Configurational Oxygen Testing Enhances Performance for Industry
In 2016, Flowserve Corporation approached WHA International, Inc. to help create a unique solution to a common problem in industry.
Flowserve manufactures a variety of large industrial oxygen components that need safety performance data, but much of this equipment is too large to feasibly perform the full component-level tests. In the absence of component test data, manufacturers commonly ensure safe performance by referencing maximum operating temperatures and pressures of the components’ materials. This approach is sound, but the results can be quite conservative.
Flowserve expected that their components could be rated to higher maximum operating conditions, and their customers could safely achieve higher performance. To explore this, they wanted to create a new “configurational” test system that could collect performance data on a partial assembly without testing the whole component.
In order to turn their concept into a reality, they knew they would need an experienced partner, and they reached out to the specialized oxygen safety engineers at WHA to work together on the unique testing project.
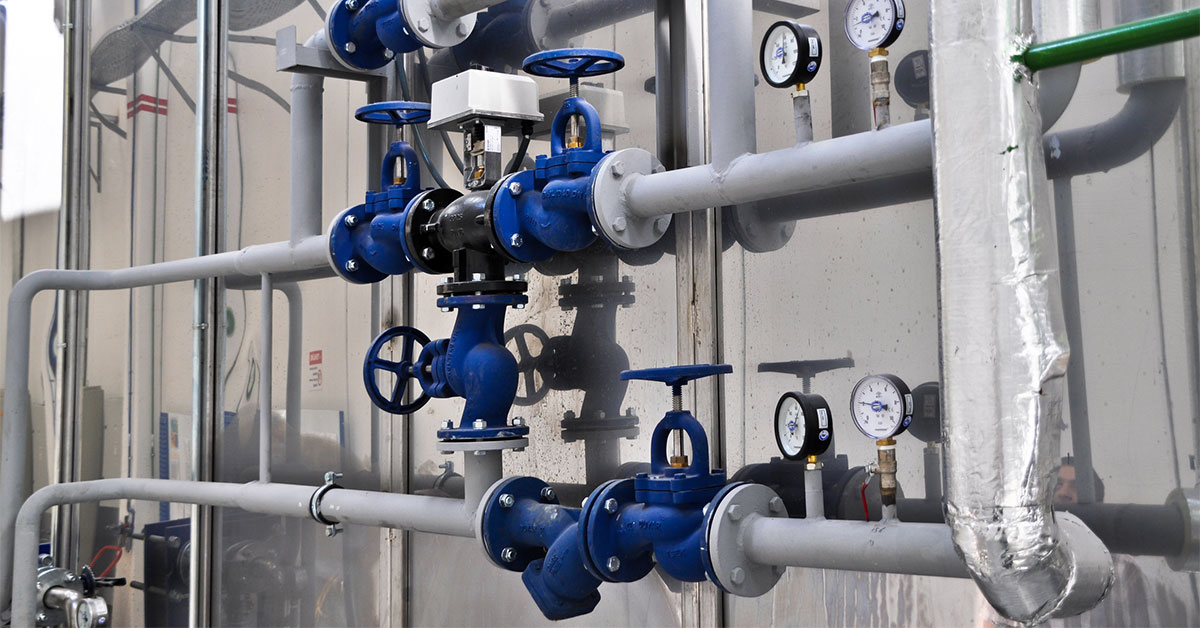
Background: Nonmetals and Oxygen Fire Risk
WHA’s Standard Testing Lead Greg Odom and Senior Oxygen Safety Engineer Gwenael Chiffoleau helped coordinate this project. Gwenael explains how nonmetals can pose a fire risk in oxygen systems: “Under sudden or extreme pressurization, nonmetals like plastics, elastomers, coatings, and lubricants can rapidly heat up and ignite. We’ve investigated many oxygen fire incidents over the years that have involved compression heating ignition.”
The Oxygen Pressure Surge (OPS) test is one standard test we can use to determine the ignition sensitivity of nonmetals or components to dynamic pressure impacts. This type of testing is also known as oxygen pressure shock, adiabatic compression, rapid pressurization, or pneumatic impact testing. It tells component designers about the ignition pressure threshold… at what pressure will the material ignite when exposed to an OPS?
Testing complete components is preferred, but it is often not feasible for large industrial oxygen equipment. In this case, OPS testing can be performed on the component’s individual materials in accordance to test standards such as ISO 21010:2017 and ASTM G74. Unfortunately, the material OPS test is severe and is likely overly conservative in many large piping applications.
“For example, PTFE X as a material is technically limited to 6 MPa according to material OPS testing, but it’s been used safely in some industries up to 70 MPa,” shares Gwenael.
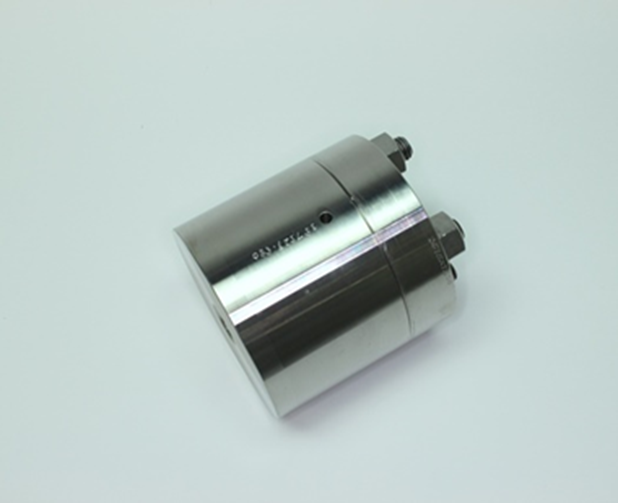
Solution: Configurational Oxygen Testing
In order to collect better data about nonmetals in large oxygen components, Flowserve and WHA looked to ISO Standard 21010:2017…
“Materials not satisfying the requirements of 5.4.2.2 or 5.4.2.3 can still be used providing they successfully pass, in their actual operating configuration, the “oxygen pressure surge test” described in Annex C of ISO 10297:2014 (e.g., for a valve sealing material, the entire valve or a representative assembly shall be tested).”
These few lines held the key. If OPS testing could not be performed on a complete component (e.g., entire valve), its materials could still be qualified “in their actual operating configuration.” The test team would need to develop a “representative assembly” to simulate the real-world configuration.
“With Flowserve’s help, we have focused on that clause about testing materials in an application-specific, realistic situation,” explains Gwenael. “The result is a combination material and component test. It isolates the important portion of the component, using the standard in the most practical way possible.”
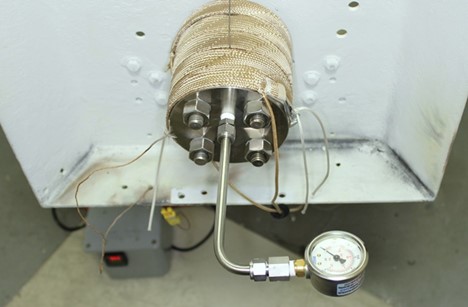
Process
To simulate real-world operating conditions, Flowserve and WHA designed and built a new partial test fixture customized to Flowserve’s component.
During an OPS test, the system achieves a rapid pressure increase (15 to 20 milliseconds) at the end of a capped tube. A pressure gauge is installed on the test article outlet port, and pressure observed by this gauge during the testing indicates a failure of the O-ring seal.
The system also tests the effects of elevated temperatures, utilizing heat tape wrapped around the test article. A controller and thermocouple both maintain heat during testing and monitor for any temperature rise that could indicate ignition of the nonmetals inside the test article.
After extensive testing, the team determined that the testing approach was valid and could result in an in-situ detectable ignition, but still relied on post-test visual examination for evidence of ignition.

Impact: Configurational Testing Expands Material Options and Improves Component Performance
Based on the results observed during this testing and the pass/fail criteria specified in ISO 10297, the test articles were judged to have successfully met the requirements of ISO 10297 Annex C – Oxygen Pressure Surge Test, at significantly higher pressures than recorded in the material OPS test.
According to ISO 21010, this “representative assembly” testing permitted the use of the subject nonmetals within a much wider margin for safe operating conditions.
Throughout the process, the new test fixture also revealed important insights into real-world operation. “For one, we found the design of the valve around the non-metals actually protects them from ignition,” says Gwenael. “Because these realistic design factors are protecting the non-metals, we found the components to be ignition resistant at much higher temperatures and pressures. We were able to demonstrate that through configurational oxygen testing.”
As a result, end-users can now get much higher performance out of the components, and Flowserve, the manufacturer, has more freedom in their materials choices. The traditional method of material-only testing severely limits manufacturers’ choices when it comes to nonmetals. They are often forced to depend upon materials that are expensive, difficult to produce and/or exhibit lower sealing performance.
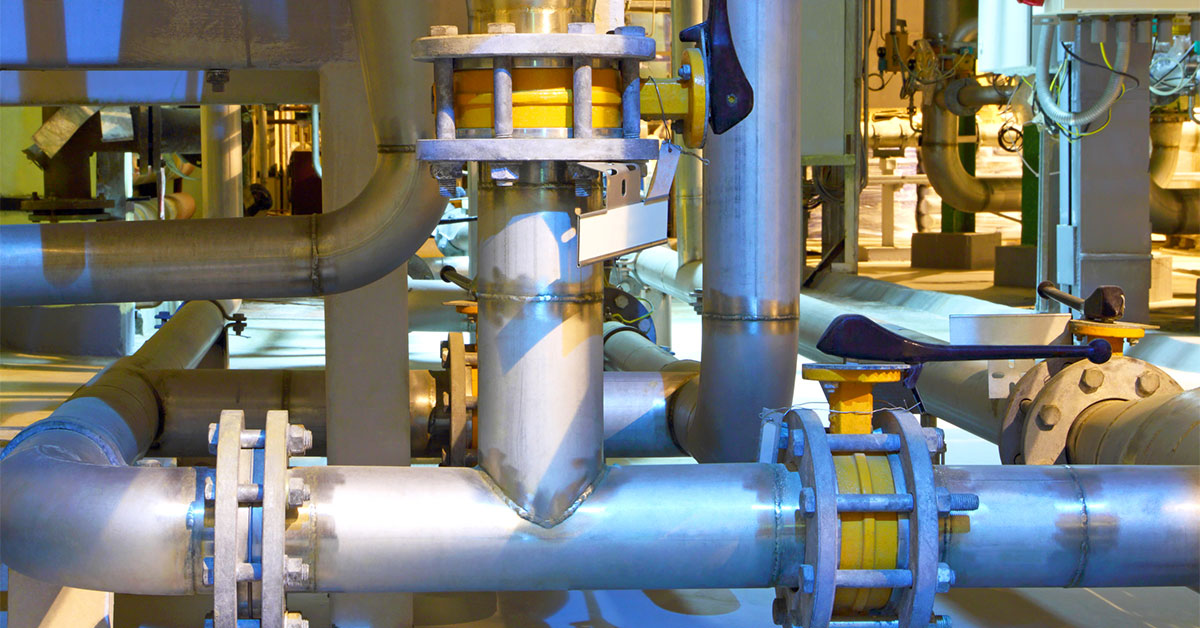
Further Reading
If you would like to learn more about this customized solution for Flowserve components, you can read more in the upcoming paper “Configurational Oxygen Compatibility Testing of Nonmetals” published by Greg Odom, Gwenael Chiffoleau, Barry Newton of WHA International in partnership with Kevin Smith and Rob Carlson of Flowserve Corporation.
Partner with WHA
If you have questions about testing for materials and components designed for oxygen service, don’t hesitate to reach out to our experienced team at WHA International. We offer a variety of standard tests as well as custom testing projects like this one.
The particular test fixture described in this story is specific to Flowserve valves, but in principle, similar fixtures could be designed for other components as well. It’s one of the many ways that WHA’s consultants are creating unique new solutions to equip industry and advance the science of oxygen safety.
Share this entry
Related Articles
Battery Safety Insights with Nic Linley, Electrical Engineer
Battery technology continues to evolve rapidly in the 21st Century, powering an expanding array of devices and…
Oxygen Cylinder Filling System Fire Case Study
Oxygen cylinders and pressure systems quietly hold enormous amounts of energy. When things go wrong, the results…
WHA Presents O2 Safety Papers at 2024 ASTM G04 Symposium
In October 2024, Gwenael Chiffoleau, Nic Linley, and Brent Houser traveled to Prague for the 16th ASTM…
Request an expert
consultation
Contact us to request a free consultation with an experienced engineer who can help you better understand your needs and our solutions.