Hydrogen Cleaning: Ensuring Safety and Reliability in Pressurized Hydrogen Systems
Highlights
- Contaminants in hydrogen systems can lead to leaks and combustion risks.
- Proper cleaning and inspection ensure parts and systems are safe for hydrogen use.
- While no definitive hydrogen cleaning standards exist, guidance does exist for various applications, and WHA helps companies understand and apply these guidelines and best practices.
Hydrogen is an increasingly important and prominent energy carrier, with applications ranging from fuel cells to electrolyzers to industrial processes. Safe handling practices, including cleaning hydrogen systems, are critical for the continued safety of these applications. However, hydrogen cleaning requirements are less well-known and often neglected.
WHA International has deep expertise in hydrogen safety and an extensive background in precision cleaning for oxygen service. As more companies grapple with hydrogen cleaning challenges, WHA is helping the industry better understand these issues so they can grow safely.
In this article, WHA Senior Chemist Wallace Foster highlights key considerations and best practices for cleaning parts and equipment used in hydrogen service.
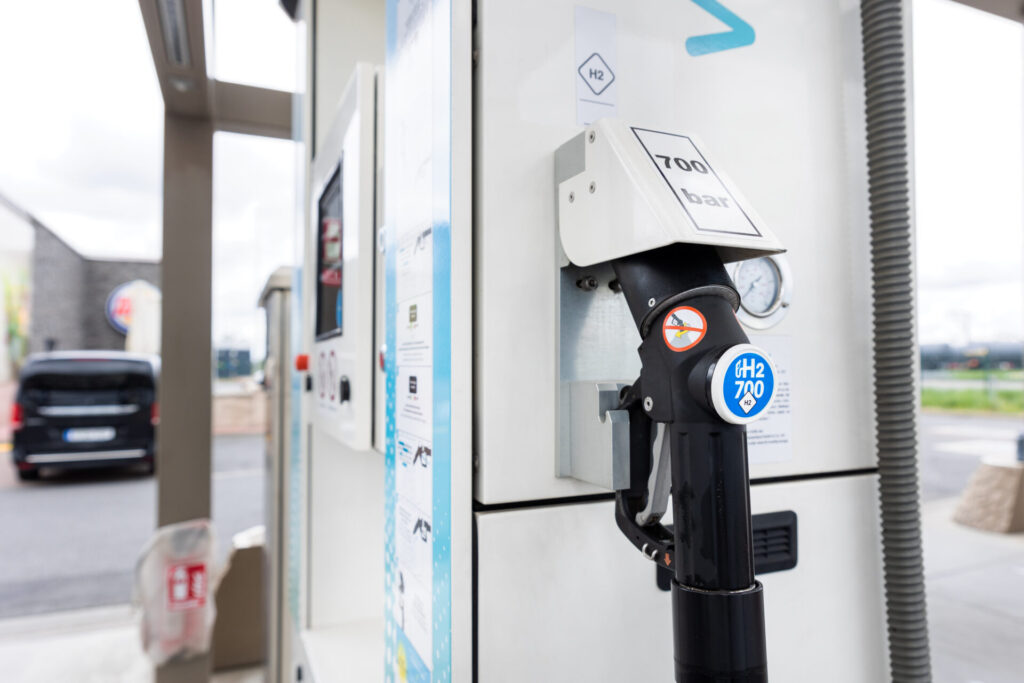
The Importance of Hydrogen Cleaning
Cleaning for both gaseous and liquid hydrogen (LH2) systems is vital for their quality, reliability, and safety. Cleaning removes non-volatile residues (NVR) and other contaminants that can compromise the hydrogen quality for critical processes but also helps minimize the potential for leaks, preventing the dangerous combustible mixture of hydrogen with air or oxygen.
“Although many of the practices behind hydrogen cleaning are the same as oxygen, we do it for fundamentally different reasons,” explains Foster, who leads WHA’s cleaning services. “In oxygen systems, contaminants are unwanted fuels that can easily ignite and cause fires. 100% hydrogen, on the other hand, is a fuel. But without an oxidizer, hydrogen is not flammable and will not ignite on its own. Therefore, in addition to hydrogen fuel quality, we’re concerned about contaminants disrupting seals and producing leaks, allowing hydrogen to mix with oxygen or air, which requires very little energy to ignite.”
Particulate Hazards in Hydrogen Systems
Hydrogen is the smallest molecule known to man and, as such, is difficult to contain in a pressure system, even with properly designed seals. Thus, the first objective in cleaning hydrogen components or systems is to remove particles to minimize the likelihood of disrupting soft goods or other seals, leading to a leak. Particulate contamination poses several risks:
- Particles can compromise pressure system seals— mechanically damaging both metal-metal seals and nonmetal seals—leading to leaks.
- Particles flowing in gaseous hydrogen can develop a different charge potential than the rest of the grounded and bonded piping system. This can create electrostatic discharge (ESD) ignition hazards, especially in vent systems where hydrogen mixes readily with air.
- Particles can severely compromise the function of sensitive equipment like fuel cells fed by the hydrogen system.
- Particles can clog filters, creating excessive pressure drops and, in extreme situations, potential filter collapse.
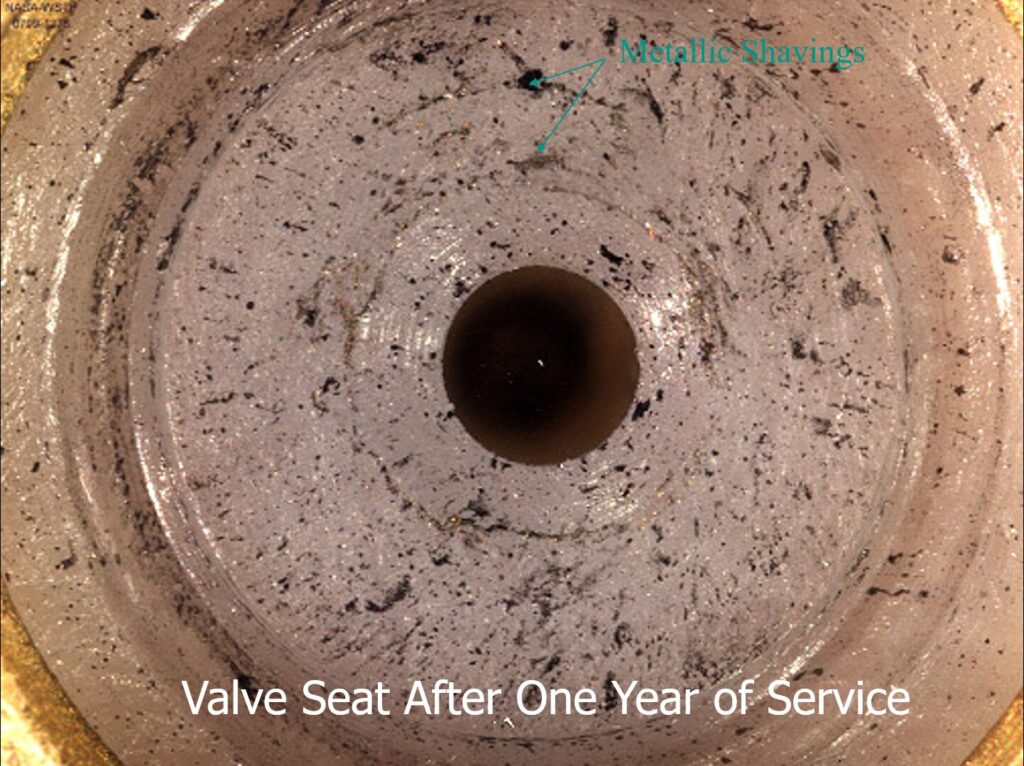
NVR Hazards in Hydrogen Systems
Non-volatile residues typically refer to oil films or greases with high surface tension that adhere to internal surfaces, causing harmful effects:
- In liquid hydrogen systems, NVR can freeze, becoming solid contaminants that pose hazards similar to particulates. Further, it is noteworthy that most lubricants become solid in LH2 and thus are not used on exposed sealing surfaces.
- NVR can affect equipment functionality or compromise hydrogen purity. In gaseous H2, NVR is not easily removed through filtration.
- NVR can act as an additional fuel in systems that mix hydrogen with oxygen, where cleanliness is crucial to preventing fires.
- The uninsulated outside surfaces of liquid hydrogen systems can reach temperatures below the liquefaction temperature of oxygen (and nitrogen) in air, leading to localized oxygen enrichment where contaminated surfaces can create an increased fire hazard.
Further reading: Why Clean for Oxygen Service?
Standards Addressing Hydrogen Cleaning
While some international standards reference the importance of cleaning hydrogen systems, no comprehensive guide or official standard exists.
WHA has listed some hydrogen standards below which reference the cleaning of hydrogen systems. The list also includes some oxygen cleaning standards and guides that are often referenced in hydrogen standards by default. The best practices WHA describes below are based on these documents. Referenced specifications include the most recent version of the following:
- ANSI/AIAA G-095A: Guide to Safety of Hydrogen and Hydrogen Systems
- CGA G-5.4: Standard for Hydrogen Piping Systems at Consumer Locations
- AIGA 033: Hydrogen Pipeline Systems
- AIGA 094: The Safe Design, Manufacture, Installation, Operation and Maintenance of Valves Used in Liquid Oxygen and Cold Gaseous Oxygen Systems
- AIGA 087: Standard for Hydrogen Piping Systems at User Locations
- ASTM G93: Standard Guide for Cleanliness Levels and Cleaning Methods for Materials and Equipment Used in Oxygen-Enriched Environments
- CGA G-4.1/EIGA Doc 33 (harmonized): Cleaning of Equipment for Oxygen Service
- CGA PS-31 CGA Position Statement on Cleanliness for Proton Exchange Membranes Hydrogen Piping / Components
- and others
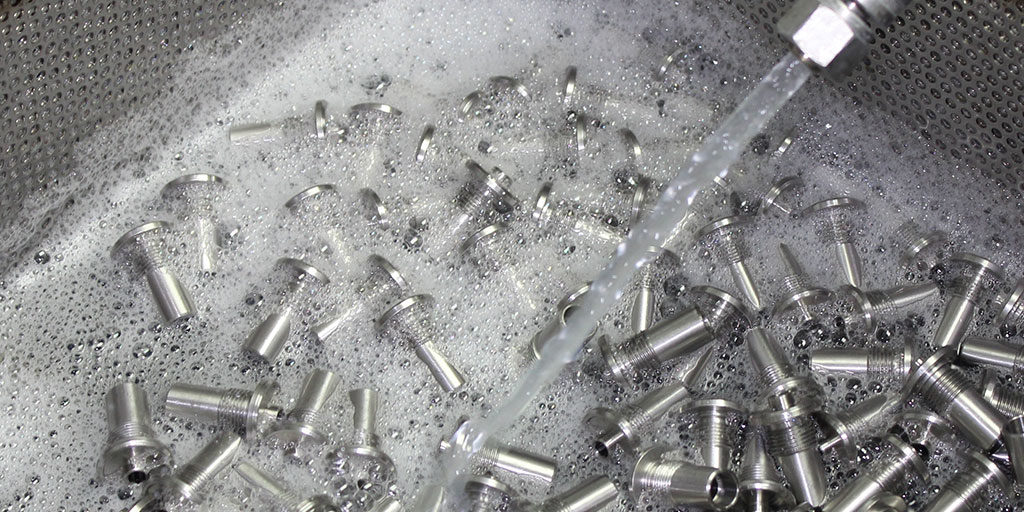
Hydrogen Cleaning Best Practices
The following summarizes best practices for cleaning gaseous hydrogen (GH2) and liquid hydrogen (LH2) systems based on current industry standards and publications. For the cleaning of oxygen systems, WHA applies a four-step approach: Start Clean, Verify Clean, Assemble Clean, and Maintain Clean. These same steps can also be applied to hydrogen system cleaning with some modifications:
1. Start Clean – Internal Surfaces Require Cleaning
NVR and particulate contaminants must be removed from hydrogen piping and equipment. Cleaning is usually performed by the original equipment manufacturer or supplier but can also be performed by the end user.
- The design of a cleaning process depends on multiple factors, including the starting and target level of cleanliness. Achieving target cleanliness is feasible with the right equipment, cleaning agents, processes, and quality control.
“There are a wide variety of cleaning methods,” says Wallace. “CGA G-4.1 and ASTM G93 outline many of them, including detergent cleaning, chemical cleaning (acid or base cleaning), and solvent cleaning. Those standards also have some guidelines for selecting the best method for your application.” - In some cases, external surfaces of uninsulated liquid hydrogen systems may also need to be cleaned to minimize NVR accumulations in an oxygen-enriched atmosphere (see above).
Cleaning Level Requirements for Hydrogen Service
It is noteworthy that oxygen cleaning standards often require quantitative verification of precision cleaning for both NVR and particulate. In contrast, hydrogen systems typically only require qualitative verification through visual inspection methods.
“Currently, there are no quantitative specifications in international hydrogen standards, which seems justified based on the nature of the hazard,” explains Wallace. “However, at a minimum, qualitative “visually clean” (VC) levels of cleanliness as verified through visual inspection techniques are considered best practice.”
Different applications may require varying cleaning levels based on their criticality. A visually clean level reflects the general minimum cleaning level recommended by industry standards.
Further Reading: Oxygen Cleaning Inspection Methods
2. Verify Clean – Visually Inspect Before Assembly
Hydrogen systems require visual inspection for contamination before assembly (See below). Surfaces must be free of particulates (e.g., corrosion, scale, weld spatter, dirt, and filings) and NVR (e.g., grease, oil, and paint).
For liquid hydrogen (LH2) systems, inspect the external surfaces of uninsulated equipment for organic contaminants. These surfaces can become cold enough to liquefy air and become oxygen-enriched.
Verification through qualitative visual inspection methods includes white light, black light, and wipe testing. However, not all methods must be used for every hydrogen application.
- White Light Inspection: Examine items under bright white light for visible grease, oil films, and particulates like filings or rust. White light can effectively cast shadows on surface debris to aid in detection. If contamination is found, reclean the item through an approved spot-cleaning method (if contamination is limited) or fully reclean the part.
- Wipe Testing: A wipe with a lint-free cloth or swab can help detect contaminants. This is especially important for internal surfaces that are inaccessible for visual inspection. Wiping should be unidirectional only to avoid “smearing” any surface contaminants and without excessive pressure to avoid removing surface oxides. After wiping, visually inspect the wipe with a white or black light and apply the inspection criteria above. Ensure there are no visible contaminants or discoloration of the wiping media.
- UV Light Inspection: Although not required in most hydrogen systems, UV (black) light inspection can be added to more effectively detect organic contaminants on critical surfaces or for critical applications. UV light creates a fluorescence of many organic compounds to aid in detecting NVR. UV lights are best specified with a wavelength of 2500 angstrom to 4000 angstrom units and a minimum light intensity of 800 μW/cm2 at the inspected surface.
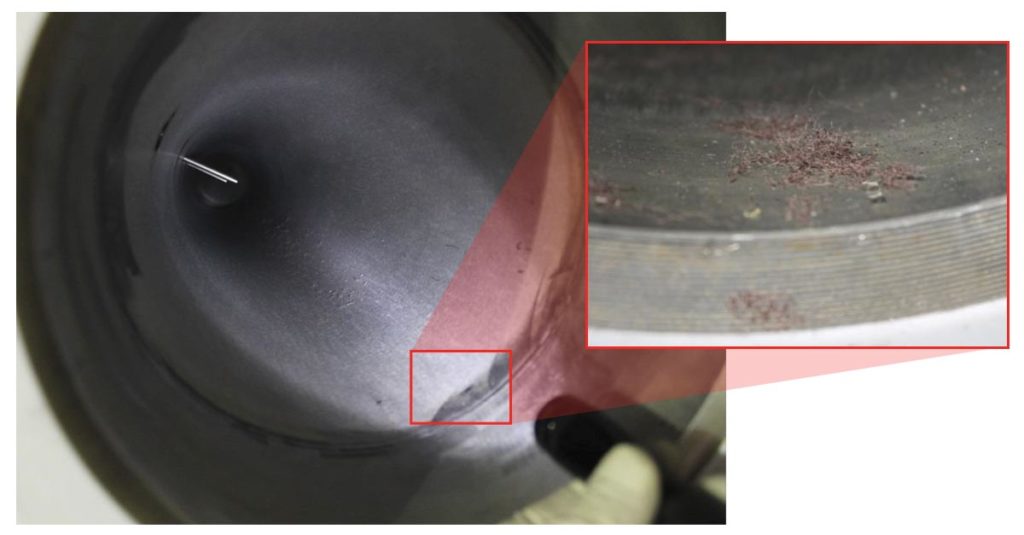
3. Assemble Clean – Use Best Assembly Practices to Avoid Generating Particulate and NVR
Best practices for assembly include using a clean area where environmental contaminants can be controlled, avoiding assembly outside in bad weather, and even using gloved hands (i.e, powder free nitrile or latex medical examination gloves) to prevent hand oils from transferring to clean surfaces.
4. Maintain Clean – Preserve Cleanliness Over the Life of the System
Use proper packaging and preservation techniques like bagging, capping, and pressurizing to maintain cleanliness from initial cleaning to installation. Labeling/tagging cleaned parts in their packaging is also important to identify and provide traceability for cleaned materials.
In addition, cleanliness can be maintained by strategic implementation of filtration in hydrogen systems and components so that operationally-generated or environmentally-generated contaminants are captured and can be effectively removed (via maintenance) over the life of the system.
Ensuring Hydrogen System Cleanliness
Achieving and maintaining the appropriate level of cleanliness is crucial for the safe, reliable operation of hydrogen systems. By adhering to industry best practices, hydrogen equipment suppliers and end-users can navigate the cleaning requirements and prepare their systems for hydrogen service.
“As the hydrogen industry continues to grow, we want to help clients navigate the standards, understand the risks, and implement best practices for hydrogen cleaning.” Wallace Foster, Senior Chemist, Cleaning Services Lead
Contact WHA International to learn more about our hydrogen safety services, which include cleanliness evaluation, process review, and consulting.
Share this entry
Related Articles
Hydrogen Cleaning: Ensuring Safety and Reliability in Pressurized Hydrogen Systems
Hydrogen is an increasingly important and prominent energy carrier, with applications ranging from fuel cells to electrolyzers…
Battery Safety Insights with Nic Linley, Electrical Engineer
Battery technology continues to evolve rapidly in the 21st Century, powering an expanding array of devices and…
Hydrogen Embrittlement: Hazards and Mitigation Strategies
Hydrogen embrittlement (HE) is a critical concern in industries utilizing hydrogen, posing significant safety concerns if not…
Request an expert
consultation
Contact us to request a free consultation with an experienced engineer who can help you better understand your needs and our solutions.