High-Energy Tests Examine the Origins of Explosive Incidents
This article about WHA’s high-energy tests originally appeared in GasWorld US Hydrogen Issue of June, 2022.
In 2020, SpaceX and NASA launched two astronauts into space — the first manned launch from US soil since the Space Shuttle Program’s retirement in 2011. The Commercial Crew Program was a resounding success, but it almost didn’t happen.
During prelaunch testing, one of the new space capsules exploded. SpaceX and NASA called together a panel of experts to find out what went wrong and how to safely resume the program. The assembled team included Dr. Harold Beeson and Joe Whitehead, both employees of WHA International Inc. at the time. In 2021, NASA presented a Space Flight Awareness (SFA) Team Award to the special group that directly contributed to the success of the Commercial Crew Program.
The investigation centered around the launch vehicle’s rocket system, which utilized hydrazine fuel and nitrogen tetroxide (NTO). NTO is an oxidizer like oxygen, but it is hypergolic, meaning that it will instantly ignite upon mixing with fuel.
This explosive combination is powerful and reliable, even in the vacuum of space. It’s used for NASA hardware, satellite propulsion, and military applications — which is why many specifics around the technology are tightly controlled.
Despite its long history of reliability, new NTO systems push the boundaries of known pressure and flow rates, sometimes causing unanticipated problems. In this case, the incident was traced back to compatibility issues between titanium (Ti) and NTO.
Because NTO is so unstable — and highly toxic — it requires special precautions for safe handling and testing. WHA International had both the experience and the resources to do so.
“The first thing you need to understand is the chemistry of the fuel or oxidizer you’re using,” explains Dr. Beeson, who spent 28 years working with hazardous fluids at NASA before coming to WHA. “You need to know how it reacts with other fuels and oxidizers and with the environment itself. Then you need to look at the unique toxicity. Once you have that understanding, you develop operations and test methods that prevent uncontrolled reactions and chemical exposure to anybody around.”
WHA has special bunkers to perform these dangerous reactions at its remote test site near Las Cruces, New Mexico. The test cells are designed for blasts with ventilation and construction to protect the public and the engineers and technicians involved. Here, the team has safely performed numerous high-energy tests involving gases like nitric oxide, nitrogen trifluoride, silane, hydrogen, and oxygen.
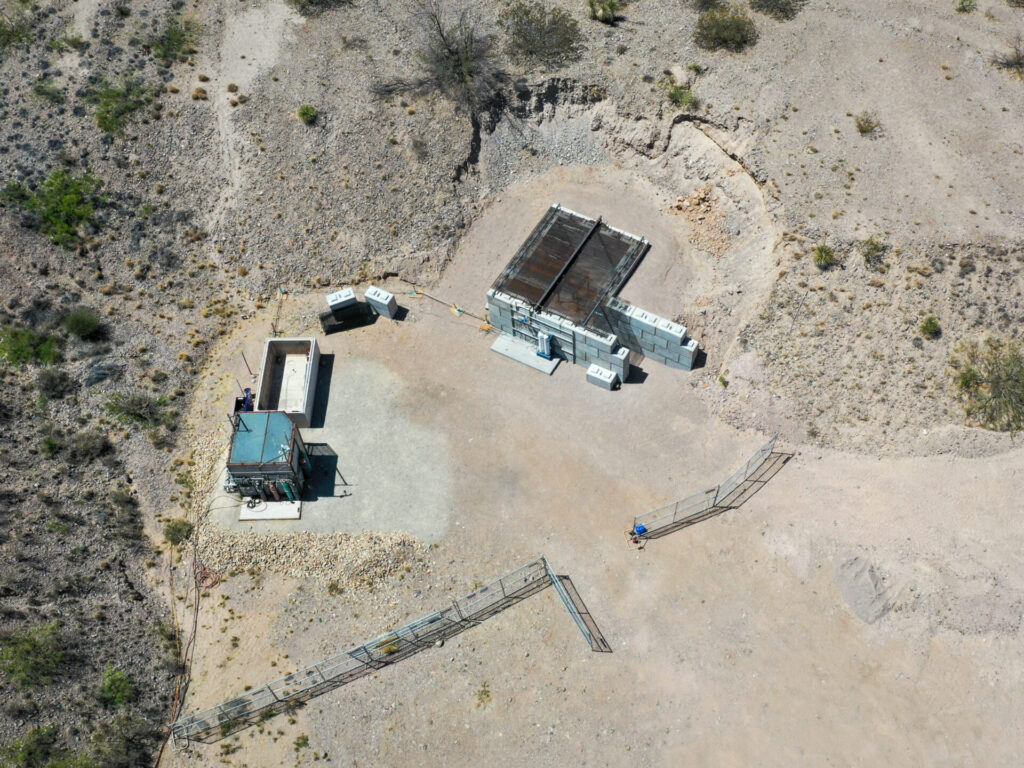
For the particular challenge presented to NASA, WHA team members worked with the NASA White Sands Test Facility (WSTF) to custom-build unique test hardware that could seal at high pressures while still providing visibility of what was happening inside. These high-speed visualizations were vital to helping the team understand what was going on in terms of flow dynamics.
Ultimately, the Ti-NTO Compatibility Assessment Team addressed several problems with design and material changes, and the Commercial Crew Program moved forward without a hitch.
“This was an enlightening experience for continued work with special oxidizers like NTO,” says Dr. Beeson. “Our findings actually influenced a key modification to NASA materials and processes guidance, which previously only required an O2 compatibility assessment. Now it states you have to do a separate compatibility assessment with test data unique to each oxidizer involved.”
Custom high-energy testing isn’t just for rocket applications; WHA regularly works with similar hazardous fuels and oxidizers to support commercial industry too.
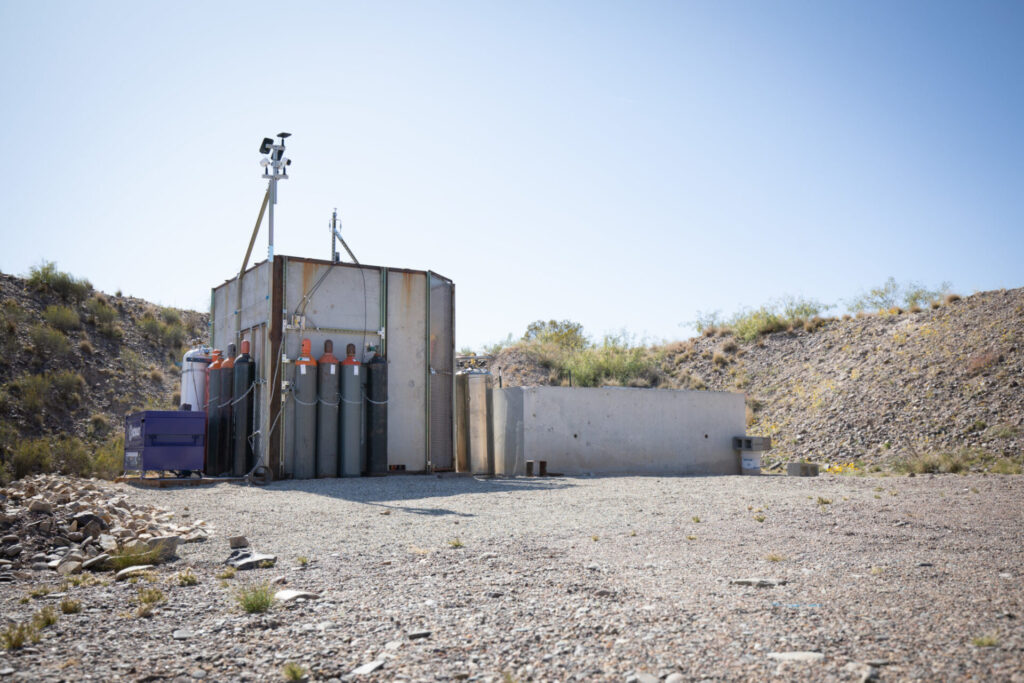
“We expect to see much more work with other fuels, including hydrogen,” shares Dr. Beeson. “We are working to develop the test techniques and improved infrastructure to handle these hazardous fluids at the increased pressures the industry is moving towards.”
Recently, the WHA team has been looking closely at nitric oxide (NO), another highly reactive substance that is used as an additive to NTO, but also has applications in the chemical, medical, healthcare, and aerospace industries. In liquid and solid form, NO is an unpredictable, highly shock-sensitive explosive. As a gas, it’s highly toxic and quickly reacts with air to produce NO2, which is also extremely poisonous.
WHA has conducted testing to evaluate the shock-sensitivity of liquid and solid (frozen) NO using a modified liquid oxygen (LOX) impact test system — similar to the custom testing performed with NASA.

Other high-energy testing at WHA revolves around synthesis gases, primarily inspired by an incident in the US several years ago. Personnel were unloading a high-pressure cylinder from a truck when it exploded, tragically resulting in one fatality.
WHA was involved in the initial failure investigation and continues to perform research for the Department of Transportation (DOT). These ongoing tests investigate the failures associated with aluminum cylinders used for transport of synthesis gases around the country.
When the synthesis gas is triggered to decompose, pressures can develop well above the burst strength of the cylinders, resulting in catastrophic failure. Some of these failures have resulted in high-fragmentation, which is unexpected for aluminum cylinders. The test program has been established to determine the reason for high-fragmentation and will assess potential environmental effects, hyrodgen interaction, and high strain rate.
Through unique custom tests like these, WHA is working to understand the base problem to provide standards organizations, regulators, and industry with the information they need to develop appropriate safety measures.
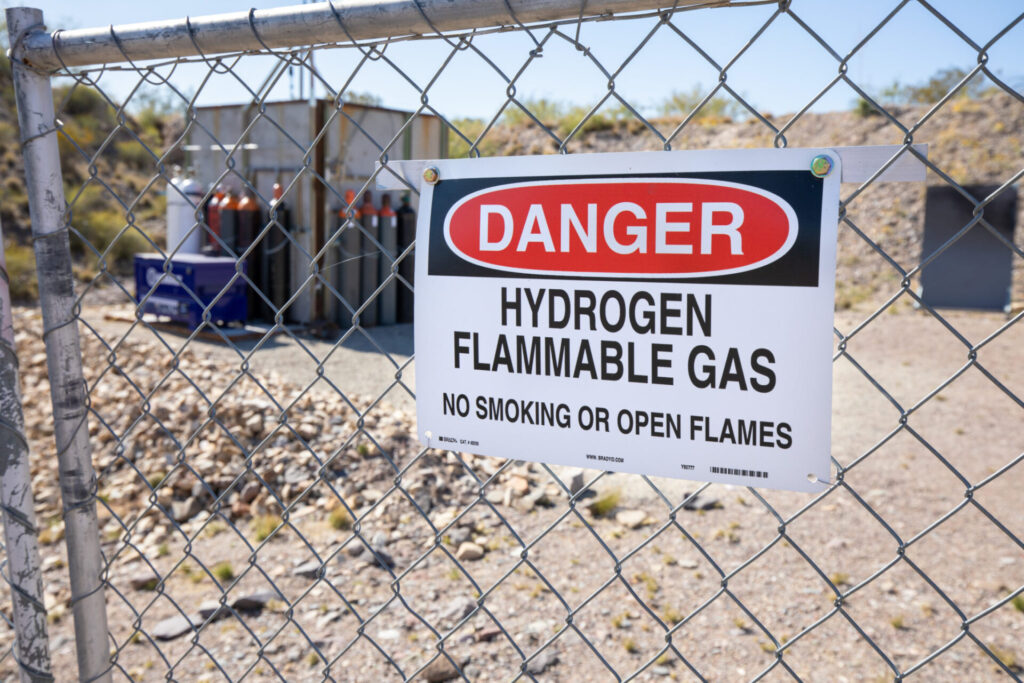
Share this entry
Related Articles
The Evolution of Particle Impact Ignition Testing in Oxygen
Earlier this year, ASTM hosted a two-day workshop on particle impact ignition organized by the ASTM Committee G04 on the…
Case Study: Aluminum Oxygen Tank Fires Initiated by Impact
In recent years, several notable oxygen tank fires have occurred after a fall or sudden impact. WHA...
Particle Impact Testing in Oxygen Supports Material Selection and Component Design
Particle impact testing helps determine the conditions required to ignite particulate contamination, materials, or components in oxygen...
Request an expert
consultation
Contact us to request a free consultation with an experienced engineer who can help you better understand your needs and our solutions.