT) set pressure instead of the American Society of Mechanical Engineers (ASME) rated pressure which was required for this vessel. The rating on the rupture disk was improperly set between 3600 to 4000 psi even though the vessel was rated to only 2450 psi. However, while this set pressure was improper for an ASME-rated vessel, the rupture disk rating was not the cause of the failure. Due to other maintenance failures, the rupture disk failed prematurely at an estimated pressure of 1800 psi during the hydrogen transfer from the tube trailer.
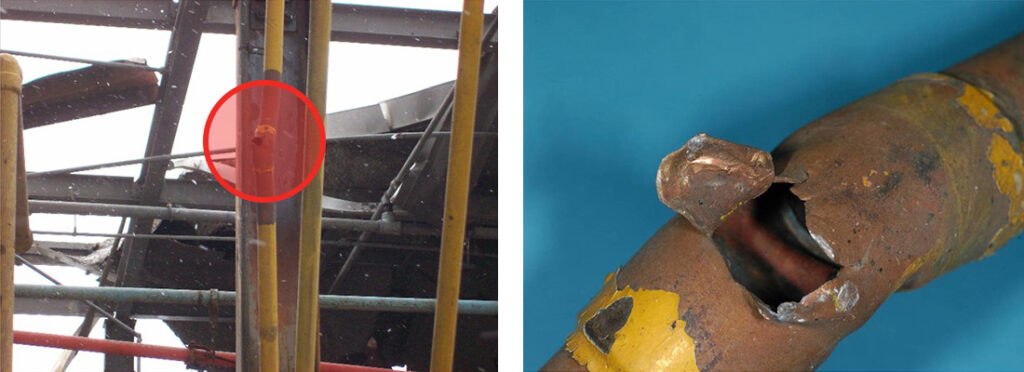
2. No management of change (MOC) for disk maintenance
Management of change was not followed during the replacement of the rupture disk just six months before the incident. An incorrect disk type was installed, and non-OEM parts with questionable compatibility were used to connect to the original relief body.
3. Indications of corrosion on the disk
Because of improper maintenance practices, uncapped vent piping exits could have allowed water to enter the system. Water accumulation may have caused corrosion that was found on the rupture disks.
4. Hydrogen piping in disrepair
The hydrogen vent piping was improperly constructed out of thin-walled copper, not rated for the pressure or thrust, and was severely corroded with multiple areas of localized thinning. The regulator cabinet was also not designed with hydrogen safety in mind since the cabinet was unventilated with relief valves venting inside. A localized fire occurred in the cabinet secondary to the initial release.
5. Improper hydrogen piping design
The copper tubing strength varied throughout the system, including some thin-walled copper intended for water service and rated to less than 500 psi. The prevailing standard in the US for vent piping specifies the use of Austenitic 300 series stainless steels and prohibits using copper tubing. During the release, the thin copper tubing was overpressurized and partially straightened under the thrust forces. One elbow in the vent piping blew out, likely due to a projectile impact – possibly from the rupture disk petal itself. The vent system was poorly designed and incapable of withstanding the thrust and pressure of an H2 release.
6. Weather awning not designed for hydrogen ventilation
The weather awning above the storage tank was not designed for ventilation as required for hydrogen safety and code compliance. When hydrogen was released, the rising gas was forced up the angled roof line and collected in the space contained by three walls. NFPA 2 6.7.1.4 states that “Walls shall not obstruct more than one side of the structure” and “obstructed area by walls shall not exceed 25% of the structure’s perimeter area.”
7. Blast origin was under the awning
Blast indicators showed that the hydrogen explosion began under the awning, although the exact ignition source is unknown. This is often the case with hydrogen failures because its minimum required ignition energy is so low. Electrostatic discharge, electrical lights in the awning, and electrical panels were all potential ignition sources.
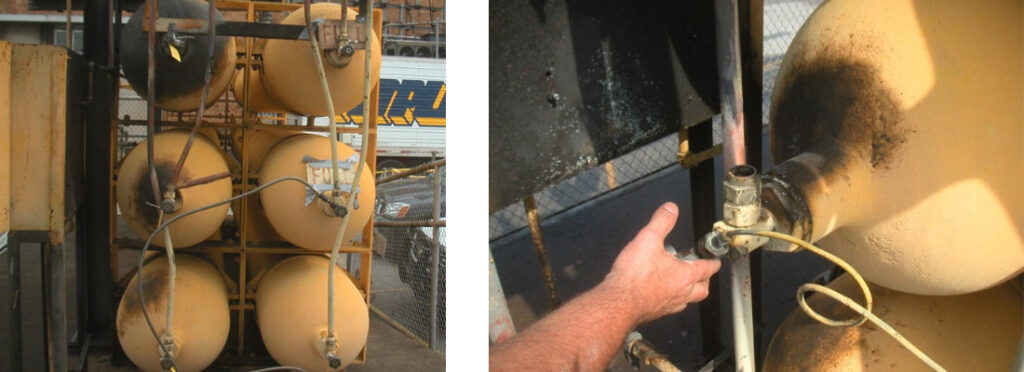
8. Failure to learn from past incidents
A similar, less severe incident occurred approximately 2-years prior at a facility owned by the same company. A rupture disk failed prematurely, resulting in the failure of a copper vent pipe and the accumulation and ignition of hydrogen. An investigation revealed lessons learned which would have prevented the much larger fatal incident at the sister plant had they been properly implemented.
Preventing Future Hydrogen Explosion Incidents
In every WHA failure analysis, our engineers aren’t just looking back to what went wrong. They are also looking forward to identify lessons learned and best practices to prevent similar incidents.
Hydrogen-specific risk analysis, such as WHA’s Hydrogen Combustion Risk Analysis (HCRA), can also help identify and mitigate hydrogen system and component design problems before an incident occurs.
This tragic accident highlights several key takeaways for the hydrogen industry:
- Use good housekeeping and maintenance practices – proper maintenance and MOC could have improved the integrity of the rupture disk and vent piping.
- Design vent stacks to withstand pressure and thrust forces associated with a release – appropriate materials and design could have prevented the failure in the vent piping.
- Design vents to prevent water ingress – best design practices could have prevented corrosion and weakening of the vent piping.
- Design weather awnings to prevent accumulation – Hydrogen is lighter than air and escapes upwards. Proper awning design could have allowed the hydrogen to escape harmlessly into the atmosphere.
- Ensure personnel are trained and aware of hydrogen-specific hazards – From initial system design to installation, ongoing use, and maintenance, hydrogen safety training helps defend against hydrogen fires and explosions, protecting lives, property, and business operations.
Take the next step in ensuring hydrogen safety in your workplace. Our hydrogen safety training and understanding our hydrogen risk management philosophy are ideal places to start.
Share this entry
Related Articles
Hydrogen Embrittlement: Hazards and Mitigation Strategies
Hydrogen embrittlement (HE) is a critical concern in industries utilizing hydrogen, posing significant safety concerns if not…
Advancing Large-Scale Electrolyzer Safety
Electrolyzer safety is becoming increasingly important as the industry undergoes significant change to meet the growing demand…
Will hydrogen power the future of Aerospace?
As the world moves towards clean energy technologies, finding alternatives to traditional fuels is particularly challenging in…
Request an expert
consultation
Contact us to request a free consultation with an experienced engineer who can help you better understand your needs and our solutions.