WHA’s Hydrogen Combustion Risk Analysis (HCRA) Method
Rapid changes in the hydrogen industry have led to a need for a more comprehensive approach to analyzing the risk of hydrogen fires and explosions. In just the last ten years, hundreds of new H2 industry safety standards have been developed, and they continue to grow in number and complexity. In many situations, hydrogen-application-specific standards and safety guidelines do not yet exist.
Without proper risk analysis and safety measures, the potential for leaks, component rupture, contamination, or even a combustion event may exist.
To meet this pressing need, WHA International has improved upon an in-depth Hydrogen Combustion Risk Analysis (HCRA) method based on NASA H2 hazard assessment protocols and decades of hydrogen failure analysis and hazard analysis experience. This meticulous process can be applied to both systems and components with variable levels of detail, depending on client needs.
With this newly refined HCRA process, we’re paving the way to a safer future for everyone involved with hydrogen.
Authority based on experience
WHA’s hydrogen safety expertise is informed by decades of failure analysis investigations. Our engineers and scientists have analyzed hundreds of incidents involving hydrogen, oxygen, and other hazardous fuels.
For years, our Oxygen Fire Risk Analysis (OFRA) method has helped set the standard for oxygen safety, protecting countless equipment and personnel around the globe. The approach is consistent with key industry standards for performing oxygen hazards analysis on systems and components.
Unfortunately, there are few equivalent standards and guidelines when it comes to hydrogen risk analysis, so our hydrogen safety experts stepped up to the plate to create something new and fill this gap. We took our experience with oxidizers and fuel gasses and customized a process unique to the hazards of hydrogen.
Our engineers have been utilizing this general approach for some time, but in light of recent growth in the hydrogen industry, they have refined the process to create an all-new formal Hydrogen Combustion Risk Analysis (HCRA) method.
WHA’s HCRA method is also informed by our active leadership and involvement in industry organizations, including ISO and the Hydrogen Safety Panel.
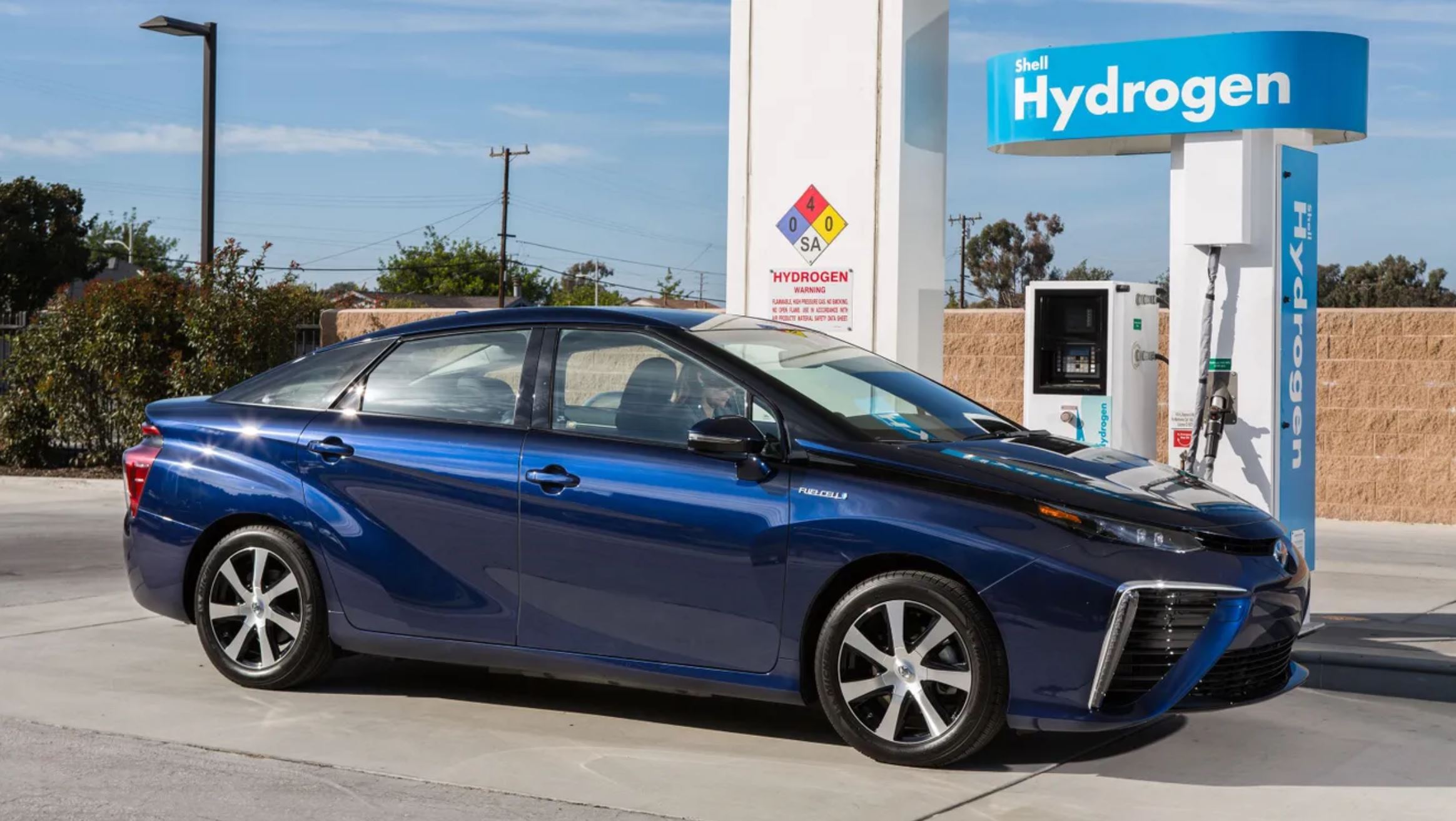
When is compliance sufficient?
Many technical professionals wonder if they should be more concerned with compliance or risk. In reality, they are two sides of the same coin.
For a manufacturer to be compliant, they must adhere to the broad-based safety requirements within their industry and adopted by their Authority Having Jurisdiction (AHJ). In many cases, compliance standards are highly conservative to accommodate a variety of applications and situations. Compliance is useful as far as established standards exist.
The benefits of customized risk analysis
Common applications of hydrogen may fall under basic compliance guidelines; however, when systems and components exceed the scope or complexity of existing standards, there will always be a need to go deeper and assess true application-specific risk. Risk analysis is a data-driven approach to assessing the likelihood of an event within a specific application.
Many new hydrogen systems are truly unique, some with novel applications or unusual operating conditions. Oftentimes, the industry is simply growing too rapidly for the standards to keep up. Regulators cannot create standards for each new application, so companies must rely on a more customized approach to risk analysis.
Companies may also utilize a risk-based approach if they have difficulty achieving minimum safety standards for compliance purposes. Because regulations are typically conservative, they sometimes come with a caveat that “safe use” criteria may be exceeded if manufacturers can provide sufficient application-specific evidence that it is safe to do so.
Even when standards do directly apply, risk analysis can also be used to identify safety vulnerabilities and increase confidence in a system or component.
You can read more about a similar risk-based approach to oxygen “safe use” criteria here.
Types of Analysis
Our risk analysis solutions can be applied to both components and systems utilizing hydrogen or hydrogen blends.
- System-Level: Analyzes the overall risks and relationships between components and subsystems within a hydrogen system. Considers design as well as operational and administrative controls.
- Component-Level: Analyzes the parts, materials, and overall risks within components intended for use in hydrogen systems.
By nature, risk analysis is a highly customized process. As such, WHA’s HCRA services can be performed at different levels, depending on the degree of detail required.
- Level 1 Hydrogen Hazards Consult (HHC): High-level review intended to provide rapid feedback. Typically appropriate for verbal remote review.
- Level 2 Hydrogen Hazards Review (HHR): The same approach as a Level 1, but includes a short summary report documenting the results.
- Level 3 Hydrogen Combustion Risk Analysis (HCRA): Our most extensive hazards analysis for hydrogen systems and components, including detailed probability rankings and recommended hazards mitigation strategies.
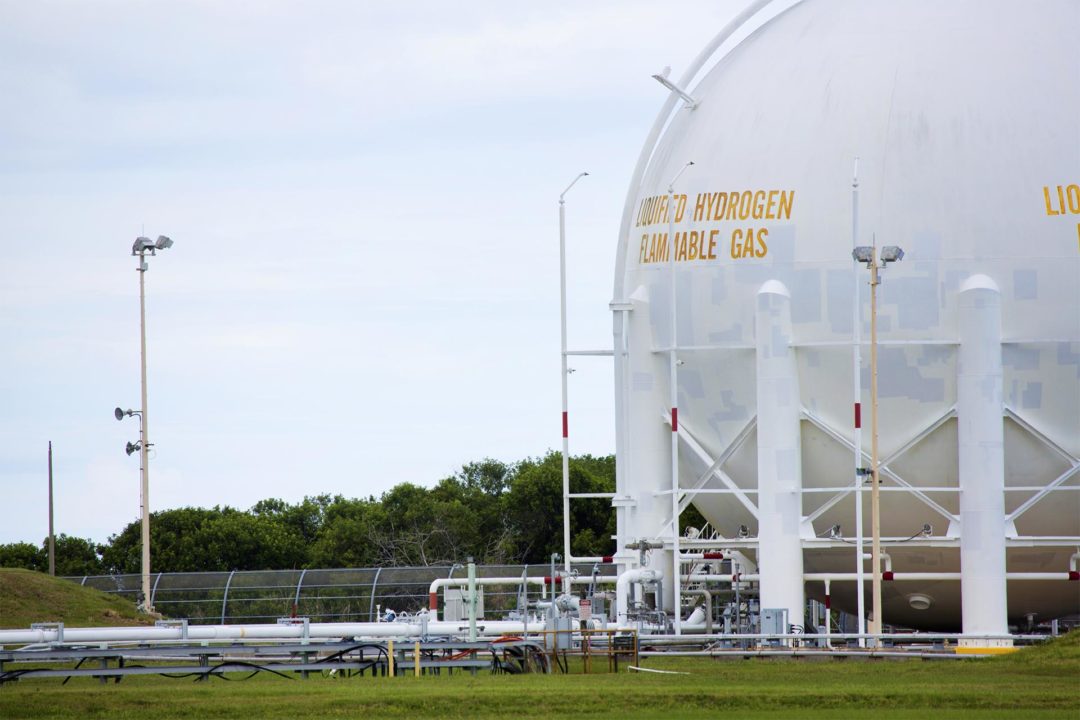
The HCRA Process
Hydrogen has several unique properties that create different risks compared to other fuel gases. It’s very lightweight (the lightest of any molecule), small, and “slippery.” Hydrogen can find its way out of many seats, seals, and components typically considered to be “airtight.” It has a wide flammability range and a low ignition energy, meaning that it can easily ignite at many different concentrations.
In simple terms, WHA’s HCRA approach considers the three components of the hydrogen fire triangle: fuel, oxidizer, and an ignition source. Because hydrogen is so easily ignited at even low concentrations, WHA’s method primarily focuses on limiting the unintentional mixing of hydrogen and an oxidizer like air.
The approach analyzes the probability of operations and failure modes that can lead to combustible mixtures and ignition events resulting in fire, deflagration, or combustion. It also considers the consequences of combustion as they relate to personnel safety, system objectives, and functional capability.
WHA’s services include:
- System documentation and component information review
- System-level hazards analysis
- Design review (overall system design and relationships between subsystems and components)
- Administrative controls review (operating, maintenance, emergency, and training procedures)
- Material compatibility analysis
- Combustion consequence and secondary effects analysis
- Detailed component analysis
Header image photo by Dennis Schroeder, NREL 32586
Share this entry
Related Articles
Battery Safety Insights with Nic Linley, Electrical Engineer
Battery technology continues to evolve rapidly in the 21st Century, powering an expanding array of devices and…
WHA Launches Oxygen Equipment Supplier Certification Program
Ignition and combustion hazards are present in almost all oxygen and oxygen-enriched systems, and catastrophic fires have…
Advancing Large-Scale Electrolyzer Safety
Electrolyzer safety is becoming increasingly important as the industry undergoes significant change to meet the growing demand…
Request an expert
consultation
Contact us to request a free consultation with an experienced engineer who can help you better understand your needs and our solutions.