Hydrogen Risk Assessment methods evolve to serve industry and end-users
The following interview originally appeared in the Hydrogen Issue of the GasWorld global magazine, published March, 2021…
Hydrogen risk assessment has been around ever since humans began recognizing the many useful applications of hydrogen. Today our assessment methodologies continue to evolve in response to the fast-growing commercial hydrogen economy.
To understand where we’ve been—and where the industry is going—we spoke with two WHA hydrogen safety experts: Harold Beeson, Ph.D. and Danielle “Dani” Murphy, Ph.D.
Dr. Beeson’s roots in hydrogen safety evolved over his long career with the United States National Aeronautics and Space Administration (NASA). In the 1990s he led the team that literally wrote the book on hydrogen safety: NASA’s Guide for Hydrogen Hazards Analysis on Components and Systems (NASA/TM-2003-212059). This was later adapted into American Institute of Aeronautics and Astronautics (AIAA) Guide to Safety of Hydrogen and Hydrogen Systems (ANSI/AIAA G-095A-2017).
Dr. Murphy also specializes in hydrogen safety and modern applications of hydrogen. She built her career conducting research at both the Colorado School of Mines and the National Renewable Energy Laboratory (NREL) where much of her work focused on fuel cells and electrolysis systems. Her expertise is also based on experience investigating hydrogen incidents as a forensic engineer…
Let’s start at the beginning. When did people start to get interested in understanding the unique risks of hydrogen?
HB: Well, there has always been some sort of HAZOP [Hazard and Operability Study] type review for hydrogen—failure modes and effects analysis, “what if” analysis—but in the 90s, we took our experience from the Oxygen Fire Risk Analysis (OFRA) method developed at NASA and we started using a similar approach to hydrogen. We needed a structured way to go component by component. You can look at a system, a subsystem, and a component to evaluate the potential fire hazards in hydrogen service. That came out as a formal guide in 2003: The Guide for Hydrogen Hazards Analysis on Components and Systems.
We created another document that expanded upon that in 2008 as an internal investigative report by NASA White Sands Test Facility (WSTF). We took the approach and developed a more detailed protocol: Hydrogen Hazards Assessment Protocol for Components and Systems.
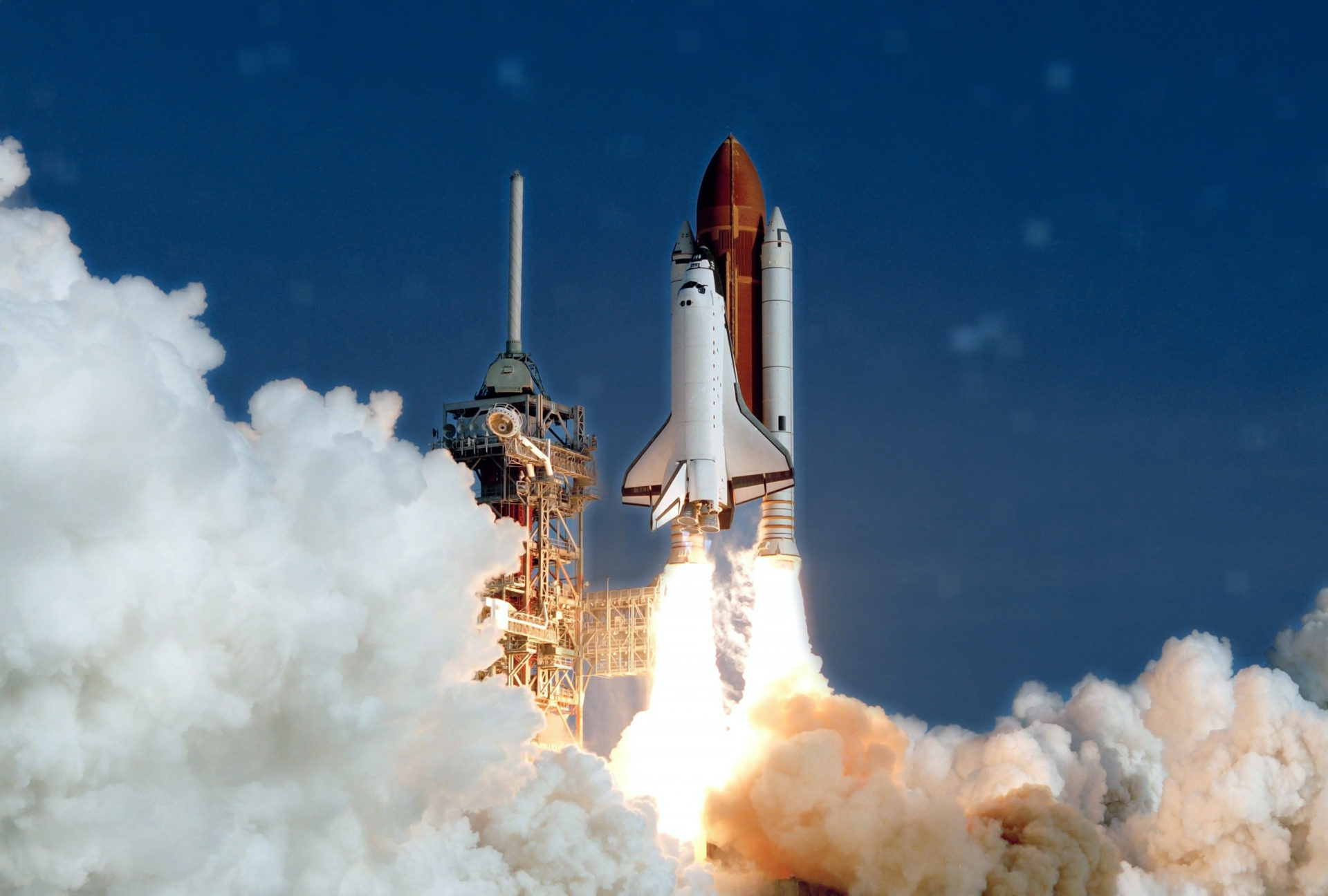
What inspired the development of these hydrogen-specific analysis methods?
HB: A HAZOP analysis will look at a system and let you divide that system up into nodes. It’s more useful at a system level as it considers overall process and operations. A Failure Modes and Effects Analysis (FMEA) is often applied at the component level. The NASA approach lets you do both using the same tool.
DM: You also have to consider that hydrogen’s properties are unique. You can always employ general risk assessment methodologies on hydrogen systems, but the most effective risk assessments process should be tailored and specific to hydrogen or hydrogen-mixtures. You need to highlight the properties — and therefore the hazards — that make it different from other fuels.
Are the analysis methods developed at NASA still used in industry today?
HB: They have been utilized with success for some time on NASA systems, including propellant systems, test systems, electrolysis systems, and fuel cells, but WHA is currently in the process of refining this tool so that it is more efficient at analyzing hydrogen systems used in industry. We need to streamline the analysis approach.
DM: The NASA methodology, although very thorough, is quite complex and requires a significant time investment. WHA is simplifying the process and enabling flexibility, while maintaining comprehensive risk assessments based on client needs. From high-level system analysis to detailed component-level risk assessments, the methodology enables a simple, data-driven, step-by-step approach to identify fire and explosion hazards and enable compliance with current codes and standards.
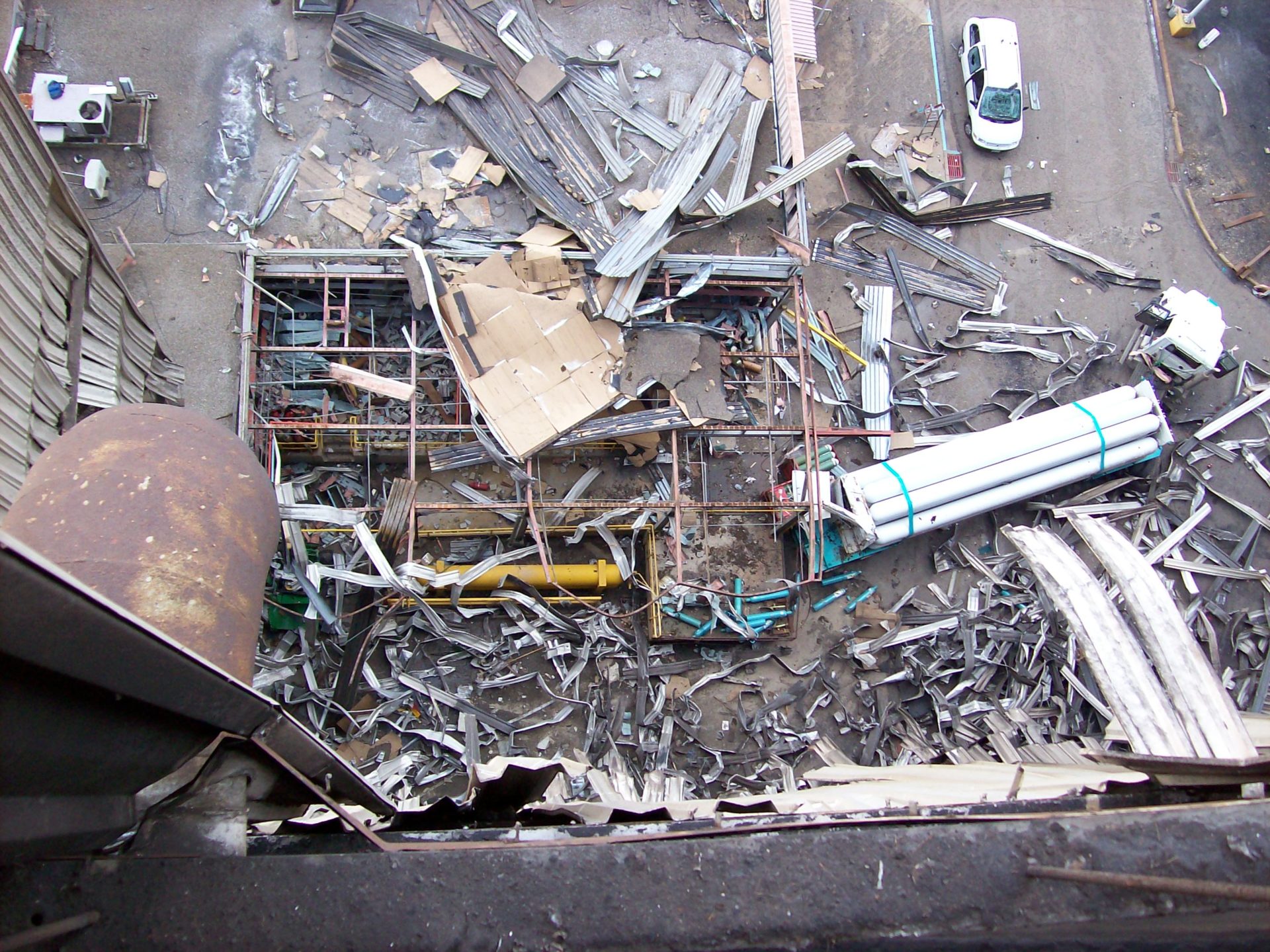
And how has our understanding of hydrogen risks evolved along the way?
HB: As we’ve progressed, one major development is that we’re moving from a qualitative-only approach and pursuing a quantitative risk assessment tool. The qualitative tool says based on experience, you could expect a failure during the lifetime of the system, but a quantitative tool gives you actual numbers. If you’re watching the weather, for instance, you don’t just want to know if it might rain, you also want to know about your chances. Is it 10%? Is it 90%? That probability is going to affect your decisions.
Another improvement is our development of a larger materials database to understand compatibility and how different materials behave around hydrogen.
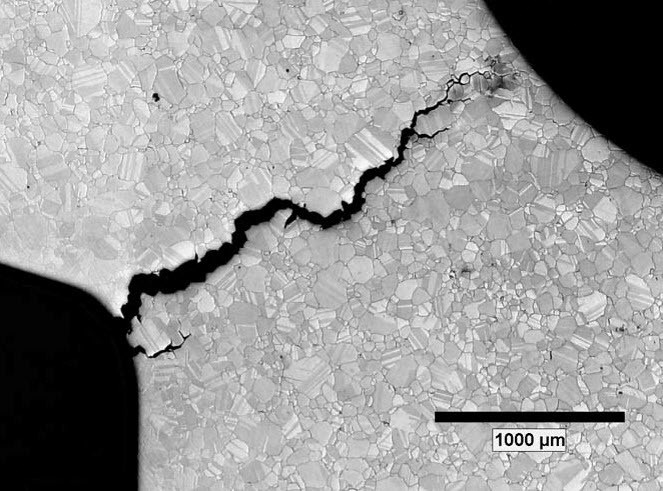
DM: Although it is well understood that hydrogen has an embrittling effect on metals, fundamental research continues to inform material compatibility decisions based on high pressures, temperatures, and stress states. Research is also expanding to include different alloys as well as hydrogen permeation through polymers that may lead to leaks, increased downtime, and life cycle issues with components exposed to hydrogen.
HB: This difference in applications is important to note. At NASA, all our work with hydrogen was at moderate pressures, 3,000-6,000 PSI (around 200-400 bar). Today with hydrogen fuel cell vehicles, you’re talking about very high pressures, greater than 10,000 PSI (around 700 bar). Understanding those new risks is important. That’s what we’re all about at WHA, using innovative, data-driven tools to help our clients use hydrogen safely. There are engineering solutions to all these technical problems.
So modern applications of hydrogen are driving the evolution of our understanding?
DM: Yes, and the growing commercial use of hydrogen has also highlighted the need for more concrete data—data like leak frequency and rates to inform quantitative risk assessments. WHA is actively involved in the Center for Hydrogen Safety working group to gather useable data on equipment and component failure rates. Quantitative risk assessment is only as good as the data associated with it. We’re focused on continuously improving the risk assessment methodologies.
It’s also important to note that as hydrogen use continues to expand to everyday users, the need for fail-safe systems becomes even more important. The original hydrogen safety guides were written for the career experts at NASA, but things change when you consider the average user at a hydrogen filling station may have no training at all. Human error could become a much bigger factor. To enable growth of the hydrogen economy we must first start with safety.
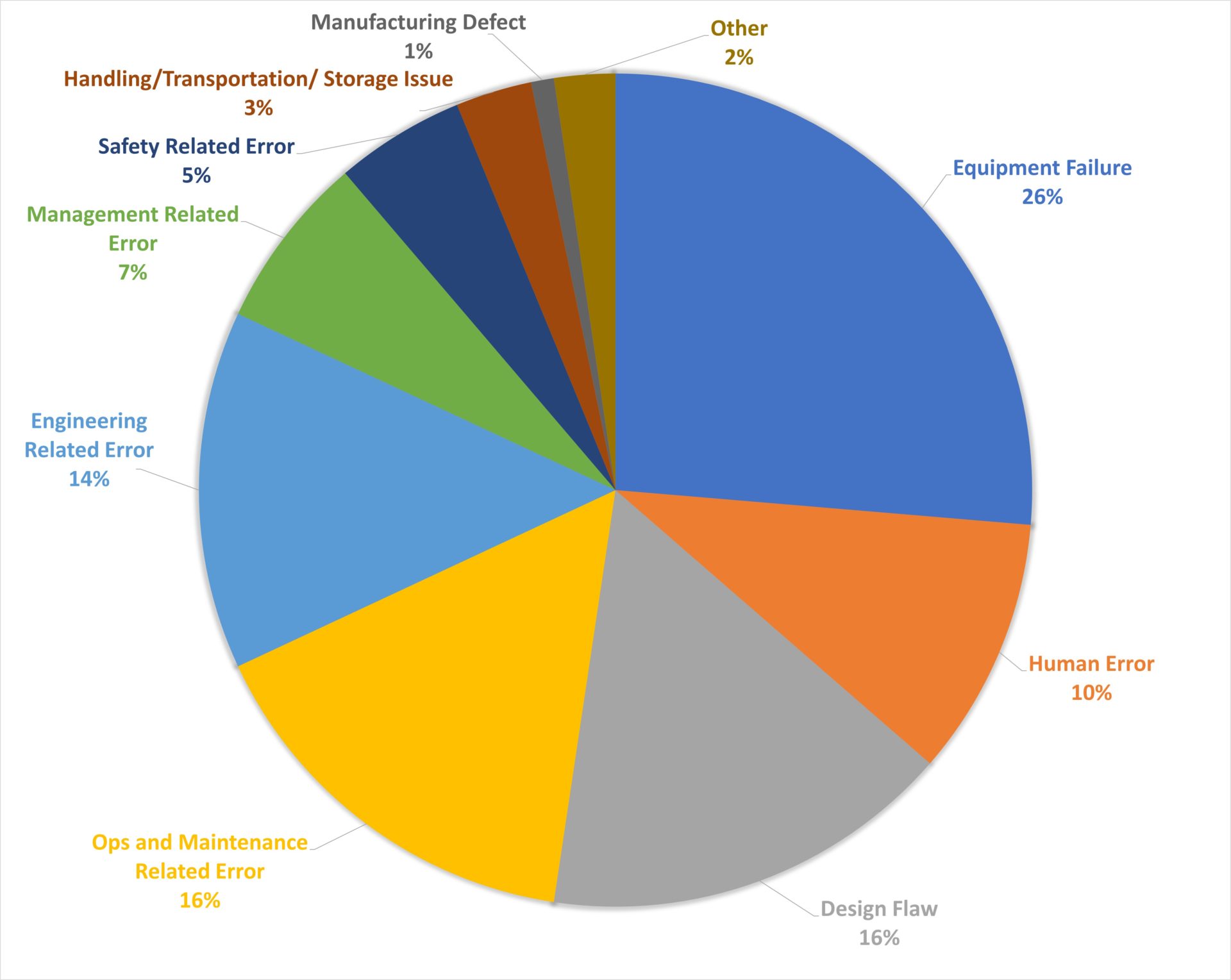
What is industry’s role? What can companies do to assess risks and stay safe?
HB: Proper training in the design of those systems is critical. Manufacturers need to understand materials compatibility in hydrogen, and their design’s potential failure modes so they can effectively manage the fire hazards. At WHA, we offer hydrogen risk assessment services for both hydrogen systems and components. We’re using these highly specialized tools right now to identify risks and help designers understand how to mitigate them.
DM: We also teach our hydrogen risk assessment methodology in our Level 3 and Level 4 training courses so other companies can benefit from the same process in their internal assessments. We provide private custom-tailored corporate training as well as open training events where anyone can attend.
Share this entry
Related Articles
Hydrogen Tank Explosion Demonstration
Typically, hydrogen is safely stored as a purified gas or liquid. Although hydrogen is a fuel, it…
Hydrogen Cleaning: Ensuring Safety and Reliability in Pressurized Hydrogen Systems
Hydrogen is an increasingly important and prominent energy carrier, with applications ranging from fuel cells to electrolyzers…
Battery Safety Insights with Nic Linley, Electrical Engineer
Battery technology continues to evolve rapidly in the 21st Century, powering an expanding array of devices and…
Request an expert
consultation
Contact us to request a free consultation with an experienced engineer who can help you better understand your needs and our solutions.