Case Study: PCTFE Dimensional Instability Results in Oxygen Fires
Because materials ignite and burn more easily in oxygen, manufacturers must select oxygen-compatible materials for O2 components and systems. Non-metals like plastics and rubbers are particularly easy to ignite, and only a few special compounds are appropriate for use with oxygen.
Even when using oxygen-compatible materials, engineers must utilize best design practices to ensure nonmetallic materials are protected — and not subjected to overload or service conditions beyond their mechanical limits.
In the 1990s, issues around a popular polychlorotrifluoroethylene (PCTFE) plastic caused numerous oxygen fire incidents. The resulting investigation and research unveiled important takeaways for materials compatibility, ultimately resulting in a new ASTM standard to help keep industry safe around oxygen.
What happened to Kel-F PCTFE?
Until the 1990s, Kel-FTM 81 served as a go-to oxygen compatible material within the aerospace industry. 3M developed this PCTFE plastic product for various workhorse applications, including O2 valve seats. The material was durable and exhibited excellent compatibility with oxygen, meaning it resisted ignition and burning within properly designed O2 components.
Kel-F was used successfully for decades until it was phased out in the mid-1990s. Based on contact with 3M personnel, we understand that the material was challenging to make correctly — as many as 19 out of 20 batches had to be rejected for failure to meet quality controls. Especially after a fire in the 3M production facility, the cost outweighed the benefit, and industry was left looking for a new PCTFE alternative.
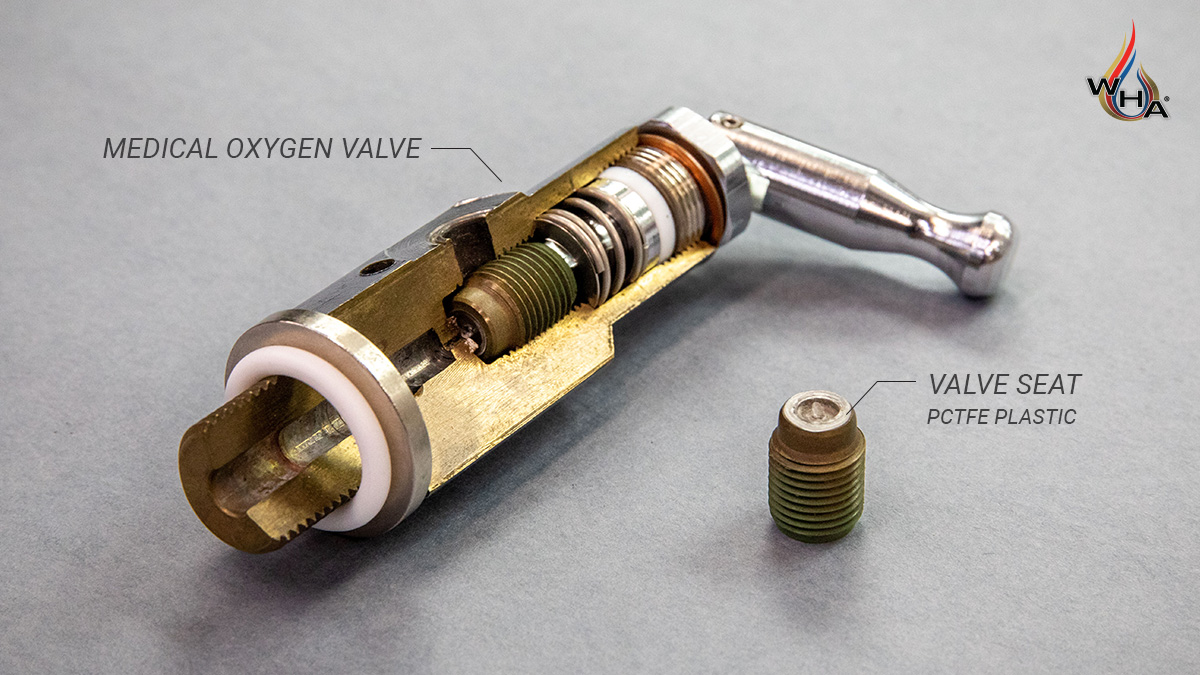
Industry struggles to understand NeoflonTM CTFE
As 3M started phasing out their production of Kel-F, they utilized the production of PCTFE material from the Japan-based company Daikin. They provided their own version of PCTFE called Neoflon CTFE M400H, which was generally consistent with 3M’s aerospace-grade PCTFE. This material was resold by 3M as Kel-F. However, after the 3M fire, they terminated the Kel-F line, and designers and manufacturers began using Neoflon in place of Kel-F. In fact, many still referred to the new Daikin product as Kel-F.
Despite the assumption of interchangeability, Neoflon and other PCTFE formulations have distinct material properties and can behave differently under stress. Some soft-seated components using PCTFE became overloaded or experienced softening in service. This problem resulted in multiple oxygen fires throughout a variety of industries. Neoflon and Kel-F both provided excellent oxygen compatibility, but it is critical to stabilize the mechanical behavior of the PCTFE under load, especially for seating applications.
“Manufacturers are still struggling with this issue. I still see new design drawings that include Kel-F, even though the material hasn’t been available for 20 years.” – Barry Newton, CEO, Principal Oxygen Safety & Forensic Engineer
Oxygen fires result from PCTFE incompatibility.
In just the first few months of 1997, WHA personnel investigated eight fires reported to the United States Food and Drug Administration (FDA) involving cylinder valves on medical oxygen cylinders. The fires resulted in a recall of approximately 8000 cylinders.
Industry called upon NASA and WHA International technical personnel to find out what went wrong. Each incident involved a PCTFE plastic valve seat, and further investigation revealed that those parts were the primary origin of ignition.
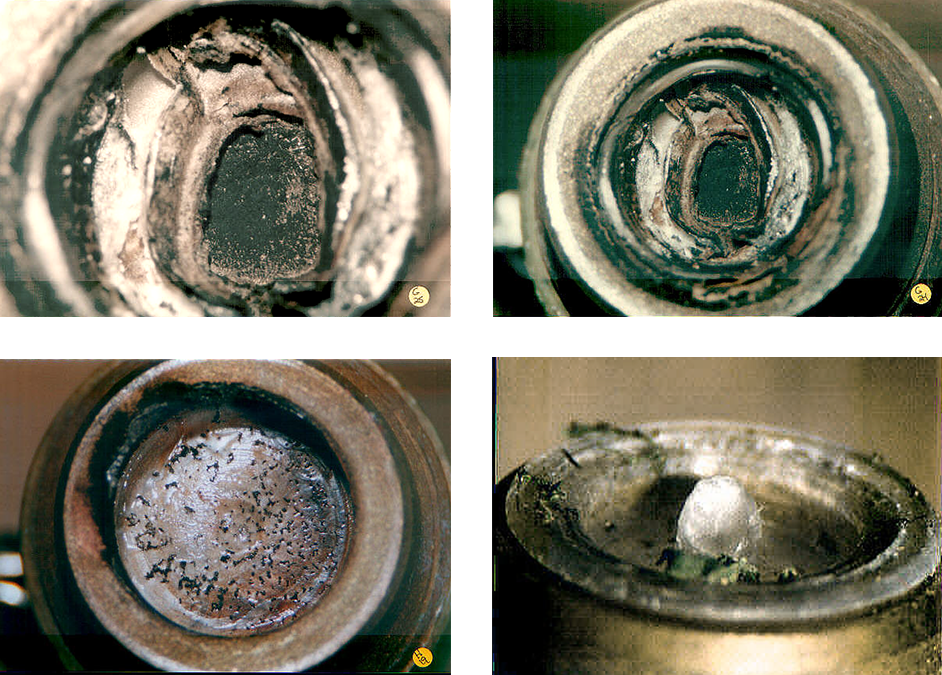
Failure analysis findings.
The WHA failure analysts identified the seat plug (nonmetallic) as the fire’s origin. Using Fourier Transform Infrared Spectroscopy (FTIR), they further confirmed that the polymeric seats were PCTFE plastic.
WHA partnered with NASA-WSTF to evaluate the mechanical stability of the PCTFE, and this joint investigation of the failed (and recalled) components showed that many of the seats had experienced significant deformation during service. Some Neoflon seats exhibited excessive coining (extrusion), and some had even begun to flow under load beyond the valve seat retainer.
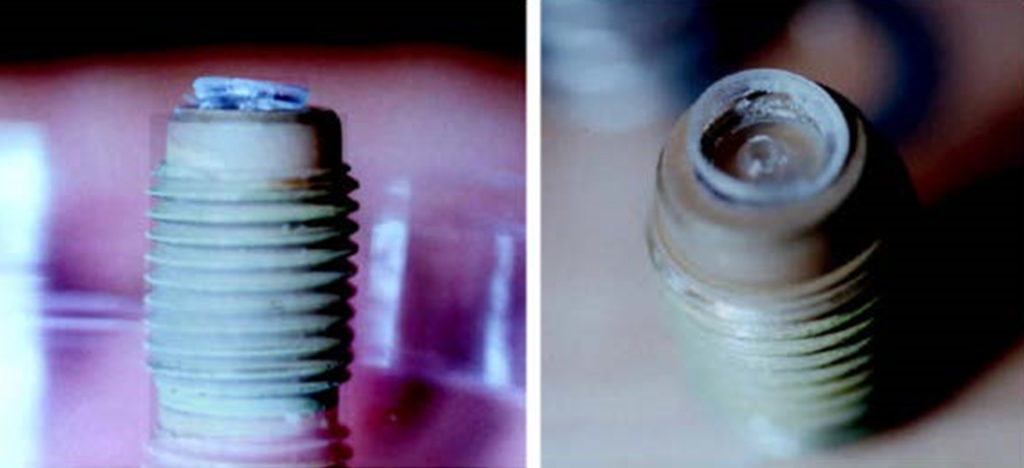
Deformation of any kind is undesirable in a sealing application, and these dimensional instabilities led to several concerns:
- Extrusion could cause gaps resulting in leaks.
- Extrusion could cause localized heating and ignition as gas flowed across the torturous path and finely divided material.
- Extrusion under static load (valve closed) could also lead to slow leaks from cylinders during storage, meaning they would not have sufficient oxygen in the cylinder when needed.
NASA and WHA performed extensive thermomechanical analysis (TMA) to understand this dimensional instability better. They also corroborated their findings with Differential Scanning Calorimetry (DSC). Finally, the teams performed gaseous oxygen (GOX) impact sensitivity tests to determine the ignitability of different PCTFE grades.
Analysis and testing indicated three possible ignition mechanisms: contaminant promotion, flow friction, and resonance (vibration). Once the PCTFE had deformed, each mechanism had the potential to ignite the material, leading to catastrophic failure, even at low operating temperatures.
Solutions to reduce effects of dimensional instability.
Because of the issues caused by deformation and dimensional instability, WHA and NASA recommended that manufacturers perform additional annealing on the PCTFE parts, which led to a new international ASTM standard on PCTFE processing (see below).
Today WHA helps manufacturers understand the benefits of PCTFE annealing and even provides outsourced annealing services. The program is run by Greg Odom, WHA senior mechanical engineer and standard test engineer.
“Annealing is used to harden the PCTFE material and give it better lasting characteristics over time. The process gives it a little more strength and increases the longevity of the part.” – Greg Odom, Senior Mechanical Engineer, Standard Test Engineer
In simple terms, annealing is a treatment that exposes the material to heating and gradual cooling temperatures. This process changes the structure of the material and relieves internal stresses. In essence, annealing kick-starts any dimensional stability in a controlled environment before the PCTFE part is put to work in an oxygen component.
Creation of a new ASTM standard
After their investigation and subsequent testing, WHA and NASA published their findings in a paper submitted to ASTM. WHA’s Dr. Barry Newton and Dr. Harold Beeson (then employed at NASA) contributed to the paper titled “Comparison of the Dimensional Stability of Kel-F 81 and Neoflon CTFE M400H Polychlorotrifluoroethylenes used in Valve Seat Applications.”
A subsequent publication captured details regarding processing parameters, annealing, and machining on the structure and dimensional stability of Neoflon M400H. (See “Effect of Molding and Machining on Neoflon CTFE M400H polychlorotrifluoroethylene Rod Stock and Valve Seat Properties.”)
The study resulted in the development of a new ASTM standard to help manufacturers stabilize the mechanical properties of PCTFE and provide a more rigorous specification for better control of dimensional stability, molecular weight, and crystallinity. (See ASTM, D 7194–05, “Standard Specifications for Aerospace Parts Machined from Polychlorotrifluoroethylene PCTFE.”)
Share this entry
Related Articles
Battery Safety Insights with Nic Linley, Electrical Engineer
Battery technology continues to evolve rapidly in the 21st Century, powering an expanding array of devices and…
Oxygen Cylinder Filling System Fire Case Study
Oxygen cylinders and pressure systems quietly hold enormous amounts of energy. When things go wrong, the results…
WHA Presents O2 Safety Papers at 2024 ASTM G04 Symposium
In October 2024, Gwenael Chiffoleau, Nic Linley, and Brent Houser traveled to Prague for the 16th ASTM…
Request an expert
consultation
Contact us to request a free consultation with an experienced engineer who can help you better understand your needs and our solutions.