Case study: medical oxygen regulator research and testing protect users around the world
Every day, medical breathing oxygen is delivered to millions of users. Oxygen plays a critical role in the ongoing Coronavirus pandemic as it’s delivered through ventilators to treat the most severe COVID-19 patients.
Today the healthcare industry uses medical oxygen equipment safely, largely without incident, but this was not always the case. In the 1990s, a disturbing rise in medical oxygen fires caused severe burns to multiple emergency personnel and cost millions in damage and lawsuits.
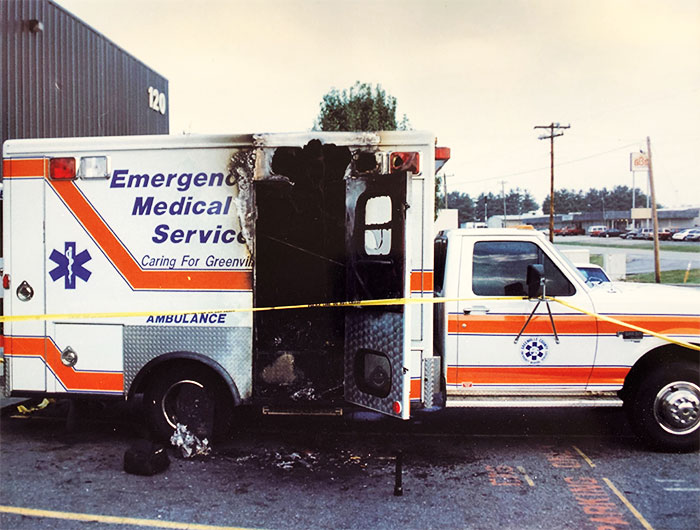
PROBLEM: A growing need for oxygen safety
Between 1993 and 1999, the United States Food and Drug Administration (FDA) received reports of 17 fires, all involving aluminum regulators attached to portable oxygen cylinders. These incidents caused severe burns to 11 healthcare workers, the loss of two ambulances, and damage to a fire station.
WHA International (then known as Wendell Hull & Associates) had developed subject matter expertise through previous investigations of 11 other medical oxygen regulator incidents around the world.
In response to the rising need, the FDA and the National Institute for Occupational Safety and Health (NIOSH) raised the alarm.
The following chain of events involved multiple distinguished organizations and dozens of scientists and engineers who put their heads together. Perhaps now more than ever, it is a success story we need to hear — a case study showing how careful methodology, enthusiastic collaboration, and scientific innovation can solve problems and protect lives.
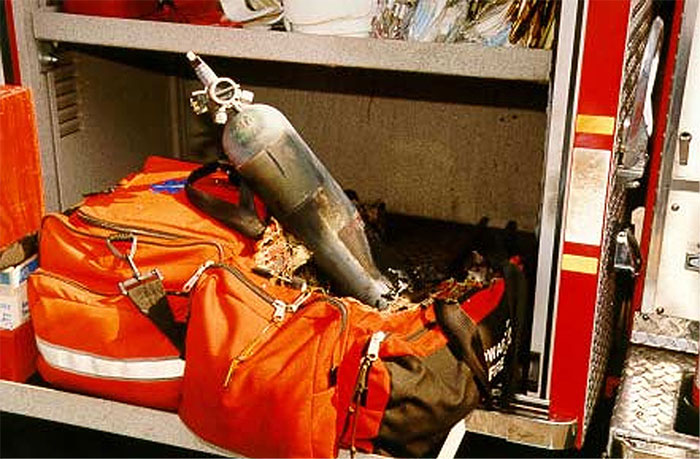
BACKGROUND: Why is oxygen so dangerous?
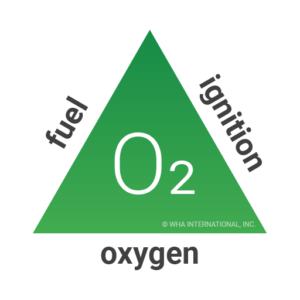
Oxygen is not a fuel (like gasoline or hydrogen). It does not burn. So why is it so dangerous?
Oxygen is an oxidizer that allows other fuels to burn. Pure or “enriched” oxygen environments are hazardous because materials can ignite more easily and burn more vigorously. Materials like aluminum don’t burn in our normal atmosphere (approximately 21% oxygen), but they will burn under elevated oxygen concentration and/or pressure.
Technical training experts here at WHA often rely upon the “fire triangle” to illustrate the relationship between fuel, oxidizer, and ignition source.
PROCESS: Global experts step up to find solutions
ASTM International took the lead to coordinate efforts around the medical oxygen regulator problem, specifically relying on Committee G04 on the “Compatibility and Sensitivity of Materials in Oxygen Enriched Atmospheres.” The committee formed a special task group to research and develop a new standard test method to evaluate and improve regulator designs.
At the time, members of WHA International held leadership positions on this committee (and still do today). WHA had long served as a critical link between government regulatory agencies and industry, and was perfectly positioned to take the lead in the investigation.
In order to develop a new standard test, the task group had to first understand what was going wrong in regulator fires around the world. Then they could attempt to create a reproducible ignition event in a lab to simulate real-world conditions. By examining distinct fire patterns and other clues, WHA forensic engineers determined that four ignition mechanisms contributed to at least 11 fires in their records.
- Heat of compression ignition – When a cylinder valve is first opened, high pressure gas flows into the mechanism and rapidly recompresses. This compression creates heat which can ignite nonmetallic materials in the regulator.
- Contaminant ignition – Heat of compression can also ignite flammable foreign contaminants within the oxygen system. Improper lubricants such as hydrocarbon oils are easily ignited.
- Particle impact ignition – Gas flows extremely fast when a valve is opened (close to the speed of sound!). This can propel small metallic particles or other contaminants with enough energy to start a fire upon impact. Aluminum is extremely susceptible to this kind of ignition.
- Promoted ignition – Once ignition has occurred upstream, fire can propagate with the gas flow to kindle other materials in its path.
Location of Incident | Date of Incident | Regulator Filter/Piston | Operation During Incident | Ignition Mechanism a |
Springfield, Ore. | 12/27/93 | SS/Alum | Flowing (5-7 min) | Particle ImpactPromoted Ignition |
Greeley, CO | 7/13/95 | SS/Alum | CV b Just Opened | Contamination |
Boone, NC | 10/6/95 | Bronze/Brass | Flowing (4-6 min) | Particle Impact |
Austin, TX | 6/14/96 | SS/Alum | CV Just Opened | Contamination |
Houston, TX C | 6/15/96 | SS/Alum | CV Just Opened | Unknown c |
Houston, TX C | 7/15/96 | SS/Alum | CV Just Opened | Heat of Compression d |
Gournee, IL | 3/23/97 | SS/Alum | CV Just Opened | Promoted Ignition |
Broward County, FL | 6/12/98 | Bronze/Aluminum | CV Just Opened | Particle Impact |
Greenville. SC | 8/27/98 | SS/Alum | CV Just Opened | Particle ImpactPromoted Ignition |
Oak Creek, WI | 1/21/99 | SS/Alum | CV Just Opened | Promoted Ignition |
Reno, NV | 1/25/99 | Bronze/Aluminum | CV Just Opened | Particle Impact |
a This column lists the ignition mechanisms that were considered to have the highest probability based on the evidence inspected.
b CV – cylinder valve
c The failure analyses for the two Houston incidents were not performed by WHA. However, WHA personnel inspected the fire-damaged regulators as part of other investigations.
d Although this incident was not investigated by WHA, the only material consumed in the fire was the regulator seat.

SOLUTIONS: Recommending improvements to medical oxygen regulator designs
From the beginning, it was clear that better materials selection could vastly improve the safety of oxygen regulators. Every incident involved regulators primarily constructed out of aluminum. Aluminum is valued for its light weight and affordability, but it is also susceptible to many ignitions. Once ignited, it can burn in oxygen in pressures as low as 170 kPa (25 psi). WHA therefore recommended that highly compatible alloys like brass be utilized for critical “oxygen wetted” areas of regulator design. Brass is heavier, but resistant to burning in oxygen up to 70 MPa (10,000 psi).
WHA also identified additional safe design principles for medical oxygen regulators. Proper materials selection, filter design, and protection for vulnerable parts can greatly reduce the risk of particle impact ignition, contaminant ignition, and promoted ignition. Safe design can also consider protection around flammable components such as valve seals and springs.
SOLUTIONS: An emphasis on safe use practices
Good oxygen components will tolerate reasonable foreseeable user error, but the human element is always the last piece of the puzzle. Several of the incidents WHA investigated involved user error, such as improper maintenance and the use of multiple gaskets or hydrocarbon lubricants between the valve and regulator.
Oxygen users at every level should be properly informed of the risks, and in fact, the United States Occupational Safety and Health Administration (OSHA) mandates that proper training be provided to personnel using hazardous materials like oxygen.
Today, WHA offers technical training to help industry stay safe around oxygen. These courses are available in a variety of formats in-person and online. Content is structured by skill level, ranging from basic hazards awareness to advanced analysis and design techniques.
- O2 Aware – introductory hazard awareness
- O2 Practice – intermediate knowledge of materials selection, ignition, and best practices for operation and maintenance
- O2 Design – advanced understanding of oxygen system design and analysis methods
- O2 Analyze – expert application of the Oxygen Fire Risk Analysis (OFRA) method, featuring case studies, and special topics for expert understanding
SOLUTIONS: Developing a new standard safety test.
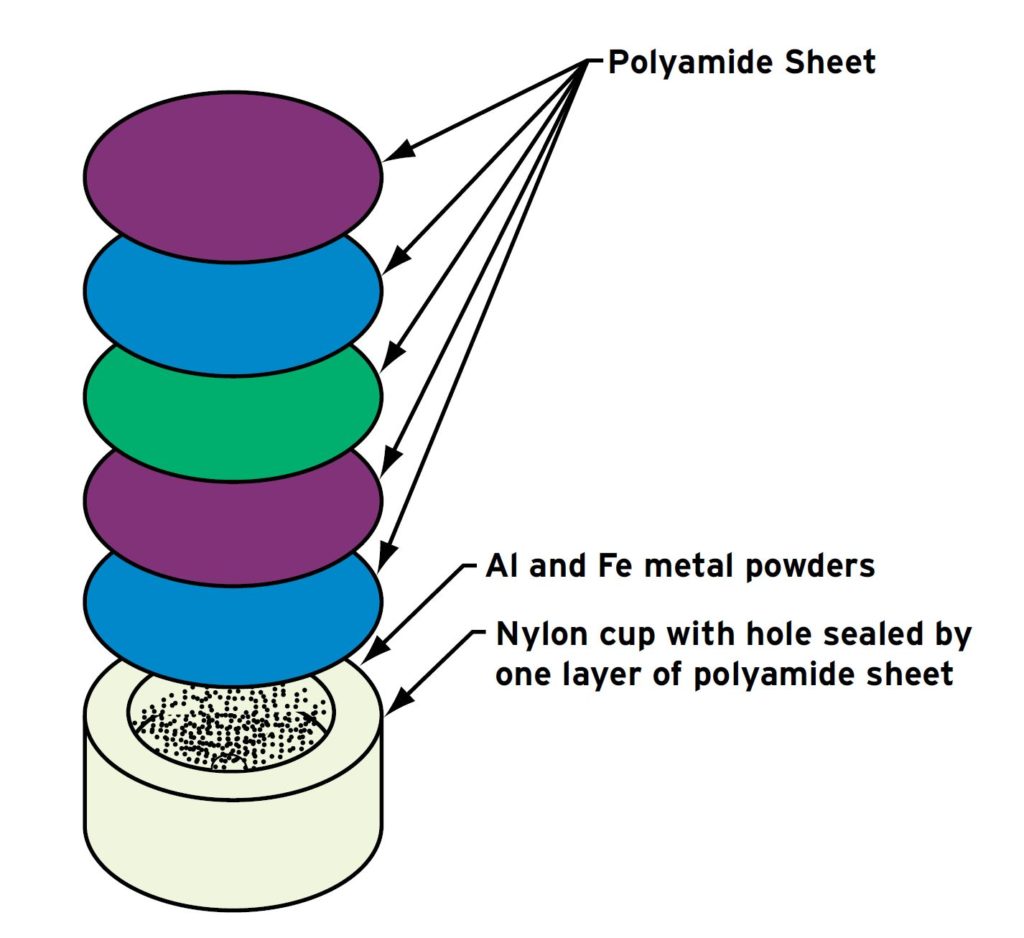
In order to develop a new standard test method, the task force first built on an existing ISO test for assessing ignition resistance to heat of compression. The new test would follow a similar approach but would “promote” or force ignition to see how the regulator would perform in a dangerous real-life ignition situation.
In order to promote ignition, WHA developed an “ignition pill” to be placed at the regulator inlet where it could be ignited by heat of compression. The pill contains a combination of metallic and nonmetallic materials, replicating contaminants that could be found in actual application. These dangerous contaminants can easily create a “kindling chain” to ignite the metallic component of the regulator.
This promoted ignition test replicates the effect of many of the historic regulator incidents. It’s enough energy to create catastrophic failure and dangerous flames. In a successful test scenario, however, a fault tolerant regulator would dissipate the heat of ignition without burning out.

Research and testing for this new standard involved cooperation with ASTM International, the FDA, and NIOSH and took place at WHA’s Test Facility and NASA White Sands Test Facility. Other laboratories around the world also helped fabricate the new ignition pills and validate consistent methodology and results.
ASTM Committee G04 approved the new promoted ignition test standard ASTM G175 in 2003.
UPDATE: Evolving technology introduces new challenges
Since the late 2000s, WHA has also been heavily involved in the application of ASTM G175 for valve integrated pressure regulators (VIPRs), which have become quite popular. These devices combine both a valve and regulator into one component that is attached to an oxygen cylinder. VIPRs are often used at higher pressures than stand-alone medical regulators.
The new intricate designs and applications of VIPRs introduce different risks, and WHA has investigated numerous brass-bodied VIPR fires. Again, in cooperation with ASTM International and the FDA, WHA led a task group and similar research efforts to improve VIPR safety. In 2013, a new version of ASTM G175 was released that included a new promoted ignition test customized for VIPRs.
RESULTS: A safer world for medical oxygen
Since the approval of this new standard almost 20 years ago, there have been no new incidents recorded involving medical oxygen regulators that met the requirements of ASTM G175. The research and development of the new test standard was a resounding success, clearly preventing any further personal harm, property damage, and expensive lawsuits.
Today, WHA typically performs promoted ignition testing on up to 15 new regulator types each year using ASTM G175. Only a few unique facilities perform this specialized kind of dangerous testing, and very few of them serve private industry.
This truly incredible achievement is a testament to the meticulous care and ingenuity of many collaborating engineers, scientists, and technicians. WHA is proud to have collaborated with multiple distinguished organizations throughout the process, including ASTM International, FDA, NIOSH and NASA.
This article is based on content originally featured in the article “Preventing Oxygen Equipment Fires: Developing an Effective ASTM International Standard to Prevent Further Devastating Medical Oxygen Fires” by WHA staff members Gwenael Chiffoleau Ph.D. and Barry Newton Ph.D., published in ASTM Standardization News, November/December 2008. The original article received the First Place 2008 ASTM International Advantage Award.
Share this entry
Related Articles
Battery Safety Insights with Nic Linley, Electrical Engineer
Battery technology continues to evolve rapidly in the 21st Century, powering an expanding array of devices and…
Oxygen Cylinder Filling System Fire Case Study
Oxygen cylinders and pressure systems quietly hold enormous amounts of energy. When things go wrong, the results…
Nonmetals Oxygen Compatibility Requirements: Guide to CGA/EIGA Compliance
The Compressed Gas Association (CGA) and European Industrial Gases Association (EIGA) have harmonized key documents providing guidance…
Request an expert
consultation
Contact us to request a free consultation with an experienced engineer who can help you better understand your needs and our solutions.