Case Study: Fire Station Medical Oxygen Cylinder Fire
Highlights
- A medical oxygen cylinder experienced a catastrophic failure and burnout during a routine fire station equipment check
- Improper use of a nylon crush gasket led to the oxygen leak and subsequent ignition
- Proper training and use of equipment can help prevent oxygen fires
Incident description
On February 5, 2005, a firefighter at Virginia Beach Fire Station #16 began his daily equipment checks.
During his inspection of the Emergency Medical Services (EMS) equipment bag, he verified the contents, which included an Emergency Cardiac Monitor (ECM), a suction unit, a blood pressure cuff, a stethoscope, a bag valve mask, and a glucometer. These items were positioned on top of a medical oxygen cylinder.
He removed the cylinder and opened the valve using a metal Crescent® wrench. After confirming the tank’s pressure (1500-2000 psig), he closed the valve with the same wrench and released the pressure using the regulator’s flow control knob.
He replaced the contents of the EMS bag and put it back into the compartment on Ladder Truck #16. A few moments later, he firefighter heard a release of pressure from the EMS compartment and turned back to see flames engulfing the bag.
The firefighter threw the burning bag to the floor, where two colleagues tried to control the blaze with fire extinguishers. Despite their efforts, the fire continued to intensify until a loud explosion occurred.
Luckily, no one was harmed in the incident.
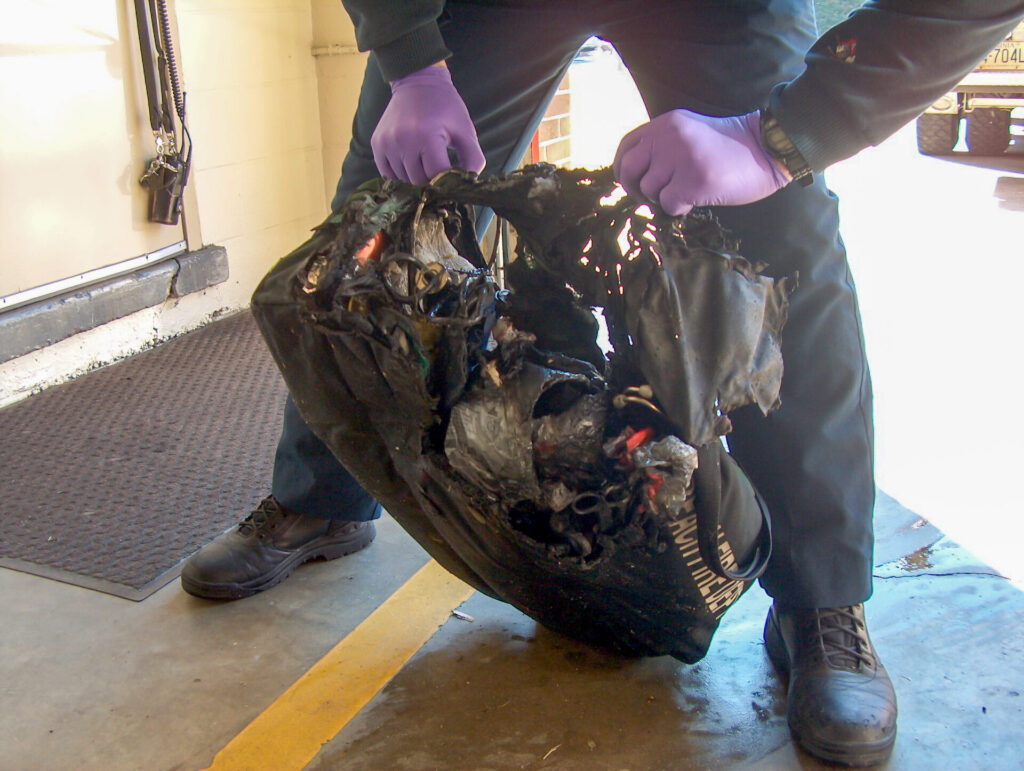
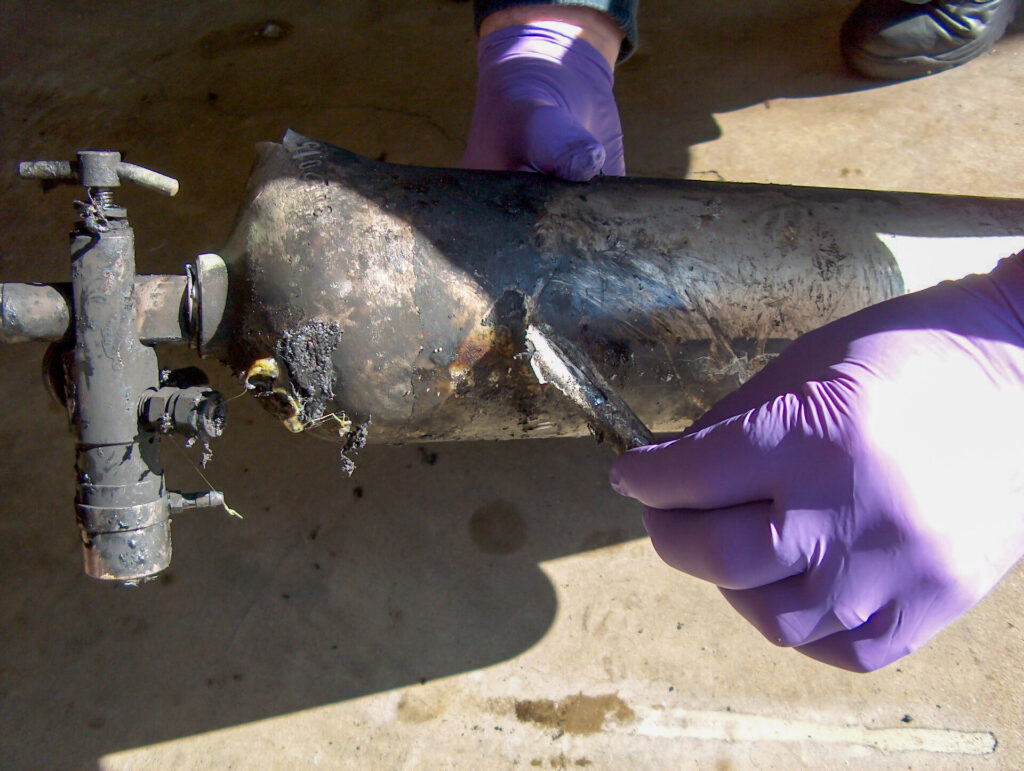
What went wrong?
Though oxygen itself is not a fuel, it makes other materials more flammable and easier to ignite than in air. This incident was caused by oxygen escaping from the medical oxygen cylinder, which made the contents of the EMS bag highly flammable. Once ignited, the situation resulted in a dangerous fire.
After the incident, the United States National Institute for Occupational Safety and Health (NIOSH) and the Food and Drug Administration (FDA) Center for Devices and Radiological Health (CDRH) reached out to WHA International, Inc. to investigate the cause and origin of the fire.
Oxygen fire origins
WHA’s failure analysis revealed that the leak began at a nylon CGA870 crush gasket, which was used to seal the regulator to the cylinder valve. These disposable parts are designed to be used only once, as they permanently deform under torque to create a good seal. After being used, they can’t seal properly again.
Unfortunately, many end-users are unaware of this limitation and often reuse crush gaskets, finding that they have to use more and more torque each time. Some practitioners even stack multiple crush gaskets in an attempt to improve the seal. WHA investigated another incident where a nurse stacked three crush gaskets together, resulting in a violent fire during use with a patient.
Further reading: learn more about oxygen cylinder safety.
Conversations with the Fire Department indicated that crush gaskets were indeed commonly used multiple times before replacement. The fact that the T-handle on the regulator yoke was bent also indicated the potential reuse of crush gaskets and the need to apply high torque to seal the interface.
Moreover, using a wrench to open and close the cylinder valve likely contributed to an overload of the valve seat and subsequent leakage. As previously seen in other incidents, an overload of plug-style cylinder valve seats is likely when applying increased mechanical advantage with a similar wrench.
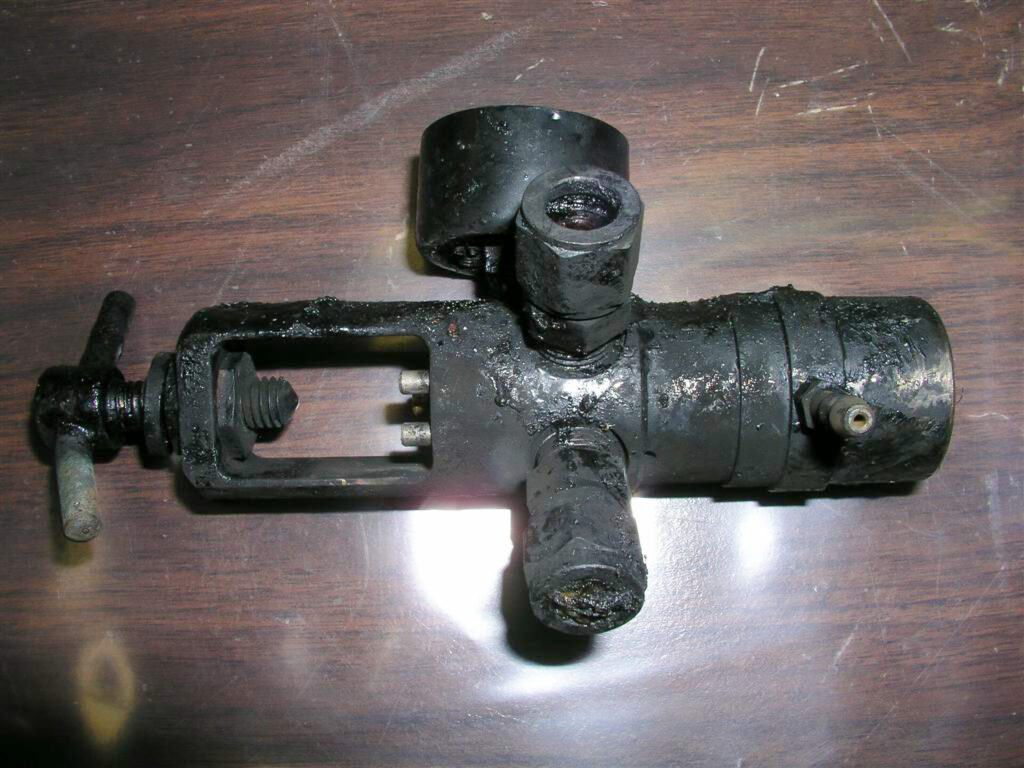
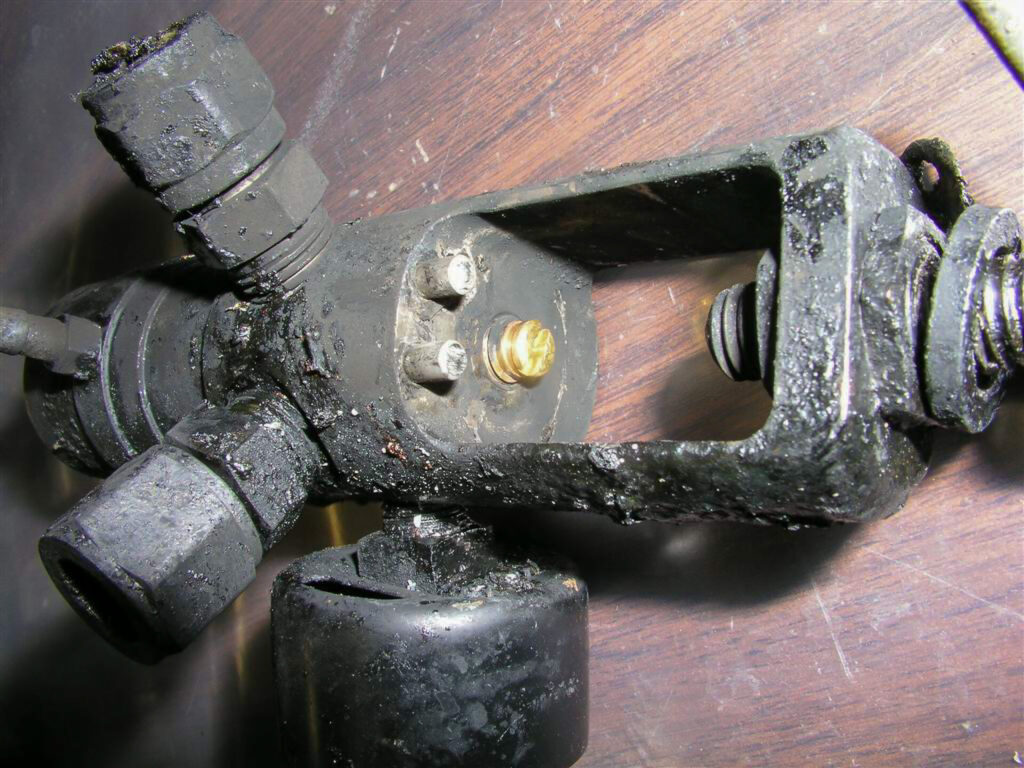
Ignition and Propagation
WHA’s investigation revealed that the crush gasket was not only the source of leaking oxygen but a likely ignition source as well.
This is in line with ASTM G88’s warning against “imping[ing] gas streams onto seats, seals, or other plastics or elastomers.” Though the phenomenon is not well understood, it is believed that this impingement can lead to “flow-induced heating,” which has been identified in several oxygen equipment fires where the only dynamic occurring during ignition was a gas leak across a polymer. The weeping or seeping gas flow generates heat within the flow path across the nonmetal surface or leak channel (see 5.2.12).
Once the CGA870 seal ignited, it rapidly kindled the surrounding contents of the EMS bag within an increasingly oxygen-enriched atmosphere. The resulting fire then caused a pressure rupture of the cylinder due to intense local heating and metal softening. The softened aluminum was sufficient to cause a breach of the medical oxygen cylinder despite its valve being equipped with a proper pressure safety device.
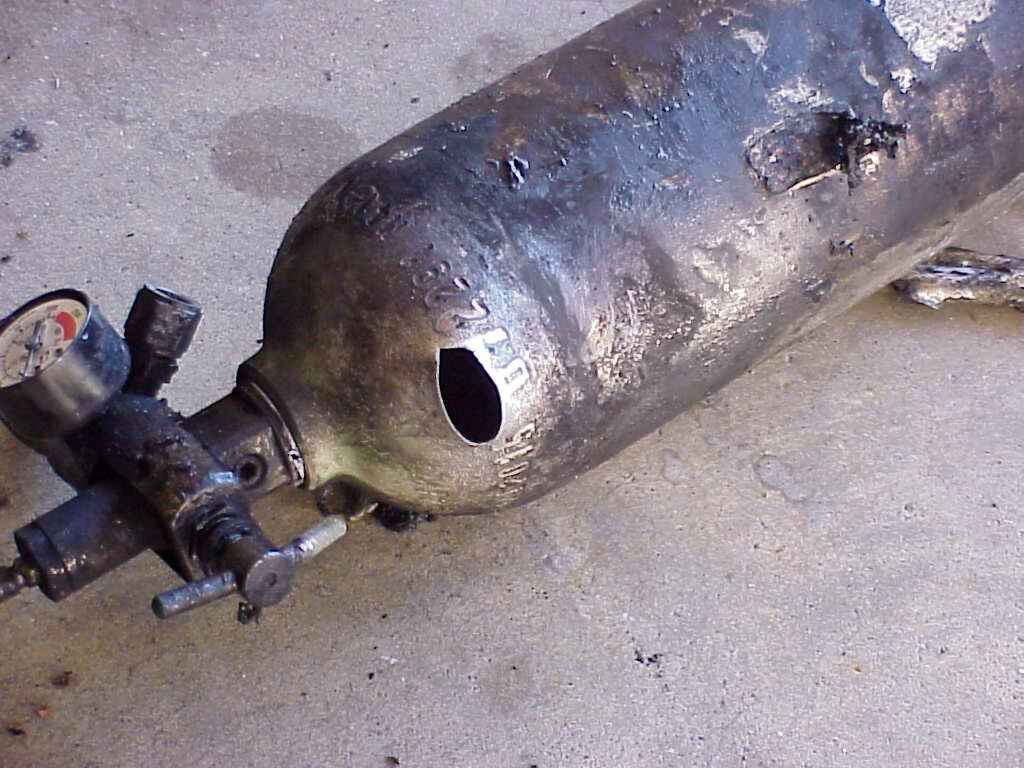
Case study takeaways for industry and end users
Although each oxygen fire is different, the investigation into this incident underlines several hazards that are typical in numerous oxygen applications.
1. Use tried and tested equipment
Employ dependable oxygen equipment from reputable suppliers who have tested their hardware and understand oxygen safety. Use hardware that has a track record of being trouble-free in oxygen service under comparable operating conditions (ASTM G88 7.11).
2. Use oxygen equipment only as intended
Carefully adhere to operational guidelines recommended by equipment manufacturers. Do not make assumptions. Crush gaskets are effective when used correctly, but they should only be considered single-use items. For repeated use, use sealing washers designed for this purpose.
Furthermore, keep in mind that seals of any kind can be contaminated by handling when replaced. Always follow best practices to maintain oxygen cleanliness.

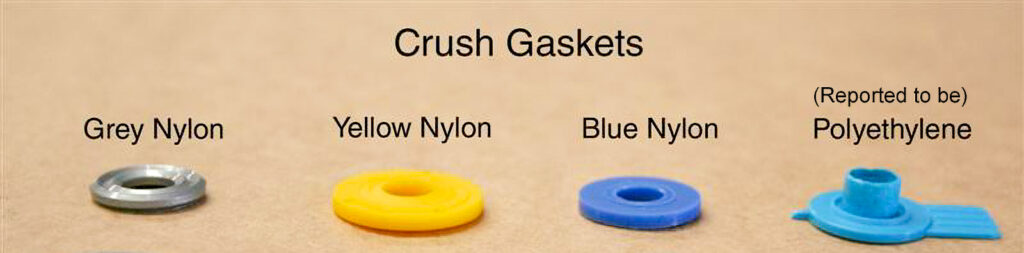
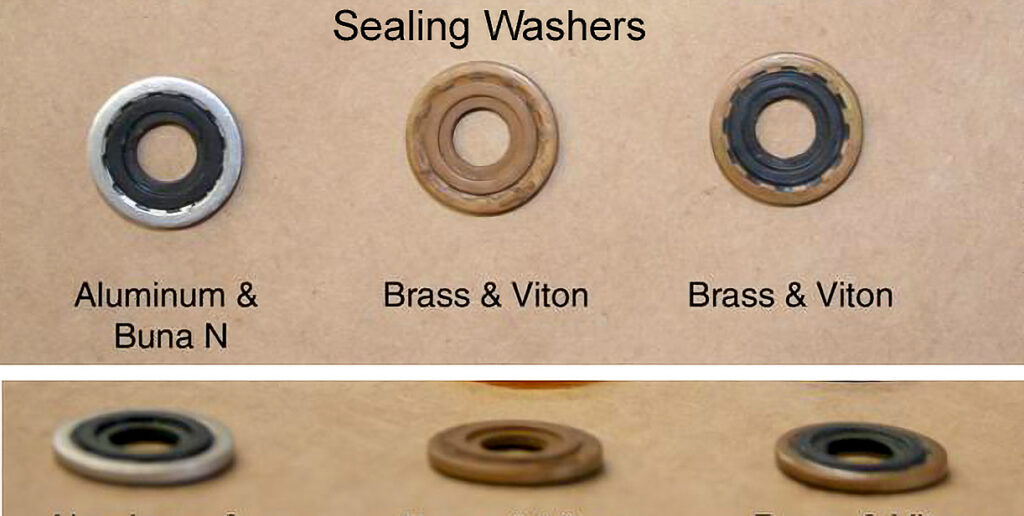
3. Provide appropriate training to all end-users and practitioners
Many oxygen fires can be attributed to user error and common misconceptions about oxygen equipment. All users should be well-versed in hazards and best practices, including proper use of equipment. Technical training for oxygen is required by governing entities like OSHA and NIOSH.
Get mandatory training from WHA. All oxygen safety courses include oxygen cylinder safety.
Defend against oxygen fires with WHA
Although rare, oxygen fires can happen without warning. The violent nature of oxygen-promoted fires can cause severe injuries or fatalities in seconds.
Around the world, medical oxygen component manufacturers, gas suppliers, and practitioners look to WHA International to provide answers and improve safety around oxygen — before a dangerous oxygen fire can harm personnel and damage property.
Hazards Analysis: Oxygen safety experts at WHA leverage their experience to identify risks in oxygen materials selection and component design. WHA’s formal Oxygen Fire Risk Analysis (OFRA) tool is the predominant method used to analyze oxygen fire risks in both systems and components for industries worldwide. After analysis, WHA’s experts can then provide recommendations on how to make systems and components safer for use with oxygen.
Oxygen Testing: WHA personnel utilize standard and custom tests to evaluate materials and components for use with oxygen. These tests range from promoted ignition of small materials samples to large-scale energetic reactions at WHA’s remote testing grounds outside Las Cruces. The resulting data can inform hazard analysis studies, improving materials selection and component designs.
Technical Training: WHA offers specialized training to help industry stay safe around oxygen. These courses are available in a variety of formats, in-person and online. Content is structured by skill level, ranging from essential hazard awareness to advanced analysis and design techniques.
Oxygen Cleaning: Because contaminant particles or greases can easily ignite or kindle a fire within an oxygen system, specialized cleaning must be performed. Every day WHA personnel clean and bag hundreds of parts for use in oxygen. Their experts also routinely evaluate cleanliness and assess cleaning processes for manufacturers worldwide.
Failure Analysis: When something goes wrong, WHA is one of the few organizations with the specialized skills to investigate the cause and origin of an oxygen fire. While these projects can involve litigation and expert witness, their efforts often go further to walk through changes to prevent similar incidents and protect lives and property in the future.
Further reading: explore more case studies from WHA International.
This case study was adapted from an article initially published by WHA International in the August 2023 GasWorld Medical Issue.
Share this entry
Related Articles
Battery Safety Insights with Nic Linley, Electrical Engineer
Battery technology continues to evolve rapidly in the 21st Century, powering an expanding array of devices and…
Oxygen Cylinder Filling System Fire Case Study
Oxygen cylinders and pressure systems quietly hold enormous amounts of energy. When things go wrong, the results…
WHA Presents O2 Safety Papers at 2024 ASTM G04 Symposium
In October 2024, Gwenael Chiffoleau, Nic Linley, and Brent Houser traveled to Prague for the 16th ASTM…
Request an expert
consultation
Contact us to request a free consultation with an experienced engineer who can help you better understand your needs and our solutions.