WHA Launches Oxygen Equipment Supplier Certification Program
Highlights
- Oxygen safety relies heavily on oxygen equipment suppliers (OES) to deliver products with oxygen-compatible materials and a verified level of cleanliness.
- Oxygen equipment suppliers face an increasingly complex landscape of safety requirements.
- WHA’s new Oxygen Equipment Supplier Certification Program helps both suppliers and their customers grow safely and confidently.
Ignition and combustion hazards are present in almost all oxygen and oxygen-enriched systems, and catastrophic fires have occurred in nearly every industry that uses oxygen. Oxygen fire risk mitigation relies heavily on oxygen equipment suppliers (OES) to consistently deliver products with traceable oxygen-compatible materials and a verified level of cleanliness.
Today, oxygen equipment suppliers (e.g., manufacturers, assemblers, or cleaners) face an increasingly complex landscape of safety requirements. They must often demonstrate compliance with multiple international standards from different industries as well as from a diverse global customer base with differing requirements.
In response, WHA has created a new Oxygen Equipment Supplier Certification Program, ensuring that oxygen-relevant processes comply with industry best practices for oxygen service and fire risk mitigation.
This new offering stands to help both suppliers and their customers grow safely and confidently in the oxygen industry.
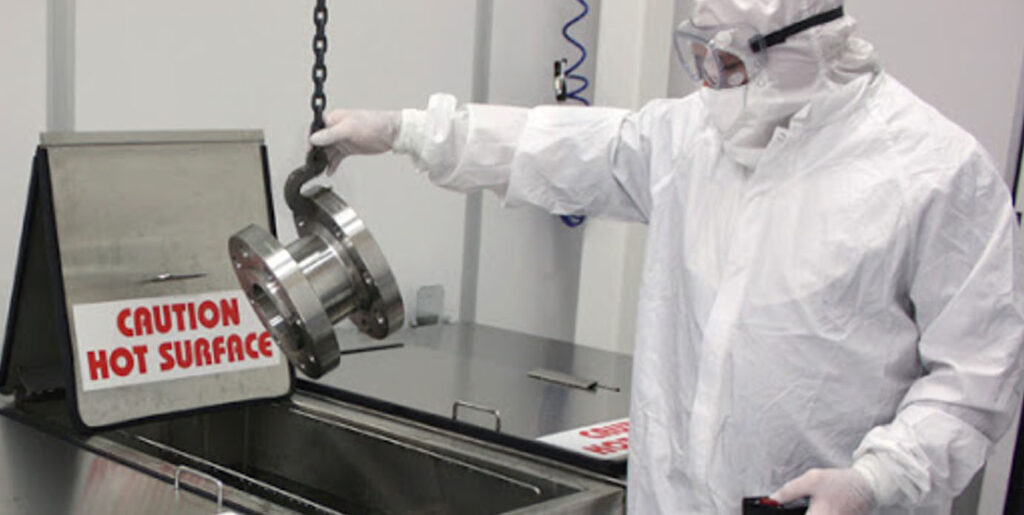
Oxygen Equipment Suppliers Face Increased Scrutiny
In recent years, several publications from the Compressed Gas Association (CGA) and the European Industrial Gases Association (EIGA) have been revised and harmonized, adding quality requirements for oxygen equipment suppliers, including valve manufacturers. Even more recently, the Manufacturers Standards Society of the Valves and Fittings Industry, Inc. (MSS) published a revision to their oxygen cleaning standard.
These documents include:
- CGA G-4.14 / EIGA Doc 200/17: Quality assurance, quality control measures for valves and spare parts, Section 13
- CGA G-4.1 / EIGA 33/18: Quality assurance, quality control measures for oxygen cleaning, Section 12
- ANSI/MSS SP-138-2023: Quality Standard Practice for Oxygen Cleaning of Valves and Fittings
The scrutiny doesn’t stop there; however, as many experienced oxygen users and suppliers, including the major industrial gas companies, have their own set of requirements. They also want to audit their suppliers to ensure their equipment is properly specified, cleaned, verified, and packaged as required for use with oxygen.
“Oxygen equipment suppliers have to consider many design factors to accommodate different customer applications,” explains WHA CEO Gwenael Chiffoleau, Ph.D. “However, most have very similar requirements for oxygen: suppliers need to demonstrate that they can produce functional, clean and compatible valves and equipment. The CGA and EIGA harmonized publications and the MSS standard provide an opportunity to target minimum requirements for suppliers that are accepted by most customers of oxygen equipment.”
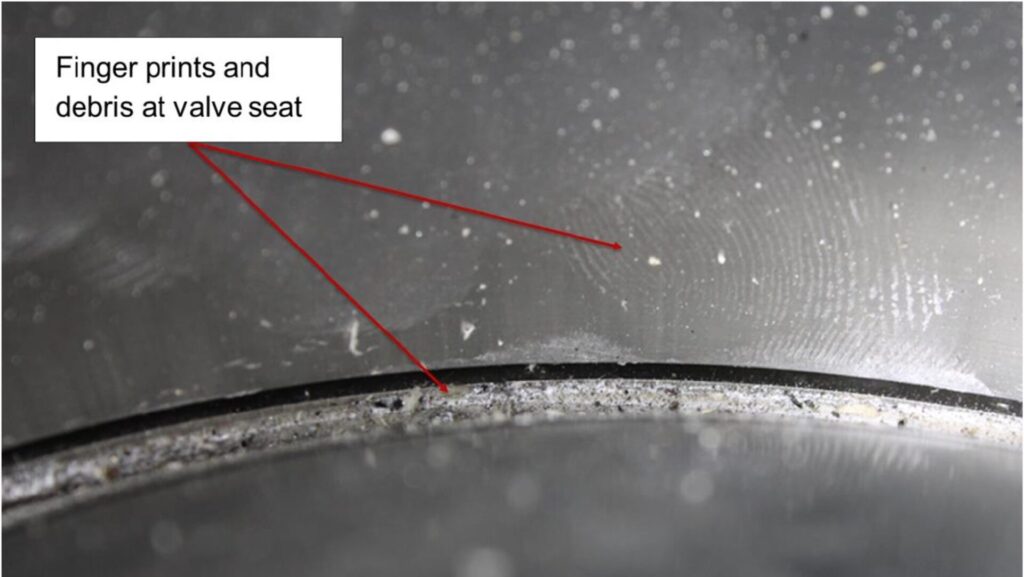
WHA Serves as an International Authority
While standards and guidelines exist, there are currently no official certifying agencies for oxygen equipment suppliers. Suppliers and customers must perform their own audits to determine compliance — an expensive and time-consuming process.
“We’ve been asked to serve in that capacity for many years,” says Elliot Forsyth, PE, WHA Chief Strategy Officer. “Now we’re stepping up to take a more formal role in offering this service because WHA is a globally recognized expert on the topic and also helped develop the standards.”
The program is primarily intended for industrial oxygen valve manufacturers, given the specific requirements listed in the CGA / EIGA documents. However, it can also be applied to suppliers of other industrial oxygen pressure equipment, such as pumps and compressors, filters, heat exchangers, piping, instrumentation, pressure vessels, and others. OESs for other oxygen industries, such as medical/healthcare and aerospace, can also benefit from this type of auditing and certification, especially considering the criticality of this equipment for life support or propulsion applications.
Auditing Oxygen Clean Processes
The certification program audit focuses on materials traceability/compliance and the processes used by suppliers to receive, clean, inspect, verify, assemble, test and package oxygen equipment. Incompatible materials and contaminants, such as particulate and non-compatible oils and greases, pose a severe fire risk, and oxygen cleanliness must be achieved and maintained throughout the process.
Common steps that are audited include:
- Receiving and tracking third-party cleaned parts
- Disassembly and pre-cleaning (if required)
- Piece part cleaning and drying
- Inspecting clean parts
- Assembling clean parts
- Pressure testing and functional testing clean assemblies
- Preserving and preparing clean assemblies for shipment
The audit scope can also include addressing customer orders, procuring, receiving, traceability, and control of materials and their associated oxygen compatibility testing/justification.
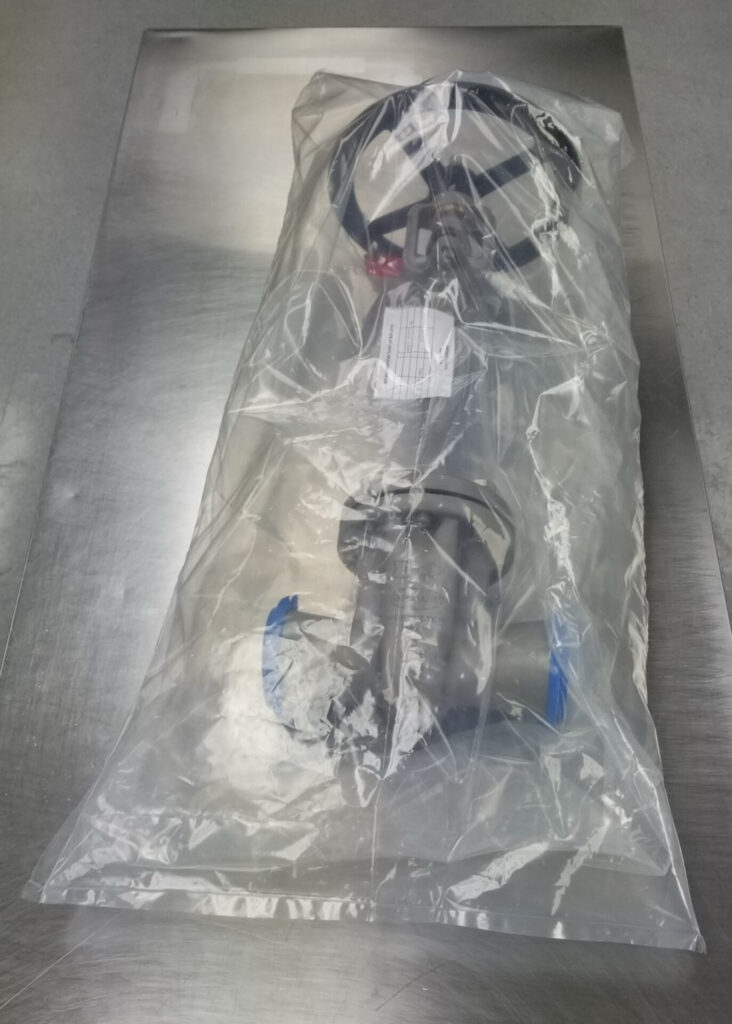
WHA’s OES Certification Process
WHA’s Oxygen Equipment Supplier Certification Program follows a phased approach. Each phase may require more than one revision in order to achieve compliance:
- Audit Scope and Plan: WHA works with the client to identify personnel, locations, and internal documentation needed for the audit, as well as the standards and cleanliness specifications each process must satisfy.
- Desktop Audit: WHA reviews the provided documentation and seeks any additional information that is required.
- Live Audits: WHA performs onsite and/or virtual inspections of the oxygen equipment supplier facilities, evaluating each process, from manufacturing to cleaning to assembly/testing to packaging and final shipping.
- Oxygen Cleanliness Verification (OCV): Tests at WHA’s laboratories quantify the cleanliness of oxygen equipment compared to the required cleanliness specifications.
- Audit Reporting and Certification: After the successful completion of phases 1-4, the supplier receives a detailed report and official certification from WHA.
After certification, suppliers will continue to receive periodic maintenance audits and checks to demonstrate that they maintain compliance.
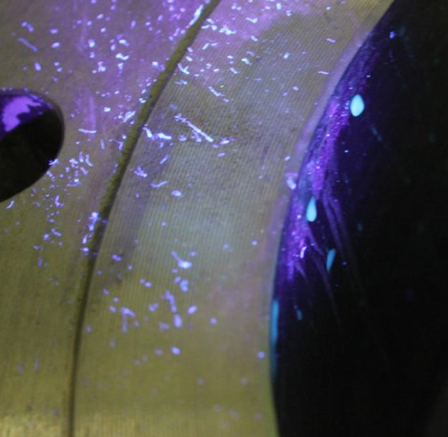
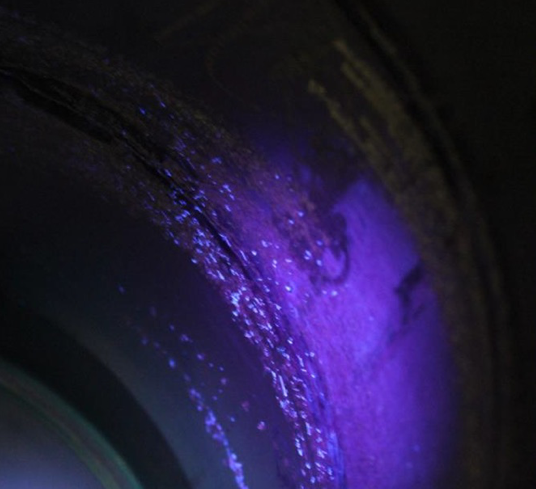
Additional Support
Throughout the process, WHA identifies nonconformities and opportunities for improvement. The program is designed to educate and equip oxygen equipment suppliers with everything they need to achieve compliance and demonstrate safe practices.
Optional consulting and support services include:
- Process Consulting: WHA can help optimize or create new oxygen cleaning programs.
- Training: WHA offers oxygen safety training customized for personnel involved with producing oxygen-clean equipment.
- Hazard Analysis: WHA offers oxygen fire risk analysis (OFRA) services for oxygen components as referenced in industry standards.
- Testing: WHA offers a wide variety of oxygen compatibility testing options to help qualify materials for oxygen service to numerous standards worldwide.
Industry Benefits
WHA’s new certification program is already benefiting equipment suppliers and their customers. When customers accept WHA’s audit in lieu of their own, the vendor certification process is dramatically simplified.
“We’re offering these services as an independent third party to help our clients achieve their goals and increase oxygen safety on a global scale,” says Dr. Chiffoleau. “Maintaining an approved supplier list is a very rigorous process, and responding to multiple audits from various customers is time-consuming. We’re cutting down the time and costs required for both suppliers and customers to do so.”
By creating a unified process and language around certification, WHA also hopes to benefit the industry as a whole with more consistency between the ways that OESs are being evaluated.
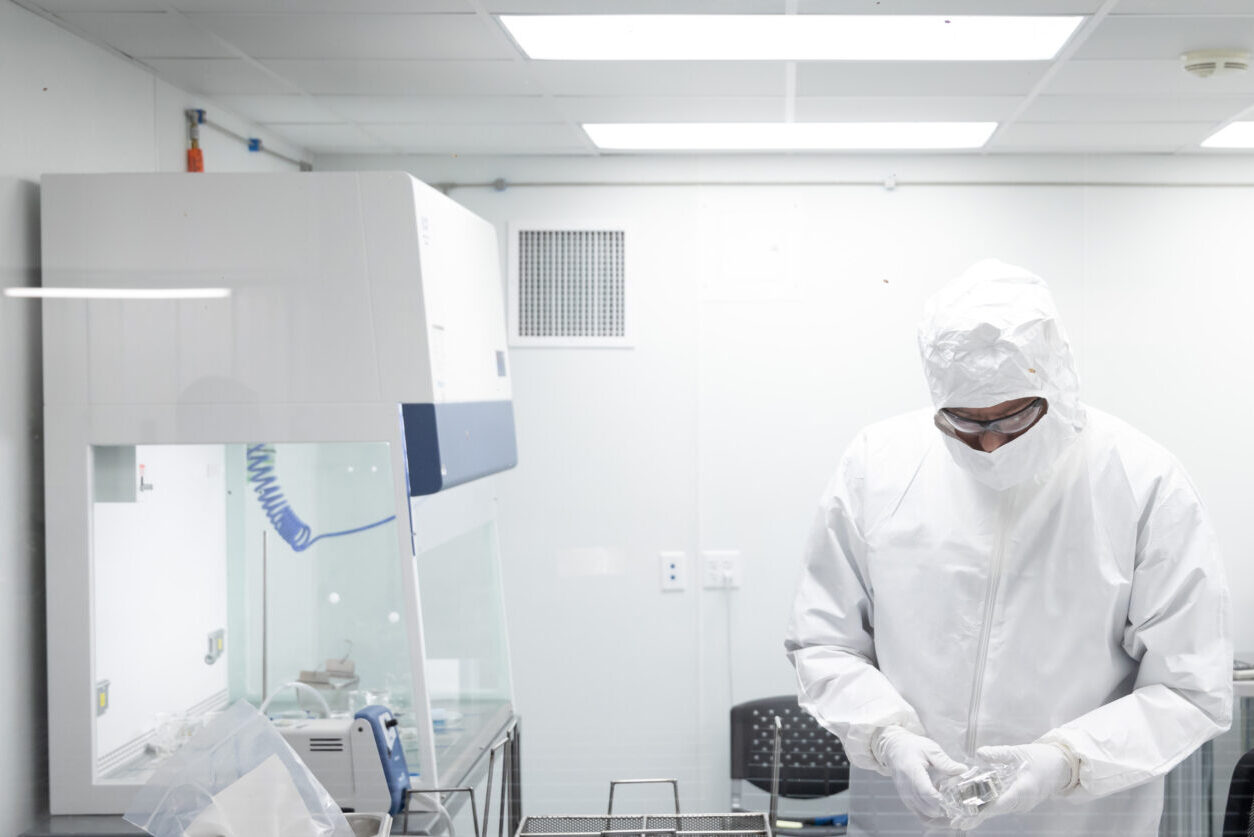
Leverage WHA’s Oxygen Equipment Supplier Certification Program
Are you a manufacturer of oxygen equipment needing to demonstrate the safety and compliance of the products you supply?
Are you a customer of oxygen equipment needing to verify the safety and compliance of the products you receive?
Contact us to learn more about WHA’s Oxygen Equipment Supplier Certification Program.
Share this entry
Related Articles
Battery Safety Insights with Nic Linley, Electrical Engineer
Battery technology continues to evolve rapidly in the 21st Century, powering an expanding array of devices and…
Oxygen Cylinder Filling System Fire Case Study
Oxygen cylinders and pressure systems quietly hold enormous amounts of energy. When things go wrong, the results…
WHA Presents O2 Safety Papers at 2024 ASTM G04 Symposium
In October 2024, Gwenael Chiffoleau, Nic Linley, and Brent Houser traveled to Prague for the 16th ASTM…
Request an expert
consultation
Contact us to request a free consultation with an experienced engineer who can help you better understand your needs and our solutions.