Case Study: Aluminum Oxygen Tank Fires Initiated by Impact
Aluminum oxygen tanks of many sizes are successfully used worldwide, largely without incident. However, in recent years, WHA has been involved with several failure analyses of medical and scuba cylinders that have ignited after a fall or sudden impact.
These oxygen tanks ignited internally and burnt out energetically during the ensuing fire. In most cases, the overall energy release was catastrophic.
This failure analysis case study compares three incidents to explore their similarities and differences.
Incident 1: 2003 Filling Plant Fire
In 2003, an aluminum cylinder fire occurred at a medical oxygen cylinder filling plant. These facilities receive empty or partially full oxygen tanks and place them on racks that simultaneously fill multiple (e.g., 30-40) cylinders (first photo below).
On this occasion, workers had just finished filling a new batch of medical oxygen tanks. As they disconnected them, one cylinder fell off the rack, impacted the concrete, and rolled underneath a cart. The operators briefly heard a hissing sound before a massive explosion occurred. The failed cylinder slammed into two other cylinders (second photo below) and caused injuries to two workers. Fortunately, both workers survived, but the incident left the workers – and the rest of the facility – justifiably shaken.
“It was clear that a major event had happened,” shared Dr. Gwenael Chiffoleau, one of the forensic engineers on the investigation. “There were fire patterns from the explosion, and cylinders, hoses, tanks, and valves scattered everywhere. Molten metal splatter had been launched onto the ceiling and walls.”
When the failed cylinder was recovered, a large hole was observed in the upper body and neck of the cylinder. Combustion patterns were visible on the interior surface of the cylinder wall for several inches below the cylinder threads (third photo).
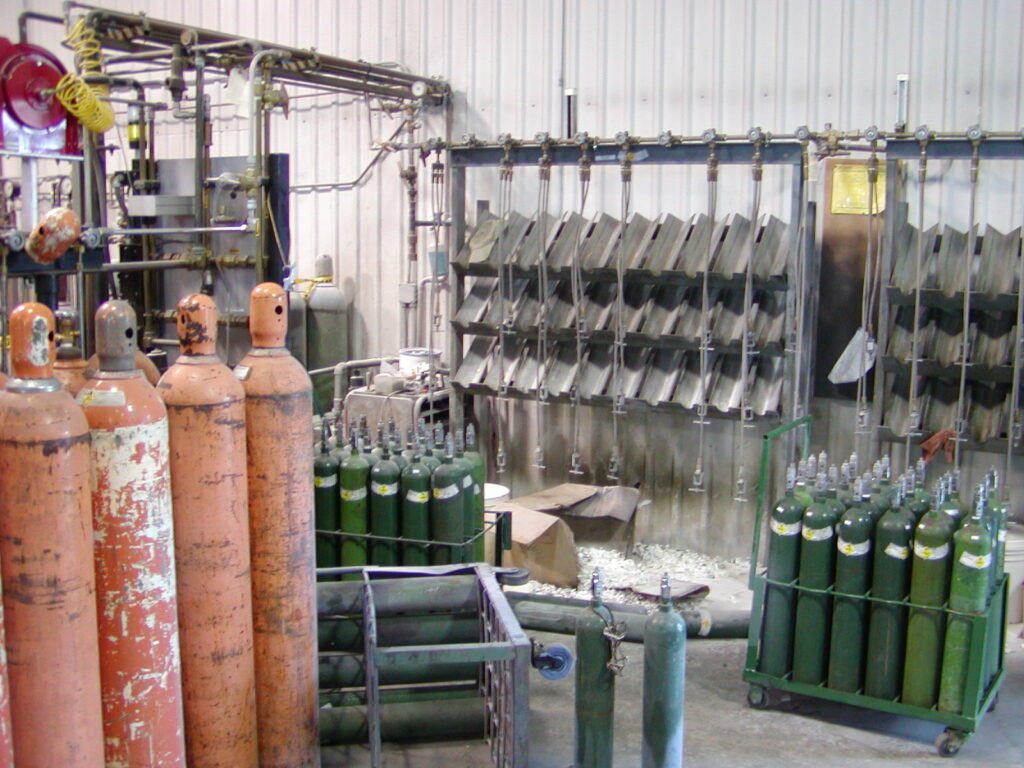
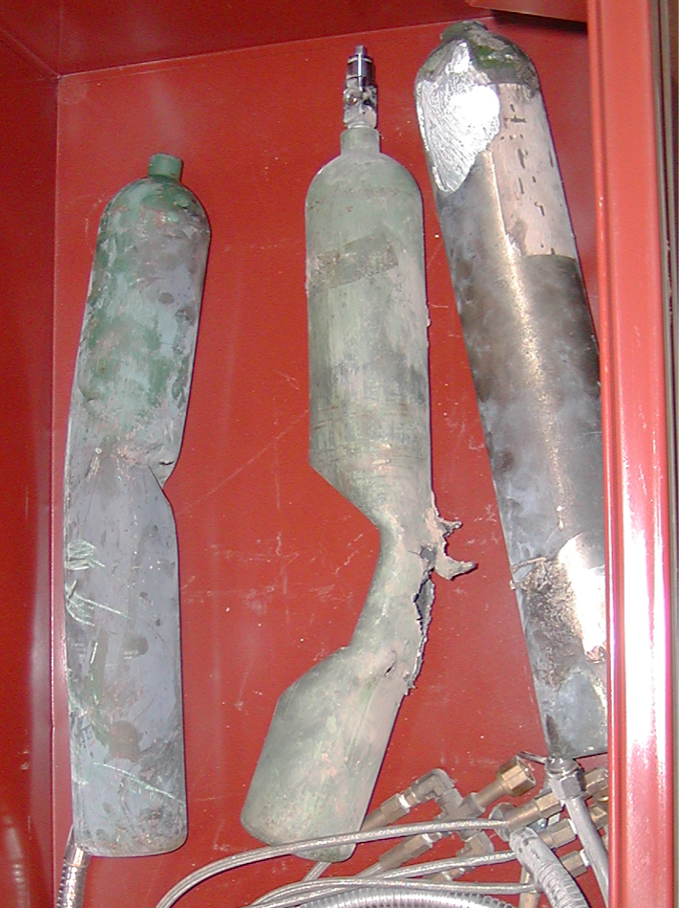
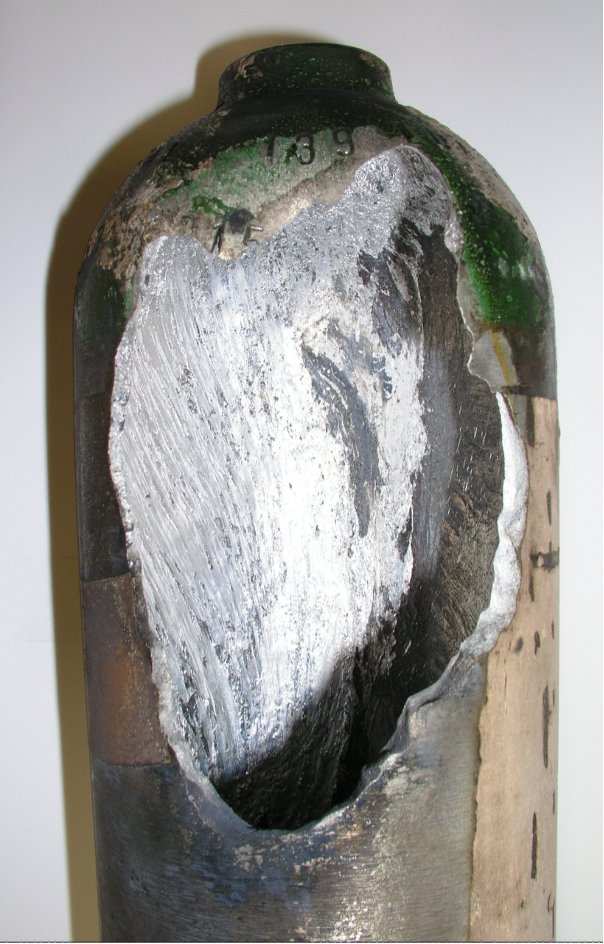
Incident 2: 2004 scuba tank fire
In 2004, an aluminum scuba cylinder caught fire while being filled with gaseous oxygen. Operators reportedly filled it with oxygen before adding nitrogen for a desired Nitrox mixture (generally considered approximately 40% oxygen and 60% nitrogen).
During the filling operation, a fire erupted inside the cylinder. This resulted in burning of the upper body/neck and ejection of a segment of the cylinder’s upper body below the threads (first photo below). This incident resulted in fatal injuries to the operator.
WHA’s subsequent investigation found combustion patterns indicating that burning aluminum residue momentarily blew backward (against the flow) through the cylinder’s scuba valve toward the attached fill adaptor before the rupture. The cylinder valve demonstrated severe melting at the base of the threads and was energetically ejected from the cylinder (second photo). The fill adaptor valve was fractured where it had initially been attached to the scuba valve (third photo). Notably, less combustion residue was observed inside the fill adaptor’s fractured outlet than in the scuba valve.
While this fracture could have occurred when the cylinder valve was ejected, the blowback patterns inside the scuba valve indicated the components were still attached to the cylinder and pressurized with oxygen (before the cylinder rupture) when the fracture developed. This suggests that an impact or bending load may have occurred to initiate the sequence of events.
Chemical and metallurgical analysis also revealed that the cylinder and scuba valve were internally contaminated with hydrocarbon residues, which are incompatible with high-pressure gaseous oxygen.
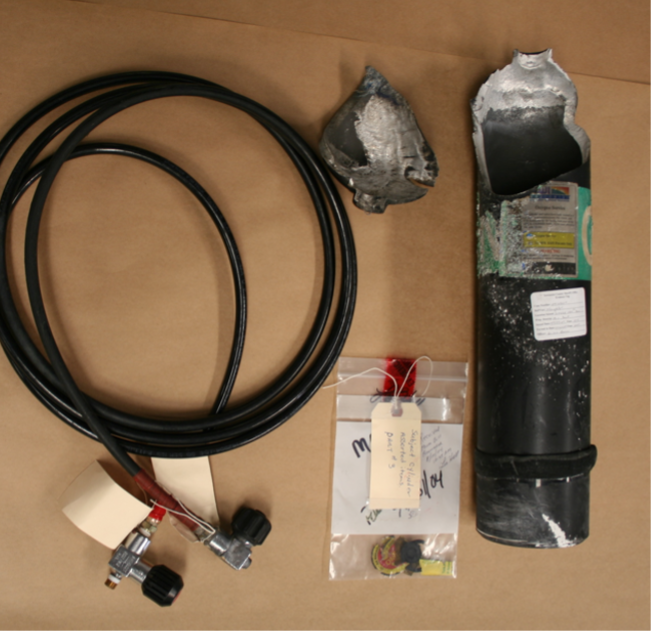
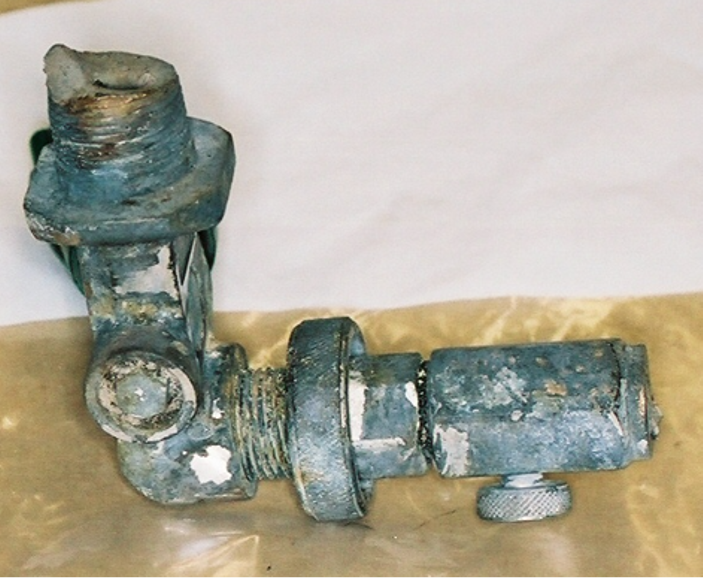
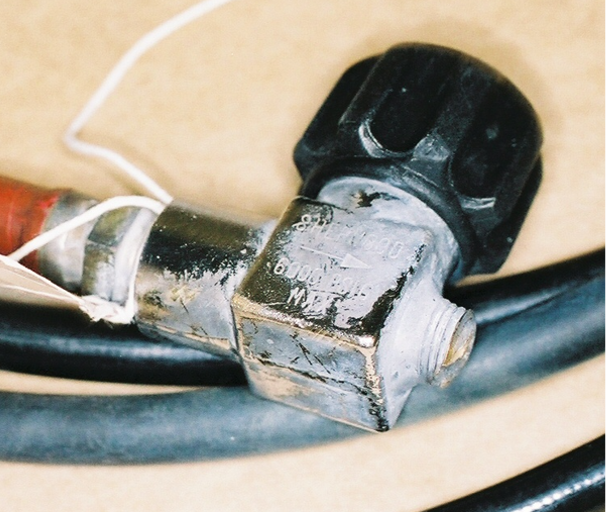
Incident 3: 2012 Scuba cylinder fire
In 2012 another scuba cylinder experienced a catastrophic fire and rupture just after it was filled with oxygen and loaded into a pickup truck.
WHA understood that the incident cylinder and a sister cylinder had just been swung into the back seat of a pickup truck, and the door closed. A venting noise was heard, followed by an explosion inside the pickup truck (first photo below). This incident did not result in a serious injury since the driver was still outside the truck, but significant damage to the vehicle occurred.
The cylinder and valve separated in the event, and the fire consumed the entire upper neck of the tank where the valve threads originally existed (second photo). The valve showed severe melting and consumption of the lower threaded area, similar to the previous fires (third photo).
Based on the incident, either a bending moment or an impact by the door (or both) was suspected as the initiating energy.
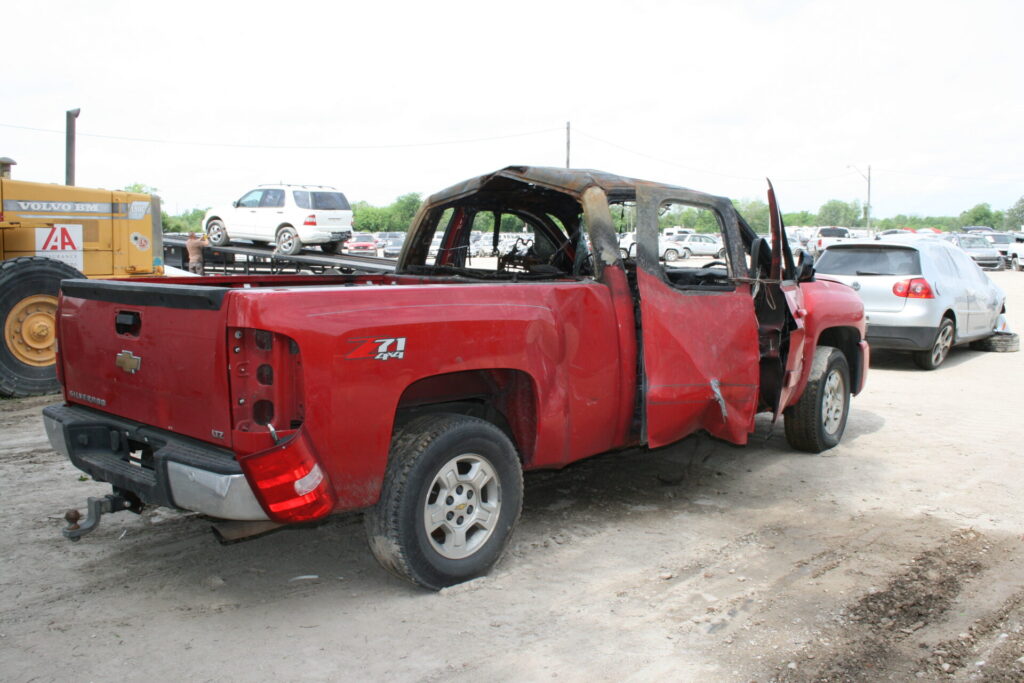
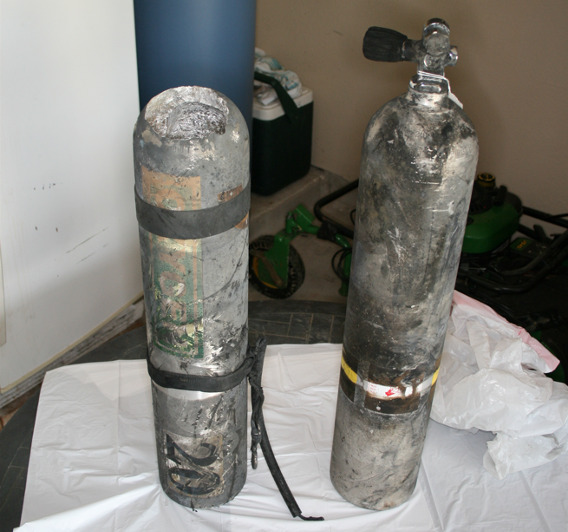
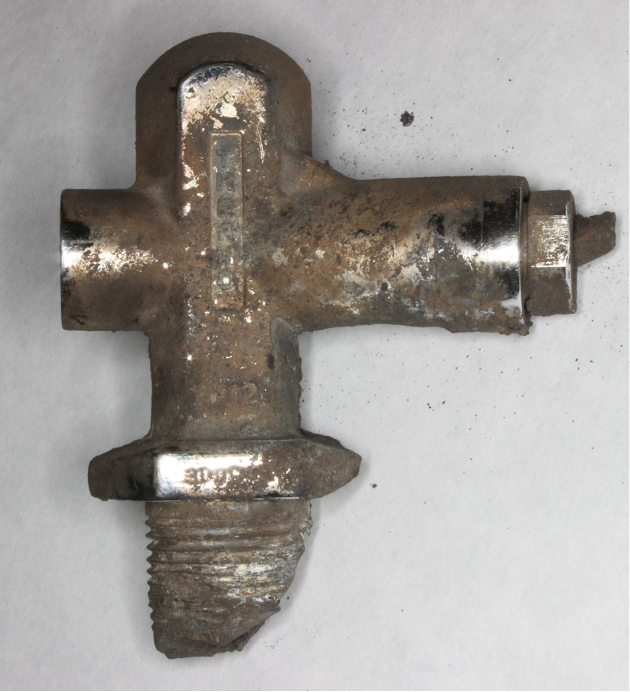
Oxygen Fire Forensic Analysis
Following each incident, WHA’s oxygen safety experts took hundreds of photographs to thoroughly document the evidence and the scene of the explosive energy release.
Back at WHA’s Test and Training Center in Las Cruces, New Mexico, technical personnel analyzed the evidence associated with these events using microscopy, chemical/metallurgical analysis, and other techniques developed by WHA to map the combustion patterns and melt/flow patterns associated with the fire propagation. Every incident exhibits individual combustion characteristics that develop from unique circumstances, which the WHA investigative analysis evaluates.
In addition to these three incidents, WHA has also investigated or is aware of other fires with medical and scuba cylinders that share some similarities. However, each event has distinguishing fire patterns and individual characteristics.
Currently, no exclusive commonality of manufacturers of either valves, cylinders, or packaged gas systems has been identified with these incidents. Although the circumstances for each incident are unique, they still share some common elements:
- The medical or scuba package was pressurized with gaseous oxygen contained by aluminum cylinders at elevated oxygen pressures (typically of about 2000 psig).
- Some foreign contamination with hydrocarbon-based contaminants was either confirmed by chemical analysis or suspected based on the filling/use environment.
- Internal ignition of the aluminum cylinder occurred in the upper neck of the cylinder in the proximity of the valve threads.
- Improper storage or mishandling of the cylinder gas package resulted in sharp impact or severe bending torque applied to the cylinder’s upper neck and valve.
- The resulting burnout of the pressurized aluminum cylinder was catastrophic.
Some failure analysis investigations are still underway, and both regulating authorities and manufacturers/distributors are keenly interested in understanding these events. So, at this time, definitive conclusions about the initiation of aluminum combustion are still being developed.
However, it may be stated that while aluminum cylinders have a long and successful history of use in medical and scuba applications, with millions of cylinders being used safely and successfully every day, some mishandling events can lead to the ignition of the aluminum and very energetic ruptures. What is the combination of circumstances that explains these events?
Looking for Answers Through Reconstruction Testing
Based on reports, fire patterns, and evidence from the forensic investigation, WHA’s oxygen safety experts are currently focused on the ignition energy and kindling chain necessary to induce sustained burning and have developed a test system capable of safely imparting a mechanical impact to valves installed on tanks pressurized with gaseous oxygen. The testing allows WHA researchers to study these incidents in a controlled environment within a test bunker capable of withstanding the energy release of a burning aluminum cylinder.
To reduce the overall energy release that might occur and still investigate the ignition energy in the neck region of the cylinder, WHA worked with a cylinder manufacturer to create mini-cylinders made of aluminum – vessels with the same valve connections and upper geometry but reduced volume, to help limit the potential energy release from ignition and rupture.
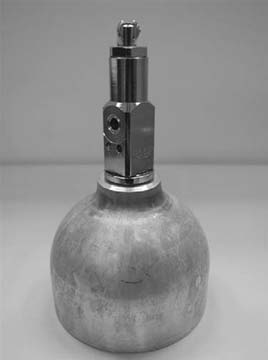
WHA’s test system utilizes an Army Ballistic Missile Agency (ABMA) type drop tower installed in one of WHA’s blast-test cells for energy containment – similar to the setup used in a liquid oxygen (LOX) mechanical impact test. In this way, various cylinder valves and valve-integrated pressure regulators can be fitted to the mini cylinders, positioned in various configurations/angles with contaminants consistent with those observed in the investigations, and subjected to impact forces at different energy levels.
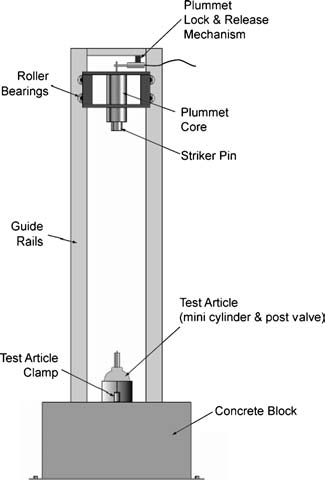
The WHA test team has conducted over 60 impact tests in different configurations with valve/cylinder assemblies prefilled with 2000 psig high-pressure oxygen, but no propagating ignitions have yet developed. Specific configurations also added incompatible lubricants (like hydrocarbon oils and particles) at the connection point between the valve and cylinder. In this testing, precursors to ignition have been observed, but full kindling of the aluminum cylinder has yet to develop. However, the WHA test system allows our researchers to vary the impact energy, configuration, and kindling chain concentrations during future tests.
Failure Analysis Findings and Subsequent Theories
While ignition energy research efforts continue, the testing completed to date demonstrates that aluminum oxygen tanks are very difficult to ignite, as shown by their long history of safe use, mainly due to the metal’s inherent ability to resist ignition.
“Aluminum naturally forms a thin oxide layer on its surface. It’s a form of corrosion like accelerated aluminum rust,” explains Dr. Chiffoleau, whose Ph.D. work focused on metals ignition and burning in oxygen. “Because this material has a tenacious oxide layer, this layer hinders the reaction of the aluminum substrate, which is required for ignition. But when this layer is breached and the fresh aluminum underneath is exposed, it can ignite in the presence of a sufficient heat source. Physical damage like impact or friction can break through that layer and generate localized heat.”
While WHA’s investigation and test experience confirms that aluminum cylinders are very difficult to ignite directly in this configuration, these incidents suggest that mishandling that leads to impact along with a kindling chain can develop under specific circumstances. While all similar incidents have unique circumstances that are individual to the event itself, the chain of events is believed to involve a combination of the following kindling elements at various levels of importance and are still being evaluated by WHA as part of its ongoing research:
- hydrocarbon contamination
- perfluorinated lubricants
- aluminum thread shavings and particles
- thin sections of aluminum threads
- aluminum cylinder thread condition and class
- folds in the bulk sections of the aluminum cylinder
Takeaways for End-Users
Proper handling of compressed gas cylinders during movement, use, and even storage is essential, and steps should be taken to ensure the cylinders are not damaged, prone to falling, and are moved/transported safely.
Dr. Chiffoleau states, “Although aluminum oxygen tanks have proven to be quite resilient, end-users should always treat them with respect and handle them carefully. The initiation event in the fires we know of developed from mishandling or a failure that caused an impact, probably on the valve, or a significant bending load introduced at the cylinder neck.”
Users should also take special care to ensure that contaminants like hydrocarbon oils and greases are not transferred onto oxygen equipment during handling and use. One common element of these incidents has been contamination that has worked its way into the oxygen system.
Users can learn more about good practices in WHA’s Oxygen Fire Hazards Training and also take advantage of available industry information such as that from the Compressed Gas Association (CGA) at CGA SP-23 Safe Use of Cylinders Containers Equipment (cganet.com).
Takeaways for Industry
Dr. Chiffoleau also reinforces that “industry should always use approved materials for cylinder/valve assemblies and follow proper oxygen cleaning practices for cylinders, valves, and filling systems.” CGA and other industry groups provide good guidance for cleaning for oxygen service. The WHA Oxygen Fire Hazards Training also guides oxygen cleaning, emphasizing the following approach:
- Start clean: All components must be adequately cleaned for oxygen service. Never install a part not “bagged and tagged” or marked as oxygen clean.
- Verify clean: Use qualitative visual inspection methods or oxygen clean verification to ensure that components are properly cleaned.
- Assemble clean: Assemble components in a clean indoor area. Use visually clean tools and powder-free gloves. Use ONLY specified oxygen-compatible lubricants and pipe tape sparingly, as directed.
- Maintain clean: Clean all exterior surfaces before opening an oxygen system and follow clean assembly practices for ongoing inspection and maintenance.
Share this entry
Related Articles
Battery Safety Insights with Nic Linley, Electrical Engineer
Battery technology continues to evolve rapidly in the 21st Century, powering an expanding array of devices and…
Oxygen Cylinder Filling System Fire Case Study
Oxygen cylinders and pressure systems quietly hold enormous amounts of energy. When things go wrong, the results…
WHA Presents O2 Safety Papers at 2024 ASTM G04 Symposium
In October 2024, Gwenael Chiffoleau, Nic Linley, and Brent Houser traveled to Prague for the 16th ASTM…
Request an expert
consultation
Contact us to request a free consultation with an experienced engineer who can help you better understand your needs and our solutions.