The Evolution of Particle Impact Ignition Testing in Oxygen
Highlights
- NASA paved the way for the historical understanding of particle impact ignition in oxygen and related testing.
- Recent work at WHA has shed new light on the specifics of particle impact ignition, including the ability of particles to ignite in curved tubing and by compression heating.
- WHA’s work advances the possibility of quantitative risk analysis methods.
Earlier this year, ASTM hosted a two-day workshop on particle impact ignition organized by the ASTM Committee G04 on the Compatibility and Sensitivity of Materials in Oxygen Enriched Atmospheres. The event was held from April 25-26, 2023, at NASA White Sands Test Facility (WSTF) in Las Cruces, NM, and Dr. Gwenael Chiffoleau, WHA International’s Chief Technical Officer, served as co-chair.
Throughout the workshop, several participants presented papers on topics of interest related to particle impact ignition and testing in oxygen.
Three presentations from engineers at WHA offered a big-picture perspective about the discipline: where we came from, where we are now, and where we are headed as an industry.
Key takeaways from these presentations are captured below.
The Origins of Particle Impact Testing
Much of our understanding of particle impact ignition comes from work by the United States National Aeronautics and Space Administration (NASA) in support of the Space Shuttle program throughout the 1980s and the 1990s.
NASA White Sands Test Facility (WSTF) developed test setups using high-pressure oxygen that flows around a test sample, either a 2.5 cm (1 in.) diameter disk or a smaller 1 cm (3/8 in.) diameter cup fabricated from a metal alloy. Particles of various sizes, shapes, masses, and materials are injected into the flow upstream, where they are rapidly accelerated to impact the sample. NASA has a sub-sonic and a supersonic gas velocity configuration of this test apparatus.
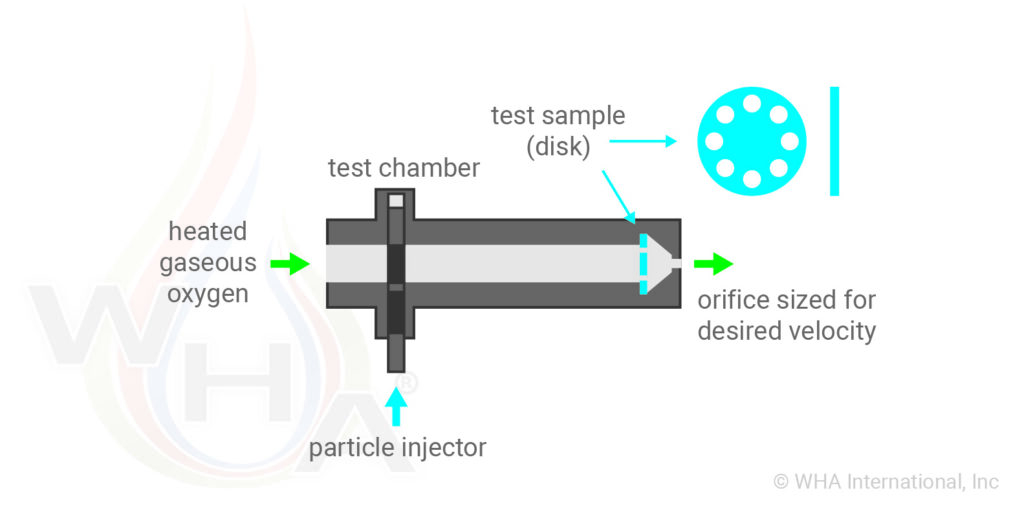
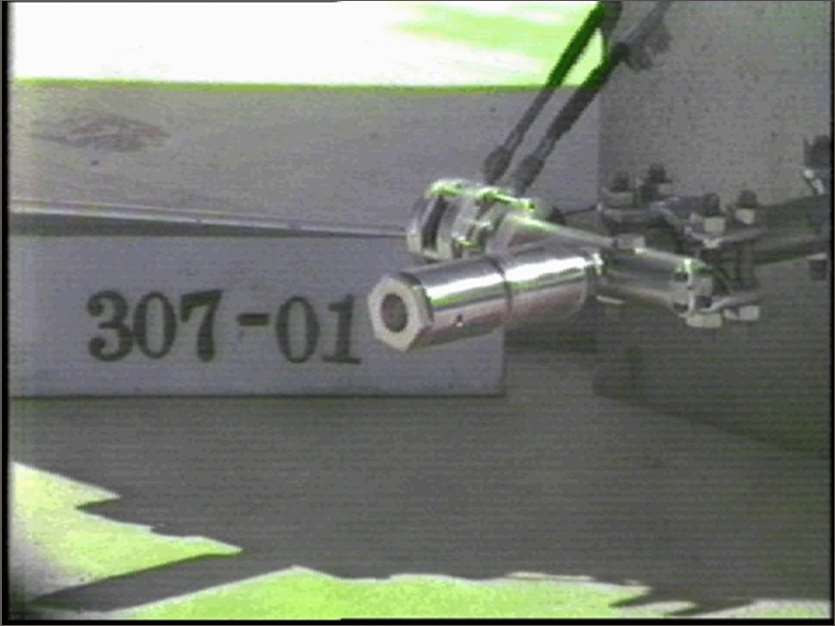
Because compressed gaseous oxygen will cool down the sample as the gas expands out of the system, a large-heat exchanger can heat the gas upstream of the test apparatus. Operators initiate flow and then wait until the system reaches a steady state condition (including pressure, temperature, and flow) before they inject the particles.
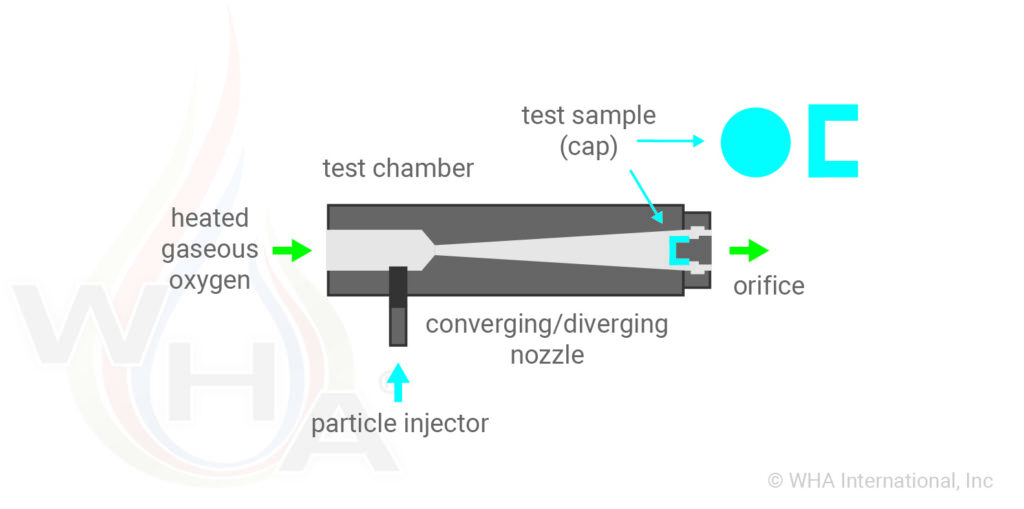
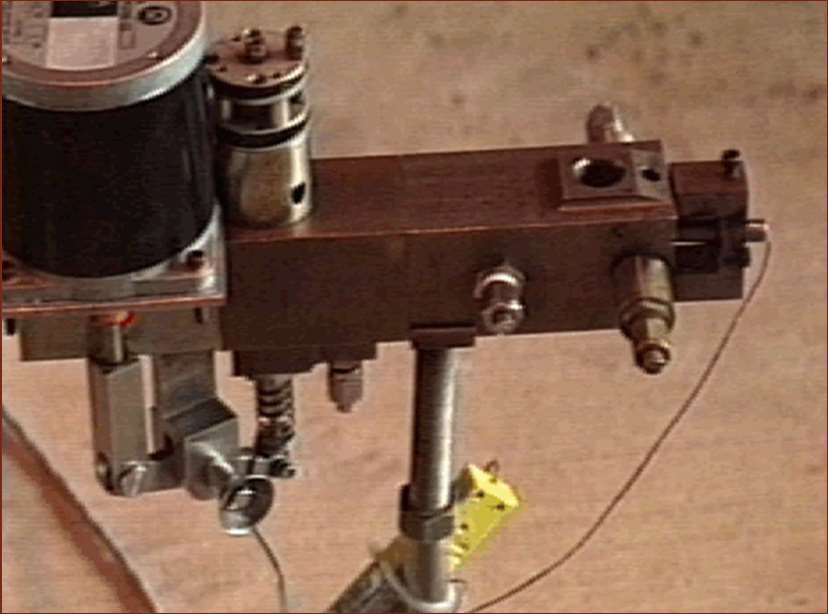
Elliot Forsyth, WHA’s Chief Strategy Officer and Principal Engineer, worked as a test engineer at NASA WSTF early in his career and performed significant particle impact ignition testing during his time there.
“In addition to providing critical data for their space program applications, NASA published multiple peer-reviewed papers on their particle impact testing in oxygen, which has benefitted all of industry. NASA’s historic particle impact testing has provided invaluable data and a fundamental understanding of the mechanics behind particle impact ignition,” says Elliot.
The Evolution of WHA’s Particle Impact Test Method
As WHA adapted specialized oxygen safety knowledge from NASA for commercial applications, its particle impact ignition test methods also evolved.
Instead of injecting particles into an already flowing stream, WHA’s system launches particles with the initial gas release. WHA’s method evaluates particle impact ignitions in this transient flow compared to NASA WSTF’s steady-state flow condition. The transient nature of WHA’s method is designed to simulate real-life flow conditions in oxygen systems during a start-up.
This configuration eliminates the need for large heat exchangers, meaning the test can run more efficiently and affordably for commercial clients. If needed, the pressurized gas can still be pre-heated (for example, 60 degrees Celsius is a common test temperature for materials in oxygen), and/or the test article can be heated (> 300 degrees Celsius).
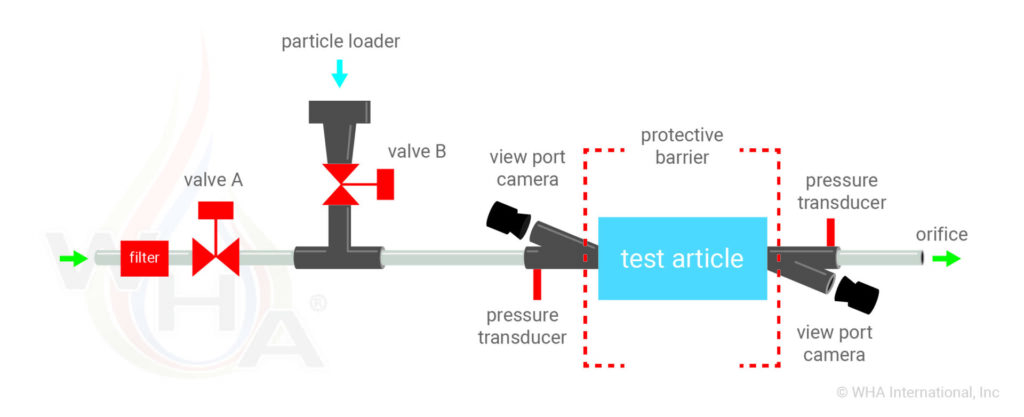
With its new particle impact test setup, WHA has been able to focus more on testing assembled components rather than material samples, closely simulating real-world conditions to evaluate the risk of ignition in application.
WHA’s Seeks to Better Understand Particle Impact Ignition
Recently, WHA engineers have utilized their new particle impact test system, fitted with state-of-the-art technology, to better understand particle impact ignition at a fundamental level.
During this “checkout testing,” the team focused primarily on what conditions are necessary for igniting the particles themselves – not necessarily the target material. They explored various gas velocities, pressures, and particle materials.
Brent Houser, a chemical engineer in charge of running WHA’s particle impact tests, played an important role in this checkout testing and presented the team’s findings during the ASTM workshop.
“It’s challenging to get ignition every time, but we were able to get consistent particle ignition in various configurations,” explains Brent. “Throughout the tests, we saw that other ignition mechanisms may play a role, like compression heating and particle friction. This was a big finding.”
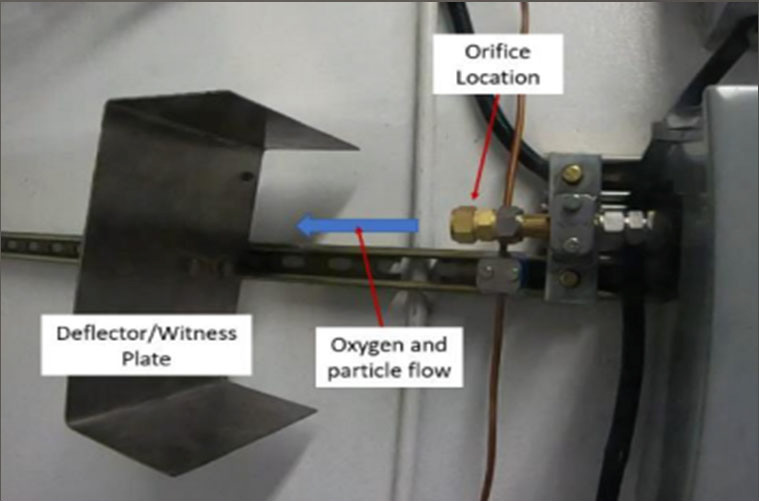
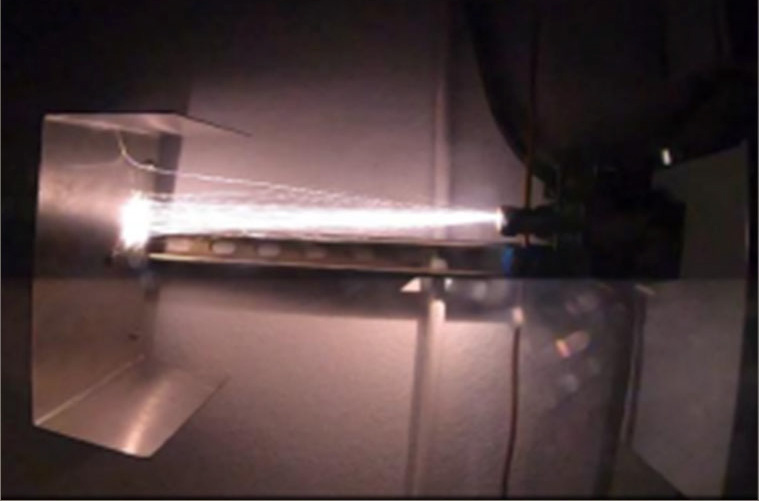
Particle Ignition on Curved Piping
As industry leaders continue to advance the science in understanding particle impact ignition, unique new test configurations provide data that help define the mechanisms at work.
Traditional particle impact testing concerns a distinct collision of a high-speed particle with a target. This mechanical event converts kinetic energy into heat energy, and enough heat can ignite the particle and/or the target material.
But what if the interaction isn’t so straightforward (literally)?
Recently, WHA engineers have tested particle impact risk for a heat exchanger application with curved oxygen tubing. A larger 8-inch pipeline delivers oxygen into multiple ¾ inch tubes that run through a larger pressure vessel filled with steam.
Because of the tube’s curved design, there are no perpendicular surfaces with which particles could impact. Instead, particles might scrape along the outer walls or deflect multiple times at different angles. Such interactions raise questions about friction heating and other potential ignition mechanisms that may not yet be understood.
Furthermore, because of the way the tubes are coiled within the larger enclosure, not all of them have the same bend radius. The smaller radius curves feature a more intense “impingement angle,” while the larger radius curves have a longer frictional contact surface. Is one configuration better or worse for particle ignition?
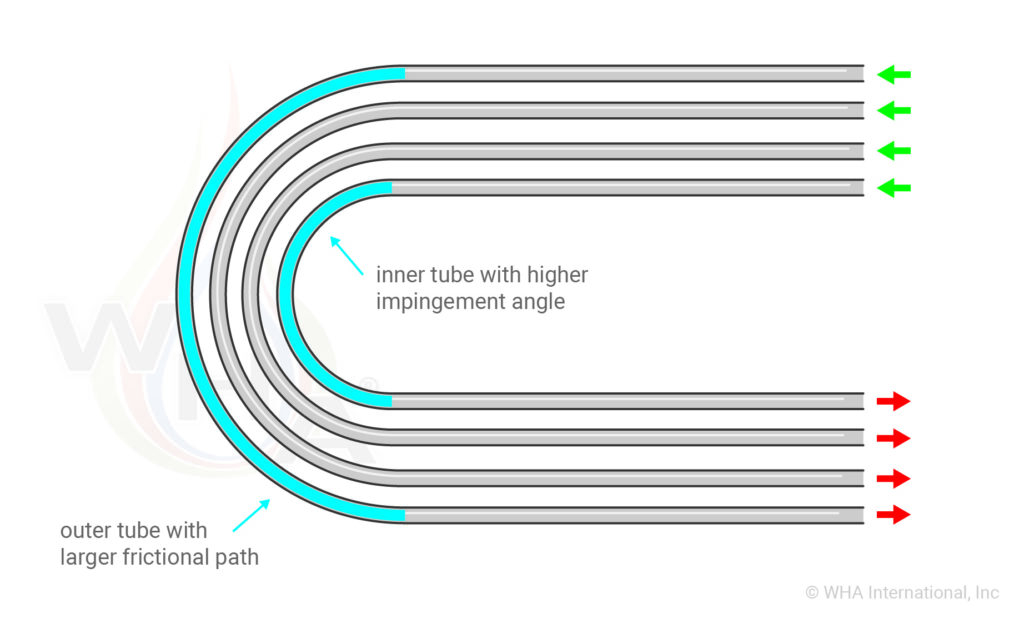
Putting Curved Piping to the Test
Even though the heat exchanger itself is quite large, WHA engineers modified their particle impact test setup to test individual 1.9 cm (¾-inch) curved tubes, one at a time. These tests and subsequent analyses were provided in partnership with Texas A&M University at Qatar (TAMUQ).
This configuration releases pre-heated high-pressure oxygen to launch pre-loaded particulate through a section of curved tubing. High-speed cameras are positioned at optical viewports to look for signs of ignition (e.g., flashes, sustained light emission). After the test, the tubing can be internally inspected for further evidence of ignition and burning.
“We weren’t even sure if we’d get a particle impact ignition with such a low angle of impact,” says Brent. “There’s not much historical data available for this kind of testing.”
Despite their uncertainty, the tests were able to reproduce consistent particle ignitions. “We even have video footage of particles burning against the sides. We were able to track them frame-by-frame and estimate their velocity.”
So, what’s the actual risk of particle ignition? Like all ignition mechanisms in oxygen, multiple factors contribute to the mechanism’s overall severity, and by reducing these factors, the probability decreases. For example, proper cleanliness is essential to minimize contaminants and reduce fire risk. And if ignition and burn-resistant materials are selected, the overall risk of particle ignition leading to burnout may be quite low.
Brent explains that while the particles in WHA’s testing did ignite and deposited combustion products (slag) on the inside of the tubing, they never kindled ignition to the stainless-steel tubes themselves. The tubing remained intact. Further material analysis from TAMUQ concluded that the internal surfaces of the tubes did not exhibit any evidence of ignition. This suggests that the particles ignited from high-speed contact with the bent tube but could not effectively transfer their combustion energy to the tubing wall in this configuration — even though the tubing is was considered flammable in the test conditions and would be expected to burn if ignited.
Further, the 300-series stainless steel tubing used in the test system is above its exemption pressure and pressure-velocity curve according to CGA G-4.4 and EIGA Doc 13. WHA believes that with further configurational particle impact ignition testing and oxygen hazard analysis, industry can better evaluate oxygen fire hazards and, in some cases, justify the use of non-exempt alloys in high gas velocity applications.
In search of quantitative risk analysis
Another big development in the world of particle impact ignition focuses on quantified ignition probability analyses (QIPA). Elliot Forsyth and Dr. Gwenael Chiffoleau gave their workshop presentation on the industry’s ongoing pursuit of QIPA.
“What we do today is more of a qualitative ignition probability analysis. That’s what our OFRA tool is,” explains Gwenael, who oversees WHA’s particle impact test program. “We provide a ranking from zero to four – from not possible to highly probable. These are qualitative expressions of probability.”
With enough test data, QIPA methods can quantify probability, similar to risk analysis performed throughout many industries where large quantities of data are used to make these calculations. For example, a risk of 10-6 represents one in a million probability of the event occurring.
“Many other industries have enough data and understanding of their sciences to provide such quantitative risk, but we’re not quite there yet,” says Gwenael. “How do we move the science towards achieving that goal? Even if we are a ways off, we should be moving in that direction.”
With better scientific understanding, more data, and new projects on the horizon, the engineers at WHA look forward to leading the charge in the ongoing evolution of particle impact ignition testing in oxygen.
Share this entry
Related Articles
Battery Safety Insights with Nic Linley, Electrical Engineer
Battery technology continues to evolve rapidly in the 21st Century, powering an expanding array of devices and…
Oxygen Cylinder Filling System Fire Case Study
Oxygen cylinders and pressure systems quietly hold enormous amounts of energy. When things go wrong, the results…
WHA Presents O2 Safety Papers at 2024 ASTM G04 Symposium
In October 2024, Gwenael Chiffoleau, Nic Linley, and Brent Houser traveled to Prague for the 16th ASTM…
Request an expert
consultation
Contact us to request a free consultation with an experienced engineer who can help you better understand your needs and our solutions.